Asphalt spreading trucks are used to spread the permeable oil layer, waterproof layer and bonding layer of the bottom layer of asphalt pavement on high-grade highways. It can also be used in the construction of county and township-level highway asphalt roads that implement layered paving technology. It consists of a car chassis, an asphalt tank, an asphalt pumping and spraying system, a thermal oil heating system, a hydraulic system, a combustion system, a control system, a pneumatic system, and an operating platform.
Knowing how to operate and maintain asphalt spreading trucks correctly can not only extend the service life of the equipment, but also ensure the smooth progress of the construction project.
So what issues should we pay attention to when working with asphalt spreading trucks?
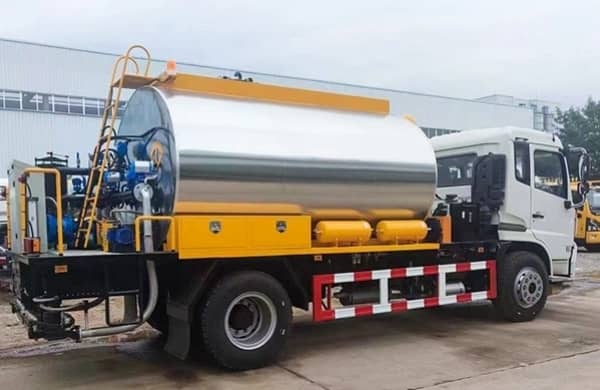

Maintenance after use
1. Fixed connection of asphalt tank:
2. After 50 hours of use, retighten all connections
End of work every day (or equipment downtime for more than 1 hour)
1. Use compressed air to empty the nozzle;
2. Add a few liters of diesel to the asphalt pump to ensure that the asphalt pump can start again smoothly:
3. Turn off the air switch on the top of the tank;
4. Bleed the gas tank;
5. Check the asphalt filter and clean the filter if necessary.
Note: Sometimes it is possible to clean the filter multiple times during the day.
6. After the expansion tank cools down, drain the condensed water;
7. Check the pressure gauge on the hydraulic suction filter. If negative pressure occurs, clean the filter;
8. Check and adjust the tightness of the asphalt pump speed measuring belt;
9. Check and tighten the vehicle speed measuring radar.
Note: When working under the vehicle, make sure the vehicle is turned off and the hand brake is applied.
per month (or every 200 hours worked)
1. Check whether the asphalt pump fasteners are loose, and if so, tighten them in time;
2. Check the lubrication condition of the servo pump electromagnetic clutch. If there is lack of oil, add 32-40# engine oil;
3. Check the burner pump filter, oil inlet filter and nozzle filter, clean or replace them in time
?Per year (or every 500 hours worked)
1. Replace the servo pump filter:
2. Replace the hydraulic oil. The hydraulic oil in the pipeline must reach 40 - 50°C to reduce the oil viscosity and fluidity before it can be replaced (start the car at room temperature of 20°C and let the hydraulic pump rotate for a period of time to meet the temperature requirements);
3. Re-tighten the fixed connection of the asphalt tank;
4. Disassemble the nozzle cylinder and check the piston gasket and needle valve;
5. Clean the thermal oil filter element.
Every two years (or every 1,000 hours worked)
1. Replace PLC battery:
2. Replace thermal oil:
3. (Check or replace the burner DC motor carbon brush).
Regular maintenance
1. The liquid level of the oil mist device should be checked before each construction. When there is a lack of oil, ISOVG32 or 1# turbine oil must be added to the upper limit of the liquid level.
2. The lifting arm of the spreading rod should be lubricated with oil in time to prevent rust and other problems from long-term use.
3. Regularly check the heating fire channel of the thermal oil furnace and clean the fire channel and chimney residues.