Trois types de centrales d'enrobage à chaud sont actuellement plus populaires
Transformer des granulats et du bitume en asphalte pour construire des routes nécessite un processus de mélange thermique. Une centrale d'enrobage est indispensable pour cela. Le but d'une usine de mélange d'asphalte est de mélanger l'agrégat et l'asphalte à une température élevée pour produire un mélange de pavage d'asphalte homogène. Le granulat utilisé peut être un matériau unique, une combinaison de granulats grossiers et fins, avec ou sans charge minérale. Le matériau liant utilisé est normalement de l'asphalte mais peut être une émulsion d'asphalte ou l'un d'une variété de matériaux modifiés. Divers additifs, y compris des matériaux liquides et en poudre, peuvent également être incorporés dans le mélange.
Il existe actuellement trois types de centrales de malaxage d'asphalte chaud plus populaires : le mélange par lots, le mélange à tambour et le mélange à tambour continu. Les trois types ont le même objectif ultime et le mélange d'asphalte doit être essentiellement similaire quel que soit le type d'usine utilisé pour le fabriquer. Les trois types d'usines diffèrent, cependant, dans le fonctionnement et le flux de matériaux, comme décrit dans les sections suivantes.
Usine d'asphalte de mélange discontinu
La centrale d'asphalte est un équipement clé pour toute entreprise de construction de routes. Toute opération de centrale d'enrobage discontinu d'asphalte a de nombreuses fonctions. Les centrales d'asphalte discontinues produisent de l'enrobé à chaud en une série de lots. Ces centrales discontinues produisent de l'enrobé à chaud dans un processus continu. Il est également possible de modifier et d'utiliser cet équipement pour la production d'enrobés à chaud à partir de matériaux recyclés. Les usines de type discontinu ont des variations qui permettent l'ajout de RAP (chaussée d'asphalte récupérée). Les composants d'une centrale d'asphalte discontinue standard sont : le système d'alimentation à froid, le système d'alimentation en asphalte, le sécheur d'agrégats, la tour de mélange et le système de contrôle des émissions. La tour de la centrale à béton se compose d'un élévateur à chaud, d'une plate-forme de criblage, de bacs à chaud, d'une trémie de pesée, d'un godet de pesée d'asphalte et d'un moulin à béton. L'agrégat utilisé dans le mélange est retiré des stocks et placé dans des bacs individuels d'alimentation à froid. Les granulats de différentes tailles sont dosés hors de leurs bacs par une combinaison de la taille de l'ouverture de la porte au fond de chaque bac et de la vitesse du tapis roulant sous le bac. Généralement, un tapis d'alimentation sous chaque bac dépose l'agrégat sur un convoyeur de collecte situé sous tous les bacs d'alimentation à froid. L'agrégat est transporté par le convoyeur de collecte et transféré vers un convoyeur de chargement. Le matériau sur le convoyeur de chargement est ensuite transporté jusqu'au séchoir à granulats.
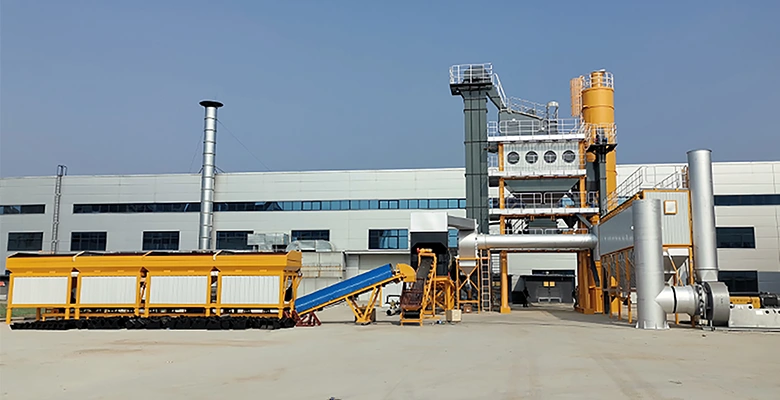
Le séchoir fonctionne à contre-courant. L'agrégat est introduit dans le séchoir à l'extrémité supérieure et est déplacé vers le bas du tambour à la fois par la rotation du tambour (écoulement par gravité) et la configuration de vol à l'intérieur du séchoir rotatif. Le brûleur est situé à l'extrémité inférieure du sécheur, et les gaz d'échappement du processus de combustion et de séchage se déplacent vers l'extrémité supérieure du sécheur, contre (contre) le flux de l'agrégat. Au fur et à mesure que l'agrégat est culbuté à travers les gaz d'échappement, le matériau est chauffé et séché. L'humidité est éliminée et évacuée du sécheur dans le cadre du flux de gaz d'échappement.
L'agrégat chaud et sec est ensuite déchargé du séchoir à l'extrémité inférieure. L'agrégat chaud est généralement transporté au sommet de la tour de mélange de l'usine par un élévateur à godets. Lors de la décharge de l'élévateur, l'agrégat passe normalement à travers un ensemble de cribles vibrants dans, généralement, l'un des quatre bacs de stockage chauds. Le matériau d'agrégat le plus fin passe directement à travers tous les tamis dans le bac chaud n° 1 ; les particules d'agrégat plus grossières sont séparées par le
tamis de tailles différentes et déposés dans l'un des autres bacs chauds. La séparation des granulats dans les trémies chaudes dépend de la taille des ouvertures du crible utilisé dans la plate-forme de criblage et de la gradation des granulats dans les trémies d'alimentation froide.
L'agrégat chauffé, séché et redimensionné est maintenu dans les bacs chauds jusqu'à ce qu'il soit déchargé d'une porte au bas de chaque bac dans une trémie de pesée. La proportion correcte de chaque agrégat est déterminée par le poids.
En même temps que l'agrégat est dosé et pesé, l'asphalte est pompé de son réservoir de stockage vers un godet de pesée chauffé séparé situé sur la tour juste au-dessus du moulin à béton. La bonne quantité de matériau est pesée dans le seau et maintenue jusqu'à ce qu'elle soit vidée dans le moulin. L'agrégat dans la trémie de pesée est vidé dans un broyeur à double arbre, et les différentes fractions d'agrégats sont mélangées ensemble pendant une très courte période de temps, généralement moins de 5 secondes. Après ce bref temps de mélange à sec, l'asphalte du godet de pesée est déchargé.
dans le pugmill, et le temps de mélange humide commence. Le temps de mélange pour le mélange de l'asphalte avec l'agrégat ne doit pas être supérieur à celui nécessaire pour recouvrir complètement les particules d'agrégat avec un film mince de matériau d'asphalte - généralement de l'ordre de 25 à 35 secondes, avec l'extrémité inférieure de cette plage étant pour un pugmill qui est en bon état. La taille du lot mélangé dans le malaxeur peut être de l'ordre de 1,81 à 5,44 tonnes (2 à 6 tonnes).
Lorsque le mélange est terminé, les portes situées au bas du moulin sont ouvertes et le mélange est déchargé dans le véhicule de transport ou dans un dispositif de transport qui transporte le mélange vers un silo à partir duquel les camions seront chargés par lots. Pour la plupart des centrales à béton, le temps nécessaire pour ouvrir les portes du moulin et décharger le mélange est d'environ 5 à 7 secondes. Le temps de mélange total (temps de mélange à sec + temps de mélange humide + temps de décharge du mélange) pour un lot peut être aussi court qu'environ 40 secondes, mais généralement, le temps de mélange total est d'environ 45 secondes.
L'usine est équipée de dispositifs de contrôle des émissions, comprenant à la fois des systèmes de collecte primaire et secondaire. Un collecteur sec ou une boîte knock-out est normalement utilisé comme collecteur primaire. Un système d'épurateur humide ou, plus souvent, un système de filtre à tissu sec (filtre à manches) peut être utilisé comme système de collecte secondaire pour éliminer les particules des gaz d'échappement qui s'échappent du sécheur et envoyer de l'air pur dans l'atmosphère à travers la cheminée. .
Si le RAP est incorporé au mélange, il est placé dans un bac d'alimentation à froid séparé à partir duquel il est livré à l'usine. Le RAP peut être ajouté au nouvel agrégat dans l'un des trois emplacements suivants : le bas de l'élévateur à chaud ; les bacs chauds ; ou, le plus souvent, la trémie de pesée. Le transfert de chaleur entre le nouveau granulat surchauffé et le matériau récupéré commence dès que les deux matériaux entrent en contact et se poursuit pendant le processus de mélange dans le malaxeur.
Usine d'asphalte à tambour
Par rapport au type discontinu, la centrale d'asphalte à mélange de tambour a moins de perte thermique, une puissance de travail inférieure, aucun débordement, moins de poussière volante et un contrôle de température stable. Le système de contrôle ajuste automatiquement le débit d'asphalte en fonction du débit d'agrégats et du rapport asphalte-agrégats prédéfini, pour assurer une sortie proportionnelle précise. Les centrales d'enrobage à tambour d'asphalte sont les types d'usines qui sont classées comme centrales de malaxage en continu, produisant de l'asphalte à chaud dans un processus continu.
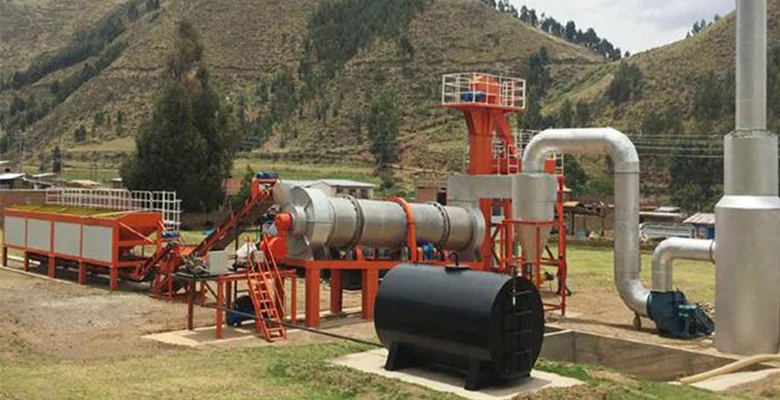
En règle générale, les systèmes d'alimentation à froid des usines de traitement par lots et de mélange à tambour d'enrobage à chaud sont similaires. Chacun se compose de bacs d'alimentation à froid, de convoyeurs d'alimentation, d'un convoyeur de collecte et d'un convoyeur de chargement. Sur la plupart des centrales à tambour et sur certaines centrales discontinues, un crible de scalpage est inclus dans le système à un moment donné. Si le RAP est également introduit dans l'usine pour produire un mélange recyclé, un ou plusieurs bacs d'alimentation à froid supplémentaires, un tapis d'alimentation et/ou un convoyeur de collecte, un crible scalpeur et un convoyeur de chargement sont nécessaires pour gérer le matériau supplémentaire. Les usines de mélange à tambour se composent de cinq composants principaux : le système d'alimentation à froid, le système d'alimentation en asphalte, le mélangeur à tambour, les silos de surpression ou de stockage et l'équipement de contrôle des émissions.
Les bacs d'alimentation à froid sont utilisés pour doser le matériel à la plante. Un tapis d'alimentation à vitesse variable est utilisé sous chaque bac. La quantité d'agrégat tirée de chaque bac peut ainsi être contrôlée à la fois par la taille de l'ouverture de la porte et la vitesse de la bande d'alimentation pour fournir une livraison précise des matériaux de différentes tailles. L'agrégat sur chaque tapis d'alimentation est déposé sur un convoyeur de collecte qui passe sous tous les bacs d'alimentation à froid. Le matériau combiné est normalement passé à travers un crible de scalpage, puis transféré sur un convoyeur de chargement pour être transporté vers le mélangeur à tambour.
Le convoyeur de chargement est équipé de deux dispositifs qui sont utilisés pour déterminer la quantité d'agrégats livrés à l'usine : un pont-bascule sous la bande transporteuse mesure le poids de l'agrégat qui passe dessus et un capteur détermine la vitesse de la bande. Ces deux valeurs sont utilisées pour calculer le poids humide de l'agrégat, en tonnes (tonnes) par heure, entrant dans le malaxeur à tambour. L'ordinateur de l'usine, avec la quantité d'humidité dans l'agrégat fournie comme valeur d'entrée, convertit le poids humide en poids sec afin de déterminer la quantité correcte d'asphalte nécessaire dans le mélange.
Le mélangeur à tambour conventionnel est un système à flux parallèle - les gaz d'échappement et l'agrégat se déplacent dans la même direction. Le brûleur est situé à l'extrémité supérieure (extrémité d'entrée des granulats) du tambour. L'agrégat entre dans le tambour soit par une goulotte inclinée au-dessus du brûleur, soit sur un convoyeur Slinger sous le brûleur. L'agrégat est déplacé vers le bas du tambour par une combinaison de la gravité et de la configuration des ailettes situées à l'intérieur du tambour. Au cours de son déplacement, l'agrégat est chauffé et l'humidité éliminée. Un voile dense d'agrégats est construit près du milieu de la longueur du tambour pour faciliter le processus de transfert de chaleur.
Si le RAP est ajouté au nouvel agrégat, il est déposé à partir de son propre bac d'alimentation à froid et de son système de convoyeur de collecte/chargement dans une entrée située près du centre de la longueur du tambour (système d'alimentation divisée). Dans ce procédé, le matériau récupéré est protégé des gaz d'échappement à haute température par le voile de granulats neufs en amont du point d'entrée du RAP. Lorsque des mélanges à haute teneur en RAP sont utilisés, il est plus probable que le RAP soit surchauffé au cours du processus. Cela peut entraîner l'émission de fumée du tambour ou endommager le RAP.
Le nouveau granulat et le matériau récupéré, s'ils sont utilisés, se déplacent ensemble dans la partie arrière du tambour. L'asphalte est tiré du réservoir de stockage par une pompe et alimenté par un compteur, où le volume approprié d'asphalte est déterminé. Le matériau liant est ensuite acheminé par un tuyau à l'arrière du tambour mélangeur, où l'asphalte est injecté sur l'agrégat. Le revêtement de l'agrégat se produit lorsque les matériaux sont culbutés ensemble et déplacés vers l'extrémité de décharge du tambour. Des charges minérales ou des fines de filtre à manches, ou les deux, sont également ajoutées à l'arrière du tambour, soit juste avant, soit en conjonction avec l'ajout de l'asphalte.
Le mélange d'asphalte est déposé dans un dispositif de transport (un convoyeur à lattes, un convoyeur à bande ou un élévateur à godets) pour être transporté vers un silo de stockage. Le silo convertit le flux continu de mélange en un flux discontinu pour le déchargement dans le véhicule de transport.
En général, le même type d'équipement de contrôle des émissions est utilisé sur la centrale à fûts et sur la centrale discontinue. Un collecteur sec primaire et un système d'épurateur humide ou un collecteur secondaire à manches peuvent être utilisés. Si un système d'épuration par voie humide est utilisé, les fines collectées ne peuvent pas être recyclées dans le mélange et sont gaspillées ; si un filtre à manches est utilisé, les fines collectées peuvent être renvoyées en totalité ou en partie dans le tambour mélangeur, ou elles peuvent être gaspillées.
Usine d'asphalte à mélange continu
Dans les usines continues, il n'y a pas d'interruption du cycle de production car le rythme de production n'est pas divisé en lots. Le mélange du matériau a lieu à l'intérieur du tambour sécheur qui est allongé, car il sèche et mélange le matériau en même temps. Puisqu'il n'y a pas de tour de mélange ni d'élévateurs, le système est donc considérablement simplifié, avec une réduction conséquente des coûts de maintenance. L'absence de crible rend cependant nécessaire des contrôles précis au début du cycle de production, avant que les agrégats ne soient introduits dans le séchoir et avant qu'ils ne soient par conséquent déchargés du séchoir sous forme d'asphalte.
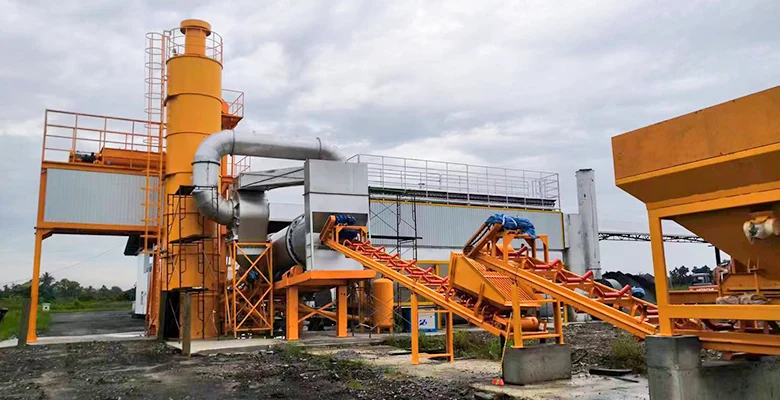
COMPTAGE GLOBAL
Semblable aux centrales d'enrobage discontinues,
le cycle de production des installations en continu commence également par les alimentateurs de froid, où les granulats sont généralement dosés au volume ; si nécessaire, l'extracteur de sable peut être équipé d'un tapis de pesée pour le dosage.
Le contrôle du poids total des granulats vierges, cependant, est effectué dans deux phases différentes du cycle de production dans les deux usines différentes. Dans le type continu, il y a une bande d'alimentation, avant que les agrégats humides ne soient introduits dans le tambour sécheur, où la teneur en humidité est réglée manuellement afin de permettre de soustraire le poids de l'eau. Par conséquent, il est extrêmement important que la teneur en humidité des granulats, en particulier du sable, ait une valeur constante qui soit continuellement contrôlée par des tests de laboratoire fréquents.
DOSAGE DU BITUME
Dans les installations en continu, le dosage du bitume est généralement volumétrique via un compteur de litres à côté de la pompe d'alimentation. Alternativement, il est possible d'installer un compteur de masse, choix nécessaire en cas d'utilisation de bitume modifié, qui nécessite de fréquentes opérations de nettoyage.
Dosage de remplissage
Dans les installations en continu, le système de dosage est normalement volumétrique, utilisant des vis d'alimentation à vitesse variable qui ont remplacé l'ancien système de dosage pneumatique.
Le panneau de contrôle est de type PLC dans toutes nos usines d'exportation. Il s'agit d'une énorme valeur ajoutée car nous pouvons personnaliser l'automate selon nos besoins. Le malaxeur à tambour équipé d'un panneau PLC est une machine différente d'une installation avec panneau à microprocesseur. Le panneau PLC est également sans entretien par rapport au panneau à microprocesseur. Nous croyons toujours qu'il faut donner le meilleur aux clients afin qu'ils puissent garder une longueur d'avance sur leurs concurrents. Tous les fabricants et exportateurs de centrales à tambour d'asphalte ne proposent pas de centrales avec panneau PLC.
Des tests préalables de toutes les usines sont effectués pour s'assurer que tout ce qui quitte notre usine est prêt à fonctionner avec moins de tracas sur le site.
Sinoroader a plus de 30 ans d'expérience dans la fabrication et un produit soutenu par un service professionnel et des pièces de rechange moins chères afin que vous chérissiez et utilisiez votre équipement pour les années à venir.