Přeměna kameniva a bitumenu na asfalt pro stavbu silnic vyžaduje proces tepelného míchání. K tomu je nezbytná obalovna asfaltu. Účelem míchačky asfaltu je mísit kamenivo a asfalt dohromady při zvýšené teplotě za vzniku homogenní směsi pro asfaltové vozovky. Použitým kamenivem může být jeden materiál, kombinace hrubého a jemného kameniva, s minerálním plnivem nebo bez něj. Použitým pojivovým materiálem je normálně asfalt, ale může to být asfaltová emulze nebo jeden z řady modifikovaných materiálů. Do směsi mohou být také začleněny různé přísady, včetně tekutých a práškových materiálů.
V současné době existují tři více populární typy míchacích zařízení na horký asfalt: vsázková směs, bubnová směs a kontinuální bubnová směs. Všechny tři typy slouží ke stejnému konečnému účelu a asfaltová směs by měla být v podstatě podobná bez ohledu na typ zařízení použitého k její výrobě. Tyto tři typy zařízení se však liší provozem a tokem materiálů, jak je popsáno v následujících částech.
Batch Mix Asphalt Plant
obalovna asfaltu je klíčovým vybavením každé silniční stavební společnosti. Jakýkoli provoz závodu na výrobu asfaltových směsí má mnoho funkcí. Asphalt Batch závody vyrábějí horkou směs asfaltu v sérii dávek. Tyto závody na výrobu vsázkových směsí produkují horký asfalt v kontinuálním procesu. Toto zařízení je také možné upravit a použít pro výrobu horké směsi asfaltu s použitím recyklovaného materiálu. Závody vsázkového typu mají variace, které umožňují přidání RAP (Reclaimed Asfalt pavement). Komponenty standardního závodu na míchání asfaltových směsí jsou: systém studeného plnění, systém dodávky asfaltu, sušička kameniva, míchací věž a systém kontroly emisí. Věž dávkovacího zařízení se skládá z horkého elevátoru, prosévací plošiny, horkých zásobníků, násypky na vážení, navažovacího kbelíku asfaltu a mlýna. Kamenivo použité ve směsi se odstraní ze skladů a umístí do samostatných zásobníků na studené krmivo. Kamenivo různých velikostí je ze zásobníků dávkováno kombinací velikosti otvoru brány na dně každého zásobníku a rychlosti dopravního pásu pod zásobníkem. Obecně platí, že podávací pás pod každým zásobníkem ukládá kamenivo na sběrný dopravník umístěný pod všemi zásobníky pro studené krmivo. Kamenivo je dopravováno sběrným dopravníkem a převáděno na zavážecí dopravník. Materiál na vsázkovém dopravníku je následně dopravován do sušárny kameniva.
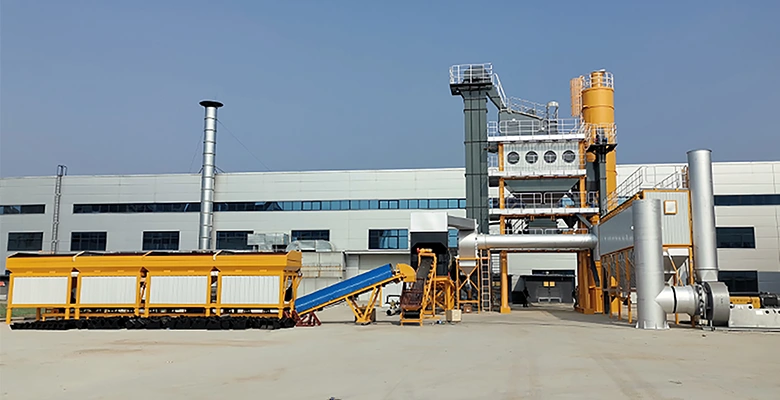
Sušička pracuje na principu protiproudu. Agregát je zaváděn do sušičky na horním konci a je posouván dolů bubnem jak rotací bubnu (gravitační tok), tak uspořádáním letu uvnitř rotačního sušiče. Hořák je umístěn na spodním konci sušárny a výfukové plyny ze spalovacího a sušícího procesu se pohybují směrem k hornímu konci sušárny, proti (proti) proudu agregátu. Při převalování agregátu výfukovými plyny se materiál zahřívá a suší. Vlhkost se odstraňuje a odvádí ze sušičky jako součást proudu výfukových plynů.
Horký, suchý agregát je pak vypouštěn ze sušičky na spodním konci. Horké kamenivo je obvykle dopravováno na vrchol míchací věže zařízení korečkovým elevátorem. Po vypuštění z elevátoru agregát normálně prochází sadou vibračních sít do typicky jedné ze čtyř horkých skladovacích nádrží. Nejjemnější kamenivo prochází přímo přes všechna síta do horkého zásobníku č. 1; hrubší částice agregátu jsou odděleny
různě velké síta a uloženy do jednoho z dalších horkých zásobníků. Separace kameniva do horkých zásobníků závisí na velikosti otvorů v sítu, který je použit v sítové desce a na gradaci kameniva v zásobníkech pro studený přívod.
Zahřátý, vysušený a upravený agregát se udržuje v horkých zásobnících, dokud není vypuštěn z uzávěru na dně každého zásobníku do násypky pro vážení. Správný podíl každého kameniva je určen hmotností.
Současně s dávkováním a vážením kameniva je asfalt čerpán z jeho skladovací nádrže do samostatné vyhřívané navažovací nádoby umístěné na věži těsně nad mlýnem. Správné množství materiálu se naváží do kbelíku a drží, dokud se nevyprázdní do mlýna. Kamenivo z násypky je vyprázdněno do dvouhřídelového válečkového mlýna a různé frakce kameniva se spolu mísí po velmi krátkou dobu — obvykle méně než 5 sekund. Po této krátké době promíchání za sucha se asfalt z navažovací nádoby vysype.
do pugmill a začíná čas mokrého míchání. Doba míchání pro smíchání asfaltu s kamenivem by neměla být delší než doba potřebná k úplnému pokrytí částic kameniva tenkým filmem asfaltového materiálu – obvykle v rozmezí 25 až 35 sekund, se spodní hranicí tohoto rozmezí. je pro pugmill, který je v dobrém stavu. Velikost vsázky smíchané v pugmillu může být v rozmezí 1,81 až 5,44 tun (2 až 6 tun).
Po dokončení míchání se otevřou dvířka na dně mlýna a směs se vypustí do tažného vozidla nebo do dopravního zařízení, které dopraví směs do sila, ze kterého budou nakládány nákladní vozy dávkovým způsobem. U většiny vsádkových závodů je doba potřebná k otevření vrátek mlýna a vypuštění směsi přibližně 5 až 7 sekund. Celková doba míchání (doba suchého míchání + doba míchání za mokra + doba vypouštění směsi) pro dávku může být jen asi 40 sekund, ale obvykle je celková doba míchání asi 45 sekund.
Zařízení je vybaveno zařízeními pro kontrolu emisí, která zahrnují primární i sekundární sběrný systém. Jako primární sběrač se běžně používá suchý kolektor nebo knockout box. Jako sekundární sběrný systém lze použít buď systém mokré pračky, nebo častěji suchý látkový filtrační systém (baghouse) k odstranění pevných částic z výfukových plynů, které proudí ze sušičky a posílají čistý vzduch do atmosféry komínem. .
Pokud je RAP zapracován do směsi, je umístěn do samostatného zásobníku na studené krmivo, ze kterého je dodáván do závodu. RAP lze přidat k novému agregátu v jednom ze tří umístění: ve spodní části horkého výtahu; horké koše; nebo nejčastěji vážní násypka. Přenos tepla mezi přehřátým novým kamenivem a regenerovaným materiálem začíná, jakmile se oba materiály dostanou do kontaktu, a pokračuje během procesu míchání v mlýně.
Drum Mix Asphalt Plant
Ve srovnání s dávkovým typem má bubnová asfaltárna menší tepelné ztráty, nižší pracovní výkon, žádné přetečení, méně létajícího prachu a stabilní regulaci teploty. Řídicí systém automaticky upravuje průtok asfaltu podle průtoku kameniva a přednastaveného poměru asfalt-kamenivo, aby byl zajištěn přesný proporcionální výstup. Závod na míchání asfaltových bubnů je typy závodů, které jsou kategorizovány jako závody na kontinuální míchání, vyrábějící horký asfalt v nepřetržitém procesu.
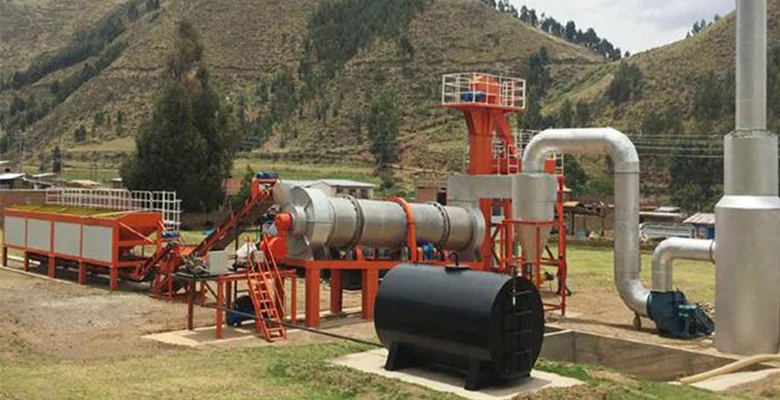
Typicky jsou systémy studeného plnění na HMA vsádkových a bubnových míchacích zařízeních podobné. Každý se skládá ze zásobníků na studené krmivo, podávacích dopravníků, sběrného dopravníku a zavážecího dopravníku. Na většině zařízení na míchání bubnů a na některých dávkových zařízeních je v určitém okamžiku do systému zahrnuto skalpovací síto. Pokud se do závodu přivádí také RAP za účelem výroby recyklované směsi, je pro manipulaci s dalším materiálem nezbytný další zásobník nebo zásobníky na krmení za studena, podávací pás a/nebo sběrací dopravník, skalpovací síto a zavážecí dopravník. Zařízení na bubnové míchačky se skládají z pěti hlavních součástí: systém podávání za studena, systém dodávky asfaltu, bubnová míchačka, vyrovnávací nebo skladovací sila a zařízení pro kontrolu emisí.
Zásobníky na krmení za studena se používají k dávkování materiálu rostlině. Pod každým zásobníkem je použit posuvný pás s proměnnou rychlostí. Množství kameniva odebíraného z každého zásobníku tak může být řízeno jak velikostí otvoru brány, tak rychlostí podávacího pásu, aby bylo zajištěno přesné dodávání materiálů různé velikosti. Kamenivo na každém podávacím pásu je ukládáno na sběrný dopravník, který běží pod všemi zásobníky na studené krmivo. Spojený materiál normálně prochází přes skalpovací síto a poté se přenese na zavážecí dopravník pro dopravu do bubnového mísiče.
Zavážecí dopravník je vybaven dvěma zařízeními, která se používají ke zjišťování množství kameniva dodávaného do závodu: vážní most pod dopravním pásem měří hmotnost kameniva, které přes něj prochází, a senzor určuje rychlost pásu. Tyto dvě hodnoty se používají k výpočtu mokré hmotnosti kameniva v tunách (tunách) za hodinu, vstupujícího do bubnového mísiče. Počítač závodu, s množstvím vlhkosti v kamenivu poskytnutým jako vstupní hodnotou, převádí mokrou hmotnost na suchou, aby určil správné množství asfaltu potřebného ve směsi.
Konvenční bubnová míchačka je systém s paralelním prouděním – výfukové plyny a agregát se pohybují stejným směrem. Hořák je umístěn na horním konci (konec vstupu kameniva) bubnu. Agregát vstupuje do bubnu buď ze šikmého skluzu nad hořákem nebo na Slinger dopravníku pod hořákem. Agregát se pohybuje dolů po bubnu kombinací gravitace a konfigurace unášečů umístěných uvnitř bubnu. Při pohybu se kamenivo ohřívá a odstraňuje vlhkost. V blízkosti středu délky bubnu je vytvořen hustý závoj z kameniva, který napomáhá procesu přenosu tepla.
Pokud je k novému kamenivu přidán RAP, je ukládán z vlastního zásobníku pro studený krmení a systému sběrného/nakládacího dopravníku do vstupu umístěného blízko středu délky bubnu (systém děleného krmení). Při tomto procesu je regenerovaný materiál chráněn před vysokoteplotními výfukovými plyny závojem nového agregátu před vstupním bodem RAP. Při použití směsí s vysokým obsahem RAP je pravděpodobnější, že se RAP během procesu přehřeje. To může mít za následek únik kouře z bubnu nebo poškození RAP.
Nové kamenivo a regenerovaný materiál, pokud je použit, se pohybují společně do zadní části bubnu. Asfalt je čerpadlem vytahován ze skladovací nádrže a přiváděn přes metr, kde je určen správný objem asfaltu. Pojivový materiál je pak přiváděn potrubím do zadní části míchacího bubnu, kde je asfalt injektován na kamenivo. K povlékání kameniva dochází, když se materiály převalují dohromady a pohybují se na výstupní konec bubnu. Minerální plnivo nebo jemné částice z pytlů nebo obojí se také přidávají do zadní části bubnu, buď těsně před přidáním asfaltu nebo ve spojení s ním.
Asfaltová směs je ukládána do dopravního zařízení (vlečný lamelový dopravník, pásový dopravník nebo korečkový elevátor) pro dopravu do skladovacího sila. Silo převádí kontinuální tok směsi na dávkový tok pro vypouštění do tažného vozidla.
Obecně se v bubnovém míchacím zařízení používá stejný typ zařízení pro kontrolu emisí jako na vsádkovém závodě. Lze použít primární suchý kolektor a buď systém mokré pračky, nebo sekundární kolektor baghouse. Pokud je použit systém mokré pračky, shromážděné jemné částice nemohou být recyklovány zpět do směsi a jsou plýtvány; v případě použití pytlíku lze nasbírané jemné částice zcela nebo zčásti vrátit do míchacího bubnu nebo je lze vyplýtvat.
Continuous Mix Asphalt Plant
V kontinuálních provozech nedochází k přerušení výrobního cyklu, protože rytmus výroby není rozdělen do dávek. Míchání materiálu probíhá uvnitř bubnu sušičky, který je podlouhlý, protože suší a zároveň míchá materiál. Protože zde nejsou žádné směšovací věže ani výtahy, je systém značně zjednodušen s následným snížením nákladů na údržbu. Absence síta však vyžaduje přesné kontroly na začátku výrobního cyklu, před tím, než je kamenivo přiváděno do sušičky a předtím, než je následně vypouštěno ze sušičky jako asfalt.
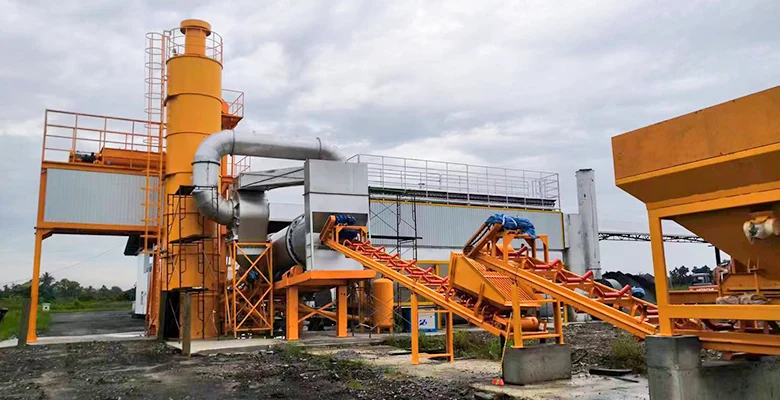
AGREGÁTNÍ MĚŘENÍ
Podobně jako u dávkových míchaček asfaltu,
Výrobní cyklus kontinuálních zařízení také začíná studenými dávkovači, kde je kamenivo obecně dávkováno podle objemu; v případě potřeby může být odsavač písku vybaven vážním pásem pro dávkování.
Řízení celkové hmotnosti primárních agregátů se však provádí ve dvou různých fázích výrobního cyklu ve dvou různých závodech. U kontinuálního typu je před přivedením vlhkého kameniva do bubnu sušičky použit podávací pás, kde se obsah vlhkosti nastavuje ručně, aby bylo možné odečíst hmotnost vody. Proto je nesmírně důležité, aby obsah vlhkosti v kamenivu, zejména písku, měl konstantní hodnotu, která je neustále sledována častými laboratorními testy.
MĚŘENÍ BITUMENU
V kontinuálních provozech je dávkování bitumenu obecně volumetrické přes litrové počítadlo za napájecím čerpadlem. Alternativně je možné nainstalovat počítadlo hmoty, což je nezbytná volba při použití modifikovaného asfaltu, který vyžaduje časté čištění.
Dávkování plniva
V kontinuálních provozech je dávkovací systém normálně objemový, používající šneky s proměnnou rychlostí, které nahradily předchozí pneumatický dávkovací systém.
Ovládací panel je typu PLC ve všech našich exportních závodech. Jedná se o obrovskou přidanou hodnotu, protože můžeme přizpůsobit PLC podle našich požadavků. Bubnová míchačka vybavená PLC panelem je jiný stroj než provoz s mikroprocesorovým panelem. PLC panel je také bezúdržbový ve srovnání s mikroprocesorovým panelem. Vždy věříme, že zákazníkům dáváme to nejlepší, aby si udrželi náskok před konkurencí. Ne všichni výrobci a vývozci zařízení na výrobu asfaltových bubnů nabízejí zařízení s PLC panelem.
Provádí se předběžné testování všech závodů, aby bylo zajištěno, že vše, co opustí naši továrnu, bude připraveno k provedení s menšími problémy na místě.
Sinoroader má více než 30 let výrobních zkušeností a produkt, který je podpořen profesionálním servisem a levnějšími náhradními díly, abyste si své vybavení vážili a používali ho po mnoho let.