Tres tipos de plantas mezcladoras de asfalto caliente actualmente son más populares
Convertir agregados y betún en asfalto para construir carreteras requiere un proceso de mezcla térmica. Una planta mezcladora de asfalto es indispensable para esto. El propósito de una planta mezcladora de asfalto es mezclar el agregado y el asfalto a una temperatura elevada para producir una mezcla de pavimentación de asfalto homogénea. El árido utilizado puede ser de un solo material, una combinación de áridos gruesos y finos, con o sin carga mineral. El material aglutinante utilizado normalmente es asfalto, pero puede ser una emulsión de asfalto o uno de una variedad de materiales modificados. También se pueden incorporar a la mezcla varios aditivos, incluidos materiales líquidos y en polvo.
Actualmente, existen tres tipos más populares de plantas mezcladoras de asfalto caliente: mezcla por lotes, mezcla en tambor y mezcla en tambor continuo. Los tres tipos tienen el mismo propósito final y la mezcla asfáltica debe ser esencialmente similar, independientemente del tipo de planta utilizada para fabricarla. Los tres tipos de plantas difieren, sin embargo, en operación y flujo de materiales, como se describe en las siguientes secciones.
Planta de mezcla de asfalto por lotesLa planta mezcladora de asfalto es un equipo clave para cualquier empresa de construcción de carreteras. Cualquier operación de una planta mezcladora de lotes de asfalto tiene muchas funciones. Las plantas de lotes de asfalto producen una mezcla de asfalto en caliente en una serie de lotes. Estas plantas de mezcla por lotes producen mezcla asfáltica en caliente en un proceso continuo. También es posible modificar y utilizar este equipo para la producción de mezcla asfáltica en caliente con material reciclado. Las plantas de tipo discontinuo tienen variaciones en las mismas que permiten la adición de RAP (pavimento asfáltico recuperado). Los componentes de una planta de mezcla por lotes de asfalto estándar son: el sistema de alimentación en frío, el sistema de suministro de asfalto, el secador de agregados, la torre mezcladora y el sistema de control de emisiones. La torre de la planta dosificadora consta de un elevador caliente, una plataforma de cribado, tolvas calientes, una tolva de pesaje, una cubeta de pesaje de asfalto y un pugmill. El agregado utilizado en la mezcla se retira de las pilas de almacenamiento y se coloca en tolvas individuales de alimentación en frío. Los agregados de diferentes tamaños se dosifican fuera de sus contenedores mediante una combinación del tamaño de la abertura de la compuerta en la parte inferior de cada contenedor y la velocidad de la cinta transportadora debajo del contenedor. Generalmente, una cinta alimentadora debajo de cada tolva deposita el agregado en un transportador de recolección ubicado debajo de todas las tolvas de alimentación en frío. El agregado es transportado por el transportador de recolección y transferido a un transportador de carga. Luego, el material en el transportador de carga se transporta hasta el secador de agregados.
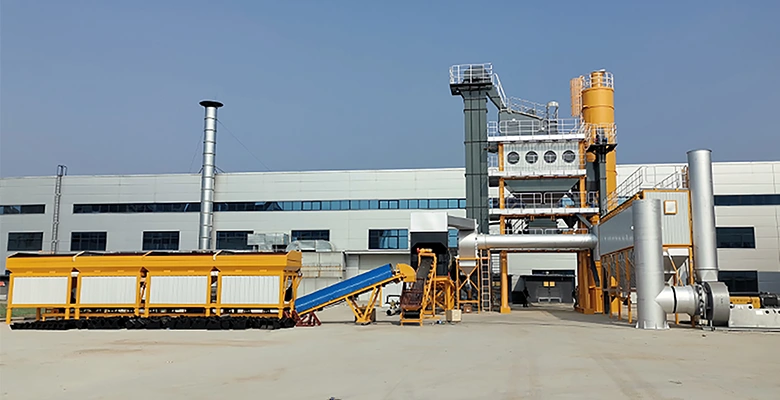
La secadora funciona a contracorriente. El agregado se introduce en el secador en el extremo superior y se mueve hacia abajo por el tambor tanto por la rotación del tambor (flujo por gravedad) como por la configuración de vuelo dentro del secador giratorio. El quemador está ubicado en el extremo inferior de la secadora, y los gases de escape del proceso de combustión y secado se mueven hacia el extremo superior de la secadora, en contra del flujo del agregado. A medida que el agregado se voltea a través de los gases de escape, el material se calienta y se seca. La humedad se elimina y sale del secador como parte de la corriente de gases de escape.
Luego, el agregado seco y caliente se descarga del secador en el extremo inferior. El agregado caliente generalmente se transporta a la parte superior de la torre de mezcla de la planta mediante un elevador de cangilones. Al descargarse del elevador, el agregado normalmente pasa a través de un conjunto de cribas vibratorias hacia, por lo general, uno de los cuatro contenedores de almacenamiento en caliente. El material agregado más fino pasa directamente a través de todas las pantallas hacia el depósito caliente n.º 1; las partículas del agregado más grueso están separadas por
pantallas de diferentes tamaños y se depositan en uno de los otros contenedores calientes. La separación del agregado en las tolvas calientes depende del tamaño de las aberturas en la criba que se usa en la plataforma de la criba y la gradación del agregado en las tolvas de alimentación en frío.
El agregado calentado, secado y redimensionado se mantiene en las tolvas calientes hasta que se descarga desde una compuerta en la parte inferior de cada tolva hacia una tolva de pesaje. La proporción correcta de cada agregado se determina por peso.
Al mismo tiempo que se dosifica y pesa el agregado, el asfalto se bombea desde su tanque de almacenamiento a una cubeta de pesaje calentada separada ubicada en la torre, justo encima del pugmill. La cantidad adecuada de material se pesa en la cubeta y se mantiene hasta que se vacía en la pugmill. El agregado en la tolva de pesaje se vacía en un molino de dos ejes y las diferentes fracciones de agregado se mezclan durante un período de tiempo muy corto, generalmente menos de 5 segundos. Después de este breve tiempo de mezcla en seco, se descarga el asfalto de la cubeta de pesaje.
en el pugmill, y comienza el tiempo de mezcla húmeda. El tiempo de mezcla para mezclar el asfalto con el agregado no debe ser mayor que el necesario para recubrir completamente las partículas de agregado con una película delgada del material asfáltico, generalmente en el rango de 25 a 35 segundos, con el extremo inferior de este rango siendo para un pugmill que esta en buen estado. El tamaño del lote mezclado en el pugmill puede estar en el rango de 1,81 a 5,44 toneladas (2 a 6 toneladas).
Cuando se ha completado la mezcla, se abren las compuertas en la parte inferior del pugmill y la mezcla se descarga en el vehículo de transporte o en un dispositivo transportador que lleva la mezcla a un silo desde el cual se cargarán los camiones por lotes. Para la mayoría de las plantas dosificadoras, el tiempo necesario para abrir las compuertas del molino y descargar la mezcla es de aproximadamente 5 a 7 segundos. El tiempo total de mezcla (tiempo de mezcla seca + tiempo de mezcla húmeda + tiempo de descarga de la mezcla) para un lote puede ser tan corto como 40 segundos, pero normalmente, el tiempo total de mezcla es de unos 45 segundos.
La planta está equipada con dispositivos de control de emisiones, que comprenden sistemas de recolección primaria y secundaria. Normalmente se utiliza un colector seco o una caja ciega como colector primario. Se puede usar un sistema de lavado húmedo o, más a menudo, un sistema de filtro de tela seca (cámara de bolsas) como sistema de recolección secundario para eliminar las partículas de los gases de escape que salen del secador y enviar aire limpio a la atmósfera a través de la chimenea. .
Si se incorpora RAP a la mezcla, se coloca en un contenedor de alimentación en frío separado desde el cual se entrega a la planta. El RAP se puede agregar al nuevo agregado en una de tres ubicaciones: la parte inferior del elevador caliente; las papeleras calientes; o, más comúnmente, la tolva de pesaje. La transferencia de calor entre el agregado nuevo sobrecalentado y el material recuperado comienza tan pronto como los dos materiales entran en contacto y continúa durante el proceso de mezcla en el pugmill.
Planta de asfalto de mezcla de tamborEn comparación con el tipo de lote, la planta de asfalto de mezcla de tambor tiene menos pérdida térmica, menor potencia de trabajo, sin desbordamiento, menos polvo volador y control de temperatura estable. El sistema de control ajusta automáticamente la tasa de flujo de asfalto de acuerdo con la tasa de flujo de agregados y la proporción de agregados de asfalto preestablecida, para garantizar una salida proporcional precisa. La planta de mezcla de tambor de asfalto es el tipo de plantas que se clasifican como plantas de mezcla continua, producen asfalto de mezcla caliente en un proceso continuo.
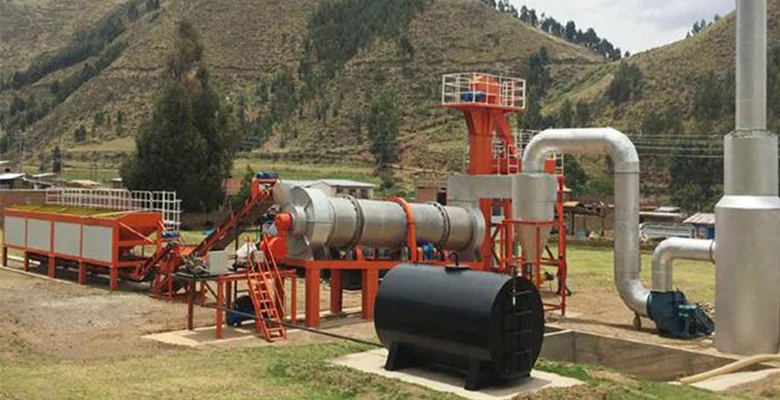
Por lo general, los sistemas de alimentación en frío en las plantas de mezcla en tambor y por lotes de HMA son similares. Cada uno consta de contenedores de alimentación en frío, transportadores de alimentación, un transportador de recolección y un transportador de carga. En la mayoría de las plantas de mezcla de tambor y en algunas plantas por lotes, en algún momento se incluye una pantalla de separación en el sistema. Si también se está alimentando RAP a la planta para producir una mezcla reciclada, se necesitan un contenedor o contenedores adicionales de alimentación en frío, una correa de alimentación y/o un transportador de recolección, una pantalla de separación y un transportador de carga para manejar el material adicional. Las plantas de mezcla de tambor constan de cinco componentes principales: el sistema de alimentación en frío, el sistema de suministro de asfalto, el mezclador de tambor, los silos de almacenamiento o compensación y el equipo de control de emisiones.
Los silos de alimentación en frío se utilizan para dosificar el material a la planta. Se utiliza una cinta alimentadora de velocidad variable debajo de cada contenedor. La cantidad de agregado extraída de cada tolva se puede controlar tanto por el tamaño de la abertura de la compuerta como por la velocidad de la correa del alimentador para proporcionar una entrega precisa de los materiales de diferentes tamaños. El agregado de cada cinta alimentadora se deposita en un transportador de recolección que pasa por debajo de todos los silos de alimentación en frío. El material combinado normalmente se pasa a través de una pantalla de separación y luego se transfiere a un transportador de carga para transportarlo al mezclador de tambor.
El transportador de carga está equipado con dos dispositivos que se utilizan para determinar la cantidad de agregado que se entrega a la planta: un puente de pesaje debajo de la cinta transportadora mide el peso del agregado que pasa sobre él y un sensor determina la velocidad de la cinta. Estos dos valores se utilizan para calcular el peso húmedo del agregado, en toneladas (toneladas) por hora, que ingresa al mezclador de tambor. La computadora de la planta, con la cantidad de humedad en el agregado proporcionada como valor de entrada, convierte el peso húmedo en peso seco para determinar la cantidad correcta de asfalto que se necesita en la mezcla.
El mezclador de tambor convencional es un sistema de flujo paralelo: los gases de escape y el agregado se mueven en la misma dirección. El quemador está ubicado en el extremo superior (extremo de entrada de agregados) del tambor. El agregado ingresa al tambor ya sea desde un conducto inclinado sobre el quemador o en un transportador Slinger debajo del quemador. El agregado se mueve hacia abajo del tambor por una combinación de gravedad y la configuración de los vuelos ubicados dentro del tambor. A medida que viaja, el agregado se calienta y se elimina la humedad. Se acumula un velo denso de agregado cerca del punto medio de la longitud del tambor para ayudar en el proceso de transferencia de calor.
Si se agrega RAP al agregado nuevo, se deposita desde su propio silo de alimentación en frío y sistema transportador de recolección/carga en una entrada ubicada cerca del centro de la longitud del tambor (sistema de alimentación dividida). En este proceso, el material recuperado está protegido de los gases de escape de alta temperatura por el velo de agregado nuevo aguas arriba del punto de entrada del RAP. Cuando se utilizan mezclas con alto contenido de RAP, es más probable que el RAP se sobrecaliente en el proceso. Esto puede provocar que se emita humo desde el tambor o que se dañe el RAP.
El agregado nuevo y el material recuperado, si se usa, se mueven juntos hacia la parte trasera del tambor. Una bomba extrae el asfalto del tanque de almacenamiento y lo alimenta a través de un medidor, donde se determina el volumen adecuado de asfalto. Luego, el material aglutinante se envía a través de una tubería a la parte trasera del tambor mezclador, donde se inyecta el asfalto sobre el agregado. El recubrimiento del agregado ocurre cuando los materiales se juntan y se mueven hacia el extremo de descarga del tambor. Los finos de relleno mineral o de la cámara de filtros, o ambos, también se agregan en la parte posterior del tambor, ya sea justo antes o junto con la adición del asfalto.
La mezcla asfáltica se deposita en un dispositivo de transporte (un transportador de listones de arrastre, una cinta transportadora o un elevador de cangilones) para su transporte a un silo de almacenamiento. El silo convierte el flujo continuo de mezcla en un flujo por lotes para su descarga en el vehículo de transporte.
En general, se utiliza el mismo tipo de equipo de control de emisiones en la planta de mezcla en tambor que en la planta dosificadora. Se puede usar un colector seco primario y un sistema de depuración húmedo o un colector secundario de cámara de filtros. Si se utiliza un sistema de lavado húmedo, los finos recolectados no se pueden reciclar nuevamente en la mezcla y se desechan; si se utiliza una cámara de bolsas, los finos recolectados pueden devolverse en su totalidad o en parte al tambor mezclador, o pueden desecharse.
Planta de asfalto de mezcla continuaEn plantas continuas no hay interrupción en el ciclo de producción ya que el ritmo de producción no se divide en lotes. La mezcla del material se lleva a cabo dentro del tambor secador que es alargado, ya que seca y mezcla el material al mismo tiempo. Al no existir torre mezcladora ni ascensores, el sistema se simplifica considerablemente, con la consiguiente reducción del coste de mantenimiento. Sin embargo, la ausencia de la pantalla hace que sea necesario tener controles precisos al comienzo del ciclo de producción, antes de que los agregados entren en la secadora y antes de que se descarguen de la secadora como asfalto.
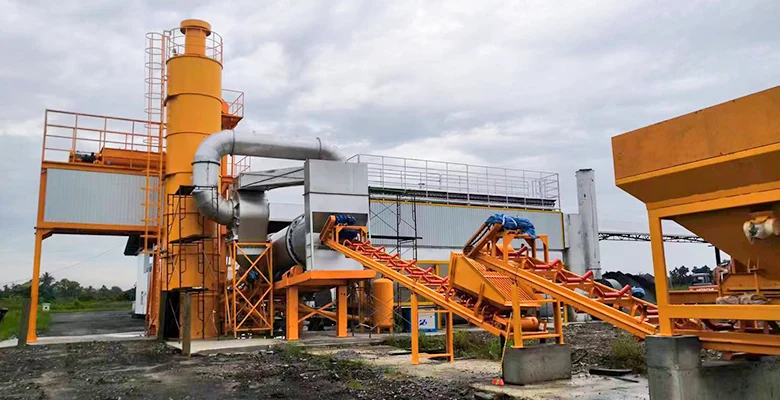
MEDICIÓN DE AGREGADOS
Similar a las plantas mezcladoras de asfalto por lotes,
el ciclo productivo de las plantas continuas también comienza con los alimentadores fríos, donde los áridos son generalmente dosificados por volumen; si es necesario, el extractor de arena se puede equipar con una cinta de pesaje para la dosificación.
Sin embargo, el control del peso total de los áridos vírgenes se realiza en dos fases diferentes del ciclo de producción en las dos plantas diferentes. En el tipo continuo hay una cinta de alimentación, antes de que los agregados húmedos se alimenten al tambor de la secadora, donde el contenido de humedad se establece manualmente para permitir que se reste el peso del agua. Por lo tanto, es extremadamente importante que el contenido de humedad en los agregados, particularmente en la arena, tenga un valor constante que se controle continuamente a través de frecuentes pruebas de laboratorio.
DOSIFICACIÓN DE BETÚN
En las plantas continuas la dosificación del betún es generalmente volumétrica a través de un contador de litros posterior a la bomba de alimentación. Alternativamente, es posible instalar un contador de masa, una opción necesaria si se utiliza betún modificado, que requiere operaciones de limpieza frecuentes.
Dosificación de relleno
En las plantas continuas el sistema de dosificación es normalmente volumétrico, utilizando tornillos de alimentación de velocidad variable que han sustituido al anterior sistema de dosificación neumática.
El panel de control es tipo PLC en todas nuestras plantas de exportación. Esta es una adición de gran valor porque podemos personalizar el PLC según nuestros requisitos. La mezcladora de tambor que está equipada con un panel de PLC es una máquina diferente a una planta con panel de microprocesador. El panel del PLC tampoco requiere mantenimiento en comparación con el panel del microprocesador. Siempre creemos en dar lo mejor a los clientes para que puedan mantenerse por delante de la competencia. No todos los fabricantes y exportadores de plantas de tambor de asfalto ofrecen plantas con panel PLC.
Se realizan pruebas previas de todas las plantas para garantizar que todo lo que sale de nuestra fábrica esté listo para funcionar con menos problemas en el sitio.
Sinoroader tiene más de 30 años de experiencia en la fabricación y un producto respaldado por un servicio profesional y repuestos más baratos para que pueda apreciar y utilizar su equipo en los años venideros.