The productive capacity, accuracy of measurement, automation of the control system, reliability of mechanical transmission and energy consumption rate of asphalt plant are closely related to the installation of the
asphalt mixing plant. For this reason, we must proceed from the current development of asphalt mixing plants, and comprehensively analyze the problems that often occur during the installation of asphalt mixing plants, to ensure the effectiveness and efficiency of asphalt mixing plant installation.
in the progress of production, whether the electrical system is reliable or not, it largely determines the asphalt mixing plant can be produced normally. In addition, it is the quality control of the mixing station. Now it is more popular in the market to configure the quality control system for the mixing station. This greatly improves the construction progress and reduces management costs.
The installation of asphalt mixing plants requires various knowledges and technical supports. Starting from the overall interests, a variety of means are comprehensively adopted for management to ensure the safety and efficiency of the installation. The installation of asphalt mixing plant is of great significance in the construction. Strengthen the installation safety management of asphalt plants is to meet modern needs, which is conductive to adapting to market competition, improving the quality of corporate image, enhancing construction safety, fully ensuring the quality of the project, reducing unnecessary losses and casualties, and promoting the smooth progress of roads construction work.
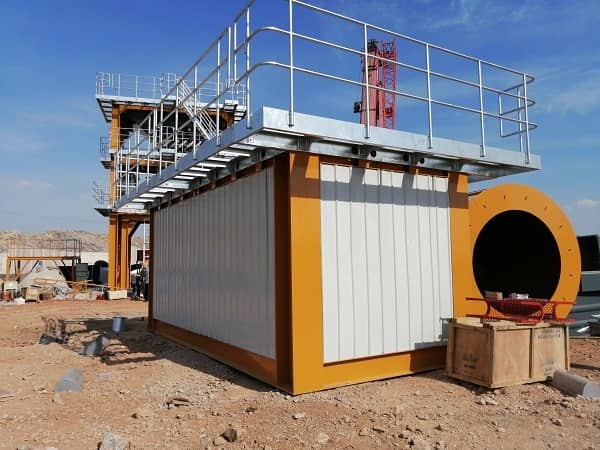
Installation of asphalt mixing plant
1、Installation and Configuration
For the installation of asphalt mixing plant, the first work is the site selection for installation. In the process of site selection for installation, we must fully consider the specific construction conditions and sites, and try to avoid the impact on the surrounding environment and residents. Therefore, environmental protection areas and residential areas should be avoided as much as possible.
It is necessary to conduct comprehensive analysis of the geological conditions of the entire site to ensure the stability and safety of the asphalt mixing plant after installation. Generally, the asphalt plants should be installed in places with relatively hard geology. If the geological conditions are more complex and relatively weak, we need to pave and harden the ground before we can install it. The purpose is to enhance the stability and safety of the installation and avoid the collapse.
In production, the vibrating screen, mixing cylinder and aggregate drying cylinder is the main part of the asphalt mixing plant that they can generate the most intense vibration, which has a certain impact on the entire mixing plant. Therefore, we should especially pay attention to the quality of the aggregate drying drum and the main building, effectively ensure the stability of the main building, and resolutely avoid damage to the entire asphalt mixing plant due to irregular construction activities and inadequate construction management monitoring. Installation poses a security risk.
In addition, long-term mechanical resonance can cause mechanical fatigue of an M30 high-strength screw and make it to break. Therefore, in order to minimize the damage caused by equipment resonance, when we install the foundation of the asphalt plants, we ensured that the same horizontal plane of the foundation does not exceed the range of ±2cm from the elevation.
2. Electrical equipment installation
The installation of electrical equipment is the key content of the installation, so it must be regulated and guided. In order to meet the construction needs of large-volume asphalt concrete mixtures, the power of the electrical equipment of the asphalt mixing plant must be increased. At present, the power consumption has reached 600kW-1000kW.
So, the cross-sectional area of the power supply line will become larger. In addition, more control lines and elements are required during the equipment construction process, which further increases the complexity of the installation. For the installation of electrical equipment, in order to enhance its safety, we generally adopt the method of wiring in cable troughs, which greatly reduces the risk of electric shock accidents happen. First of all, before wiring we need to carefully check the cables, and use the shaker test method to test the cables with larger diameters to ensure that the insulation value of each cable used meets the use standards to avoid short circuits or open circuits. When installing the control system circuit of the asphalt mixing plant, it is necessary to fully consider the influence of electromagnetism on the control system, and adopt various methods to prevent it.
When installing high-power motor cables in asphalt mixing plants, we need to use self-adhesive high-pressure tape to wrap the terminals tightly to prevent the motor vibration terminal from wearing through the tape and
short-circuiting, avoiding the danger of burning the motor. At the same time, the lines of the asphalt mixing plant should pay attention to protection and concealment work, and obvious safety protection warning signs should be set up in places prone to electric shock accidents to avoid line aging. In addition, due to the complexity and variability of construction environmental conditions, we need to install lightning arresters to avoid lightning accidents.
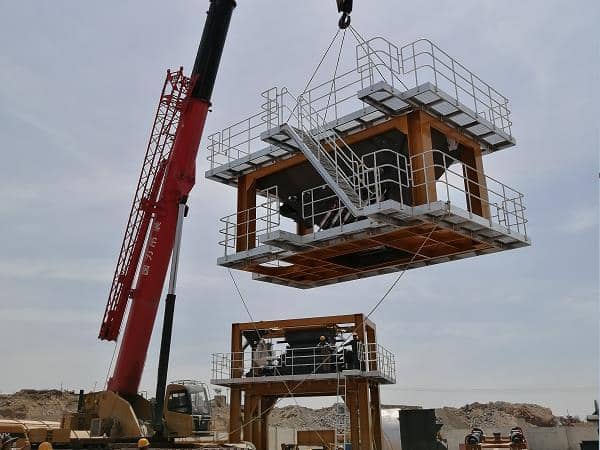
3. the high quality management system
Information management is the installation of a management system on the mixer by the manufacturer. This system is an online real-time monitoring and management platform integrating real-time monitoring, over-standard warning, over-standard processing, data analysis statistics and charts. Through real-time monitoring and collection of data, it is transmitted to In the background of the mixing plant management system, after system processing and analysis, the production chart is intuitively displayed in the background. The supervisor and the owner can log in to view the detailed information of the asphalt concrete, and the production use of
each plate of asphalt concrete will also be recorded and saved for the later stage. Data traceability provides the basis.
And when the production error exceeds the standard, SMS warning will be sent to the owner and the supervisor, so that they can send someone to check the production, which not only saves the time, does not need to
spend all day in the mixing plant, but also can ensure the quality of asphalt concrete. The real-time monitoring and data sharing can also be carried out. The leadership can also monitor the quality of asphalt concrete in real time, and provide data traceability for later problems.
Compared with the management of traditional
asphalt concrete mixing plants, information management can control the quality of asphalt concrete from the source, avoiding the production of unqualified products and the
waste of raw materials. Improve work efficiency, reduce management costs, strengthen construction quality, and ensure construction progress.