Asphalt concrete mixing plant construction technology and management 1. Raw material quality management
[1].Hot asphalt mixture is composed of aggregate, powder and asphalt. The management of raw materials mainly involves how to ensure the quality and safe production of raw materials in all aspects of storage, transportation, loading and unloading, and inspection.
1.1 Management and sampling of asphalt materials
1.1.1 Quality management of asphalt materials
(1) Asphalt materials should be accompanied by the original factory’s quality certificate and factory inspection form when entering the asphalt mixing plant.
(2) The laboratory shall take samples of each batch of asphalt arriving at the site to check whether it meets the requirements of the specification.
(3) After the laboratory sampling and inspection pass, the materials department should issue an acceptance form, recording the asphalt source, label, quantity, arrival date, invoice number, storage location, inspection quality, and the location where the asphalt is used, etc.
(4) After each batch of asphalt is inspected, no less than 4kg of material sample should be retained for reference.
1.1.2 Sampling of asphalt materials
(1) Sampling of asphalt materials should ensure representativeness of the material samples. Asphalt tanks should have dedicated sampling valves and sampling should not be taken from the top of the asphalt tank. Before sampling, 1.5 liters of asphalt should be drained to flush away contaminants from valves and pipes.
(2) The sampling container should be clean and dry. Label containers well.
1.2 Storage, transportation and management of aggregates
(1) Aggregates should be stacked on a hard, clean site. The stacking site should have good waterproof and drainage facilities. Fine aggregates should be covered with awning cloth, and aggregates of different specifications should be separated by partition walls. When stacking materials with a bulldozer, it should be noted that the thickness of each layer should not exceed 1.2m thick. The disturbance to the aggregates should be minimized when stacked by a bulldozer, and the pile should not be pushed into a trough shape on the same plane.
(2) Each batch of materials entering the site should be sampled and analyzed in accordance with the specifications for the specifications, gradation, mud content, needle flake content and other characteristics of the aggregate. Only after it is proven to be qualified can it be admitted to the site for stacking, and an acceptance form will be issued. All indicators of material quality inspection should comply with the specifications and owner's document requirements. During the construction process, the grading characteristics of the material pile should be regularly checked and monitored for changes.
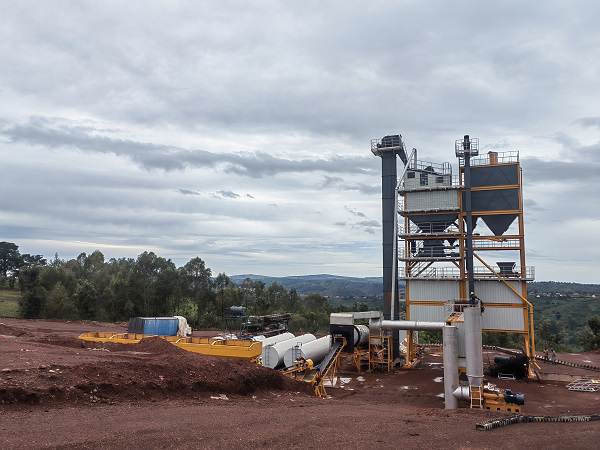
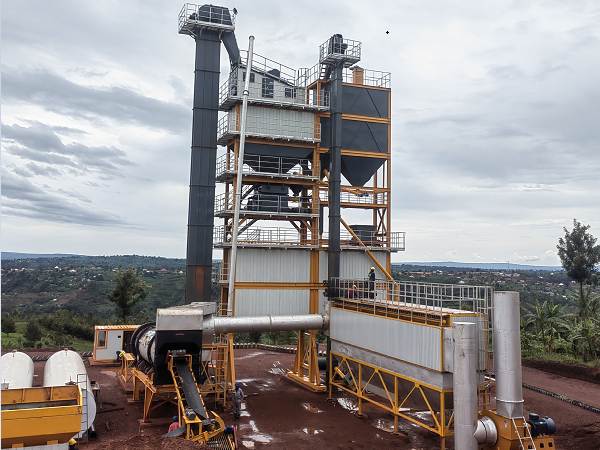
[2]. Construction of aggregate, mineral powder and asphalt supply systems
(1) The loader operator should face the side of the pile where coarse materials are not rolling down when loading. When loading, the bucket inserted into the pile should be stacked upward with a boom, and then step back. Do not use Digging by rotating the bucket reduces material segregation.
(2) For parts where obvious coarse material segregation has occurred, they should be remixed before loading; the loader operator should always keep each cold material bin full to prevent mixing during loading.
(3) The flow of cold material should be checked frequently to avoid intermittent material supply and material surge.
(4) The speed of the feeding belt should be maintained at a medium speed when calibrating productivity, and the speed adjustment range should not exceed 20 to 80% of the speed.
(5). Ore powder should be prevented from absorbing moisture and clumping. For this reason, the compressed air used for arch breaking must be separated by water before it can be used. The powder in the ore powder conveying device should be emptied after the completion of the project.
(6) Before the operation of the mixing equipment, the thermal oil furnace should be started to heat the asphalt in the asphalt tank to the specified temperature, and all parts of the asphalt supply system should be preheated. When starting the asphalt pump, the oil inlet valve should be closed and allowed to idle. Start, then slowly open the fuel inlet valve and gradually load. At the end of the work, the asphalt pump should be reversed for several minutes to pump the asphalt in the pipeline back into the asphalt tank.
[3]. Construction of drying and heating system
(1) When starting the work, the drying drum should be started by manual control when the cold material supply system is shut down. The burner should be ignited and the cylinder should be preheated with low fire for 5 to 10 minutes before loading. When loading, the feed amount should be gradually increased. According to the temperature of the hot material at the discharge port, the oil supply volume is gradually increased until the specified production volume and stable temperature conditions are reached before switching to automatic control mode.
(2) When the cold material system suddenly stops feeding or other accidents occur during work, the burner should be turned off first to allow the drum to continue rotating. The induced draft fan should continue to draw air, and then shut down after the drum is completely cooled. The machine should be shut down gradually in the same manner at the end of the workday.
(4) Always check whether the infrared thermometer is clean, wipe off dust, and maintain good sensing capabilities.
(5) When the moisture content of the cold material is high, the automatic control system will be out of control and the temperature will oscillate up and down. At this time, manual control should be used and the residual moisture content of the hot material should be checked. If it is too high, the production volume should be reduced.
6) The residual moisture content of hot aggregates should be checked regularly, especially on rainy days. The residual moisture content should be controlled below 0.1%.
(7) The exhaust gas temperature should not be too high or too low. It is generally controlled at around 135~180℃. If the exhaust gas temperature remains high and the aggregate temperature rises accordingly, it is mostly due to the high moisture content of the cold material. Production volume should be reduced in time.
(8) The pressure difference between the inside and outside of the bag dust collector should be maintained within a certain range. If the pressure difference is too large, it means that the bag is seriously blocked, and the bag needs to be processed and replaced in time.
[4]. Construction of hot material screening and storage system
(1) The hot material screening system should be regularly checked to see if it is overloaded and whether the screen is blocked or has holes. If it is found that the material accumulation on the screen surface is too high, it should be stopped and adjusted.
(2) The mixing rate of the 2# hot silo should be checked periodically, and the mixing rate should not exceed 10%.
(3) When the supply of the hot material system is unbalanced and the flow rate of the cold material bin needs to be changed, gradually adjust it. The feed supply of a certain bin should not be suddenly increased, otherwise the gradation of the aggregate will be seriously affected.
[5]. Construction of metering control and mixing system
(1) The weighing data of each batch of mixture recorded by the computer is a powerful means to check whether the measurement control system is working normally. After the machine is turned on every day and the work is stable, the weighing data should be printed continuously for 2 hours, and its systematic errors and random errors should be analyzed. If it is found that the requirements exceed the requirements, the system work should be checked in time, the reasons should be analyzed, and they should be eliminated.
(2) The mixing system should not stop during the mixing process. When the mixing equipment stops working while waiting for the truck, the mixture in the mixing tank should be emptied.
(3) After the mixing tank is finished every day, the mixing tank should be scrubbed with hot mineral materials to remove the residual asphalt in the mixing tank. Usually, coarse aggregate and fine aggregate should be used to wash 1 to 2 times each.
(4) When using a lifting hopper to unload the mixed material into the finished product silo, the hopper must be positioned in the center of the silo to discharge, otherwise longitudinal segregation will occur in the barrel, that is, the coarse material will roll to one side of the silo.
(5) When a scraper conveyor is used to unload the mixed material into the batching hopper and then into the finished product silo, a part of the mixed material should be saved for each discharge of the ingredients to prevent the mixed material conveyed by the scraper from falling directly into the material after all the materials are emptied. segregation in the warehouse.
6) When unloading materials from the finished product silo to the truck, the truck is not allowed to move while unloading but should be unloaded in piles. Otherwise, serious segregation will occur. Truck drivers are also not allowed to add a small amount of material to the pile in order to reach the rated capacity. of mixture.
(7) When discharging materials from the finished product warehouse, the discharge door should be opened quickly and the mixed materials should not be allowed to flow out slowly to avoid segregation.
(8) When unloading materials to a truck, it is not allowed to unload to the center of the truck trough. Materials should be discharged to the front of the truck trough, then to the rear, and then to the center.
[6]. Mixing control of asphalt mixture
(1) In the production process of asphalt mixture, indicators such as the dosage and mixing temperature of asphalt and various mineral materials can be accurately printed plate by plate, and the weight of asphalt mixture can be accurately printed.
(2) Heating temperature control of asphalt. The asphalt pump meets the principles of pumping and uniform ejection and can meet the requirements of the heating temperature of the lower asphalt layer between 160°C and 170°C and the heating temperature of the mineral aggregate between 170°C and 180°C.
(3) The mixing time should be such that the asphalt mixture is mixed uniformly, with a bright black color, no whitening, agglomeration or separation of thick and fine aggregates. The mixing time is controlled to be 5 seconds for dry mixing and 40 seconds for wet mixing (required by the owner).
(4) During the mixing production process, the operator can monitor various instrument data at any time, observe the working status of various machinery and the color form of the factory mixture, and promptly communicate with the laboratory and make adjustments if abnormal conditions are found.
(5) During the production process, the quality of the materials and the temperature, mix ratio and whetstone ratio of the mixture shall be inspected according to the specified frequency and method, and records shall be made respectively.
[7]. Temperature control during construction of asphalt mixture
The construction control temperature of asphalt mixture is as shown in the table below.
Temperature name of each process Temperature control requirements of each process
Asphalt heating temperature 160℃~170℃
Mineral material heating temperature 170℃~180℃
The factory temperature of the mixture is within the normal range of 150℃~165℃.
The temperature of the mixture transported to the site shall not be lower than 145℃
Paving temperature 135℃~165℃
Rolling temperature is not less than 130℃
The surface temperature after rolling is not less than 90℃
Open traffic temperature is not higher than 50℃
[8]. Loading of transport trucks at the asphalt mixing plant
The vehicles transporting asphalt mixture are all over 15t, meeting the large-tonnage thermal insulation requirements, and are covered with tarpaulin insulation during transportation. In order to prevent asphalt from sticking to the carriage, after cleaning the bottom and side panels of the carriage, apply a thin layer of a mixture of thermal oil and water (oil: water = 1:3) evenly on the stainless steel chain, and clean the wheels.
When loading the material truck at the discharge port, it must move the parking space back and forth in the order of front, back and middle. It must not be piled high to reduce the segregation of coarse and fine aggregates. After the car is loaded and the temperature is measured, the asphalt mixture is immediately covered tightly with an insulating tarpaulin and transported to the paving site smoothly.
Based on the analysis of the construction methods and management measures of the asphalt concrete mixing station, the main points are to strictly control the mixing, temperature and loading of the asphalt mixture, as well as the mixing and rolling temperatures of the asphalt concrete, thereby ensuring the quality and improvement of the overall highway pavement Construction progress.