वर्तमान में तीन प्रकार के गर्म डामर मिश्रण संयंत्र अधिक लोकप्रिय हैं
सड़कें बनाने के लिए समुच्चय और बिटुमेन को डामर में बदलने के लिए थर्मल मिश्रण प्रक्रिया की आवश्यकता होती है। इसके लिए डामर मिश्रण संयंत्र अपरिहार्य है। डामर मिश्रण संयंत्र का उद्देश्य एक सजातीय डामर फ़र्श मिश्रण का उत्पादन करने के लिए ऊंचे तापमान पर समुच्चय और डामर को एक साथ मिश्रित करना है। उपयोग किया जाने वाला समुच्चय एक एकल सामग्री हो सकता है, मोटे और महीन समुच्चय का संयोजन, खनिज भराव के साथ या उसके बिना। उपयोग की जाने वाली बाइंडर सामग्री सामान्यतः डामर होती है, लेकिन डामर इमल्शन या विभिन्न संशोधित सामग्रियों में से एक हो सकती है। तरल और पाउडर सामग्री सहित विभिन्न योजकों को भी मिश्रण में शामिल किया जा सकता है।
वर्तमान में हॉट डामर मिक्सिंग प्लांट के तीन और लोकप्रिय प्रकार हैं: बैच मिक्स, ड्रम मिक्स, और निरंतर ड्रम मिक्स। सभी तीन प्रकार एक ही अंतिम उद्देश्य की पूर्ति करते हैं, और डामर मिश्रण अनिवार्य रूप से समान होना चाहिए, भले ही इसके निर्माण के लिए उपयोग किए जाने वाले पौधे का प्रकार कुछ भी हो। हालाँकि, तीन प्रकार के पौधे संचालन और सामग्री के प्रवाह में भिन्न होते हैं, जैसा कि निम्नलिखित अनुभागों में वर्णित है।
बैच मिक्स डामर प्लांटडामर मिक्सिंग प्लांट किसी भी सड़क निर्माण कंपनी के लिए प्रमुख उपकरण है। किसी भी डामर बैच मिक्स प्लांट ऑपरेशन के कई कार्य होते हैं। डामर बैच संयंत्र बैचों की एक श्रृंखला में गर्म मिश्रण डामर का उत्पादन करते हैं। ये बैच मिक्स प्लांट एक सतत प्रक्रिया में हॉट मिक्स डामर का उत्पादन करते हैं। पुनर्नवीनीकरण सामग्री का उपयोग करके गर्म मिश्रण डामर के उत्पादन के लिए इस उपकरण को बदलना और उपयोग करना भी संभव है। बैच प्रकार के पौधों में विविधताएं होती हैं जो आरएपी (पुनः प्राप्त डामर फुटपाथ) को जोड़ने की अनुमति देती हैं। एक मानक डामर बैच मिक्स प्लांट के घटक हैं: कोल्डफ़ीड सिस्टम, डामर आपूर्ति प्रणाली, एग्रीगेट ड्रायर, मिक्सिंग टॉवर और उत्सर्जन-नियंत्रण प्रणाली। बैच प्लांट टावर में एक हॉट एलिवेटर, एक स्क्रीन डेक, हॉट डिब्बे, एक वेट हॉपर, एक डामर वेट बाल्टी और एक पगमिल होता है। मिश्रण में उपयोग किए गए समुच्चय को भंडार से हटा दिया जाता है और अलग-अलग कोल्ड-फीड डिब्बे में रखा जाता है। प्रत्येक बिन के नीचे गेट के उद्घाटन के आकार और बिन के नीचे कन्वेयर बेल्ट की गति के संयोजन से विभिन्न आकारों के समुच्चय को उनके डिब्बे से बाहर निकाला जाता है। आम तौर पर, प्रत्येक बिन के नीचे एक फीडर बेल्ट सभी कोल्ड-फीड डिब्बे के नीचे स्थित एक एकत्रित कन्वेयर पर समुच्चय जमा करता है। समुच्चय को संग्रहण कन्वेयर द्वारा ले जाया जाता है और चार्जिंग कन्वेयर में स्थानांतरित किया जाता है। फिर चार्जिंग कन्वेयर पर मौजूद सामग्री को एग्रीगेट ड्रायर तक ले जाया जाता है।
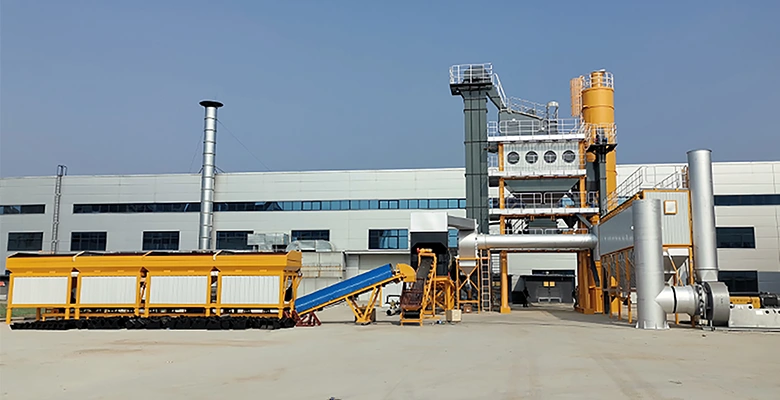
ड्रायर काउंटर-फ्लो आधार पर काम करता है। समुच्चय को ऊपरी छोर पर ड्रायर में पेश किया जाता है और ड्रम घूर्णन (गुरुत्वाकर्षण प्रवाह) और घूर्णन ड्रायर के अंदर उड़ान विन्यास दोनों द्वारा ड्रम के नीचे ले जाया जाता है। बर्नर ड्रायर के निचले सिरे पर स्थित होता है, और दहन और सुखाने की प्रक्रिया से निकलने वाली गैसें, समुच्चय के प्रवाह के विपरीत, ड्रायर के ऊपरी सिरे की ओर बढ़ती हैं। जैसे ही समुच्चय को निकास गैसों के माध्यम से गिराया जाता है, सामग्री को गर्म किया जाता है और सुखाया जाता है। निकास गैस धारा के हिस्से के रूप में नमी को हटा दिया जाता है और ड्रायर से बाहर ले जाया जाता है।
फिर गर्म, शुष्क समुच्चय को निचले सिरे पर ड्रायर से निकाल दिया जाता है। गर्म समुच्चय को आमतौर पर बाल्टी लिफ्ट द्वारा प्लांट मिक्सिंग टॉवर के शीर्ष तक ले जाया जाता है। लिफ्ट से डिस्चार्ज होने पर, समुच्चय आमतौर पर कंपन स्क्रीन के एक सेट से होकर गुजरता है, आमतौर पर, चार गर्म भंडारण डिब्बे में से एक में। बेहतरीन समुच्चय सामग्री सभी स्क्रीनों के माध्यम से सीधे नंबर 1 हॉट बिन में जाती है; मोटे समुच्चय कणों को अलग किया जाता है
अलग-अलग आकार की स्क्रीनें और अन्य गर्म डिब्बे में जमा की गईं। गर्म डिब्बे में समुच्चय का पृथक्करण स्क्रीन डेक में उपयोग की जाने वाली स्क्रीन में खुलेपन के आकार और कोल्ड-फीड डिब्बे में समुच्चय के क्रम पर निर्भर करता है।
गर्म, सूखे और परिवर्तित समुच्चय को गर्म डिब्बे में रखा जाता है जब तक कि प्रत्येक बिन के नीचे एक गेट से वजन हॉपर में छुट्टी नहीं दी जाती है। प्रत्येक समुच्चय का सही अनुपात वजन द्वारा निर्धारित होता है।
उसी समय जब समुच्चय को आनुपातिक और तौला जा रहा है, डामर को उसके भंडारण टैंक से पगमिल के ठीक ऊपर टॉवर पर स्थित एक अलग गर्म तौल बाल्टी में पंप किया जा रहा है। सामग्री की उचित मात्रा को बाल्टी में तौला जाता है और पगमिल में खाली होने तक रखा जाता है। वेट हॉपर में समुच्चय को ट्विन-शाफ्ट पगमिल में खाली कर दिया जाता है, और विभिन्न समुच्चय अंशों को बहुत ही कम समय के लिए एक साथ मिलाया जाता है - आमतौर पर 5 सेकंड से भी कम समय के लिए। इस संक्षिप्त शुष्क-मिश्रण समय के बाद, वेट बकेट से डामर निकल जाता है।
पगमिल में, और गीला-मिश्रण का समय शुरू होता है। समुच्चय के साथ डामर के मिश्रण के लिए मिश्रण का समय डामर सामग्री की एक पतली फिल्म के साथ समुच्चय कणों को पूरी तरह से कोट करने के लिए आवश्यक समय से अधिक नहीं होना चाहिए - आमतौर पर 25 से 35 सेकंड की सीमा में, इस सीमा के निचले सिरे के साथ एक पगमिल के लिए जो अच्छी स्थिति में है। पगमिल में मिश्रित बैच का आकार 1.81 से 5.44 टन (2 से 6 टन) तक हो सकता है।
जब मिश्रण पूरा हो जाता है, तो पगमिल के नीचे के गेट खोल दिए जाते हैं, और मिश्रण को ढोने वाले वाहन में या एक परिवहन उपकरण में छोड़ दिया जाता है जो मिश्रण को एक साइलो में ले जाता है जहां से ट्रकों को बैच फैशन में लोड किया जाएगा। अधिकांश बैच पौधों के लिए, पगमिल गेट खोलने और मिश्रण को डिस्चार्ज करने में लगभग 5 से 7 सेकंड का समय लगता है। एक बैच के लिए कुल मिश्रण समय (सूखा-मिश्रण समय + गीला-मिश्रण समय + मिश्रण निर्वहन समय) लगभग 40 सेकंड जितना कम हो सकता है, लेकिन आम तौर पर, कुल मिश्रण समय लगभग 45 सेकंड होता है।
संयंत्र उत्सर्जन-नियंत्रण उपकरणों से सुसज्जित है, जिसमें प्राथमिक और माध्यमिक दोनों संग्रह प्रणालियाँ शामिल हैं। ड्राई कलेक्टर या नॉकआउट बॉक्स का उपयोग आमतौर पर प्राथमिक कलेक्टर के रूप में किया जाता है। या तो गीले स्क्रबर सिस्टम या, अधिक बार, सूखे कपड़े फिल्टर सिस्टम (बैगहाउस) का उपयोग ड्रायर से निकलने वाली निकास गैसों से कण पदार्थ को हटाने और स्टैक के माध्यम से वातावरण में स्वच्छ हवा भेजने के लिए द्वितीयक संग्रह प्रणाली के रूप में किया जा सकता है। .
यदि आरएपी को मिश्रण में शामिल किया गया है, तो इसे एक अलग कोल्ड-फीड बिन में रखा जाता है, जहां से इसे संयंत्र तक पहुंचाया जाता है। आरएपी को तीन स्थानों में से एक में नए समुच्चय में जोड़ा जा सकता है: गर्म लिफ्ट के नीचे; गर्म डिब्बे; या, आमतौर पर, वेट हॉपर। सुपरहीटेड नए समुच्चय और पुनः प्राप्त सामग्री के बीच गर्मी हस्तांतरण जैसे ही दो सामग्रियों के संपर्क में आता है शुरू हो जाता है और पगमिल में मिश्रण प्रक्रिया के दौरान जारी रहता है।
ड्रम मिक्स डामर प्लांटबैच प्रकार की तुलना में, ड्रम मिक्स डामर प्लांट में कम तापीय हानि, कम कार्य शक्ति, कोई अतिप्रवाह, कम धूल उड़ना और स्थिर तापमान नियंत्रण होता है। सटीक आनुपातिक आउटपुट सुनिश्चित करने के लिए, नियंत्रण प्रणाली स्वचालित रूप से समुच्चय प्रवाह दर और पूर्व-सेटिंग डामर-समुच्चय अनुपात के अनुसार डामर प्रवाह दर को समायोजित करती है। डामर ड्रम मिक्स प्लांट उन पौधों के प्रकार हैं जिन्हें निरंतर मिश्रण संयंत्रों के रूप में वर्गीकृत किया जाता है, जो निरंतर प्रक्रिया में गर्म मिश्रण डामर का उत्पादन करते हैं।
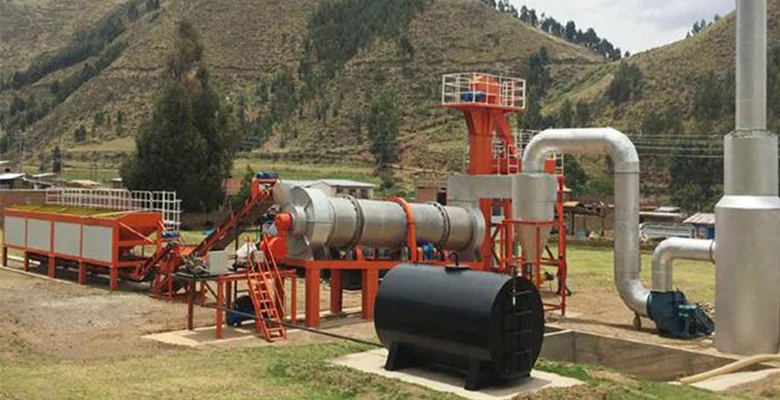
आमतौर पर एचएमए बैच और ड्रम-मिक्स प्लांट पर कोल्ड-फीड सिस्टम समान होते हैं। प्रत्येक में कोल्डफ़ीड डिब्बे, फीडर कन्वेयर, एक संग्रहण कन्वेयर और एक चार्जिंग कन्वेयर शामिल हैं। अधिकांश ड्रम-मिक्स संयंत्रों और कुछ बैच संयंत्रों पर, किसी बिंदु पर सिस्टम में एक स्केलिंग स्क्रीन शामिल की जाती है। यदि आरएपी को पुनर्नवीनीकरण मिश्रण का उत्पादन करने के लिए संयंत्र में भी डाला जा रहा है, तो अतिरिक्त सामग्री को संभालने के लिए एक अतिरिक्त कोल्ड-फीड बिन या डिब्बे, फीडर बेल्ट और/या इकट्ठा करने वाला कन्वेयर, स्केलिंग स्क्रीन और चार्जिंग कन्वेयर आवश्यक हैं। ड्रम-मिक्स प्लांट में पांच प्रमुख घटक होते हैं: कोल्ड-फीड सिस्टम, डामर आपूर्ति प्रणाली, ड्रम मिक्सर, सर्ज या स्टोरेज साइलो और उत्सर्जन नियंत्रण उपकरण।
कोल्ड-फीड डिब्बे का उपयोग पौधे की सामग्री को अनुपातित करने के लिए किया जाता है। प्रत्येक बिन के नीचे एक वैरिएबल-स्पीड फीडर बेल्ट का उपयोग किया जाता है। इस प्रकार विभिन्न आकार की सामग्रियों की सटीक डिलीवरी प्रदान करने के लिए प्रत्येक बिन से निकाले गए समुच्चय की मात्रा को गेट खोलने के आकार और फीडर बेल्ट की गति दोनों द्वारा नियंत्रित किया जा सकता है। प्रत्येक फीडर बेल्ट पर एकत्रीकरण को एक एकत्रित कन्वेयर पर जमा किया जाता है जो सभी कोल्ड-फीड डिब्बे के नीचे चलता है। संयुक्त सामग्री को आम तौर पर स्केलिंग स्क्रीन के माध्यम से पारित किया जाता है और फिर ड्रम मिक्सर तक परिवहन के लिए चार्जिंग कन्वेयर में स्थानांतरित किया जाता है।
चार्जिंग कन्वेयर दो उपकरणों से सुसज्जित है जिनका उपयोग संयंत्र में वितरित किए जाने वाले समुच्चय की मात्रा निर्धारित करने के लिए किया जाता है: कन्वेयर बेल्ट के नीचे एक वजन पुल इसके ऊपर से गुजरने वाले समुच्चय के वजन को मापता है, और एक सेंसर बेल्ट की गति निर्धारित करता है। इन दो मानों का उपयोग ड्रम मिक्सर में प्रवेश करने वाले टन (टन) प्रति घंटे में समुच्चय के गीले वजन की गणना करने के लिए किया जाता है। प्लांट कंप्यूटर, इनपुट मान के रूप में प्रदान की गई समुच्चय में नमी की मात्रा के साथ, मिश्रण में आवश्यक डामर की सही मात्रा निर्धारित करने के लिए गीले वजन को सूखे वजन में परिवर्तित करता है।
पारंपरिक ड्रम मिक्सर एक समानांतर-प्रवाह प्रणाली है - निकास गैसें और समुच्चय एक ही दिशा में चलते हैं। बर्नर ड्रम के ऊपरी सिरे (एग्रीगेट इनलेट सिरे) पर स्थित होता है। समुच्चय या तो बर्नर के ऊपर झुके हुए ढलान से या बर्नर के नीचे स्लिंगर कन्वेयर पर ड्रम में प्रवेश करता है। गुरुत्वाकर्षण के संयोजन और ड्रम के अंदर स्थित उड़ानों के विन्यास द्वारा समुच्चय को ड्रम के नीचे ले जाया जाता है। जैसे ही यह यात्रा करता है, समुच्चय गर्म हो जाता है और नमी दूर हो जाती है। गर्मी-स्थानांतरण प्रक्रिया में सहायता के लिए ड्रम की लंबाई के मध्य बिंदु के पास समुच्चय का एक घना पर्दा बनाया जाता है।
यदि आरएपी को नए समुच्चय में जोड़ा जाता है, तो इसे अपने स्वयं के कोल्ड-फीड बिन और संग्रहण/चार्जिंग कन्वेयर सिस्टम से ड्रम लंबाई (स्प्लिट-फीड सिस्टम) के केंद्र के पास स्थित इनलेट में जमा किया जाता है। इस प्रक्रिया में, पुनः प्राप्त सामग्री को आरएपी प्रवेश बिंदु के अपस्ट्रीम में नए समुच्चय के पर्दे द्वारा उच्च तापमान निकास गैसों से संरक्षित किया जाता है। जब उच्च आरएपी सामग्री वाले मिश्रण का उपयोग किया जाता है, तो यह अधिक संभावना है कि इस प्रक्रिया में आरएपी ज़्यादा गरम हो जाएगा। इसके परिणामस्वरूप ड्रम से धुआं निकल सकता है या आरएपी को नुकसान हो सकता है।
नया समुच्चय और पुनः प्राप्त सामग्री, यदि उपयोग की जाती है, तो ड्रम के पिछले हिस्से में एक साथ चली जाती है। डामर को भंडारण टैंक से एक पंप द्वारा खींचा जाता है और एक मीटर के माध्यम से डाला जाता है, जहां डामर की उचित मात्रा निर्धारित की जाती है। फिर बाइंडर सामग्री को एक पाइप के माध्यम से मिक्सिंग ड्रम के पीछे पहुंचाया जाता है, जहां डामर को समुच्चय पर इंजेक्ट किया जाता है। समुच्चय की कोटिंग तब होती है जब सामग्रियों को एक साथ गिराया जाता है और ड्रम के डिस्चार्ज सिरे पर ले जाया जाता है। खनिज भराव या बैगहाउस जुर्माना, या दोनों, ड्रम के पीछे, या तो डामर जोड़ने से ठीक पहले या संयोजन में जोड़े जाते हैं।
भंडारण साइलो में परिवहन के लिए डामर मिश्रण को एक संदेशवाहक उपकरण (ड्रैग स्लैट कन्वेयर, बेल्ट कन्वेयर, या बाल्टी एलिवेटर) में जमा किया जाता है। साइलो मिश्रण के निरंतर प्रवाह को ढोने वाले वाहन में निर्वहन के लिए बैच प्रवाह में परिवर्तित करता है।
सामान्य तौर पर, ड्रम-मिक्स प्लांट पर बैच प्लांट की तरह ही उसी प्रकार के उत्सर्जन-नियंत्रण उपकरण का उपयोग किया जाता है। एक प्राथमिक सूखा कलेक्टर और या तो एक गीला स्क्रबर सिस्टम या एक बैगहाउस सेकेंडरी कलेक्टर का उपयोग किया जा सकता है। यदि गीली स्क्रबर प्रणाली का उपयोग किया जाता है, तो एकत्र किए गए जुर्माने को वापस मिश्रण में पुनर्चक्रित नहीं किया जा सकता है और वे बर्बाद हो जाते हैं; यदि बैगहाउस का उपयोग किया जाता है, तो एकत्रित जुर्माना पूरे या आंशिक रूप से मिक्सिंग ड्रम में वापस किया जा सकता है, या उन्हें बर्बाद किया जा सकता है।
सतत मिश्रण डामर संयंत्रनिरंतर संयंत्रों में उत्पादन चक्र में कोई रुकावट नहीं होती है क्योंकि उत्पादन की लय बैचों में विभाजित नहीं होती है। सामग्री का मिश्रण ड्रायर ड्रम के अंदर होता है जो लम्बा होता है, क्योंकि यह एक ही समय में सूख जाता है और सामग्री को मिला देता है। चूंकि वहां कोई मिक्सिंग टावर या लिफ्ट नहीं हैं, इसलिए सिस्टम को काफी सरल बनाया गया है, जिसके परिणामस्वरूप रखरखाव की लागत में कमी आई है। हालाँकि, स्क्रीन की अनुपस्थिति के कारण उत्पादन चक्र की शुरुआत में, समुच्चय को ड्रायर में डालने से पहले और परिणामस्वरूप डामर के रूप में ड्रायर से निकलने से पहले सटीक नियंत्रण रखना आवश्यक हो जाता है।
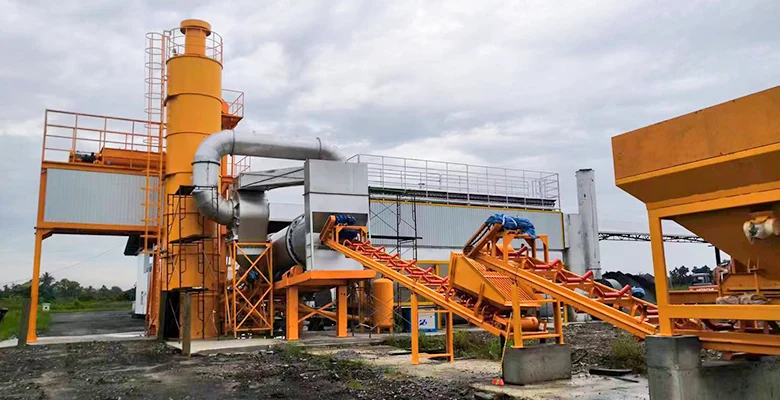
समग्र पैमाइश
बैच डामर मिश्रण संयंत्रों के समान,
निरंतर पौधों का उत्पादन चक्र भी ठंडे फीडरों से शुरू होता है, जहां समुच्चय को आम तौर पर मात्रा के आधार पर मापा जाता है; यदि आवश्यक हो, तो रेत निकालने वाले यंत्र में पैमाइश के लिए वेट-बेल्ट लगाया जा सकता है।
हालाँकि, वर्जिन समुच्चय के कुल वजन का नियंत्रण दो अलग-अलग संयंत्रों में उत्पादन चक्र के दो अलग-अलग चरणों में किया जाता है। निरंतर प्रकार में नम समुच्चय को ड्रायर ड्रम में डालने से पहले एक फीड बेल्ट होता है, जहां पानी के वजन को कम करने की अनुमति देने के लिए नमी की मात्रा मैन्युअल रूप से सेट की जाती है। इसलिए समुच्चय, विशेष रूप से रेत में नमी की मात्रा का एक स्थिर मूल्य होना बेहद जरूरी है, जिसकी लगातार प्रयोगशाला परीक्षणों के माध्यम से निगरानी की जाती है।
बिटुमेन मीटरिंग
निरंतर पौधों में बिटुमेन मीटरिंग आम तौर पर फ़ीड पंप के बगल में एक लीटर-काउंटर के माध्यम से वॉल्यूमेट्रिक होती है। वैकल्पिक रूप से, एक मास काउंटर स्थापित करना संभव है, यदि संशोधित बिटुमेन का उपयोग किया जाता है, तो यह एक आवश्यक विकल्प है, जिसके लिए लगातार सफाई कार्यों की आवश्यकता होती है।
भराव पैमाइश
निरंतर संयंत्रों में मीटरिंग प्रणाली सामान्य रूप से वॉल्यूमेट्रिक होती है, जिसमें वैरिएबल-स्पीड फ़ीड स्क्रू का उपयोग किया जाता है, जिसने पिछले वायवीय मीटरिंग सिस्टम को बदल दिया है।
हमारे सभी निर्यात संयंत्रों में नियंत्रण कक्ष पीएलसी प्रकार का है। यह एक बड़ा मूल्यवर्धन है क्योंकि हम अपनी आवश्यकता के अनुसार पीएलसी को अनुकूलित कर सकते हैं। पीएलसी पैनल से सुसज्जित ड्रम मिक्सर माइक्रोप्रोसेसर पैनल वाले प्लांट की तुलना में एक अलग मशीन है। माइक्रोप्रोसेसर पैनल की तुलना में पीएलसी पैनल रखरखाव मुक्त भी है। हम हमेशा ग्राहकों को सर्वश्रेष्ठ देने में विश्वास करते हैं ताकि वे अपने प्रतिस्पर्धियों से आगे रह सकें। डामर ड्रम प्लांट के सभी निर्माता और निर्यातक पीएलसी पैनल वाले प्लांट की पेशकश नहीं करते हैं।
यह सुनिश्चित करने के लिए सभी संयंत्रों का पूर्व परीक्षण किया जाता है कि जो कुछ भी हमारे कारखाने से निकलता है वह साइट पर कम परेशानी के साथ प्रदर्शन करने के लिए तैयार है।
सिनोरोडर के पास विनिर्माण का 30 से अधिक वर्षों का अनुभव है और यह एक ऐसा उत्पाद है जो पेशेवर सेवा और सस्ते पुर्जों द्वारा समर्थित है ताकि आप आने वाले वर्षों तक अपने उपकरणों को संजोकर रखें और उनका उपयोग करें।