રસ્તાઓ બનાવવા માટે એગ્રીગેટ્સ અને બિટ્યુમેનને ડામરમાં ફેરવવા માટે થર્મલ મિશ્રણ પ્રક્રિયાની જરૂર પડે છે. આ માટે ડામર મિક્સિંગ પ્લાન્ટ અનિવાર્ય છે. ડામર મિશ્રણ પ્લાન્ટનો હેતુ એક સમાન ડામર પેવિંગ મિશ્રણ બનાવવા માટે એલિવેટેડ તાપમાને એકંદર અને ડામરને એકસાથે મિશ્રિત કરવાનો છે. વપરાયેલ એકંદર એક જ સામગ્રી હોઈ શકે છે, બરછટ અને ઝીણા એકત્રનું મિશ્રણ, ખનિજ ફિલર સાથે અથવા વગર. ઉપયોગમાં લેવાતી બાઈન્ડર સામગ્રી સામાન્ય રીતે ડામર હોય છે પરંતુ તે ડામર મિશ્રણ અથવા વિવિધ સંશોધિત સામગ્રીમાંથી એક હોઈ શકે છે. પ્રવાહી અને પાઉડર સામગ્રી સહિત વિવિધ ઉમેરણોને પણ મિશ્રણમાં સમાવી શકાય છે.
હાલમાં ત્રણ વધુ લોકપ્રિય પ્રકારના ગરમ ડામર મિશ્રણ છોડ છે: બેચ મિક્સ, ડ્રમ મિક્સ અને સતત ડ્રમ મિક્સ. ત્રણેય પ્રકારો સમાન અંતિમ હેતુ પૂરા પાડે છે, અને ડામર મિશ્રણ તેના ઉત્પાદન માટે ઉપયોગમાં લેવાતા છોડના પ્રકારને ધ્યાનમાં લીધા વિના આવશ્યકપણે સમાન હોવું જોઈએ. ત્રણ પ્રકારના છોડ અલગ પડે છે, જો કે, સામગ્રીના સંચાલન અને પ્રવાહમાં, નીચેના વિભાગોમાં વર્ણવ્યા પ્રમાણે.
બેચ મિક્સ ડામર પ્લાન્ટ
ડામર મિશ્રણ પ્લાન્ટ કોઈપણ માર્ગ બાંધકામ કંપની માટે મુખ્ય સાધન છે. કોઈપણ ડામર બેચ મિક્સ પ્લાન્ટ ઓપરેશનમાં ઘણા કાર્યો હોય છે. ડામર બેચના છોડ બેચની શ્રેણીમાં હોટ મિક્સ ડામરનું ઉત્પાદન કરે છે. આ બેચ મિક્સ પ્લાન્ટ્સ સતત પ્રક્રિયામાં હોટ મિક્સ ડામરનું ઉત્પાદન કરે છે. રિસાયકલ કરેલ સામગ્રીનો ઉપયોગ કરીને હોટ મિક્સ ડામરના ઉત્પાદન માટે આ સાધનોમાં ફેરફાર કરવો અને તેનો ઉપયોગ કરવો પણ શક્ય છે. બેચ પ્રકારના છોડમાં વિવિધતા હોય છે જે આરએપી (પુનઃપ્રાપ્ત ડામર પેવમેન્ટ) ઉમેરવાની મંજૂરી આપે છે. પ્રમાણભૂત ડામર બેચ મિક્સ પ્લાન્ટના ઘટકો છે: કોલ્ડફીડ સિસ્ટમ, ડામર સપ્લાય સિસ્ટમ, એગ્રીગેટ ડ્રાયર, મિક્સિંગ ટાવર અને ઉત્સર્જન-નિયંત્રણ સિસ્ટમ. બેચ પ્લાન્ટ ટાવરમાં હોટ એલિવેટર, સ્ક્રીન ડેક, હોટ ડબ્બા, વેઈટ હોપર, ડામર વજનની ડોલ અને પગમિલનો સમાવેશ થાય છે. મિશ્રણમાં વપરાયેલ એકંદરને ભંડારમાંથી દૂર કરવામાં આવે છે અને વ્યક્તિગત કોલ્ડ-ફીડ ડબ્બામાં મૂકવામાં આવે છે. દરેક ડબ્બાના તળિયે ગેટ ખોલવાના કદ અને ડબ્બા હેઠળના કન્વેયર બેલ્ટની ગતિના સંયોજન દ્વારા વિવિધ કદના એકંદર તેમના ડબ્બામાંથી પ્રમાણિત કરવામાં આવે છે. સામાન્ય રીતે, દરેક ડબ્બાની નીચે ફીડર બેલ્ટ તમામ કોલ્ડ-ફીડ ડબ્બા હેઠળ સ્થિત ગેધરીંગ કન્વેયર પર એકંદર જમા કરે છે. એગ્રીગેટને ગેધરીંગ કન્વેયર દ્વારા પરિવહન કરવામાં આવે છે અને ચાર્જીંગ કન્વેયરમાં ટ્રાન્સફર કરવામાં આવે છે. ચાર્જિંગ કન્વેયર પરની સામગ્રીને પછી એકંદર સુકાં સુધી લઈ જવામાં આવે છે.
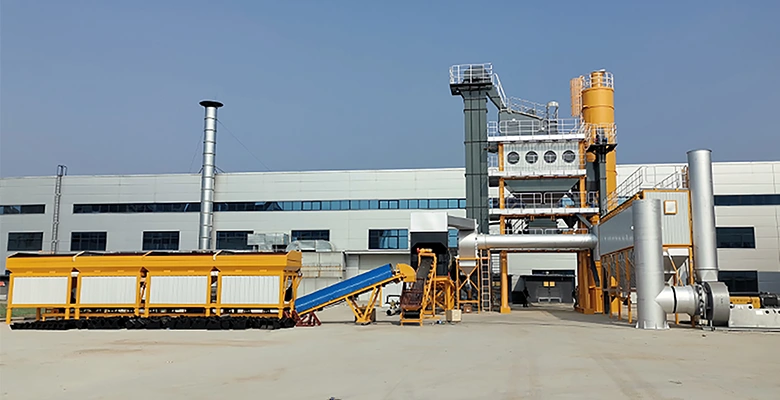
ડ્રાયર કાઉન્ટર-ફ્લો ધોરણે કામ કરે છે. એગ્રીગેટને ઉપરના છેડે ડ્રાયરમાં દાખલ કરવામાં આવે છે અને ડ્રમ રોટેશન (ગુરુત્વાકર્ષણ પ્રવાહ) અને ફરતા ડ્રાયરની અંદર ફ્લાઇટ કન્ફિગરેશન બંને દ્વારા ડ્રમની નીચે ખસેડવામાં આવે છે. બર્નર ડ્રાયરના નીચલા છેડે સ્થિત છે, અને કમ્બશન અને સૂકવણી પ્રક્રિયામાંથી એક્ઝોસ્ટ વાયુઓ સુકાંના ઉપરના છેડા તરફ, એકંદરના પ્રવાહની સામે (કાઉન્ટર ટુ) જાય છે. એક્ઝોસ્ટ વાયુઓ દ્વારા એકંદર ગૂંચવવામાં આવે છે, સામગ્રીને ગરમ અને સૂકવવામાં આવે છે. એક્ઝોસ્ટ ગેસ સ્ટ્રીમના ભાગ રૂપે ડ્રાયરમાંથી ભેજ દૂર કરવામાં આવે છે અને હાથ ધરવામાં આવે છે.
ગરમ, શુષ્ક એકંદર પછી નીચલા છેડે સુકાંમાંથી છોડવામાં આવે છે. ગરમ એકંદર સામાન્ય રીતે બકેટ એલિવેટર દ્વારા પ્લાન્ટ મિક્સિંગ ટાવરની ટોચ પર લઈ જવામાં આવે છે. એલિવેટરમાંથી ડિસ્ચાર્જ થવા પર, એકંદર સામાન્ય રીતે વાઇબ્રેટિંગ સ્ક્રીનના સમૂહમાંથી પસાર થાય છે, સામાન્ય રીતે, ચાર હોટ સ્ટોરેજ ડબ્બામાંથી એક. શ્રેષ્ઠ એકંદર સામગ્રી તમામ સ્ક્રીનમાંથી સીધી નંબર 1 હોટ બિનમાં જાય છે; બરછટ એકંદર કણો દ્વારા અલગ કરવામાં આવે છે
વિવિધ કદની સ્ક્રીનો અને અન્ય હોટ ડબ્બામાંથી એકમાં જમા કરવામાં આવે છે. હોટ ડબ્બામાં એગ્રીગેટનું વિભાજન એ સ્ક્રીન ડેકમાં ઉપયોગમાં લેવાતા સ્ક્રીનના ઓપનિંગ્સના કદ અને કોલ્ડ-ફીડ ડબ્બામાં એગ્રીગેટનું ક્રમાંકન પર આધાર રાખે છે.
દરેક ડબ્બાના તળિયે આવેલા ગેટમાંથી વેઇટ હોપરમાં વિસર્જિત ન થાય ત્યાં સુધી ગરમ, સૂકવવામાં આવેલ અને માપ બદલાયેલ એકંદરને ગરમ ડબ્બામાં રાખવામાં આવે છે. દરેક એકંદરનું યોગ્ય પ્રમાણ વજન દ્વારા નક્કી કરવામાં આવે છે.
એગ્રીગેટનું પ્રમાણ અને વજન કરવામાં આવી રહ્યું છે તે જ સમયે, ડામરને તેની સ્ટોરેજ ટાંકીમાંથી પગમિલની બરાબર ઉપર ટાવર પર સ્થિત અલગ ગરમ વજનની બકેટમાં પમ્પ કરવામાં આવી રહ્યો છે. સામગ્રીની યોગ્ય માત્રાને ડોલમાં તોલવામાં આવે છે અને પગમિલમાં ખાલી ન થાય ત્યાં સુધી તેને પકડી રાખવામાં આવે છે. વજનના હોપરમાં એકંદર ટ્વીન-શાફ્ટ પગમિલમાં ખાલી કરવામાં આવે છે, અને વિવિધ એકંદર અપૂર્ણાંકો ખૂબ જ ટૂંકા ગાળા માટે - સામાન્ય રીતે 5 સેકન્ડથી ઓછા સમય માટે મિશ્રિત થાય છે. આ સંક્ષિપ્ત સૂકા-મિશ્રણ સમય પછી, વજનની ડોલમાંથી ડામર છોડવામાં આવે છે.
પગમિલમાં, અને ભીના મિશ્રણનો સમય શરૂ થાય છે. એકંદર સાથે ડામરને મિશ્રિત કરવા માટેનો સમય ડામર સામગ્રીની પાતળી ફિલ્મ સાથે એકંદર કણોને સંપૂર્ણપણે કોટ કરવા માટે જરૂરી કરતાં વધુ ન હોવો જોઈએ - સામાન્ય રીતે 25 થી 35 સેકન્ડની રેન્જમાં, આ શ્રેણીના નીચલા છેડા સાથે. પગમિલ માટે છે જે સારી સ્થિતિમાં છે. પગમિલમાં મિશ્રિત બેચનું કદ 1.81 થી 5.44 ટન (2 થી 6 ટન) ની રેન્જમાં હોઈ શકે છે.
જ્યારે મિશ્રણ પૂર્ણ કરવામાં આવે છે, ત્યારે પગમિલના તળિયેના દરવાજા ખોલવામાં આવે છે, અને મિશ્રણને હૉલ વાહનમાં અથવા કન્વેઇંગ ડિવાઇસમાં છોડવામાં આવે છે જે મિશ્રણને સિલોમાં લઈ જાય છે જેમાંથી ટ્રક બેચ ફેશનમાં લોડ કરવામાં આવશે. મોટાભાગના બેચ પ્લાન્ટ્સ માટે, પગમિલના દરવાજા ખોલવા અને મિશ્રણને ડિસ્ચાર્જ કરવા માટે જરૂરી સમય આશરે 5 થી 7 સેકન્ડનો છે. બેચ માટે મિશ્રણનો કુલ સમય (ડ્રાય-મિક્સ ટાઈમ + વેટ-મિક્સ ટાઈમ + મિક્સ ડિસ્ચાર્જ ટાઈમ) લગભગ 40 સેકન્ડ જેટલો ટૂંકો હોઈ શકે છે, પરંતુ સામાન્ય રીતે કુલ મિશ્રણનો સમય લગભગ 45 સેકન્ડનો હોય છે.
પ્લાન્ટ ઉત્સર્જન-નિયંત્રણ ઉપકરણોથી સજ્જ છે, જેમાં પ્રાથમિક અને ગૌણ સંગ્રહ પ્રણાલીનો સમાવેશ થાય છે. ડ્રાય કલેક્ટર અથવા નોકઆઉટ બોક્સ સામાન્ય રીતે પ્રાથમિક કલેક્ટર તરીકે ઉપયોગમાં લેવાય છે. કાં તો ભીની સ્ક્રબર સિસ્ટમ અથવા, વધુ વખત, ડ્રાય ફેબ્રિક ફિલ્ટર સિસ્ટમ (બેગહાઉસ) નો ઉપયોગ ડ્રાયરમાંથી બહાર નીકળતા એક્ઝોસ્ટ વાયુઓમાંથી રજકણોને દૂર કરવા અને સ્ટેક દ્વારા વાતાવરણમાં સ્વચ્છ હવા મોકલવા માટે ગૌણ સંગ્રહ સિસ્ટમ તરીકે કરી શકાય છે. .
જો આરએપીને મિશ્રણમાં સામેલ કરવામાં આવે, તો તેને એક અલગ કોલ્ડ-ફીડ ડબ્બામાં મૂકવામાં આવે છે જેમાંથી તેને પ્લાન્ટ સુધી પહોંચાડવામાં આવે છે. આરએપી ત્રણ સ્થાનોમાંથી એકમાં નવા એકંદરમાં ઉમેરી શકાય છે: ગરમ એલિવેટરની નીચે; ગરમ ડબ્બા; અથવા, સામાન્ય રીતે, વજન હોપર. સુપરહીટેડ નવા એગ્રીગેટ અને પુનઃપ્રાપ્ત સામગ્રી વચ્ચે હીટ ટ્રાન્સફર શરૂ થાય છે કે તરત જ બે સામગ્રી સંપર્કમાં આવે છે અને પગમિલમાં મિશ્રણ પ્રક્રિયા દરમિયાન ચાલુ રહે છે.
ડ્રમ મિક્સ ડામર પ્લાન્ટ
બેચના પ્રકાર સાથે સરખામણી કરીએ તો, ડ્રમ મિક્સ ડામર પ્લાન્ટમાં ઓછી થર્મલ નુકશાન, ઓછી કામ કરવાની શક્તિ, ઓવરફ્લો નહીં, ઓછી ધૂળ ઉડતી અને સ્થિર તાપમાન નિયંત્રણ છે. કંટ્રોલ સિસ્ટમ ચોક્કસ પ્રમાણસર આઉટપુટની ખાતરી કરવા માટે, એગ્રીગેટ્સ ફ્લો રેટ અને પ્રી-સેટિંગ ડામર-એગ્રીગેટ્સ રેશિયો અનુસાર આપમેળે ડામર પ્રવાહ દરને સમાયોજિત કરે છે. ડામર ડ્રમ મિક્સ પ્લાન્ટ એ એવા છોડના પ્રકારો છે કે જેને સતત મિશ્રણ છોડ તરીકે વર્ગીકૃત કરવામાં આવે છે, જે સતત પ્રક્રિયામાં હોટ મિક્સ ડામરનું ઉત્પાદન કરે છે.
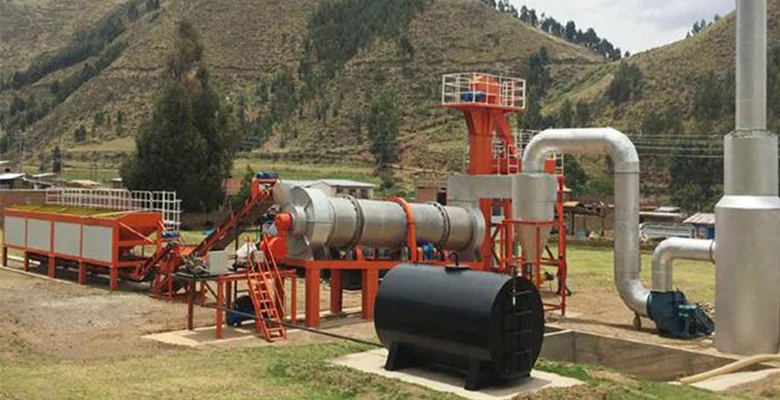
સામાન્ય રીતે HMA બેચ અને ડ્રમ-મિક્સ પ્લાન્ટ્સ પર કોલ્ડ-ફીડ સિસ્ટમ્સ સમાન હોય છે. દરેકમાં કોલ્ડફીડ ડબ્બા, ફીડર કન્વેયર, ગેધરીંગ કન્વેયર અને ચાર્જીંગ કન્વેયરનો સમાવેશ થાય છે. મોટાભાગના ડ્રમ-મિક્સ પ્લાન્ટ્સ પર અને કેટલાક બેચ પ્લાન્ટ્સ પર, સિસ્ટમમાં અમુક સમયે એક સ્કેલ્પિંગ સ્ક્રીનનો સમાવેશ થાય છે. જો RAP પણ પ્લાન્ટમાં રિસાયકલ કરેલ મિશ્રણ પેદા કરવા માટે ખવડાવવામાં આવે છે, તો વધારાની સામગ્રીને હેન્ડલ કરવા માટે વધારાના કોલ્ડ-ફીડ ડબ્બા અથવા ડબ્બા, ફીડર બેલ્ટ અને/અથવા ગેધરીંગ કન્વેયર, સ્કેલ્પીંગ સ્ક્રીન અને ચાર્જીંગ કન્વેયર જરૂરી છે. ડ્રમ-મિક્સ પ્લાન્ટમાં પાંચ મુખ્ય ઘટકોનો સમાવેશ થાય છે: કોલ્ડ-ફીડ સિસ્ટમ, ડામર સપ્લાય સિસ્ટમ, ડ્રમ મિક્સર, સર્જ અથવા સ્ટોરેજ સિલોઝ અને ઉત્સર્જન નિયંત્રણ સાધનો.
કોલ્ડ-ફીડ ડબ્બાનો ઉપયોગ છોડની સામગ્રીના પ્રમાણ માટે થાય છે. દરેક ડબ્બા હેઠળ વેરિયેબલ-સ્પીડ ફીડર બેલ્ટનો ઉપયોગ થાય છે. આમ દરેક ડબ્બામાંથી ખેંચવામાં આવેલ એકંદરની માત્રાને અલગ-અલગ કદની સામગ્રીની ચોક્કસ ડિલિવરી પૂરી પાડવા માટે ગેટ ખોલવાના કદ અને ફીડર બેલ્ટની ઝડપ બંને દ્વારા નિયંત્રિત કરી શકાય છે. દરેક ફીડર બેલ્ટ પરની કુલ રકમ એક ગેધરીંગ કન્વેયર પર જમા કરવામાં આવે છે જે તમામ કોલ્ડ-ફીડ ડબ્બાઓની નીચે ચાલે છે. સંયુક્ત સામગ્રી સામાન્ય રીતે સ્કેલ્પિંગ સ્ક્રીનમાંથી પસાર થાય છે અને પછી ડ્રમ મિક્સરમાં પરિવહન માટે ચાર્જિંગ કન્વેયરમાં સ્થાનાંતરિત થાય છે.
ચાર્જિંગ કન્વેયર બે ઉપકરણોથી સજ્જ છે જેનો ઉપયોગ પ્લાન્ટને વિતરિત કરવામાં આવતા એકંદર જથ્થો નક્કી કરવા માટે થાય છે: કન્વેયર બેલ્ટની નીચે એક વજનનો પુલ તેની ઉપરથી પસાર થતા એકંદરના વજનને માપે છે, અને સેન્સર બેલ્ટની ગતિ નક્કી કરે છે. આ બે મૂલ્યોનો ઉપયોગ ડ્રમ મિક્સરમાં દાખલ થતાં, કલાક દીઠ ટન (ટન) માં એકંદર ભીના વજનની ગણતરી કરવા માટે થાય છે. પ્લાન્ટ કોમ્પ્યુટર, ઇનપુટ મૂલ્ય તરીકે પૂરા પાડવામાં આવેલ એકંદરમાં ભેજની માત્રા સાથે, મિશ્રણમાં જરૂરી ડામરની સાચી માત્રા નક્કી કરવા માટે ભીના વજનને શુષ્ક વજનમાં રૂપાંતરિત કરે છે.
પરંપરાગત ડ્રમ મિક્સર એ સમાંતર-પ્રવાહ પ્રણાલી છે - એક્ઝોસ્ટ વાયુઓ અને એકંદરે એક જ દિશામાં આગળ વધે છે. બર્નર ડ્રમના ઉપરના છેડે (એગ્રિગેટ ઇનલેટ એન્ડ) પર સ્થિત છે. એકંદર ડ્રમમાં પ્રવેશે છે કાં તો બર્નરની ઉપરના ઝુકાવમાંથી અથવા બર્નરની નીચે સ્લિંગર કન્વેયર પર. ગુરુત્વાકર્ષણના સંયોજન અને ડ્રમની અંદર સ્થિત ફ્લાઇટ્સનું રૂપરેખાંકન દ્વારા એકંદર ડ્રમ નીચે ખસેડવામાં આવે છે. જેમ જેમ તે મુસાફરી કરે છે, એકંદર ગરમ થાય છે અને ભેજ દૂર થાય છે. હીટ-ટ્રાન્સફર પ્રક્રિયામાં મદદ કરવા માટે ડ્રમની લંબાઈના મધ્યબિંદુની નજીક એકંદરનો ગાઢ પડદો બાંધવામાં આવે છે.
જો RAP ને નવા એગ્રીગેટમાં ઉમેરવામાં આવે છે, તો તે તેના પોતાના કોલ્ડ-ફીડ બિન અને ગેધરીંગ/ચાર્જિંગ કન્વેયર સિસ્ટમમાંથી ડ્રમની લંબાઈ (સ્પ્લિટ-ફીડ સિસ્ટમ) ના કેન્દ્રની નજીક સ્થિત ઇનલેટમાં જમા થાય છે. આ પ્રક્રિયામાં, આરએપી એન્ટ્રી પોઈન્ટના નવા એકંદર અપસ્ટ્રીમના પડદા દ્વારા પુનઃપ્રાપ્ત સામગ્રીને ઉચ્ચ-તાપમાન એક્ઝોસ્ટ વાયુઓથી સુરક્ષિત કરવામાં આવે છે. જ્યારે ઉચ્ચ RAP સામગ્રી સાથેના મિશ્રણનો ઉપયોગ કરવામાં આવે છે, ત્યારે પ્રક્રિયામાં RAP વધુ ગરમ થવાની શક્યતા વધુ છે. આના પરિણામે ડ્રમમાંથી ધુમાડો નીકળી શકે છે અથવા RAP ને નુકસાન થઈ શકે છે.
નવી એકંદર અને પુનઃપ્રાપ્ત સામગ્રી, જો ઉપયોગમાં લેવામાં આવે તો, ડ્રમના પાછળના ભાગમાં એકસાથે ખસેડો. ડામરને સ્ટોરેજ ટાંકીમાંથી પંપ દ્વારા ખેંચવામાં આવે છે અને મીટર દ્વારા ખવડાવવામાં આવે છે, જ્યાં ડામરનું યોગ્ય પ્રમાણ નક્કી કરવામાં આવે છે. બાઈન્ડર સામગ્રીને પછી એક પાઇપ દ્વારા મિક્સિંગ ડ્રમના પાછળના ભાગમાં પહોંચાડવામાં આવે છે, જ્યાં ડામરને એકંદર પર ઇન્જેક્ટ કરવામાં આવે છે. એકંદર કોટિંગ થાય છે કારણ કે સામગ્રી એકસાથે ટમ્બલ થાય છે અને ડ્રમના ડિસ્ચાર્જ છેડે ખસેડવામાં આવે છે. ખનિજ પૂરક અથવા બેગહાઉસ દંડ, અથવા બંને, ડ્રમના પાછળના ભાગમાં પણ ઉમેરવામાં આવે છે, કાં તો ડામરના ઉમેરા સાથે અથવા તેના ઉમેરા સાથે.
ડામર મિશ્રણને સ્ટોરેજ સિલો સુધી પરિવહન માટે કન્વેઇંગ ડિવાઇસ (ડ્રેગ સ્લેટ કન્વેયર, બેલ્ટ કન્વેયર અથવા બકેટ એલિવેટર) માં જમા કરવામાં આવે છે. સિલો મિશ્રણના સતત પ્રવાહને હૉલ વાહનમાં ડિસ્ચાર્જ કરવા માટે બેચ ફ્લોમાં રૂપાંતરિત કરે છે.
સામાન્ય રીતે, બેચ પ્લાન્ટની જેમ ડ્રમ-મિક્સ પ્લાન્ટ પર સમાન પ્રકારના ઉત્સર્જન-નિયંત્રણ સાધનોનો ઉપયોગ થાય છે. પ્રાથમિક ડ્રાય કલેક્ટર અને કાં તો વેટ સ્ક્રબર સિસ્ટમ અથવા બેગહાઉસ સેકન્ડરી કલેક્ટરનો ઉપયોગ કરી શકાય છે. જો વેટ સ્ક્રબર સિસ્ટમનો ઉપયોગ કરવામાં આવે, તો એકત્રિત કરવામાં આવેલ દંડને ફરીથી મિશ્રણમાં રિસાયકલ કરી શકાતો નથી અને તે વેડફાઈ જાય છે; જો બેગહાઉસનો ઉપયોગ કરવામાં આવે છે, તો એકત્રિત કરવામાં આવેલ દંડ સંપૂર્ણ અથવા આંશિક રીતે મિશ્રણ ડ્રમમાં પરત કરી શકાય છે, અથવા તેનો વ્યય થઈ શકે છે.
સતત મિક્સ ડામર પ્લાન્ટ
સતત છોડમાં ઉત્પાદન ચક્રમાં કોઈ વિક્ષેપ પડતો નથી કારણ કે ઉત્પાદનની લય બેચમાં વિભાજિત થતી નથી. સામગ્રીનું મિશ્રણ ડ્રાયર ડ્રમની અંદર થાય છે જે વિસ્તરેલ હોય છે, કારણ કે તે સૂકાય છે અને તે જ સમયે સામગ્રીને મિશ્રિત કરે છે. ત્યાં કોઈ મિક્સિંગ ટાવર અથવા એલિવેટર્સ ન હોવાથી, આથી જાળવણીના ખર્ચમાં પરિણામી ઘટાડા સાથે, સિસ્ટમ નોંધપાત્ર રીતે સરળ બનાવવામાં આવી છે. જો કે સ્ક્રીનની ગેરહાજરી ઉત્પાદન ચક્રની શરૂઆતમાં, એગ્રીગેટ્સને ડ્રાયરમાં ખવડાવવામાં આવે તે પહેલાં અને પરિણામે તેને ડામર તરીકે ડ્રાયરમાંથી ડિસ્ચાર્જ કરવામાં આવે તે પહેલાં ચોક્કસ નિયંત્રણો જરૂરી બનાવે છે.
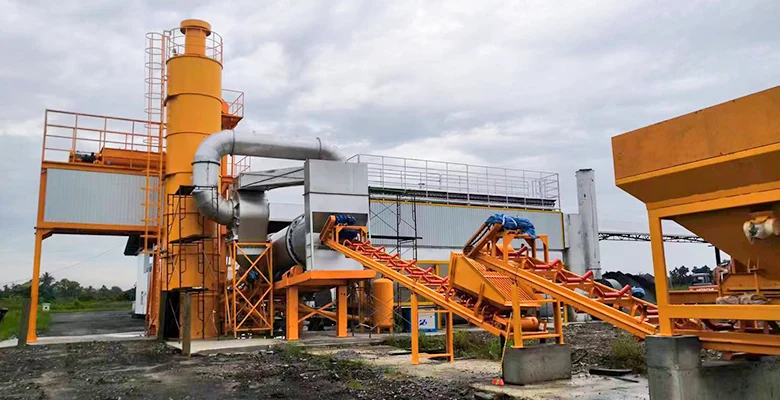
એકંદર મીટરિંગ
બેચ ડામર મિશ્રણ છોડ જેવું જ,
સતત છોડનું ઉત્પાદન ચક્ર પણ ઠંડા ફીડરથી શરૂ થાય છે, જ્યાં એકંદર સામાન્ય રીતે વોલ્યુમ દ્વારા માપવામાં આવે છે; જો જરૂરી હોય તો, રેતી કાઢવાના યંત્રને મીટરિંગ માટે વજન-પટ્ટા સાથે ફીટ કરી શકાય છે.
વર્જિન એગ્રીગેટ્સના કુલ વજનનું નિયંત્રણ, જોકે, બે અલગ-અલગ છોડમાં ઉત્પાદન ચક્રના બે અલગ-અલગ તબક્કામાં પ્રભાવિત થાય છે. સતત પ્રકારમાં એક ફીડ પટ્ટો હોય છે, ભેજવાળા એકત્રને સુકાંના ડ્રમમાં ખવડાવવામાં આવે તે પહેલાં, જ્યાં પાણીના વજનને બાદ કરી શકાય તે માટે ભેજનું પ્રમાણ મેન્યુઅલી સેટ કરવામાં આવે છે. આથી એગ્રીગેટ્સમાં ભેજનું પ્રમાણ, ખાસ કરીને રેતીનું સતત મૂલ્ય હોવું અત્યંત અગત્યનું છે જેનું વારંવાર પ્રયોગશાળા પરીક્ષણો દ્વારા સતત નિરીક્ષણ કરવામાં આવે છે.
બિટ્યુમેન મીટરિંગ
સતત છોડમાં બિટ્યુમેન મીટરિંગ સામાન્ય રીતે ફીડ પંપના અનુગામી લિટર-કાઉન્ટર દ્વારા વોલ્યુમેટ્રિક હોય છે. વૈકલ્પિક રીતે, સામૂહિક કાઉન્ટર સ્થાપિત કરવું શક્ય છે, જો સંશોધિત બિટ્યુમેનનો ઉપયોગ કરવામાં આવે તો તે જરૂરી પસંદગી છે, જેને વારંવાર સફાઈ કામગીરીની જરૂર પડે છે.
ફિલર મીટરિંગ
સતત છોડમાં મીટરિંગ સિસ્ટમ સામાન્ય રીતે વોલ્યુમેટ્રિક હોય છે, જેમાં વેરિયેબલ-સ્પીડ ફીડ સ્ક્રૂનો ઉપયોગ કરવામાં આવે છે જેણે અગાઉની ન્યુમેટિક મીટરિંગ સિસ્ટમને બદલી નાખી છે.
અમારા તમામ નિકાસ પ્લાન્ટમાં કંટ્રોલ પેનલ પીએલસી પ્રકારનું છે. આ એક વિશાળ મૂલ્યવર્ધન છે કારણ કે અમે અમારી જરૂરિયાત મુજબ PLC કસ્ટમાઇઝ કરી શકીએ છીએ. ડ્રમ મિક્સર જે પીએલસી પેનલથી સજ્જ છે તે માઇક્રોપ્રોસેસર પેનલવાળા પ્લાન્ટ કરતાં અલગ મશીન છે. માઇક્રોપ્રોસેસર પેનલની સરખામણીમાં PLC પેનલ પણ જાળવણી મુક્ત છે. અમે હંમેશા ગ્રાહકોને શ્રેષ્ઠ આપવામાં માનીએ છીએ જેથી તેઓ તેમની સ્પર્ધામાં આગળ રહી શકે. ડામર ડ્રમ પ્લાન્ટના તમામ ઉત્પાદકો અને નિકાસકારો પીએલસી પેનલ સાથે પ્લાન્ટ ઓફર કરતા નથી.
અમારી ફેક્ટરીમાંથી બહાર નીકળતી કોઈપણ વસ્તુ સાઇટ પર ઓછી મુશ્કેલી સાથે કરવા માટે તૈયાર છે તેની ખાતરી કરવા માટે તમામ પ્લાન્ટનું પૂર્વ પરીક્ષણ કરવામાં આવે છે.
સિનોરોડર પાસે 30 વર્ષથી વધુનો મેન્યુફેક્ચરિંગ અનુભવ છે અને પ્રોફેશનલ સર્વિસ અને સસ્તા સ્પેર્સ દ્વારા સમર્થિત પ્રોડક્ટ છે જેથી કરીને તમે આવનારા વર્ષો સુધી તમારા સાધનોનો ઉપયોગ કરો અને તેનો ઉપયોગ કરો.