Reasons affecting productivity
Unqualified raw materials
Large deviation in coarse aggregate gradation: At present, the coarse aggregate used in the project is produced by multiple stone factories and transported to the construction site. Each stone factory uses different types of crushers such as hammer, jaw or impact to process crushed stone. In addition, each stone factory does not have strict, unified and standardized production management, and has no unified requirements for the wear degree of production equipment such as crushing hammers and screens. The actual coarse aggregate specifications produced by each stone factory deviate greatly from the requirements of highway construction technical specifications. The above reasons cause the coarse aggregate gradation to deviate greatly and fail to meet the gradation requirements.
Sinosun HMA-2000 asphalt mixing plant has a total of 5 silos, and the particle size of coarse aggregate stored in each silo is as follows: 1# silo is 0~3mm, 2# silo is 3~11mm, 3# silo is 11~16mm, 4# silo is 16~22mm, and 5# silo is 22~30mm.
Take 0~5mm coarse aggregate as an example. If the 0~5mm coarse aggregate produced by the stone plant is too coarse, the coarse aggregate entering the 1# silo will be too small and the coarse aggregate entering the 2# silo will be too large during the screening process of the asphalt mixing plant, causing the 2# silo to overflow and the 1# silo to wait for material. If the coarse aggregate is too fine, the coarse aggregate entering the 2# silo will be too small and the coarse aggregate entering the 1# silo will be too large, causing the 1# silo to overflow and the 2# silo to wait for material. If the above situation occurs in other silos, it will cause multiple silos to overflow or wait for material, resulting in a decrease in the productivity of the asphalt mixing plant.
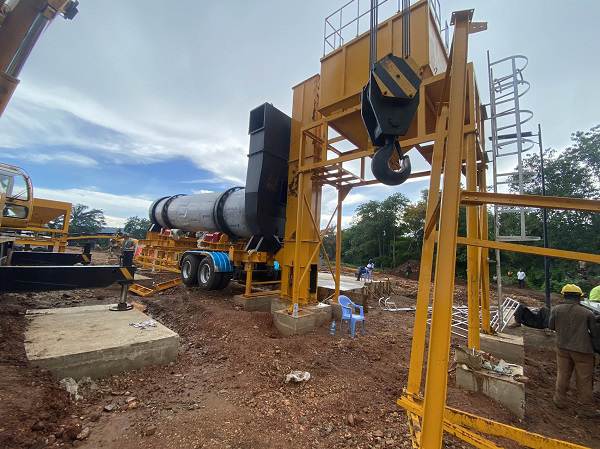
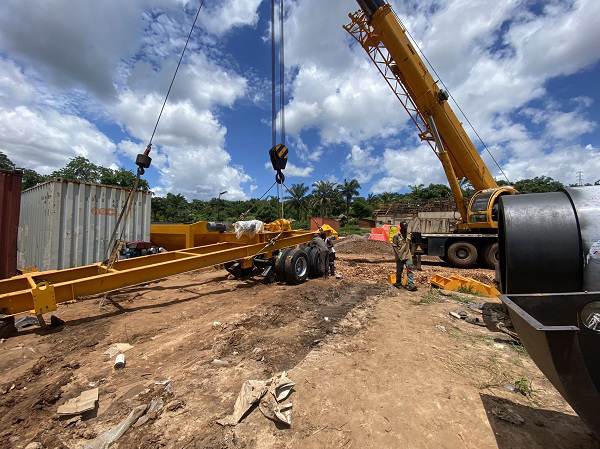
The fine aggregate contains a lot of water and soil: When the river sand contains a lot of water, it will affect the mixing time and temperature of the mixture. When it contains a lot of mud, it will block the cold material bin, causing the hot material bin to wait for material or overflow, and in severe cases, it will affect the oil-stone ratio. When the machine-made sand or stone chips contain a lot of water, it can cause the fine aggregate in the cold material bin to be transported incoherently, and it can also cause the hot material bin to overflow or even overflow from multiple bins; when the fine aggregate contains a lot of soil, it affects the bag dust removal effect. These problems with fine aggregates will eventually lead to unqualified asphalt mixtures.
Mineral powder is too wet or damp: filler mineral powder does not need to be heated, but if the mineral powder is processed using wet materials, or is damp and agglomerated during transportation and storage, the mineral powder cannot fall smoothly when the asphalt mixture is mixed, which can cause the mineral powder to be unmetered or metered slowly, resulting in overflow from the hot material bin or even overflow from multiple bins, and eventually causing the Jinqing mixing station to be forced to shut down due to failure to produce qualified Jinqing mixtures.
Asphalt temperature is too low or too high: When the asphalt temperature is too low, its fluidity becomes poor, which may cause slow or untimely metering, overflow, and uneven adhesion between asphalt and gravel (commonly known as "white material"). When the asphalt temperature is too high, it is easy to "burn", causing the asphalt to become ineffective and unusable, resulting in a waste of raw materials.
Unstable production gradation
Randomly adjust the primary distribution of cold materials: When the raw materials change, some vegetable greenhouse operators adjust the primary distribution of cold materials at will in order to improve productivity. Usually, the following two methods are adopted: one is to adjust the supply of cold materials, which will directly change the primary distribution of cold materials, and also change the gradation of finished materials; the second is to adjust the feed amount of cold material bin, which will affect the screening efficiency of hot aggregates, and the oil-stone ratio will also change accordingly.
Unreasonable mix ratio: The production mix ratio is the mixing ratio of various types of sand and stone in the finished asphalt mixture specified in the design, which is determined by the laboratory. The target mix ratio is set to further guarantee the production mix ratio, and can be adjusted appropriately according to actual conditions during production. If the production mix ratio or the target mix ratio is unreasonable, it will cause the stones in each metering bin of the mixing station to be disproportionate, and it cannot be weighed in time, the mixing cylinder will run idle, and the output will be reduced.
The oil-stone ratio refers to the ratio of the mass of asphalt to sand and gravel in the asphalt mixture, which is an important indicator for controlling the quality of asphalt mixture. If the oil-stone ratio is too large, the road surface will be oily after paving and rolling. If the oil-stone ratio is too small, the concrete material will be loose and will not be formed after rolling.
Other factors: Other factors that lead to unstable production grading include non-standard materials for ore processing, and serious excessive content of soil, dust and powder in sand and stone.
Unreasonable arrangement of vibrating screen
After being screened by the vibrating screen, the hot aggregates are respectively sent to their respective hot material bins. Whether the hot aggregates can be fully screened is related to the arrangement of the vibrating screen and the length of the material flow on the screen. The vibrating screen arrangement is divided into flat screen and inclined screen. When the screen is too flat and the material transported to the screen is excessive, the screening efficiency of the vibrating screen will decrease, and even the screen will be blocked. At this time, the particles that do not pass through the screen holes will have a bunker. If the bunker rate is too large, it will cause an increase in fine aggregate in the mixture, causing the gradation of the asphalt mixture to change.
Improper equipment adjustment and operation
Improper adjustment: manifested in improper setting of dry mixing and wet mixing time, improper opening of mineral powder butterfly valve, and improper adjustment of hopper opening and closing time. The general mixing cycle time of HMA2000 asphalt plant is 45s, the theoretical production capacity is 160t/h, the actual mixing cycle time is 55s, and the actual output is 130t/h. Calculated based on 10 hours of work per day, the daily output can reach 1300t. If the output is increased on this basis, the mixing cycle time must be shortened under the premise of ensuring quality.
If the opening of the mineral powder discharge butterfly valve is adjusted too large, it will cause inaccurate metering and affect the grading; if the opening is too small, it will cause slow metering or no metering and waiting for material. If the fine material content (or water content) in the aggregate is high, the resistance of the material curtain in the drying drum will increase. At this time, if the air volume of the induced draft fan is increased unilaterally, it will cause excessive discharge of fine material, resulting in a lack of fine material in the heated aggregate.
Illegal operation: During the production process, a silo may have material shortage or overflow. In order to increase production, the on-site operator violates the operating procedures and uses the cold material adjustment button in the operation room to add material to other silos, resulting in the mixed asphalt mixture not meeting the technical specifications and the asphalt content fluctuating. The on-site operator lacks professional circuit maintenance knowledge, short-circuits the circuit or conducts illegal debugging, resulting in line blockage and signal failure, which will affect the normal production of asphalt mixture.
High equipment failure rate
Burner failure: poor fuel atomization or incomplete combustion, combustion pipeline blockage and other reasons can all cause the burner combustion efficiency to decrease. Metering system failure: mainly the zero point of the metering system of the asphalt metering scale and the mineral powder metering scale drifts, causing metering errors. Especially for the tendon green metering, if the error is 1kg, it will seriously affect the oil-stone ratio. After the asphalt mixing station has been in production for a period of time, the metering scale will be inaccurate due to changes in ambient temperature and voltage, as well as the influence of accumulated materials in the weighing bucket. Circuit signal failure: inaccurate feeding of each silo may be caused by sensor failure. Under the influence of external environments such as humidity, low temperature, dust pollution and interference signals, electrical components with high sensitivity such as proximity switches, limit switches, magnetic rings, butterfly valves, etc. may work abnormally, thereby affecting the output of the asphalt mixing station. Mechanical failure: if the cylinder, screw conveyor, metering scale is deformed and stuck, the drying drum deviates, the bearing is damaged, the screen mesh is damaged, the mixing cylinder blades, mixing arms, drying drum linings, etc. fall off due to wear, all of which can produce waste and affect normal production.