Az adalékanyagok és a bitumen aszfalttá alakítása utak építéséhez termikus keverési folyamatot igényel. Ehhez nélkülözhetetlen az aszfaltkeverő üzem. Az aszfaltkeverő üzem célja az adalékanyag és az aszfalt magas hőmérsékleten történő összekeverése, homogén aszfaltburkolati keverék előállítására. A felhasznált adalékanyag lehet egyetlen anyag, durva és finom adalékanyagok kombinációja, ásványi töltőanyaggal vagy anélkül. Az alkalmazott kötőanyag általában aszfalt, de lehet aszfalt emulzió vagy számos módosított anyag valamelyike. Különféle adalékanyagok, így folyékony és por alakú anyagok is beépíthetők a keverékbe.
Jelenleg három népszerűbb melegaszfaltkeverő üzem létezik: szakaszos keverék, dobkeverék és folyamatos dobkeverő. Mindhárom típus ugyanazt a végső célt szolgálja, és az aszfaltkeveréknek alapvetően hasonlónak kell lennie, függetlenül a gyártásához használt üzem típusától. A három üzemtípus azonban működésében és anyagáramlásában különbözik, amint azt a következő szakaszokban ismertetjük.
Batch Mix Aszfaltgyáraz aszfaltkeverő üzem minden útépítő cég kulcsfontosságú felszerelése. Bármely aszfaltkeverő üzemnek számos funkciója van. Az Asphalt Batch üzemek sorozatban állítják elő a meleg keverék aszfaltot. Ezek a szakaszos keveréküzemek folyamatos folyamatban állítanak elő forró aszfaltkeveréket. Ez a berendezés megváltoztatható és újrahasznosított anyagok felhasználásával meleg keverék aszfalt előállítására is használható. A szakaszos típusú üzemekben vannak olyan változatok, amelyek lehetővé teszik a RAP (regenerált aszfaltburkolat) hozzáadását. A szabványos szakaszos aszfaltkeverő üzem alkotóelemei: hidegtápláló rendszer, aszfalt ellátó rendszer, sóderszárító, keverőtorony és emisszió-szabályozó rendszer. A szakaszos üzem torony egy melegliftből, egy szűrőfedélzetből, forró tartályokból, egy mérőgaratból, egy aszfalt mérővödörből és egy pugmalomból áll. A keverékben felhasznált adalékanyagot eltávolítják a készletekből, és egyedi hidegadagoló edényekbe helyezik. A különböző méretű aggregátumokat az egyes tárolóedények alján lévő kapunyílás méretének és a tartály alatti szállítószalag sebességének kombinációjával osztják ki a tartályaikból. Általában az egyes rekeszek alatt lévő adagolószalag az összes hidegadagoló tartály alatt elhelyezett gyűjtőszalagra helyezi az aggregátumot. Az aggregátumot a gyűjtő szállítószalag szállítja, és egy töltő szállítószalagra továbbítja. A töltőszalagon lévő anyagot ezután felvisszük az adalékanyag-szárítóba.
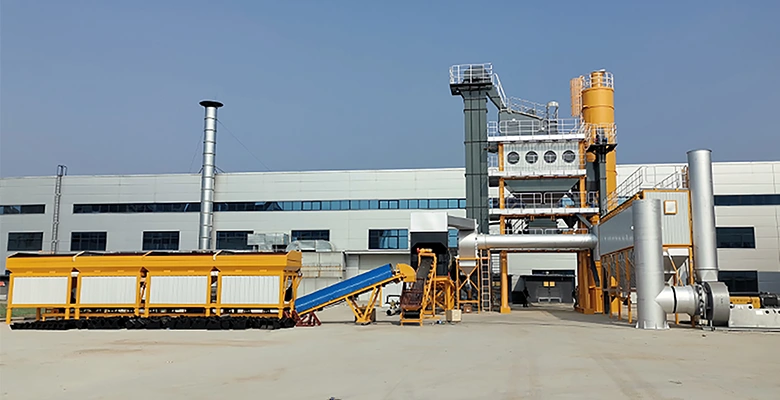
A szárító ellenáramú alapon működik. Az adalékanyagot a felső végén vezetik be a szárítóba, és mind a dob forgása (gravitációs áramlás), mind a forgó szárító belsejében lévő járati konfiguráció révén lefelé mozgatják a dobon. Az égő a szárító alsó végén található, és az égési és szárítási folyamatból származó kipufogógázok a szárító felső vége felé mozognak, az aggregátum áramlásával szemben (ellentétes). Miközben az aggregátum átjut a kipufogógázokon, az anyagot felmelegítik és szárítják. A nedvességet eltávolítják, és a kipufogógáz-áram részeként kivezetik a szárítóból.
A forró, száraz aggregátum ezután kiürül a szárítóból az alsó végén. A forró adalékanyagot általában serleges lifttel szállítják a növénykeverő torony tetejére. A felvonóból való kiürítéskor az aggregátum általában egy rezgő szitakészleten halad át a négy forró tárolótartály egyikébe. A legfinomabb adalékanyag közvetlenül az összes szitán keresztül kerül az 1. számú melegtárolóba; a durvább aggregált részecskéket a
különböző méretű képernyőket, és a másik forró tárolóedénybe helyezzük. Az adalékanyag szétválasztása a forró tartályokba a szitafedélzetben használt szita nyílásainak méretétől és a hidegadagoló tartályokban lévő adalékanyag fokozatosságától függ.
A felmelegített, szárított és átméretezett aggregátumot a forró tartályokban tartják, amíg ki nem ürítik az egyes tartályok alján található ajtókból egy mérőgaratba. Az egyes aggregátumok helyes arányát a tömeg határozza meg.
Az adalékanyag arányosításával és mérlegelésével egyidejűleg az aszfaltot a tárolótartályából egy külön fűtött mérővödörbe szivattyúzzák, amely a tornyon közvetlenül a mopómalom felett található. A megfelelő mennyiségű anyagot bemérik a vödörbe, és ott tartják, amíg ki nem ürítik a pugmalomba. A mérőgaratban lévő adalékanyagot egy ikertengelyes pugmalomba ürítik, és a különböző adalékanyag-frakciókat nagyon rövid ideig – általában 5 másodpercnél rövidebb ideig – összekeverik. E rövid szárazkeverési idő után az aszfalt a mérővödörből kiürül.
a pugmalomba, és kezdődik a nedves keverési idő. Az aszfalt adalékanyaggal való összekeverésének ideje nem lehet több, mint az adalékanyag-szemcsék vékony aszfaltréteggel való teljes bevonásához szükséges idő – általában 25-35 másodperc, ennek a tartománynak az alsó határával. lévén egy jó állapotú pugmalomhoz. A pugmalomban kevert tétel mérete 1,81-5,44 tonna (2-6 tonna) lehet.
A keverés befejeztével a pugmalom alján lévő kapuk kinyílnak, és a keveréket a szállítójárműbe vagy egy szállítóberendezésbe engedik ki, amely a keveréket egy silóba szállítja, ahonnan a teherautókat szakaszosan rakják be. A legtöbb szakaszos üzemben körülbelül 5-7 másodpercre van szükség a pugmill kapuinak kinyitásához és a keverék kiürítéséhez. A teljes keverési idő (száraz keverési idő + nedves keverési idő + keverék kiürítési ideje) körülbelül 40 másodperc is lehet, de jellemzően a teljes keverési idő körülbelül 45 másodperc.
Az üzem kibocsátáscsökkentő eszközökkel van felszerelve, amelyek elsődleges és másodlagos gyűjtőrendszereket is tartalmaznak. Elsődleges kollektorként általában száraz kollektort vagy kiütődobozt használnak. Másodlagos gyűjtőrendszerként nedves mosórendszer, vagy gyakrabban száraz szövetszűrőrendszer (zsákház) használható, hogy eltávolítsa a részecskéket a szárítóból kiáramló kipufogógázokból, és tiszta levegőt küldjön a légkörbe a kéményen keresztül. .
Ha a RAP-ot bekeverik a keverékbe, akkor azt egy külön hidegadagoló edénybe helyezik, ahonnan az üzembe szállítják. A RAP három hely egyikén adható hozzá az új aggregátumhoz: a meleglift alján; a forró kukák; vagy leggyakrabban a mérőgarat. A hőátadás a túlhevített új aggregátum és az újrahasznosított anyag között azonnal megkezdődik, amint a két anyag érintkezik, és a keverési folyamat során folytatódik a pugmalomban.
Drum Mix AszfaltgyárA kötegelt típushoz képest a dobkeverékes aszfaltgyár kisebb hőveszteséggel, kisebb munkateljesítménnyel rendelkezik, nincs túlfolyás, kevesebb por repül és stabil hőmérséklet-szabályozással rendelkezik. A vezérlőrendszer automatikusan beállítja az aszfalt áramlási sebességét az aggregátum áramlási sebességének és az előre beállított aszfalt-aggregátum aránynak megfelelően, hogy biztosítsa a pontos arányos teljesítményt. Az aszfaltdobos keverőüzem azon üzemtípusok, amelyek folyamatos keverőüzemként vannak besorolva, és folyamatos folyamatban állítanak elő forró aszfaltkeveréket.
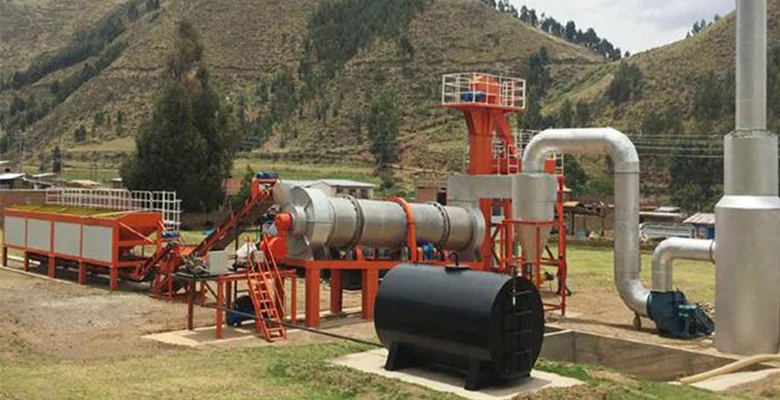
A HMA szakaszos és dobkeverő üzemekben jellemzően hasonlóak a hidegadagoló rendszerek. Mindegyik hidegadagoló tartályból, adagoló szállítószalagból, gyűjtőszállítószalagból és töltő szállítószalagból áll. A legtöbb dobkeverős üzemben és néhány szakaszos üzemben a rendszer bizonyos pontokon beépítik a scalping képernyőt. Ha RAP-ot is betáplálnak az üzembe, hogy újrahasznosított keveréket állítsanak elő, egy további hidegadagoló tartály vagy tartályok, adagolószalag és/vagy gyűjtőszállítószalag, szikrázó szita és töltő szállítószalag szükséges a többletanyag kezeléséhez. A dobkeverő üzemek öt fő összetevőből állnak: a hidegadagoló rendszerből, az aszfalt ellátó rendszerből, a dobkeverőből, a kiegyenlítő- vagy tárolósilókból és a kibocsátáscsökkentő berendezésekből.
A hidegadagoló edényeket az anyag növényhez való arányosítására használják. Mindegyik tartály alatt változtatható sebességű adagolószalag található. Az egyes edényekből kiszívott adalékanyag mennyisége így szabályozható mind a kapunyílás méretével, mind az adagolószalag sebességével, így biztosítva a különböző méretű anyagok pontos szállítását. Az egyes adagolószalagokon lévő adalékanyagot egy gyűjtőszalagra helyezik, amely az összes hidegadagoló tartály alatt fut. A kombinált anyagot rendszerint átengedik egy szikrázó szitán, majd egy töltő szállítószalagra szállítják a dobkeverőhöz.
A töltő szállítószalag két eszközzel van felszerelve, amelyek az üzembe szállított adalékanyag mennyiségének meghatározására szolgálnak: a szállítószalag alatti mérőhíd méri a rajta áthaladó adalékanyag tömegét, és egy érzékelő határozza meg a szalag sebességét. Ezt a két értéket használják a dobkeverőbe belépő adalékanyag nedves tömegének kiszámítására tonnában (tonnában) óránként. Az üzemi számítógép az adalékanyagban lévő nedvességmennyiség bemeneti értékével a nedves tömeget száraz tömeggé alakítja át, hogy meghatározza a keverékben szükséges aszfalt helyes mennyiségét.
A hagyományos dobkeverő párhuzamos áramlású rendszer – a kipufogógázok és az aggregátum ugyanabba az irányba mozog. Az égő a dob felső végén (az aggregát bemeneti végén) található. Az adalékanyag vagy az égő feletti ferde csúszdán keresztül, vagy az égő alatti Slinger szállítószalagon lép be a dobba. Az aggregátumot a gravitáció és a dob belsejében elhelyezkedő járatok konfigurációja kombinációja mozgatja lefelé a dobon. Menet közben az aggregátum felmelegszik, és a nedvességet eltávolítják. A dob hosszának felezőpontja közelében sűrű aggregátumfátyol épül fel, hogy segítse a hőátadási folyamatot.
Ha a RAP-ot hozzáadják az új aggregátumhoz, akkor az a saját hidegadagoló tartályából és gyűjtő/feltöltő szállítószalag rendszeréből kerül le a dob hosszának középpontjához közel található bemenetbe (osztott adagolású rendszer). Ebben a folyamatban a visszanyert anyagot a RAP belépési pontja előtt új aggregátum fátyla védi a magas hőmérsékletű kipufogógázoktól. Ha magas RAP-tartalmú keveréket használnak, valószínűbb, hogy a RAP túlmelegszik a folyamat során. Ennek eredményeként füst távozhat a dobból, vagy károsodhat a RAP.
Az új adalékanyag és az újrahasznosított anyag, ha használják, együtt mozog a dob hátsó részébe. Az aszfaltot egy szivattyú húzza ki a tárolótartályból, és egy mérőn keresztül vezeti át, ahol meghatározzák a megfelelő aszfaltmennyiséget. A kötőanyagot ezután egy csövön keresztül a keverődob hátsó részébe juttatják, ahol az aszfaltot az adalékanyagra fecskendezik. Az aggregátum bevonása akkor következik be, amikor az anyagokat összeforgatják, és a dob kiürítő végéhez mozgatják. Ásványi töltőanyagot vagy zacskószemcséket, vagy mindkettőt szintén a dob hátuljába adják, közvetlenül az aszfalt hozzáadása előtt vagy azzal együtt.
Az aszfaltkeveréket egy szállítóberendezésbe (húzóléc-szállítószalag, hevederes szállítószalag vagy serleges felvonó) rakják le, hogy a tárolósilóba szállítsák. A siló a keverék folyamatos áramlását szakaszos áramlássá alakítja, és a szállítójárműbe üríti.
Általában ugyanazt a típusú kibocsátáscsökkentő berendezést használják a dobkeverő üzemben, mint a szakaszos üzemben. Elsődleges száraz kollektor és nedves mosórendszer vagy zsákházas másodlagos kollektor használható. Ha nedves mosórendszert használnak, az összegyűjtött finomszemcséket nem lehet visszaforgatni a keverékbe, és elpazarolják; zsákház használata esetén az összegyűjtött finomszemcséket részben vagy egészben vissza lehet juttatni a keverődobba, vagy elpazarolni.
Folyamatos keverésű aszfaltgyárA folyamatos üzemekben nincs fennakadás a termelési ciklusban, mivel a termelés ritmusa nincs tételekre bontva. Az anyag keverése a szárítódobban történik, amely megnyúlt, mivel egyszerre szárad és keveri az anyagot. Mivel nincs keverőtorony vagy lift, ezért a rendszer jelentősen leegyszerűsödik, aminek következtében a karbantartási költségek is csökkennek. A szita hiánya azonban szükségessé teszi a pontos ellenőrzést a gyártási ciklus elején, mielőtt az aggregátumokat a szárítóba adagolnák, és mielőtt a szárítóból aszfaltként kiürülnének.
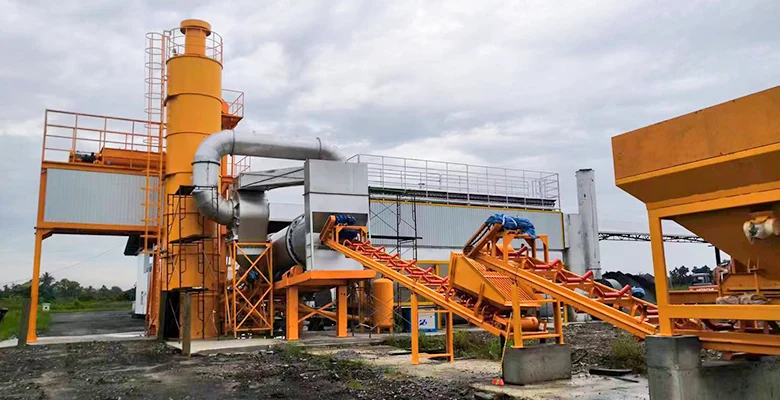
ÖSSZEGMÉRÉS
Hasonlóan a szakaszos aszfaltkeverő üzemekhez,
a folyamatos üzemek termelési ciklusa is a hideg adagolókkal kezdődik, ahol az aggregátumokat általában térfogat szerint mérik; ha szükséges, a homokszívóba mérõszalaggal is felszerelhetõ az adagoláshoz.
A szűz aggregátumok össztömegének szabályozása azonban a termelési ciklus két különböző fázisában történik a két különböző üzemben. A folyamatos típusnál van egy adagolószalag, mielőtt a nedves adalékanyagokat a szárítódobba táplálják, ahol a nedvességtartalom manuálisan beállítható, hogy a víz tömegét le lehessen vonni. Ezért rendkívül fontos, hogy az adalékanyagok, különösen a homok nedvességtartalmának állandó értéke legyen, amelyet gyakori laboratóriumi vizsgálatokkal folyamatosan ellenőriznek.
BITUMMÉRÉS
Folyamatos üzemekben a bitumenadagolás általában térfogati, a betápláló szivattyú utáni literszámlálón keresztül történik. Alternatív megoldásként lehetőség van tömegszámláló beépítésére is, amely szükséges választás módosított bitumen alkalmazása esetén, ami gyakori tisztítási műveleteket igényel.
Töltőanyag adagolás
A folyamatos üzemekben az adagolórendszer általában térfogatmérős, változó fordulatszámú előtolócsavarokkal, amelyek a korábbi pneumatikus adagolórendszert váltották fel.
A vezérlőpanel minden exportüzemünkben PLC típusú. Ez hatalmas értéktöbblet, mert a PLC-t igényeinknek megfelelően testre szabhatjuk. A PLC panellel felszerelt dobkeverő más gép, mint egy mikroprocesszoros panellel ellátott üzem. A PLC panel a mikroprocesszoros panelhez képest karbantartásmentes. Mindig hiszünk abban, hogy a legjobbat adjuk ügyfeleinknek, hogy versenytársaik előtt maradhassanak. Nem minden aszfaltdobgyártó gyártó és exportőr kínál PLC panellel ellátott üzemet.
Az összes üzem előzetes tesztelése megtörténik annak biztosítása érdekében, hogy bármi, ami elhagyja gyárunkat, készen álljon a telephelyen történő kisebb gondok nélküli teljesítésre.
A Sinoroader több mint 30 éves gyártási tapasztalattal és egy olyan termékkel rendelkezik, amelyet professzionális szerviz és olcsóbb alkatrészek támogatnak, így Ön hosszú éveken át ápolja és használja berendezéseit.