The brief discussion on four key points in the installation and maintenance of electrical systems in asphalt concrete mixing plants
Asphalt concrete mixing plant is an important equipment in highway construction. It integrates mechanical, electrical and automation technologies. The production capacity of the asphalt concrete mixing plant (hereinafter referred to as asphalt plant), the degree of automation and measurement accuracy of the control system, and the energy consumption rate have now basically become the main factors to measure its performance.
From a broad perspective, the installation of asphalt plants mainly includes foundation production, mechanical metal structure installation, electrical system installation and debugging, asphalt heating and pipeline installation. The mechanical metal structure can be installed in one step under the condition that the asphalt plant foundation is well constructed, and few adjustments and changes will be made in subsequent production. Asphalt heating and pipeline installation mainly serve asphalt heating. The installation workload mainly depends on the equipment for storing and heating asphalt. In production, the reliability of electrical transmission and control systems is one of the important factors affecting the normal production of asphalt plants. This article only focuses on the installation and maintenance of the electrical control system of the asphalt mixer. Combined with the actual situation on site, it briefly discusses the four key points of the installation and maintenance of the electrical system of the asphalt mixer, and discusses and learns with peers.
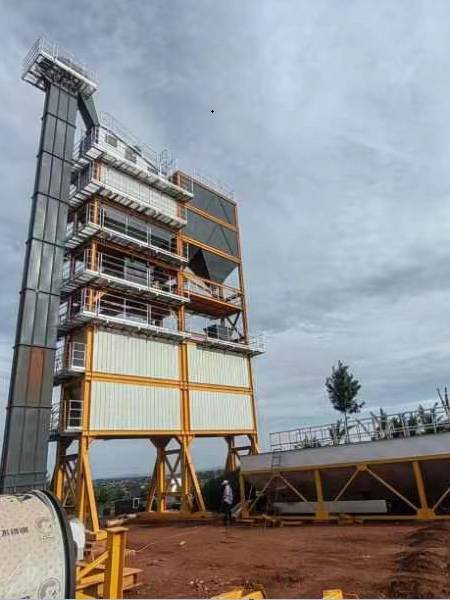
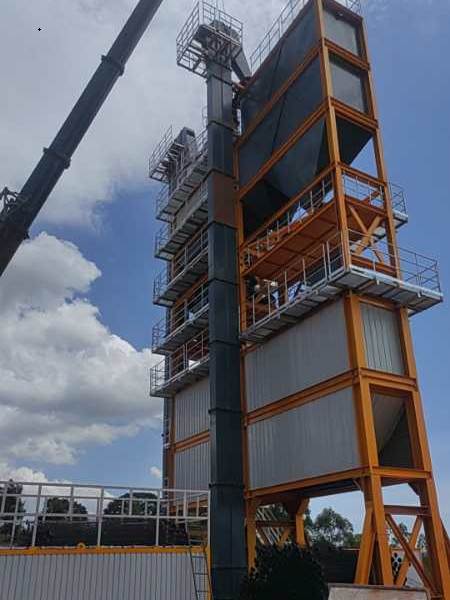
(1) Familiar with the system, familiar with the principles, reasonable wiring, and good wiring connections
Regardless of whether the asphalt plant is installed or moved to a new construction site, technicians and maintenance personnel engaged in electrical installation must first be familiar with the control mode and principles of the entire electrical system based on the working process of the asphalt mixer, as well as the distribution of the system and some key control components. The specific function of the cylinder makes the installation of the cylinder relatively easy.
When wiring, according to the drawings and the installation positions of electrical components, they are concentrated from the peripheral part to each control unit or from the periphery to the control room. Appropriate paths must be selected for the layout of the cables, and weak current cables and strong current signal cables are required to be arranged in separate slots.
The electrical system of the mixing plant includes strong current, weak current, AC, DC, digital signals, and analog signals. In order to ensure that these electrical signals can be transmitted effectively and reliably, each control unit or electrical component can output correct control signals in a timely manner. And it can reliably drive each actuator, and the reliability of the connection of the electrical circuit has a great influence. Therefore, during the installation process, it is necessary to ensure that the connections at each wiring joint are reliable and the electrical components are installed and tightened.
The main control units of asphalt mixers generally use industrial computers or PLCs (programmable logic controllers). Their control processes are basically based on the internal circuit detecting electrical input signals that meet certain logical relationships, and then promptly outputting signals that meet certain logical relationships. Electrical signals drive relays or other electrical units or components. The operation of these relatively precise components is generally relatively reliable. If a fault occurs during operation or debugging, first check whether all relevant input signals are input in place, and then check whether all required output signals are available and whether they are output according to logical requirements. Under normal circumstances, as long as the input signal is valid and reliable and meets the logic requirements, the output signal will be output according to the internal program design requirements, unless the wiring head (wiring plug-in board) is loose or the peripheral components and circuits related to these control units are faulty. Of course, under certain special circumstances, the internal components of the unit may be damaged or a circuit board may fail.
(2) Do a good job in grounding (or zero connection) protection of the electrical system, and do a good job in lightning protection grounding of the entire machine and sensor shielding grounding
From the perspective of the grounding system of the power supply, if the power supply adopts the TT system, when installing the mixing station, the metal frame of the mixing station and the electrical cabinet shell of the control room must be reliably grounded for protection. If the power supply adopts TN-C standard, when we install the mixing station, we must reliably ground the metal frame of the mixing station and the electrical cabinet shell of the control room and reliably connect to zero. In this way, on the one hand, the conductive frame of the mixing station can be realized. The protection is connected to zero, and the neutral line of the electrical system of the mixing station is repeatedly grounded. If the power supply adopts TN-S (or TN-C-S) standard, when we install the mixing station, we only need to reliably connect the metal frame of the mixing station and the electrical cabinet shell of the control room to the protection line of the power supply. Regardless of the power supply system, the grounding resistance of the grounding point must not be greater than 4Ω.
In order to prevent the mixing station from being harmed by lightning strikes, when installing the mixing station, a lightning rod must be installed at the point of the mixing station, and all components of the mixing station must be within the effective protection zone of the lightning rod. The grounding down conductor of the lightning rod should be a copper wire with a cross-section of not less than 16mm2 and an insulated protective sheath. The grounding point should be located at least 20m away from other grounding points of the mixing station in a place without pedestrians or facilities, and the grounding point should be guaranteed to be The ground resistance is below 30Ω.
When installing the mixing station, the shielded wires of all sensors must be reliably grounded. This grounding point can also connect the grounding down wire of the control unit. However, this grounding point is different from the protective grounding point and anti-intrusion protection mentioned above. Lightning grounding point, this grounding point should be at least 5m away from the protective grounding point in a straight line, and the grounding resistance should not be greater than 4Ω.
(3) Carry out debugging work carefully
When the mixing plant is first assembled, debugging may require a lot of effort and time, because many problems may be found during debugging, such as wiring errors, inappropriate component or control unit parameter settings, inappropriate component installation locations, component damage, etc. The reason, the specific reason, must be judged and corrected or adjusted based on the drawings, actual conditions and inspection results.
After the main body of the mixing station and the electrical system are installed in place, careful debugging work must be done. First, start with a single motor and a single action to manually control the no-load test. If there is a problem, check whether the circuit and electrical components are normal. If a single motor has a single action, try the operation. If everything is normal, you can enter the manual or automatic control no-load test of some units. If everything is normal, then enter the automatic no-load test of the whole machine. After completing these tasks, do a full machine load test. After the debugging work is completed, it can be said that the installation work of the mixing station is basically completed and the asphalt mixing station has production capacity.