Täitematerjalide ja bituumeni asfaldiks muutmine teede ehitamiseks nõuab termilist segamisprotsessi. Asfaldisegamise tehas on selleks asendamatu. Asfaldisegamistehase eesmärk on segada täitematerjal ja asfalt kõrgel temperatuuril kokku, et saada homogeenne asfaltkatte segu. Kasutatav täitematerjal võib olla üks materjal, jämedate ja peente täitematerjalide kombinatsioon, mineraalse täiteainega või ilma. Kasutatav sideaine on tavaliselt asfalt, kuid see võib olla ka asfaldiemulsioon või üks paljudest muudetud materjalidest. Segusse võib lisada ka erinevaid lisandeid, sealhulgas vedelaid ja pulbrilisi materjale.
Praegu on veel kolm populaarsemat tüüpi kuuma asfaldi segamise tehast: partii, trummelsegu ja pidev trummelsegu. Kõigil kolmel tüübil on sama lõppeesmärk ja asfaldisegu peaks olema põhimõtteliselt sarnane, olenemata selle valmistamiseks kasutatud tehase tüübist. Need kolme tüüpi tehased erinevad siiski töö ja materjalide voolu poolest, nagu on kirjeldatud järgmistes osades.
Partii segaasfalditehas
asfaldisegutehas on iga tee-ehitusettevõtte põhivarustus. Igal asfaldisegu tehase tööl on palju funktsioone. Asfaldipartii tehased toodavad kuuma asfalti segu partiidena. Need partiisegutehased toodavad pidevas protsessis kuuma segu asfalti. Seda seadet on võimalik ka ümbertöödelda ja kasutada kuuma asfaldi valmistamiseks, kasutades taaskasutatud materjali. Partiitüüpi tehastes on variatsioone, mis võimaldavad lisada RAP-i (regenereeritud asfaltkate). Standardse asfaldisegutehase komponendid on: külmtoitesüsteem, asfaldi etteandesüsteem, täitematerjali kuivati, segamistorn ja heitgaaside kontrollsüsteem. Partiitehase torn koosneb kuumaliftist, ekraanitekist, kuumadest prügikastidest, kaalumispunkrist, asfaldikaalu ämbrist ja pugveskist. Segus kasutatud täitematerjal eemaldatakse varudest ja asetatakse üksikutesse külmsöötmiskastidesse. Erineva suurusega täitematerjalid jaotatakse nende prügikastidest välja, kombineerides iga prügikasti põhjas oleva värava ava suurust ja prügikasti all oleva konveieri kiirust. Üldjuhul asetab iga prügikasti all olev toitelint täitematerjali kogumiskonveierile, mis asub kõigi külmsöötmiskastide all. Täitematerjal transporditakse kogumiskonveieri abil ja viiakse laadimiskonveierile. Seejärel kantakse laadimiskonveieril olev materjal üles täitematerjalide kuivatisse.
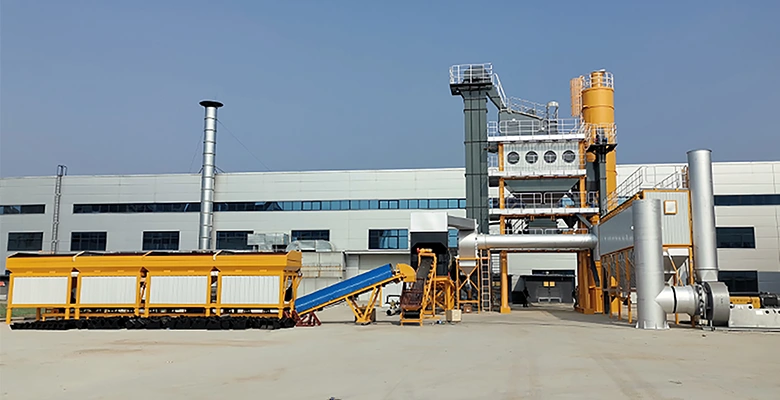
Kuivati töötab vastuvoolu põhimõttel. Täitematerjal sisestatakse kuivatisse ülemises otsas ja liigutatakse mööda trumlit alla nii trumli pöörlemise (gravitatsioonivool) kui ka pöörleva kuivati sees oleva lennukonfiguratsiooni abil. Põleti asub kuivati alumises otsas ning põlemis- ja kuivatamisprotsessi heitgaasid liiguvad kuivati ülemise otsa poole, täitematerjali voolu vastu (vastupidiselt). Kui täitematerjal lastakse läbi heitgaaside, materjal kuumutatakse ja kuivatatakse. Niiskus eemaldatakse ja eemaldatakse kuivatist heitgaasivoolu osana.
Kuum ja kuiv täitematerjal lastakse seejärel kuivatist välja alumisest otsast. Kuum täitematerjal transporditakse tavaliselt koppliftiga taimede segamistorni tippu. Liftist väljumisel läheb täitematerjal tavaliselt läbi vibreerivate ekraanide komplekti, tavaliselt ühte neljast kuumast hoiukastist. Kõige peenem täitematerjal läheb otse läbi kõigi ekraanide kuuma prügikasti nr 1; jämedamad täiteosakesed on eraldatud
erineva suurusega ekraanidele ja asetatakse mõnda teise kuuma prügikasti. Täitematerjali eraldamine kuumadesse prügikastidesse sõltub sõela avade suurusest, mida kasutatakse sõelaplaadis, ja täitematerjali gradatsioonist külmsöötesalvedes.
Kuumutatud, kuivatatud ja muudetud suurust täitematerjale hoitakse kuumades mahutites, kuni see tühjendatakse iga prügikasti põhjas olevast väravast kaalupunkrisse. Iga täitematerjali õige osakaal määratakse kaalu järgi.
Samal ajal täitematerjali proportsioonide ja kaalumisega pumbatakse asfalt akumulatsioonipaagist eraldi soojendusega kaalukoppi, mis asub tornis vahetult mopsveski kohal. Õige kogus materjali kaalutakse ämbrisse ja hoitakse kuni mopsveskisse tühjendamiseni. Kaalupunkris olev täitematerjal tühjendatakse kahe võlliga mopsveskisse ja erinevad täitematerjalide fraktsioonid segatakse kokku väga lühikese aja jooksul – tavaliselt vähem kui 5 sekundi jooksul. Pärast seda lühikest kuivsegamisaega tühjendatakse kaaluämbrist asfalt.
pugveskisse ja algab märgsegamise aeg. Asfaldi segamisaeg täitematerjaliga ei tohiks olla pikem kui kuluv aeg täitematerjali osakeste täielikuks katmiseks õhukese asfaltmaterjali kilega – tavaliselt 25–35 sekundit, selle vahemiku alumine ots olles heas seisukorras mopsveski jaoks. Pugveskis segatava partii suurus võib jääda vahemikku 1,81–5,44 tonni (2–6 tonni).
Kui segamine on lõppenud, avatakse mopsveski põhjas olevad väravad ja segu juhitakse veoautosse või transpordiseadmesse, mis kannab segu silohoidlasse, kust laaditakse veokid partiidena. Enamiku partiitehaste puhul kulub mopsveski väravate avamiseks ja segu tühjendamiseks umbes 5–7 sekundit. Partii kogusegamisaeg (kuivsegamise aeg + märgsegamise aeg + segu tühjendamise aeg) võib olla nii lühike kui umbes 40 sekundit, kuid tavaliselt on kogu segamisaeg umbes 45 sekundit.
Tehas on varustatud heitekontrolliseadmetega, mis hõlmavad nii esmaseid kui ka sekundaarseid kogumissüsteeme. Põhikollektorina kasutatakse tavaliselt kuivkollektorit või väljalülituskasti. Sekundaarse kogumissüsteemina saab kasutada kas märgpuhastit või sagedamini kuivriidest filtrisüsteemi (kotimaja), et eemaldada kuivatist välja voolavatest heitgaasidest tahked osakesed ja suunata läbi korstna atmosfääri puhast õhku. .
Kui segusse lisatakse RAP-i, asetatakse see eraldi külmsöötmiskasti, kust see tehasesse tarnitakse. RAP-i saab uuele agregaadile lisada ühes kolmest asukohast: kuuma lifti põhjas; kuumad prügikastid; või kõige sagedamini kaalupunker. Soojusülekanne ülekuumendatud uue täitematerjali ja taaskasutatud materjali vahel algab kohe, kui need kaks materjali kokku puutuvad, ja jätkub segamisprotsessi ajal pugveskis.
Drum Mix Asfalditehas
Võrreldes partii tüübiga on trumlisasfalditehasel väiksem soojuskadu, väiksem töövõimsus, ülevoolu puudumine, vähem tolmu ja stabiilne temperatuurikontroll. Juhtsüsteem reguleerib automaatselt asfaldi voolukiirust vastavalt täitematerjalide voolukiirusele ja eelseadistatud asfaldi-täitematerjalide suhtele, et tagada täpne proportsionaalne väljund. Asfalditrumli segutehas on seda tüüpi tehased, mis liigitatakse pideva segamise tehasteks ja mis toodavad kuuma asfalti pidevas protsessis.
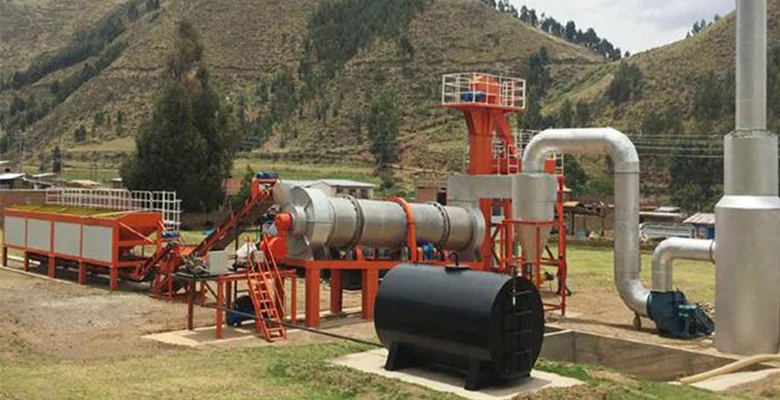
Tavaliselt on HMA partii- ja trummelsegutehaste külmsöötmissüsteemid sarnased. Igaüks neist koosneb külmsöötmiskastidest, etteandekonveieritest, kogumiskonveierist ja laadimiskonveierist. Enamikul trummelseguseadmetel ja mõnel partiitehasel on süsteemis mingil hetkel kaasas skaleerimisekraan. Kui RAP-i söödetakse tehasesse ka ringlussevõetud segu tootmiseks, on lisamaterjali käitlemiseks vajalik täiendav külmsöötmiskast või -kastid, etteandelint ja/või kogumiskonveier, skalpimissõel ja laadimiskonveier. trummelsegutehased koosnevad viiest peamisest komponendist: külmtoitesüsteem, asfaldi etteandesüsteem, trummelsegisti, tõusu- või hoiusilod ja heitgaaside kontrollseadmed.
Külmtoitekaste kasutatakse materjali proportsiooniks taimega. Iga prügikasti all kasutatakse muutuva kiirusega söötmisrihma. Igast prügikastist väljavõetava täitematerjali kogust saab seega reguleerida nii värava ava suuruse kui ka etteandelindi kiirusega, et tagada erineva suurusega materjalide täpne kohaletoimetamine. Igal etteandelindil olev täitematerjal kantakse kogumiskonveierile, mis kulgeb kõigi külmsöötmiskastide all. Kombineeritud materjal lastakse tavaliselt läbi skaleerimissõela ja seejärel kantakse laadimiskonveierile trummelsegisti transportimiseks.
Laadimiskonveier on varustatud kahe seadmega, mille abil määratakse tehasesse tarnitava täitematerjali kogust: konveierilindi all olev kaalusild mõõdab sellest üle liikuva täitematerjali massi ja andur määrab lindi kiiruse. Neid kahte väärtust kasutatakse trummelmikserisse siseneva täitematerjali märgkaalu arvutamiseks tonnides (tonnides) tunnis. Tehasearvuti, mille sisendväärtusena on esitatud täitematerjali niiskuse kogus, teisendab märgkaalu kuivmassiks, et määrata segus vajalik asfaldi õige kogus.
Tavaline trummelsegisti on paralleelvoolusüsteem – heitgaasid ja agregaat liiguvad samas suunas. Põleti asub trumli ülemises otsas (agregaadi sisselaskeotsas). Täitematerjal siseneb trumlisse kas põleti kohal olevast kaldrennist või põleti all olevast Slingeri konveierist. Täitematerjal liigub trumli alla raskusjõu ja trumlis asuvate lendude konfiguratsiooni kombinatsiooni abil. Liikudes täitematerjal kuumutatakse ja niiskus eemaldatakse. Trumli pikkuse keskpunkti lähedale on üles ehitatud tihe täitematerjali loor, mis aitab kaasa soojusülekande protsessile.
Kui uuele täitematerjalile lisatakse RAP, ladestatakse see oma külmsöötmiskastist ja kogumiskonveierisüsteemist sisselaskeavasse, mis asub trumli pikkuse keskpunkti lähedal (jaotatud etteandesüsteem). Selles protsessis kaitstakse taaskasutatud materjali kõrge temperatuuriga heitgaaside eest uue täitematerjali looriga, mis asub RAP-i sisenemispunktist ülesvoolu. Kui kasutatakse suure RAP-sisaldusega segusid, on tõenäolisem, et RAP kuumeneb protsessi käigus üle. See võib põhjustada trumlist suitsu eraldumist või RAP-i kahjustamist.
Uus täitematerjal ja taaskasutatud materjal, kui seda kasutatakse, liiguvad koos trumli tagumisse ossa. Asfalt tõmmatakse pumba abil mahutist välja ja juhitakse läbi arvesti, kus määratakse õige asfaldi maht. Seejärel juhitakse sideaine toru kaudu segamistrumli tagaossa, kus asfalt süstitakse täitematerjalile. Täitematerjali katmine toimub siis, kui materjalid lükatakse kokku ja viiakse trumli väljalaskeotsa. Mineraalne täiteaine või kotipesa või mõlemad lisatakse ka trumli tagaossa, kas vahetult enne asfaldi lisamist või koos sellega.
Asfaldisegu ladestatakse transpordiseadmesse (liistkonveier, lintkonveier või koplift), et transportida hoidlasse. Silo muudab pideva seguvoolu partiivooluks, mis juhitakse veosõidukisse.
Üldiselt kasutatakse trummelsegutehases sama tüüpi heitekontrolliseadmeid kui partiitehases. Kasutada saab primaarset kuivkollektorit ja kas märgpuhasti süsteemi või kottmaja sekundaarset kollektorit. Kui kasutatakse märgpuhasti süsteemi, ei saa kogutud peeneid segusse tagasi töödelda ja need lähevad raisku; kui kasutatakse kotti, võib kogutud peenraha kas täielikult või osaliselt segamistrumlisse tagasi viia või raisata.
Pideva segaasfalditehas
Pidevates tehastes ei esine tootmistsüklis katkestusi, kuna tootmisrütmi ei jaotata partiideks. Materjali segamine toimub kuivati trumlis, mis on piklik, kuna see kuivab ja segab materjali samal ajal. Kuna puuduvad segamistornid ega liftid, on süsteem seetõttu oluliselt lihtsustatud ja sellest tulenevalt vähenevad hoolduskulud. Sõela puudumine nõuab aga täpset juhtimist tootmistsükli alguses, enne täitematerjalide kuivatisse söötmist ja enne nende kuivatist asfaldina väljastamist.
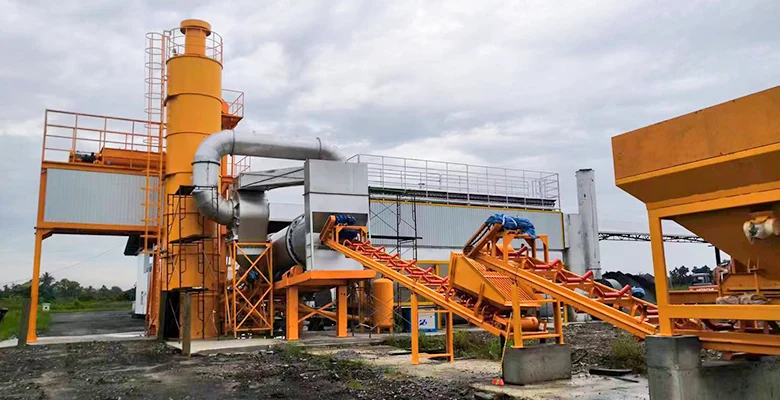
AGREGAADI MÕÕTMINE
Sarnaselt partiide asfaldisegamisseadmetega,
ka pidevseadmete tootmistsükkel algab külmsööturitega, kus täitematerjale mõõdetakse üldjuhul mahu järgi; Vajadusel saab liivatõmbeseadmele paigaldada mõõtmiseks kaalurihma.
Kasutamata täitematerjalide kogumassi kontrollimine toimub aga kahes erinevas tehases tootmistsükli kahes erinevas faasis. Pideva tüübi puhul on enne niiskete täitematerjalide suunamist kuivati trumlisse etteandelin, kus niiskusesisaldus on käsitsi seadistatud, et võimaldada vee massi lahutamist. Seetõttu on äärmiselt oluline, et täitematerjalide, eriti liiva niiskusesisaldus oleks konstantne, mida jälgitakse pidevalt sagedaste laboratoorsete testidega.
BITUUMENI MÕÕTMINE
Pidevates tehastes on bituumeni doseerimine tavaliselt mahuline läbi toitepumbale järgneva liitriloenduri. Alternatiivina on võimalik paigaldada massiloendur, mis on vajalik valik modifitseeritud bituumeni kasutamisel, mis nõuab sagedasi puhastustoiminguid.
Täiteaine mõõtmine
Pidevates seadmetes on doseerimissüsteem tavaliselt mahuline, kasutades muutuva kiirusega etteandekruvisid, mis on asendanud varasema pneumaatilise doseerimissüsteemi.
Juhtpaneel on kõigis meie eksporditehastes PLC-tüüpi. See on tohutu lisaväärtus, sest saame kohandada PLC-d vastavalt meie nõuetele. PLC-paneeliga trummelmikser on teistsugune masin kui mikroprotsessoripaneeliga tehas. PLC-paneel on võrreldes mikroprotsessorpaneeliga ka hooldusvaba. Usume alati klientidele parima andmisesse, et nad saaksid oma konkurentidest ees püsida. Mitte kõik asfalditrumlitehaste tootjad ja eksportijad ei paku PLC-paneeliga tehast.
Kõikide tehaste eeltestimine toimub tagamaks, et kõik, mis meie tehasest lahkub, on valmis kohapeal väiksema vaevata tööks.
Sinoroaderil on enam kui 30-aastane tootmiskogemus ja toode, mille taga on professionaalne teenindus ja odavamad varuosad, et te hindaksite ja kasutaksite oma seadmeid aastaid.