Три вида инсталации за смесване на горещ асфалт в момента са по-популярни
Превръщането на инертни материали и битум в асфалт за изграждане на пътища изисква процес на термично смесване. Инсталацията за смесване на асфалт е незаменима за това. Целта на инсталацията за смесване на асфалт е да смеси инертни материали и асфалт заедно при повишена температура, за да произведе хомогенна асфалтова смес. Използваният инертен материал може да бъде единичен материал, комбинация от едри и фини инертни материали, със или без минерален пълнител. Използваният свързващ материал обикновено е асфалт, но може да бъде асфалтова емулсия или един от различни модифицирани материали. Различни добавки, включително течни и прахообразни материали, също могат да бъдат включени в сместа.
Понастоящем има три по-популярни типа инсталации за смесване на горещ асфалт: партидна смес, барабанна смес и непрекъсната барабанна смес. И трите вида служат за една и съща крайна цел и асфалтовата смес трябва да бъде по същество сходна, независимо от вида на инсталацията, използвана за нейното производство. Трите вида инсталации обаче се различават по работа и поток от материали, както е описано в следващите раздели.
Завод за партиден смесен асфалт
асфалтосмесителната инсталация е ключово оборудване за всяка пътностроителна фирма. Всяка операция на асфалтова смесителна инсталация има много функции. Заводите за производство на партиди от асфалт произвеждат гореща асфалтова смес в серия от партиди. Тези инсталации за смесване на партиди произвеждат горещ асфалтов микс в непрекъснат процес. Също така е възможно да се промени и използва това оборудване за производство на горещ асфалтов микс, като се използва рециклиран материал. Инсталациите от партиден тип имат вариации в тях, които позволяват добавяне на RAP (рециклирана асфалтова настилка). Компонентите на стандартна инсталация за партиден асфалтов микс са: система за студено подаване, система за подаване на асфалт, сушилня за инертни материали, смесителна кула и система за контрол на емисиите. Кулата на партидния завод се състои от горещ асансьор, сито, горещи контейнери, теглилен бункер, кофа за претегляне на асфалт и мелница. Инертният материал, използван в сместа, се отстранява от запасите и се поставя в отделни контейнери за студено захранване. Инертните материали с различни размери се пропорционират от техните контейнери чрез комбинация от размера на отвора на вратата в долната част на всеки контейнер и скоростта на транспортната лента под контейнера. Обикновено захранващата лента под всеки контейнер отлага инертния материал върху събирателен конвейер, разположен под всички контейнери за студено захранване. Инертният материал се транспортира от събирателния конвейер и се прехвърля към зареждащ конвейер. След това материалът върху зареждащия конвейер се транспортира до сушилнята за инертни материали.
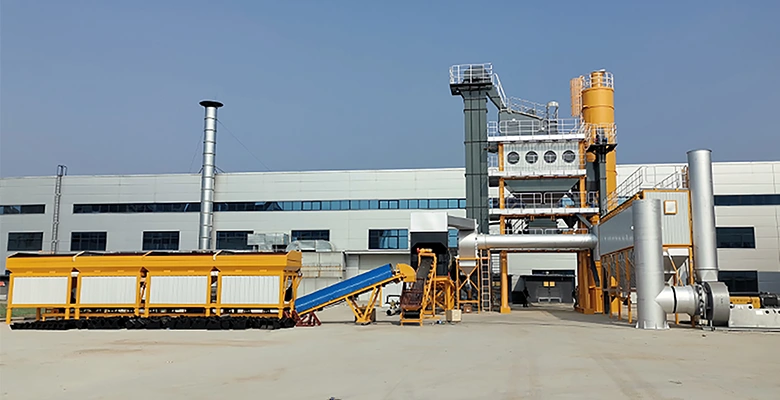
Сушилнята работи на противопоточен принцип. Инертният материал се вкарва в сушилнята в горния край и се придвижва надолу по барабана както от въртенето на барабана (гравитационен поток), така и от конфигурацията на полета вътре във въртящата се сушилня. Горелката е разположена в долния край на сушилнята, а отработените газове от процеса на изгаряне и сушене се движат към горния край на сушилнята, срещу (насреща) потока на агрегата. Тъй като агрегатът се преобръща през изгорелите газове, материалът се нагрява и изсушава. Влагата се отстранява и извежда от сушилнята като част от потока отработени газове.
След това горещият сух агрегат се изхвърля от сушилнята в долния край. Горещият агрегат обикновено се транспортира до горната част на смесителната кула на инсталацията чрез кофичен елеватор. При изпускане от асансьора, агрегатът обикновено преминава през набор от вибриращи сита в, обикновено, един от четирите резервоара за горещо съхранение. Най-финият инертен материал преминава директно през всички сита в горещ контейнер №1; по-едрите агрегатни частици се разделят от
сита с различни размери и депозирани в един от другите горещи контейнери. Разделянето на инертния материал в горещите бункери зависи от размера на отворите в ситото, което се използва в ситовата палуба, и градацията на инертния материал в бункерите за студено захранване.
Нагретият, изсушен и преоразмерен агрегат се държи в горещите контейнери, докато не бъде изхвърлен от портата на дъното на всеки контейнер в теглилен бункер. Правилното съотношение на всеки агрегат се определя от теглото.
В същото време, когато инертният материал се пропорционира и претегля, асфалтът се изпомпва от резервоара за съхранение в отделна отопляема кофа за претегляне, разположена на кулата точно над мелницата. Правилното количество материал се претегля в кофата и се държи, докато се изпразни в мелницата. Инертният материал в бункера за претегляне се изпразва в мелница с два вала и различните фракции на инертния материал се смесват заедно за много кратък период от време — обикновено по-малко от 5 секунди. След това кратко време за суха смес, асфалтът от кофата за претегляне се изхвърля.
в мелницата и времето за мокро смесване започва. Времето за смесване на асфалта с инертния материал не трябва да бъде повече от необходимото за пълното покриване на инертните частици с тънък слой от асфалтовия материал - обикновено в диапазона от 25 до 35 секунди, с долния край на този диапазон е за мелница, която е в добро състояние. Размерът на партидата, смесена в мелницата, може да бъде в диапазона от 1,81 до 5,44 тона (2 до 6 тона).
Когато смесването е завършено, вратите на дъното на мелницата се отварят и сместа се изхвърля в транспортното средство или в транспортно устройство, което пренася сместа към силоз, от който камионите ще бъдат заредени на партиди. За повечето партидни инсталации времето, необходимо за отваряне на портите на мелницата и изпускане на сместа, е приблизително 5 до 7 секунди. Общото време за смесване (време за сухо смесване + време за мокро смесване + време за разтоварване на сместа) за партида може да бъде толкова кратко, колкото около 40 секунди, но обикновено общото време за смесване е около 45 секунди.
Заводът е оборудван с устройства за контрол на емисиите, включващи първична и вторична системи за събиране. Като първичен колектор обикновено се използва сух колектор или нокаут кутия. Мокра скруберна система или по-често филтърна система от суха тъкан (торба) може да се използва като вторична система за събиране за отстраняване на прахови частици от изгорелите газове, които изтичат от сушилнята и изпраща чист въздух в атмосферата през комина .
Ако RAP е включен в сместа, той се поставя в отделен контейнер за студено захранване, от който се доставя в завода. RAP може да се добави към новия агрегат на едно от трите места: дъното на горещия асансьор; горещите кошчета; или, най-често, бункера за теглене. Преносът на топлина между прегрятия нов агрегат и регенерирания материал започва веднага щом двата материала влязат в контакт и продължава по време на процеса на смесване в мелницата.
Барабанна асфалтова смес
В сравнение с партиден тип, асфалтовата инсталация с барабанна смес има по-малко термични загуби, по-ниска работна мощност, без преливане, по-малко летящ прах и стабилен контрол на температурата. Системата за управление автоматично регулира дебита на асфалта според дебита на инертните материали и предварително зададеното съотношение асфалт-инертни материали, за да осигури прецизна пропорционална производителност. Инсталациите за барабанна асфалтова смес са типовете инсталации, които се категоризират като инсталации за непрекъснато смесване, произвеждат гореща асфалтова смес в непрекъснат процес.
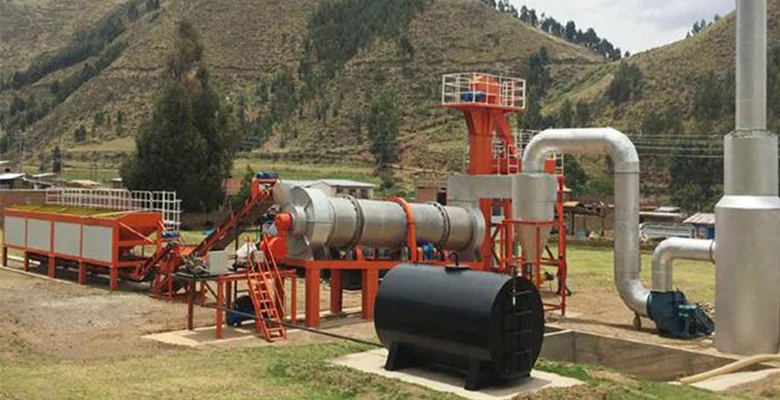
Обикновено системите за студено подаване на HMA партидни и барабанни смесителни инсталации са подобни. Всеки се състои от контейнери за студено захранване, захранващи конвейери, събирателен конвейер и зареждащ конвейер. В повечето инсталации за барабанни смеси и в някои партидни инсталации в даден момент в системата е включено сито за скалпиране. Ако RAP също се подава в завода, за да се произведе рециклирана смес, са необходими допълнителен резервоар или контейнери за студено захранване, захранваща лента и/или събирателен конвейер, сито за скалпиране и транспортьор за зареждане за обработка на допълнителния материал. инсталациите за барабанни смеси се състоят от пет основни компонента: система за студено подаване, система за подаване на асфалт, барабанен миксер, силози за пренапрежение или съхранение и оборудване за контрол на емисиите.
Контейнерите за студено захранване се използват за пропорциониране на материала към растението. Под всеки контейнер се използва подаваща лента с променлива скорост. По този начин количеството инертен материал, изтеглен от всеки бункер, може да се контролира както от размера на отвора на вратата, така и от скоростта на захранващата лента, за да се осигури точно подаване на материалите с различни размери. Инертният материал на всеки захранващ ремък се отлага върху събирателен конвейер, който минава под всички контейнери за студено захранване. Комбинираният материал обикновено преминава през сито за скалпиране и след това се прехвърля към зареждащ конвейер за транспортиране до барабанния миксер.
Зареждащият конвейер е снабден с две устройства, които се използват за определяне на количеството инертни материали, доставяни в завода: кантар под конвейерната лента измерва теглото на инертните материали, преминаващи над нея, а сензор определя скоростта на лентата. Тези две стойности се използват за изчисляване на мокрото тегло на инертния материал, в тонове (тонове) на час, влизащ в барабанния миксер. Компютърът на завода, с количеството влага в инертния материал, предоставено като входна стойност, преобразува мокрото тегло в сухо тегло, за да определи правилното количество асфалт, необходимо в сместа.
Конвенционалният барабанен миксер е система с паралелен поток - отработените газове и агрегатът се движат в една и съща посока. Горелката е разположена в горния край (края на входа на агрегата) на барабана. Инертният материал влиза в барабана или от наклонен улей над горелката, или върху конвейер Slinger под горелката. Инертният материал се придвижва надолу по барабана чрез комбинация от гравитация и конфигурация на летците, разположени вътре в барабана. Докато пътува, агрегатът се нагрява и влагата се отстранява. Плътен воал от инертен материал е изграден близо до средата на дължината на барабана, за да подпомогне процеса на пренос на топлина.
Ако RAP се добави към новия инертен материал, той се депозира от собствения му контейнер за студено подаване и събирателна/зареждаща конвейерна система във вход, разположен близо до центъра на дължината на барабана (система за разделно подаване). В този процес регенерираният материал е защитен от високотемпературните изгорели газове чрез воала от нов агрегат преди входната точка на RAP. Когато се използват смеси с високо съдържание на RAP, по-вероятно е RAP да се прегрее в процеса. Това може да доведе до отделяне на дим от барабана или повреда на RAP.
Новият агрегат и регенерираният материал, ако се използва, се придвижват заедно в задната част на барабана. Асфалтът се изтегля от резервоара с помпа и се подава през измервателен уред, където се определя правилният обем асфалт. След това свързващият материал се доставя през тръба в задната част на смесителния барабан, където асфалтът се инжектира върху инертния материал. Покриването на инертния материал се получава, когато материалите се срутват заедно и се преместват към края на разтоварването на барабана. Минерален пълнител или фини частици от торбички, или и двете, също се добавят в задната част на барабана, или непосредствено преди, или заедно с добавянето на асфалта.
Асфалтовата смес се депозира в транспортно устройство (плъзгач, лентов транспортьор или кофичен елеватор) за транспортиране до силоз за съхранение. Силозът преобразува непрекъснатия поток от смес в партиден поток за разтоварване в транспортното средство.
По принцип същият тип оборудване за контрол на емисиите се използва в инсталацията за барабанна смес, както и в инсталацията за партиди. Могат да се използват първичен сух колектор и система за мокър скрубер или торбен вторичен колектор. Ако се използва система за мокър скрубер, събраните фини частици не могат да бъдат рециклирани обратно в сместа и се губят; ако се използва резервоар, събраните глоби могат да бъдат върнати изцяло или частично в смесителния барабан или могат да бъдат изхабени.
Инсталация за непрекъснат смесен асфалт
В непрекъснатите инсталации няма прекъсване на производствения цикъл, тъй като ритъмът на производство не е разделен на партиди. Смесването на материала става вътре в барабана на сушилнята, който е удължен, тъй като същевременно суши и смесва материала. Тъй като няма смесителна кула или асансьори, системата е значително опростена, с последващо намаляване на разходите за поддръжка. Липсата на сито обаче налага наличието на прецизни контроли в началото на производствения цикъл, преди агрегатите да се подадат в сушилнята и преди да бъдат изхвърлени от сушилнята като асфалт.
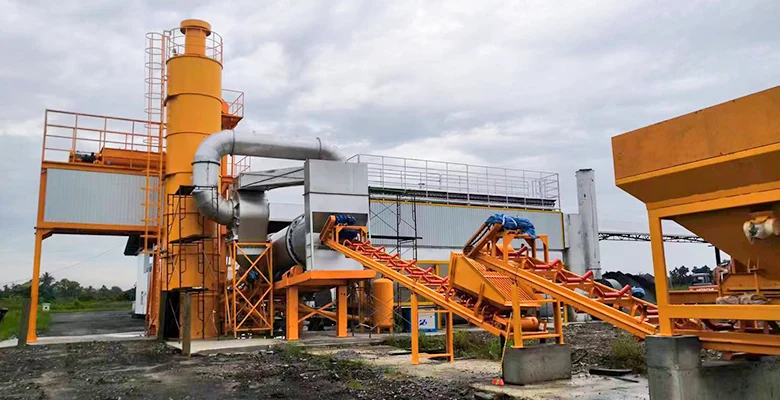
ОБЪРНО ИЗМЕРВАНЕ
Подобно на инсталациите за смесване на партиден асфалт,
производственият цикъл на непрекъснатите инсталации също започва със студените хранилки, където инертните материали обикновено се дозират по обем; ако е необходимо, екстракторът за пясък може да бъде снабден с тегловна лента за измерване.
Контролът на общото тегло на необработените инертни материали обаче се извършва в две различни фази на производствения цикъл в двете различни инсталации. При непрекъснатия тип има захранваща лента, преди влажните инертни материали да се подадат в сушилния барабан, където съдържанието на влага се настройва ръчно, за да се позволи изваждането на теглото на водата. Ето защо е изключително важно съдържанието на влага в инертните материали, особено в пясъка, да има постоянна стойност, която непрекъснато да се следи чрез чести лабораторни тестове.
ДОЗИРАНЕ НА БИТУМ
В непрекъснатите инсталации дозирането на битум обикновено е обемно чрез брояч на литри след захранващата помпа. Като алтернатива е възможно да се инсталира масов брояч, необходим избор, ако се използва модифициран битум, което изисква чести операции по почистване.
Дозиране на пълнителя
В непрекъснатите инсталации дозиращата система обикновено е обемна, използвайки захранващи шнекове с променлива скорост, които са заменили предишната пневматична дозираща система.
Контролният панел е тип PLC във всички наши заводи за износ. Това е огромна добавена стойност, защото можем да персонализираме PLC според нашите изисквания. Барабанният миксер, който е оборудван с PLC панел, е различна машина от инсталация с микропроцесорен панел. PLC панелът също не изисква поддръжка в сравнение с микропроцесорния панел. Ние винаги вярваме в даването на най-доброто на клиентите, за да могат да изпреварят конкуренцията си. Не всички производители и износители на инсталации за варели за асфалт предлагат инсталации с PLC панел.
Извършват се предварителни тестове на всички инсталации, за да се гарантира, че всичко, което напусне нашата фабрика, е готово за работа с по-малко проблеми на обекта.
Sinoroader имат повече от 30 години опит в производството и продукт, който е подкрепен от професионално обслужване и по-евтини резервни части, така че да цените и използвате вашето оборудване за години напред.