Drei Arten von Heißasphaltmischanlagen erfreuen sich derzeit größerer Beliebtheit
Die Umwandlung von Zuschlagstoffen und Bitumen in Asphalt für den Straßenbau erfordert einen thermischen Mischprozess. Eine Asphaltmischanlage ist hierfür unverzichtbar. Der Zweck einer Asphaltmischanlage besteht darin, Gesteinskörnung und Asphalt bei erhöhter Temperatur miteinander zu vermischen, um eine homogene Asphaltmischung zu erzeugen. Als Gesteinskörnung kann ein einzelnes Material, eine Kombination aus groben und feinen Gesteinskörnungen mit oder ohne mineralischem Füllstoff verwendet werden. Das verwendete Bindemittelmaterial ist normalerweise Asphalt, es kann sich jedoch auch um eine Asphaltemulsion oder eines von verschiedenen modifizierten Materialien handeln. Der Mischung können auch verschiedene Zusatzstoffe, einschließlich flüssiger und pulverförmiger Materialien, beigemischt werden.
Derzeit gibt es drei weitere beliebte Arten von Heißasphaltmischanlagen: Chargenmischung, Trommelmischung und kontinuierliche Trommelmischung. Alle drei Typen dienen letztendlich demselben Zweck und die Asphaltmischung sollte im Wesentlichen ähnlich sein, unabhängig von der Art der Anlage, die zu ihrer Herstellung verwendet wird. Die drei Anlagentypen unterscheiden sich jedoch in der Funktionsweise und im Materialfluss, wie in den folgenden Abschnitten beschrieben wird.
Batch-Mix-Asphaltanlage
Eine Asphaltmischanlage ist eine Schlüsselausrüstung für jedes Straßenbauunternehmen. Jeder Betrieb einer Asphaltmischanlage hat viele Funktionen. Asphaltmischanlagen produzieren Heißasphalt in mehreren Chargen. Diese Batch-Mix-Anlagen produzieren im kontinuierlichen Prozess Heißasphalt. Es ist auch möglich, diese Ausrüstung umzubauen und für die Herstellung von Heißasphalt aus recyceltem Material zu verwenden. Bei Batch-Anlagen gibt es Varianten, die die Zugabe von RAP (Reclaimed Asphalt Pavement) ermöglichen. Die Komponenten einer Standard-Asphalt-Chargenmischanlage sind: das Kaltzufuhrsystem, das Asphaltversorgungssystem, der Zuschlagstofftrockner, der Mischturm und das Emissionskontrollsystem. Der Turm der Gemengeanlage besteht aus einem Heißaufzug, einem Siebdeck, Heißbunkern, einem Wiegebehälter, einem Asphaltwiegekübel und einer Pugmill. Der in der Mischung verwendete Zuschlagstoff wird aus den Lagerbeständen entnommen und in einzelne Kaltfutterbehälter gegeben. Zuschlagstoffe unterschiedlicher Größe werden aus ihren Behältern durch eine Kombination aus der Größe der Toröffnung am Boden jedes Behälters und der Geschwindigkeit des Förderbandes unter dem Behälter dosiert. Im Allgemeinen legt ein Zufuhrband unter jedem Behälter die Zuschlagstoffe auf einem Sammelförderer ab, der sich unter allen Kaltaufgabebehältern befindet. Das Aggregat wird vom Sammelband transportiert und auf ein Beschickungsband übergeben. Anschließend wird das Material auf dem Beschickungsband zum Zuschlagstofftrockner befördert.
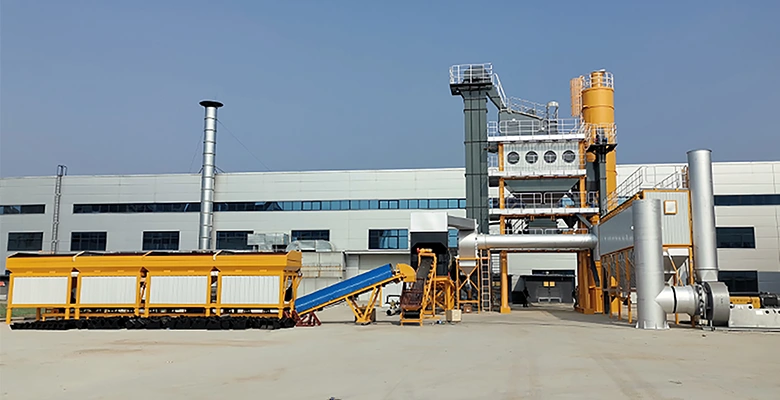
Der Trockner arbeitet im Gegenstromprinzip. Das Aggregat wird am oberen Ende in den Trockner eingeführt und sowohl durch die Trommelrotation (Schwerkraftströmung) als auch durch die Flugkonfiguration im rotierenden Trockner nach unten bewegt. Der Brenner befindet sich am unteren Ende des Trockners und die Abgase aus dem Verbrennungs- und Trocknungsprozess bewegen sich entgegen (gegen) der Strömung des Aggregats zum oberen Ende des Trockners. Während das Aggregat durch die Abgase wirbelt, wird das Material erhitzt und getrocknet. Feuchtigkeit wird entfernt und als Teil des Abgasstroms aus dem Trockner transportiert.
Das heiße, trockene Aggregat wird dann am unteren Ende aus dem Trockner ausgetragen. Der heiße Zuschlagstoff wird üblicherweise mit einem Becherwerk nach oben in den Mischturm der Anlage transportiert. Bei der Entladung aus dem Elevator gelangt das Zuschlagstoff normalerweise durch eine Reihe von Vibrationssieben in typischerweise einen von vier Warmlagerbehältern. Das feinste Zuschlagstoffmaterial gelangt direkt durch alle Siebe in den Heißbehälter Nr. 1; Die gröberen Aggregatpartikel werden dadurch abgetrennt
Siebe unterschiedlicher Größe werden in einen der anderen Heißbehälter abgelegt. Die Trennung der Zuschlagstoffe in den Warmbehältern hängt von der Größe der Öffnungen im Sieb, das im Siebdeck verwendet wird, und der Abstufung der Zuschlagstoffe in den Kaltbehältern ab.
Das erhitzte, getrocknete und in der Größe geänderte Zuschlagstoff wird in den heißen Behältern aufbewahrt, bis es durch ein Tor am Boden jedes Behälters in einen Wiegetrichter entladen wird. Der richtige Anteil jedes Zuschlagstoffs wird durch das Gewicht bestimmt.
Während das Zuschlagstoff dosiert und gewogen wird, wird der Asphalt aus seinem Lagertank in einen separaten beheizten Wiegebehälter gepumpt, der sich auf dem Turm direkt über dem Pugmill befindet. Die richtige Materialmenge wird in den Eimer eingewogen und dort aufbewahrt, bis er in die Pugmill entleert wird. Der Zuschlagstoff im Wiegebehälter wird in eine Doppelwellen-Pugmill entleert und die verschiedenen Zuschlagstofffraktionen werden für einen sehr kurzen Zeitraum – normalerweise weniger als 5 Sekunden – miteinander vermischt. Nach dieser kurzen Trockenmischzeit wird der Asphalt aus dem Wiegeeimer ausgetragen.
in die Pugmill, und die Nassmischzeit beginnt. Die Mischzeit zum Mischen des Asphalts mit dem Zuschlagstoff sollte nicht länger sein als die Zeit, die erforderlich ist, um die Zuschlagstoffpartikel vollständig mit einem dünnen Film des Asphaltmaterials zu überziehen – normalerweise im Bereich von 25 bis 35 Sekunden, wobei das untere Ende dieses Bereichs liegt Es handelt sich um eine Pugmill, die in gutem Zustand ist. Die Größe der in der Pugmill gemischten Charge kann im Bereich von 1,81 bis 5,44 Tonnen (2 bis 6 Tonnen) liegen.
Wenn das Mischen abgeschlossen ist, werden die Tore am Boden der Mischmühle geöffnet und die Mischung in das Transportfahrzeug oder in eine Fördervorrichtung entladen, die die Mischung zu einem Silo transportiert, von dem aus LKWs schubweise beladen werden. Bei den meisten Chargenanlagen beträgt die Zeit, die zum Öffnen der Pugmill-Tore und zum Entleeren der Mischung benötigt wird, etwa 5 bis 7 Sekunden. Die Gesamtmischzeit (Trockenmischzeit + Nassmischzeit + Mischentladezeit) für eine Charge kann nur etwa 40 Sekunden betragen, typischerweise beträgt die Gesamtmischzeit jedoch etwa 45 Sekunden.
Die Anlage ist mit Emissionskontrollgeräten ausgestattet, die sowohl primäre als auch sekundäre Sammelsysteme umfassen. Als Primärkollektor wird üblicherweise ein Trockenkollektor oder eine Knockout-Box verwendet. Als sekundäres Sammelsystem kann entweder ein Nasswäschersystem oder häufiger ein Trockengewebefiltersystem (Baghouse) verwendet werden, um Partikel aus den Abgasen zu entfernen, die aus dem Trockner strömen und saubere Luft durch den Schornstein in die Atmosphäre abgeben .
Wenn RAP in die Mischung eingearbeitet wird, wird es in einen separaten Kaltfutterbehälter gegeben, von wo aus es an die Anlage geliefert wird. Das RAP kann dem neuen Aggregat an einer von drei Stellen hinzugefügt werden: am Boden des Heißaufzugs; die heißen Behälter; oder am häufigsten der Wiegetrichter. Die Wärmeübertragung zwischen dem überhitzten Neuzuschlagstoff und dem wiedergewonnenen Material beginnt, sobald die beiden Materialien in Kontakt kommen, und setzt sich während des Mischvorgangs in der Pugmill fort.
Trommelmischasphaltanlage
Im Vergleich zum Batch-Typ weisen Trommelmischasphaltanlagen weniger Wärmeverluste, eine geringere Arbeitsleistung, kein Überlaufen, weniger Staubflug und eine stabile Temperaturkontrolle auf. Das Steuersystem passt die Asphaltdurchflussrate automatisch entsprechend der Zuschlagstoffdurchflussrate und dem voreingestellten Asphalt-Zuschlagstoff-Verhältnis an, um eine präzise proportionale Leistung zu gewährleisten. Bei Asphalttrommelmischanlagen handelt es sich um Anlagentypen, die als kontinuierliche Mischanlagen kategorisiert werden und heiße Asphaltmischungen in einem kontinuierlichen Prozess produzieren.
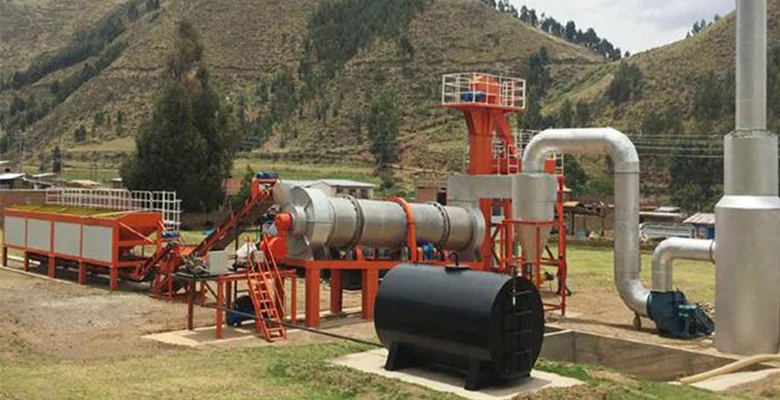
Typischerweise sind die Kaltbeschickungssysteme bei HMA-Batch- und Trommelmischanlagen ähnlich. Jedes besteht aus Kaltfutterbehältern, Zuführbändern, einem Sammelband und einem Beschickungsband. Bei den meisten Trommelmischanlagen und einigen Batch-Anlagen ist irgendwann ein Vorsieb in das System integriert. Wenn der Anlage auch Raps zugeführt wird, um eine recycelte Mischung herzustellen, sind ein oder mehrere zusätzliche Kaltfutterbehälter, ein Zuführband und/oder ein Sammelförderer, ein Grobsieb und ein Beschickungsförderer erforderlich, um das zusätzliche Material zu verarbeiten. Trommelmischanlagen bestehen aus fünf Hauptkomponenten: dem Kaltbeschickungssystem, dem Asphaltversorgungssystem, dem Trommelmischer, den Puffer- oder Lagersilos und der Emissionskontrollausrüstung.
Die Kaltfutterbehälter dienen der Dosierung des Materials in die Pflanze. Unter jedem Behälter wird ein Zufuhrband mit variabler Geschwindigkeit verwendet. Die aus jedem Behälter entnommene Zuschlagstoffmenge kann somit sowohl durch die Größe der Toröffnung als auch durch die Geschwindigkeit des Zufuhrbandes gesteuert werden, um eine genaue Lieferung der unterschiedlich großen Materialien zu gewährleisten. Die Zuschlagstoffe auf jedem Zufuhrband werden auf einem Sammelförderer abgelegt, der unter allen Kaltaufgabebehältern verläuft. Das kombinierte Material wird normalerweise durch ein Grobsieb geleitet und dann auf ein Beschickungsband für den Transport zum Trommelmischer übertragen.
Das Beschickungsband ist mit zwei Vorrichtungen ausgestattet, die zur Bestimmung der an die Anlage gelieferten Zuschlagstoffmenge dienen: Eine Wägebrücke unter dem Förderband misst das Gewicht des darüber laufenden Zuschlagstoffs und ein Sensor ermittelt die Geschwindigkeit des Bandes. Diese beiden Werte werden verwendet, um das Nassgewicht des Zuschlagstoffs in Tonnen (Tonnen) pro Stunde zu berechnen, der in den Trommelmischer gelangt. Der Anlagencomputer wandelt mit der als Eingabewert bereitgestellten Feuchtigkeitsmenge im Zuschlagstoff das Nassgewicht in Trockengewicht um, um die richtige Asphaltmenge zu bestimmen, die in der Mischung benötigt wird.
Der herkömmliche Trommelmischer ist ein Parallelstromsystem – die Abgase und das Aggregat bewegen sich in die gleiche Richtung. Der Brenner befindet sich am oberen Ende (Aggregateinlass) der Trommel. Das Zuschlagstoff gelangt entweder über eine geneigte Rutsche über dem Brenner oder über ein Slinger-Förderband unter dem Brenner in die Trommel. Das Aggregat wird durch eine Kombination aus Schwerkraft und der Konfiguration der im Inneren der Trommel befindlichen Mitnehmer in der Trommel nach unten bewegt. Während der Bewegung wird das Aggregat erhitzt und die Feuchtigkeit entfernt. Nahe der Mitte der Trommellänge wird ein dichter Aggregatschleier aufgebaut, der den Wärmeübertragungsprozess unterstützt.
Wenn dem neuen Zuschlagstoff RAP hinzugefügt wird, wird es aus seinem eigenen Kaltaufgabebehälter und Sammel-/Ladefördersystem in einen Einlass nahe der Mitte der Trommellänge abgelegt (Split-Feed-System). Bei diesem Verfahren wird das zurückgewonnene Material durch den Schleier aus neuem Aggregat vor dem RAP-Eintrittspunkt vor den Abgasen mit hoher Temperatur geschützt. Bei der Verwendung von Mischungen mit hohem RAP-Anteil ist die Wahrscheinlichkeit größer, dass das RAP dabei überhitzt. Dies kann dazu führen, dass Rauch aus der Trommel austritt oder das RAP beschädigt wird.
Der neue Zuschlagstoff und das wiedergewonnene Material, sofern verwendet, bewegen sich gemeinsam in den hinteren Teil der Trommel. Der Asphalt wird mit einer Pumpe aus dem Lagertank angesaugt und durch einen Zähler geleitet, wo das richtige Asphaltvolumen bestimmt wird. Das Bindemittel wird dann durch ein Rohr in die Rückseite der Mischtrommel gefördert, wo der Asphalt auf den Zuschlagstoff gespritzt wird. Die Beschichtung des Zuschlagstoffs erfolgt, wenn die Materialien zusammengewirbelt und zum Austragsende der Trommel bewegt werden. Mineralfüllstoffe oder Feinstoffe aus der Baggeranlage oder beides werden ebenfalls in die Rückseite der Trommel gegeben, entweder unmittelbar vor oder in Verbindung mit der Zugabe des Asphalts.
Das Asphaltgemisch wird in einer Fördervorrichtung (einem Schleppplattenförderer, einem Bandförderer oder einem Becherwerk) abgelegt und zu einem Lagersilo transportiert. Das Silo wandelt den kontinuierlichen Mischungsfluss in einen Chargenfluss für die Entladung in das Transportfahrzeug um.
Im Allgemeinen wird in der Trommelmischanlage die gleiche Art von Emissionskontrollausrüstung verwendet wie in der Batch-Anlage. Es können ein primärer Trockenkollektor und entweder ein Nasswäschersystem oder ein sekundärer Baghouse-Kollektor verwendet werden. Wenn ein Nasswäschersystem verwendet wird, können die gesammelten Feinstoffe nicht wieder in die Mischung zurückgeführt werden und werden verschwendet; Bei Verwendung einer Sackanlage können die gesammelten Feinanteile ganz oder teilweise in die Mischtrommel zurückgeführt oder verschwendet werden.
Kontinuierliche Mischasphaltanlage
In kontinuierlichen Anlagen gibt es keine Unterbrechung im Produktionszyklus, da der Produktionsrhythmus nicht in Chargen unterteilt ist. Die Durchmischung des Materials erfolgt in der länglichen Trocknertrommel, die das Material gleichzeitig trocknet und vermischt. Da kein Mischturm oder Aufzüge vorhanden sind, wird das System erheblich vereinfacht, was zu einer Reduzierung der Wartungskosten führt. Das Fehlen des Siebes erfordert jedoch genaue Kontrollen zu Beginn des Produktionszyklus, bevor die Zuschlagstoffe dem Trockner zugeführt werden und bevor sie anschließend als Asphalt aus dem Trockner ausgetragen werden.
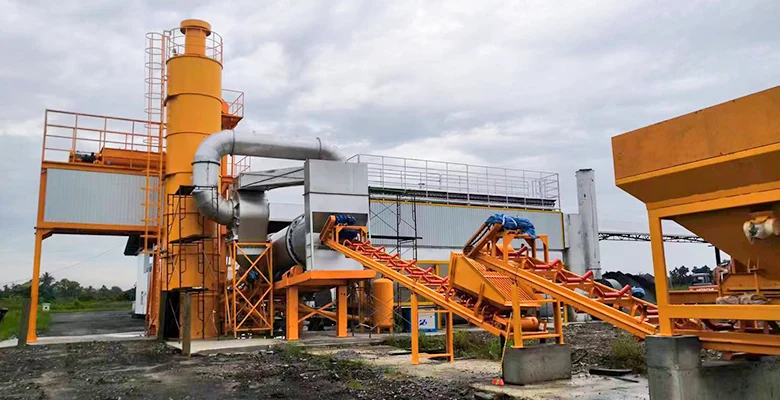
GESAMTDOSIERUNG
Ähnlich wie Batch-Asphaltmischanlagen,
Der Produktionszyklus von kontinuierlichen Anlagen beginnt ebenfalls mit den Kaltdosierern, wo die Zuschlagstoffe in der Regel nach Volumen dosiert werden. Bei Bedarf kann der Sandabscheider zur Dosierung mit einem Wiegeband ausgestattet werden.
Die Kontrolle des Gesamtgewichts der Neuzuschlagstoffe erfolgt jedoch in zwei unterschiedlichen Phasen des Produktionszyklus in den beiden unterschiedlichen Anlagen. Beim kontinuierlichen Typ gibt es ein Zufuhrband, bevor die feuchten Zuschlagstoffe in die Trocknertrommel geleitet werden, wo der Feuchtigkeitsgehalt manuell eingestellt wird, um das Gewicht des Wassers abziehen zu können. Daher ist es äußerst wichtig, dass der Feuchtigkeitsgehalt der Zuschlagstoffe, insbesondere des Sandes, einen konstanten Wert aufweist, der durch häufige Labortests kontinuierlich überwacht wird.
BITUMEN-DOSIERUNG
Bei kontinuierlichen Anlagen erfolgt die Bitumendosierung im Allgemeinen volumetrisch über einen Literzähler im Anschluss an die Förderpumpe. Alternativ besteht die Möglichkeit, einen Massezähler zu installieren, eine notwendige Wahl, wenn modifiziertes Bitumen verwendet wird, das häufige Reinigungsvorgänge erfordert.
Füllstoffdosierung
In kontinuierlichen Anlagen ist das Dosiersystem normalerweise volumetrisch und verwendet Förderschnecken mit variabler Geschwindigkeit, die das bisherige pneumatische Dosiersystem ersetzt haben.
Das Bedienfeld ist in allen unseren Exportwerken vom Typ SPS. Dies ist ein enormer Mehrwert, da wir die SPS an unsere Anforderungen anpassen können. Der Trommelmischer, der mit einem SPS-Panel ausgestattet ist, ist eine andere Maschine als eine Anlage mit Mikroprozessor-Panel. Das SPS-Panel ist im Vergleich zum Mikroprozessor-Panel außerdem wartungsfrei. Wir glauben stets daran, unseren Kunden das Beste zu geben, damit sie ihrer Konkurrenz einen Schritt voraus sein können. Nicht alle Hersteller und Exporteure von Asphalttrommelanlagen bieten Anlagen mit PLC-Panel an.
Alle Anlagen werden vorab getestet, um sicherzustellen, dass alles, was unser Werk verlässt, vor Ort ohne großen Aufwand betriebsbereit ist.
Sinoroader verfügt über mehr als 30 Jahre Erfahrung in der Herstellung und ein Produkt, das durch professionellen Service und günstigere Ersatzteile unterstützt wird, sodass Sie Ihre Ausrüstung viele Jahre lang schätzen und nutzen können.