Synchronous gravel sealing technology has been promoted and applied at home and abroad. It is an economical and efficient maintenance technology. A synchronous gravel sealing truck is used to spread the asphalt binder (modified asphalt, emulsified asphalt, etc.) and single particle size stones (commonly used 4 to 6 mm, 6 to 10 mm) on the road surface simultaneously, and then pass through the rubber tire roller compactor Or the natural rolling of vehicles forms a wearing layer of asphalt gravel pavement. It can repair road cracks, reduce pavement reflective cracks, and enhance wear. The asphalt film formed on the road surface can well resist the penetration of surface water. It has a short construction period, simple technology, and strong applicability. At present, the synchronous gravel seal layer is mostly used in the preventive maintenance of expressways, ordinary highways, county and township roads, and can also be used in the base wearing layer of new roads and the lower seal layer of reinforced road surfaces. When construction funds are tight, it can be used as a transitional pavement for low-grade highways.
During the specific construction process, this technology mostly focuses on the upper layer, while the upper sealing layer and the wearing layer are often ignored, resulting in a loss of resources. In recent years, technologies such as micro-surfacing and ultrasonic abrasion have continued to emerge. In the process of preventive maintenance of asphalt roads, sealing technology is often used. Commonly used technologies include hot and cold thin layer covering and crack sealing. layers and many other types. The main choice of sealing layer technology for asphalt pavement is the simultaneous asphalt gravel sealing layer. This technology can effectively save the cost of the project. In addition, since this technology was used in France at the end of the 20th century, it has rapidly expanded to the United States and Europe. Countries, including a few in Asia, Africa, and Australia, have also begun to use this technology in specific projects. Data shows that only about 5% of European projects do not use this technology for preventive maintenance of roads. Currently, when using this sealing technology in our country, the following requirements must be met.

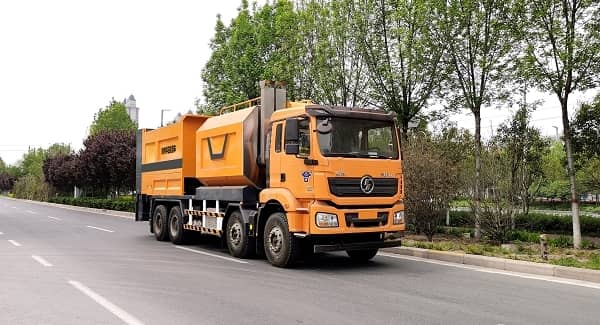
(1) Aggregate requirements. In order to resist the wear and tear of vehicles during highway operation, pavement aggregates need to have sufficient hardness. Especially in the case of heavy traffic flow and vehicle load, the selection of aggregate hardness becomes more prominent; the gradation is usually not mixed with powder. Use a single type of gradation; when selecting aggregates, be sure to use a cube shape to prevent the appearance of pin-type flakes and ensure adequate embedding of the aggregate in the asphalt.
(2) Asphalt. The selection of asphalt must first meet the relevant requirements for asphalt selection set by the highway department. On the basis of meeting the specifications, emulsified, modified, rubber, or ordinary petroleum asphalt can be selected.
(3) Material usage. When using gravel sealing technology for road maintenance, the stones need to be tightly combined, and the stone must be fully covered by asphalt to resist wear and tear on the road surface by the wheels. Once the spreading amount is too much, the asphalt binder will be squeezed out from the gaps in the stones when the vehicle rolls over the road, and an oil surface will appear, thereby reducing the anti-skid and friction index of the road; however, If the amount of stone spread is too small, the stones cannot be effectively bonded, and the stones may be thrown out of the road surface.
In summary, the use of asphalt simultaneous gravel sealing technology has a very important practical effect. It can not only effectively prevent water accumulation on the road, improve the shear strength of the road, but also effectively enhance the performance of the road under low and high temperature conditions. The high crack resistance prevents the asphalt surface from being damaged by erosion or cracking. This technology spreads modified asphalt and compliant stone evenly on the road surface at the same time to ensure an effective combination between the two and enhance the stickiness and strength between the two. In addition, this technology is highly efficient, convenient, saves resources and costs, and has strong feasibility. At the same time, due to the high requirements for related equipment, labor costs are greatly reduced. Therefore, this technical method can be promoted to improve the crack resistance and anti-skid performance of asphalt roads as much as possible.