Tre tipi di impianti di miscelazione di asfalto caldo attualmente sono più popolari
Trasformare inerti e bitume in asfalto per costruire strade richiede un processo di miscelazione termica. A tal fine è indispensabile un impianto di miscelazione dell'asfalto. Lo scopo di un impianto di miscelazione dell'asfalto è quello di miscelare l'aggregato e l'asfalto insieme ad una temperatura elevata per produrre una miscela omogenea per la pavimentazione dell'asfalto. L'aggregato utilizzato può essere monomateriale, una combinazione di aggregati grossolani e fini, con o senza carica minerale. Il materiale legante usato è normalmente asfalto ma può essere un'emulsione di asfalto o uno di una varietà di materiali modificati. Nella miscela possono anche essere incorporati vari additivi, inclusi materiali liquidi e in polvere.
Esistono attualmente tre tipi più popolari di impianti di miscelazione di asfalto caldo: miscelazione batch, miscelazione a tamburo e miscelazione a tamburo continua. Tutti e tre i tipi hanno lo stesso scopo finale e la miscela di asfalto dovrebbe essere essenzialmente simile indipendentemente dal tipo di impianto utilizzato per produrla. Le tre tipologie di impianto si differenziano però per funzionamento e flusso dei materiali, come descritto nelle sezioni successive.
Batch Mix impianto di asfaltol'impianto di miscelazione dell'asfalto è un'attrezzatura fondamentale per qualsiasi impresa di costruzioni stradali. Qualsiasi funzionamento dell'impianto di miscelazione di asfalto ha molte funzioni. Gli impianti Asphalt Batch producono conglomerato bituminoso a caldo in una serie di lotti. Questi impianti di miscelazione discontinua producono conglomerato bituminoso a caldo in un processo continuo. È anche possibile modificare e utilizzare questa attrezzatura per la produzione di conglomerato bituminoso a caldo utilizzando materiale riciclato. Gli impianti di tipo batch presentano variazioni che consentono l'aggiunta di RAP (pavimentazione in asfalto recuperato). I componenti di un impianto standard di miscelazione di asfalto sono: il sistema di alimentazione a freddo, il sistema di alimentazione dell'asfalto, l'essiccatore di aggregati, la torre di miscelazione e il sistema di controllo delle emissioni. La torre dell'impianto batch è costituita da un elevatore a caldo, un piano di vagliatura, contenitori a caldo, una tramoggia di pesatura, una benna di pesatura dell'asfalto e un mulino a rulli. L'aggregato utilizzato nella miscela viene rimosso dalle scorte e collocato in singoli contenitori di alimentazione a freddo. Aggregati di diverse dimensioni vengono dosati dai loro contenitori in base a una combinazione delle dimensioni dell'apertura del cancello sul fondo di ciascun contenitore e della velocità del nastro trasportatore sotto il contenitore. Generalmente, un nastro di alimentazione sotto ogni silo deposita l'inerte su un trasportatore di raccolta posto sotto tutti i silo di alimentazione a freddo. L'aggregato viene trasportato dal trasportatore di raccolta e trasferito ad un trasportatore di caricamento. Il materiale sul trasportatore di carico viene quindi trasportato fino all'essiccatore inerti.
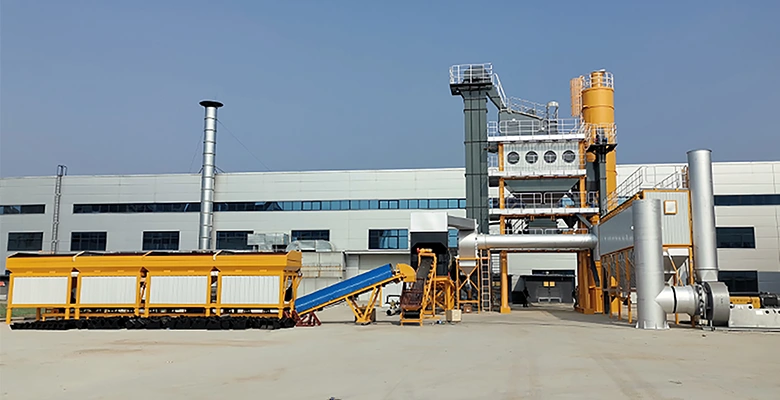
L'essiccatore funziona in controcorrente. L'aggregato viene introdotto nell'essiccatore all'estremità superiore e viene spostato lungo il tamburo sia dalla rotazione del tamburo (flusso di gravità) che dalla configurazione di volo all'interno dell'essiccatore rotante. Il bruciatore si trova all'estremità inferiore dell'essiccatore e i gas di scarico del processo di combustione ed essiccazione si spostano verso l'estremità superiore dell'essiccatore, contro (contro) il flusso dell'aggregato. Quando l'aggregato viene fatto rotolare attraverso i gas di scarico, il materiale viene riscaldato ed essiccato. L'umidità viene rimossa ed espulsa dall'essiccatore come parte del flusso di gas di scarico.
L'aggregato caldo e secco viene quindi scaricato dall'essiccatore all'estremità inferiore. L'aggregato caldo viene solitamente trasportato alla sommità della torre di miscelazione dell'impianto mediante un elevatore a tazze. Dopo lo scarico dall'elevatore, l'aggregato passa normalmente attraverso una serie di vagli vibranti in, tipicamente, uno dei quattro silos di stoccaggio caldo. Il miglior materiale aggregato passa direttamente attraverso tutti gli schermi nel contenitore caldo n. 1; le particelle di aggregato più grossolane sono separate dal
vagli di diverse dimensioni e depositati in uno degli altri contenitori caldi. La separazione dell'aggregato nelle tramogge calde dipende dalla dimensione delle aperture nel vaglio che viene utilizzato nel piano di vagliatura e dalla gradazione dell'aggregato nelle tramogge di alimentazione a freddo.
L'aggregato riscaldato, essiccato e ridimensionato viene trattenuto nelle tramogge calde fino a quando non viene scaricato da un cancello sul fondo di ciascuna tramoggia in una tramoggia di pesatura. La proporzione corretta di ciascun aggregato è determinata dal peso.
Nello stesso momento in cui l'aggregato viene dosato e pesato, l'asfalto viene pompato dal suo serbatoio di stoccaggio a un secchio di pesatura riscaldato separato situato sulla torre appena sopra il mulino a pug. La giusta quantità di materiale viene pesata nel secchio e trattenuta fino a quando non viene svuotata nel pugmill. L'aggregato nella tramoggia di pesatura viene svuotato in un mulino a rulli a doppio albero e le diverse frazioni di aggregato vengono miscelate insieme per un periodo di tempo molto breve, solitamente inferiore a 5 secondi. Dopo questo breve tempo di miscelazione a secco, l'asfalto viene scaricato dalla benna di pesatura.
nel pugmill e inizia il tempo di miscelazione a umido. Il tempo di miscelazione per la miscelazione dell'asfalto con l'aggregato non dovrebbe essere superiore a quello necessario per rivestire completamente le particelle di aggregato con un film sottile del materiale di asfalto, solitamente nell'intervallo da 25 a 35 secondi, con l'estremità inferiore di questo intervallo essendo per un pugmill che è in buone condizioni. La dimensione del lotto miscelato nel pugmill può essere compresa tra 1,81 e 5,44 tonnellate (da 2 a 6 tonnellate).
Terminata la miscelazione, vengono aperte le saracinesche sul fondo del mulino a ricircolo e la miscela viene scaricata nel mezzo di traino o in un dispositivo di trasporto che trasporta la miscela in un silo dal quale i camion verranno caricati in modo discontinuo. Per la maggior parte degli impianti batch, il tempo necessario per aprire i cancelli del mulino a pug e scaricare la miscela è di circa 5-7 secondi. Il tempo totale di miscelazione (tempo di miscelazione a secco + tempo di miscelazione a umido + tempo di scarico della miscela) per un lotto può essere di soli 40 secondi circa, ma in genere il tempo di miscelazione totale è di circa 45 secondi.
L'impianto è dotato di dispositivi di controllo delle emissioni, comprendenti sia sistemi di raccolta primari che secondari. Come collettore primario viene normalmente utilizzato un collettore a secco o un knockout box. Come sistema di raccolta secondario è possibile utilizzare un sistema di abbattimento a umido o, più spesso, un sistema di filtri in tessuto a secco (baghouse) per rimuovere il particolato dai gas di scarico che fuoriescono dall'essiccatore e inviare aria pulita nell'atmosfera attraverso il camino .
Se il RAP è incorporato nella miscela, viene collocato in un contenitore di alimentazione a freddo separato da cui viene consegnato all'impianto. Il RAP può essere aggiunto al nuovo aggregato in una delle tre posizioni: il fondo dell'ascensore caldo; i cassonetti caldi; o, più comunemente, la tramoggia di pesatura. Il trasferimento di calore tra il nuovo aggregato surriscaldato e il materiale di recupero inizia non appena i due materiali entrano in contatto e continua durante il processo di miscelazione nel pugmill.
Impianto di asfalto misto a tamburoRispetto al tipo di lotto, l'impianto di asfalto a tamburo ha una minore perdita termica, una potenza di lavoro inferiore, nessun trabocco, meno polvere che vola e un controllo della temperatura stabile. Il sistema di controllo regola automaticamente la portata dell'asfalto in base alla portata degli aggregati e al rapporto asfalto-aggregati preimpostato, per garantire un'uscita proporzionale precisa. L'impianto di miscelazione di fusti di asfalto è il tipo di impianti classificati come impianti di miscelazione continua, che producono asfalto a miscela calda in un processo continuo.
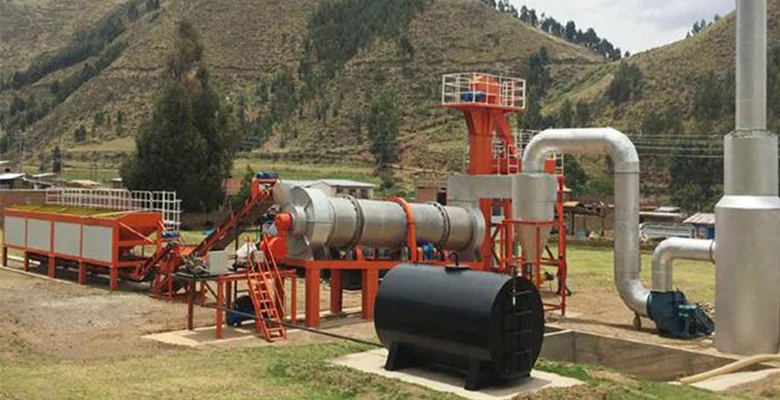
In genere i sistemi di alimentazione a freddo sugli impianti HMA batch e drum-mix sono simili. Ciascuno è costituito da contenitori di alimentazione a freddo, trasportatori di alimentazione, un trasportatore di raccolta e un trasportatore di carico. Nella maggior parte degli impianti di miscelazione in fusti e in alcuni impianti batch, a un certo punto nel sistema è incluso un vaglio di scalpatura. Se anche il RAP viene immesso nell'impianto per produrre una miscela riciclata, sono necessari uno o più bidoni di alimentazione a freddo, un nastro di alimentazione e/o un nastro di raccolta, un vaglio di scalpatura e un nastro di carico aggiuntivi per gestire il materiale in eccesso. Gli impianti di miscelazione a tamburo sono costituiti da cinque componenti principali: il sistema di alimentazione a freddo, il sistema di alimentazione dell'asfalto, il miscelatore a tamburo, i silos di riempimento o di stoccaggio e le apparecchiature per il controllo delle emissioni.
I silos di alimentazione a freddo vengono utilizzati per dosare il materiale all'impianto. Sotto ogni contenitore viene utilizzato un nastro di alimentazione a velocità variabile. La quantità di materiale inerte prelevato da ciascun contenitore può quindi essere controllata sia dalla dimensione dell'apertura del cancello che dalla velocità del nastro alimentatore per fornire un'erogazione precisa dei materiali di diverse dimensioni. L'aggregato su ciascun nastro di alimentazione viene depositato su un trasportatore di raccolta che scorre sotto tutti i silos di alimentazione a freddo. Il materiale combinato viene normalmente fatto passare attraverso un vaglio di scalpatura e quindi trasferito a un trasportatore di caricamento per il trasporto al mescolatore a tamburo.
Il trasportatore di carico è dotato di due dispositivi che servono a determinare la quantità di inerti in arrivo all'impianto: una pesa a ponte posta sotto il nastro trasportatore misura il peso dell'inerte che lo attraversa e un sensore determina la velocità del nastro. Questi due valori vengono utilizzati per calcolare il peso umido dell'aggregato, in tonnellate (tonnellate) all'ora, che entra nel mescolatore a tamburo. Il computer dell'impianto, con la quantità di umidità nell'aggregato fornita come valore di input, converte il peso umido in peso secco per determinare la corretta quantità di asfalto necessaria nella miscela.
Il tradizionale miscelatore a tamburo è un sistema a flusso parallelo: i gas di scarico e l'aggregato si muovono nella stessa direzione. Il bruciatore si trova all'estremità superiore (estremità di ingresso dell'aggregato) del tamburo. L'aggregato entra nel tamburo o da uno scivolo inclinato sopra il bruciatore o su un trasportatore Slinger sotto il bruciatore. L'aggregato viene spostato lungo il tamburo da una combinazione di gravità e la configurazione dei voli situati all'interno del tamburo. Mentre viaggia, l'aggregato viene riscaldato e l'umidità viene rimossa. Un denso velo di aggregato viene formato vicino al punto medio della lunghezza del tamburo per favorire il processo di trasferimento del calore.
Se il RAP viene aggiunto al nuovo inerte, viene depositato dal proprio silo di alimentazione a freddo e dal sistema di nastri trasportatori di raccolta/caricamento in un ingresso situato vicino al centro della lunghezza del tamburo (sistema di alimentazione divisa). In questo processo, il materiale recuperato è protetto dai gas di scarico ad alta temperatura dal velo di nuovo aggregato a monte del punto di ingresso del RAP. Quando vengono utilizzate miscele con un alto contenuto di RAP, è più probabile che il RAP si surriscaldi durante il processo. Ciò potrebbe provocare l'emissione di fumo dal tamburo o danni al RAP.
Il nuovo aggregato e il materiale di recupero, se utilizzato, si spostano insieme nella parte posteriore del tamburo. L'asfalto viene prelevato dal serbatoio di stoccaggio da una pompa e alimentato attraverso un metro, dove viene determinato il volume corretto di asfalto. Il materiale legante viene quindi erogato attraverso un tubo nella parte posteriore del tamburo di miscelazione, dove l'asfalto viene iniettato sull'aggregato. Il rivestimento dell'aggregato avviene quando i materiali vengono fatti rotolare insieme e spostati verso l'estremità di scarico del tamburo. Nella parte posteriore del tamburo vengono aggiunti anche riempitivi minerali o polveri fini a maniche, o entrambi, appena prima o in concomitanza con l'aggiunta dell'asfalto.
Il conglomerato bituminoso viene depositato in un dispositivo di trasporto (un trasportatore a tapparelle, un nastro trasportatore o un elevatore a tazze) per il trasporto a un silo di stoccaggio. Il silo converte il flusso continuo di miscela in un flusso batch per lo scarico nel veicolo di trasporto.
In generale, nell'impianto di miscelazione in fusti viene utilizzato lo stesso tipo di apparecchiatura per il controllo delle emissioni utilizzato nell'impianto batch. È possibile utilizzare un collettore primario a secco e un sistema di abbattimento a umido o un collettore secondario a maniche. Se viene utilizzato un sistema di abbattimento a umido, i fini raccolti non possono essere riciclati nuovamente nella miscela e vengono sprecati; se si utilizza un filtro a maniche, i fini raccolti possono essere restituiti in tutto o in parte al tamburo di miscelazione, oppure possono essere sprecati.
Impianto di miscelazione continua dell'asfaltoNegli impianti continui non c'è interruzione del ciclo produttivo in quanto il ritmo di produzione non è suddiviso in lotti. La miscelazione del materiale avviene all'interno del tamburo essiccatore che è di forma allungata, in quanto contemporaneamente essicca e rimescola il materiale. Non essendoci torri di miscelazione o elevatori, l'impianto risulta quindi notevolmente semplificato, con conseguente abbattimento dei costi di manutenzione. L'assenza del vaglio rende però necessari controlli precisi all'inizio del ciclo produttivo, prima che gli inerti vengano immessi nell'essiccatoio e prima che vengano conseguentemente scaricati dall'essiccatoio come asfalto.
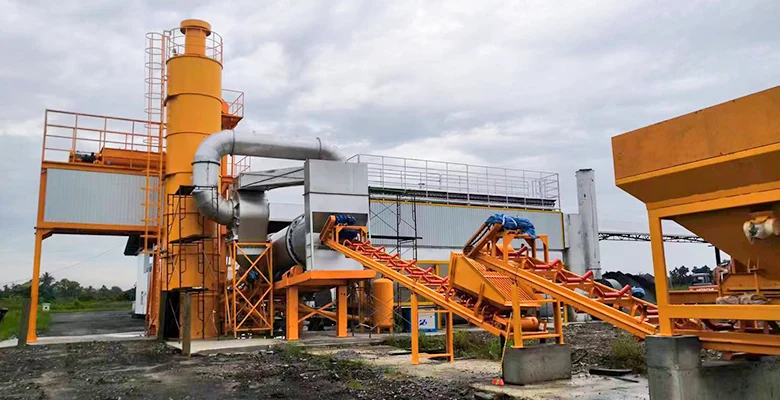
MISURAZIONE AGGREGATA
Simile agli impianti di miscelazione di conglomerati bituminosi,
anche il ciclo produttivo degli impianti continui inizia con gli alimentatori a freddo, dove gli inerti vengono generalmente dosati a volume; se necessario, l'estrattore di sabbia può essere dotato di un nastro pesatore per il dosaggio.
Il controllo del peso totale degli inerti vergini, invece, viene effettuato in due diverse fasi del ciclo produttivo nei due diversi stabilimenti. Nel tipo continuo è presente un nastro di alimentazione, prima che gli inerti umidi vengano immessi nel tamburo essiccatore, dove il contenuto di umidità viene impostato manualmente per consentire la sottrazione del peso dell'acqua. Pertanto è estremamente importante che il contenuto di umidità degli inerti, in particolare della sabbia, abbia un valore costante che viene continuamente monitorato attraverso frequenti test di laboratorio.
DOSAGGIO DEL BITUME
Negli impianti continui il dosaggio del bitume è generalmente volumetrico tramite un contalitri posto a valle della pompa di alimentazione. In alternativa è possibile installare un contamasse, scelta necessaria se si utilizza bitume modificato, che richiede frequenti operazioni di pulizia.
Dosaggio riempitivo
Negli impianti continui il sistema di dosaggio è normalmente volumetrico, utilizzando coclee di alimentazione a velocità variabile che hanno sostituito il precedente sistema di dosaggio pneumatico.
Il pannello di controllo è di tipo PLC in tutti i nostri impianti di esportazione. Questa è un'enorme aggiunta di valore perché possiamo personalizzare il PLC secondo le nostre esigenze. L'impastatrice a tamburo dotata di quadro PLC è una macchina diversa da un impianto con quadro a microprocessore. Il pannello PLC è inoltre esente da manutenzione rispetto al pannello a microprocessore. Crediamo sempre nel dare il meglio ai clienti in modo che possano stare al passo con la concorrenza. Non tutti i produttori ed esportatori di impianti a tamburo per asfalto offrono impianti con pannello PLC.
Il test preliminare di tutti gli impianti viene eseguito per garantire che tutto ciò che esce dalla nostra fabbrica sia pronto per funzionare con meno problemi sul sito.
Sinoroader ha più di 30 anni di esperienza nella produzione e un prodotto supportato da un servizio professionale e ricambi più economici in modo da amare e utilizzare la tua attrezzatura per gli anni a venire.