הפיכת אגרגטים וביטומן לאספלט לבניית כבישים דורשת תהליך ערבוב תרמי. מפעל ערבוב אספלט הוא הכרחי לשם כך. מטרתו של מפעל ערבוב אספלט היא למזג אגרגט ואספלט יחד בטמפרטורה מוגברת כדי לייצר תערובת ריצוף אספלט הומוגנית. האגרגט המשמש יכול להיות חומר בודד, שילוב של אגרגטים גסים ועדינים, עם או בלי חומר מילוי מינרלי. חומר הקלסר המשמש הוא בדרך כלל אספלט, אך עשוי להיות תחליב אספלט או אחד ממגוון חומרים שעברו שינוי. ניתן לשלב בתערובת גם תוספים שונים, לרבות חומרים נוזליים ואבקתיים.
ישנם שלושה סוגים פופולריים נוספים של מפעלי ערבוב אספלט חם כרגע: תערובת אצווה, תערובת תופים ותערובת תופים רציפה. כל שלושת הסוגים משרתים את אותה מטרה סופית, ותערובת האספלט צריכה להיות דומה במהותה ללא קשר לסוג המפעל המשמש לייצורה. עם זאת, שלושת סוגי המפעלים שונים בתפעול ובזרימת החומרים, כפי שמתואר בסעיפים הבאים.
מפעל אספלט מיקס אצווהמפעל ערבוב אספלט הוא ציוד מפתח לכל חברת בניית כבישים. לכל פעולת מפעל תערובת אספלט יש פונקציות רבות. מפעלי אספלט אצווה מייצרים אספלט תערובת חמה בסדרה של קבוצות. מפעלי תערובת אצווה אלו מייצרים אספלט תערובת חמה בתהליך מתמשך. כמו כן, ניתן לשנות ולהשתמש בציוד זה לייצור אספלט תערובת חמה באמצעות חומר ממוחזר. למפעלים מסוג אצווה יש וריאציות בהם המאפשרות הוספת RAP (Reclaimed asphalt relay). המרכיבים של מפעל תערובות אספלט סטנדרטי הם: מערכת הזנה קרה, מערכת אספקת אספלט, מייבש צבירה, מגדל ערבוב ומערכת בקרת פליטה. מגדל מפעלי האצווה מורכב ממעלית חמה, סיפון מסך, פחים חמים, הופר שקילה, דלי שקילה אספלט ומחסנית. האגרגט המשמש בתערובת מוסר ממאגרים ומוכנס לפחי הזנה קרים בודדים. אגרגטים בגדלים שונים עוברים פרופורציות מתוך הפחים שלהם על ידי שילוב של גודל פתח השער בתחתית כל פח ומהירות המסוע מתחת לפח. בדרך כלל, חגורת הזנה מתחת לכל פח מפקידה את האגרגט על מסוע איסוף הממוקם מתחת לכל פחי ההזנה הקרה. האגרגט מועבר על ידי מסוע האיסוף ומועבר למסוע טעינה. לאחר מכן, החומר על מסוע הטעינה נישא עד למייבש הצבירה.
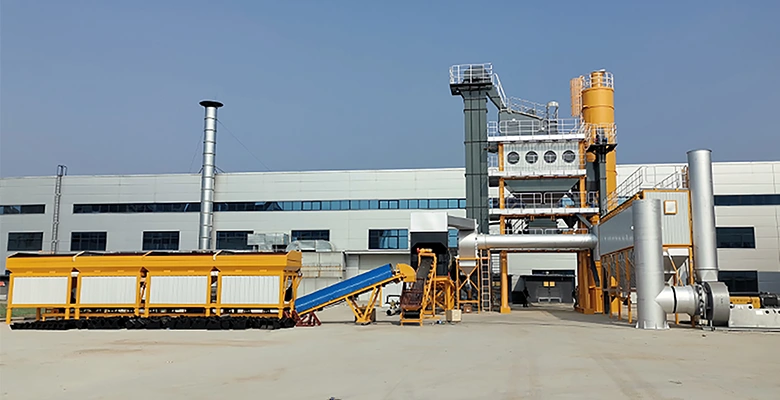
המייבש פועל על בסיס זרימה נגדית. האגרגט מוכנס למייבש בקצה העליון ומוזז במורד התוף הן על ידי סיבוב התוף (זרימת כוח הכבידה) והן על ידי תצורת הטיסה בתוך המייבש המסתובב. המבער ממוקם בקצה התחתון של המייבש, וגזי הפליטה מתהליך הבעירה והייבוש נעים לכיוון הקצה העליון של המייבש, כנגד (נגד) זרימת האגרגט. כשהאגרגט מתגלגל דרך גזי הפליטה, החומר מחומם ומייבש. הלחות מוסרת ומוציאה מהמייבש כחלק מזרם גז הפליטה.
לאחר מכן, האגרגט החם והיבש משוחרר מהמייבש בקצה התחתון. האגרגט החם מועבר בדרך כלל לראש מגדל ערבוב המפעל באמצעות מעלית דלי. עם הפריקה מהמעלית, האגרגט עובר בדרך כלל דרך קבוצה של מסכים רוטטים לתוך, בדרך כלל, אחד מארבעה פחי אחסון חמים. החומר המצטבר הטוב ביותר עובר ישירות דרך כל המסכים לפח החם מספר 1; חלקיקי המצטבר הגסים יותר מופרדים על ידי ה
מסכים בגדלים שונים ומופקדים באחד מהפחים החמים האחרים. הפרדת האגרגט לתוך הפחים החמים תלויה בגודל הפתחים במסך המשמש בסיפון המסך ובהדרגה של האגרגט בפחי ההזנה הקרה.
האגרגט המחומם, המיובש והשינוי בגודלו מוחזק בפחים החמים עד לשחרור משער בתחתית כל פח לתוך קופסת שקילה. היחס הנכון של כל אגרגט נקבע לפי משקל.
במקביל לפרופורציה ושקילה של האגרגט, נשאב האספלט ממיכל האגירה שלו לדלי שקילה מחומם נפרד הממוקם על המגדל ממש מעל הפוגמטח. הכמות הנכונה של החומר נשקללת לתוך הדלי ומוחזקה עד לריקון לתוך הפאגמין. האגרגט במיכל השקילה מרוקן לתוך טחנת פאגט דו-ציר, ושברי האגרגט השונים מעורבבים יחד לפרק זמן קצר מאוד - בדרך כלל פחות מ-5 שניות. לאחר זמן ערבוב יבש קצר זה, האספלט מדלי השקילה נפרק.
לתוך הפאגמין, וזמן הערבוב הרטוב מתחיל. זמן הערבוב לערבוב של האספלט עם האגרגט לא צריך להיות יותר מזה הדרוש לציפוי מלא של חלקיקי האגרגט בסרט דק של חומר האספלט - בדרך כלל בטווח של 25 עד 35 שניות, עם הקצה התחתון של טווח זה. להיות עבור פאגמיל במצב טוב. גודל האצווה המעורבבת ב-pugmill יכול להיות בטווח של 1.81 עד 5.44 טון (2 עד 6 טון).
לאחר השלמת הערבוב, השערים בתחתית הפוגמין נפתחים, והתערובת מוזרקת לרכב ההובלה או למכשיר שינוע המוביל את התערובת לממגורה ממנה יועמסו משאיות בצורה אצווה. עבור רוב מפעלי האצווה, הזמן הדרוש לפתיחת שערי הפאגמיל ופריקת התערובת הוא כ-5 עד 7 שניות. זמן הערבוב הכולל (זמן ערבוב יבש + זמן ערבוב רטוב + זמן פריקת תערובת) עבור אצווה יכול להיות קצר עד כ-40 שניות, אך בדרך כלל, זמן הערבוב הכולל הוא כ-45 שניות.
המפעל מצויד בהתקני בקרת פליטה, הכוללים מערכות איסוף ראשוניות ומשניות כאחד. אספן יבש או קופסת נוקאאוט משמשים בדרך כלל כאספן העיקרי. ניתן להשתמש במערכת קרצוף רטוב או, לעתים קרובות יותר, מערכת סינון בד יבש (תיק) כמערכת האיסוף המשנית כדי להסיר חלקיקים מגזי הפליטה הזורמים מהמייבש ושולחים אוויר נקי לאטמוספירה דרך הערימה. .
אם RAP משולב בתערובת, הוא מונח בפח נפרד להזנה קרה שממנו הוא מועבר למפעל. ניתן להוסיף את ה-RAP למצרף החדש באחד משלושה מיקומים: בחלק התחתון של המעלית החמה; הפחים החמים; או, בדרך כלל, קופסת השקילה. העברת חום בין האגרגט החדש המחומם לחומר המוחזר מתחיל ברגע ששני החומרים באים במגע וממשיך במהלך תהליך הערבוב ב-pugmill.
מפעל אספלט תופים מיקסבהשוואה לסוג אצווה, למפעל אספלט תערובת תופים יש פחות אובדן תרמי, כוח עבודה נמוך יותר, אין הצפת יתר, פחות עוף אבק ובקרת טמפרטורה יציבה. מערכת הבקרה מתאימה אוטומטית את קצב זרימת האספלט בהתאם לקצב זרימת האגרגטים ויחס אספלט-אגרגטים מוגדר מראש, כדי להבטיח תפוקה פרופורציונלית מדויקת. מפעל תערובת תופי אספלט הוא סוגי המפעלים שמסווגים כמפעלי ערבוב רציף, מייצרים אספלט תערובת חמה בתהליך מתמשך.
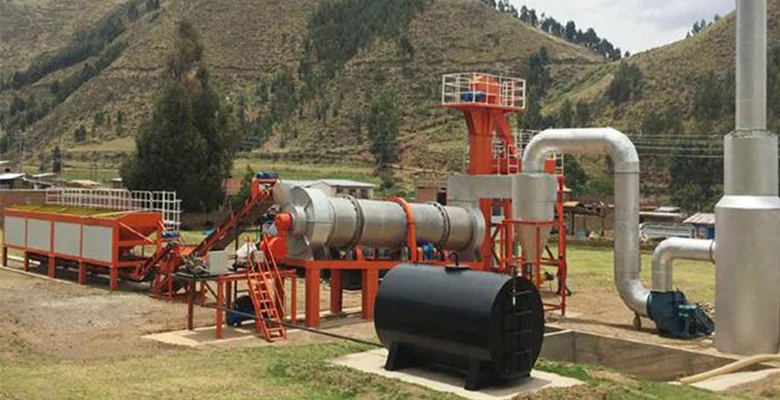
בדרך כלל מערכות ההזנה הקרה במפעלי אצווה ותופים של HMA דומות. כל אחד מורכב ממיכלי הזנה קרים, מסועי הזנה, מסוע איסוף ומסוע טעינה. ברוב מפעלי תערובת תופים ובחלק מצמחי אצווה, כלול במערכת בשלב מסוים מסך קרקפת. אם RAP מוזנת למפעל גם כדי לייצר תערובת ממוחזרת, יש צורך בפח או פחים נוספים להזנה קרה, רצועת הזנה ו/או מסוע איסוף, מסך קרקפת ומסוע טעינה כדי לטפל בחומר הנוסף. מפעלי תערובת תופים מורכבים מחמישה מרכיבים עיקריים: מערכת הזנה קרה, מערכת אספקת אספלט, מערבל תופים, ממגורות נחשול או אחסון, וציוד בקרת פליטה.
פחי ההזנה הקרה משמשים לפרופורציה של החומר לצמח. נעשה שימוש בחגורת הזנה במהירות משתנה מתחת לכל פח. לפיכך ניתן לשלוט בכמות האגרגט הנמשך מכל פח הן על ידי גודל פתח השער והן על ידי מהירות חגורת ההזנה כדי לספק אספקה מדויקת של החומרים בגדלים שונים. האגרגט על כל חגורת הזנה מופקד על מסוע איסוף העובר מתחת לכל פחי ההזנה הקרה. החומר המשולב מועבר בדרך כלל דרך מסך קרקפת ולאחר מכן מועבר למסוע טעינה להובלה למערבל התוף.
מסוע הטעינה מצויד בשני מכשירים המשמשים לקביעת כמות האגרגט המועברת למפעל: גשר שקילה מתחת למסוע מודד את משקל האגרגט העובר מעליו, וחיישן קובע את מהירות הרצועה. שני ערכים אלו משמשים לחישוב המשקל הרטוב של אגרגט, בטונות (טון) לשעה, הנכנס למערבל התוף. מחשב המפעל, עם כמות הלחות בצבר מסופקת כערך קלט, ממיר את המשקל הרטוב למשקל יבש על מנת לקבוע את כמות האספלט הנכונה הדרושה בתערובת.
מערבל התוף הרגיל הוא מערכת זרימה מקבילה - גזי הפליטה והאגרגט נעים באותו כיוון. המבער ממוקם בקצה העליון (קצה הכניסה המצטבר) של התוף. האגרגט נכנס לתוף או ממצנח משופע מעל המבער או על מסוע Slinger מתחת למבער. האגרגט מועבר במורד התוף על ידי שילוב של כוח המשיכה ותצורת הטיסות הממוקמות בתוך התוף. תוך כדי נסיעה, האגרגט מחומם והלחות מוסרת. צעיף צפוף של אגרגט נבנה ליד נקודת האמצע של אורך התוף כדי לסייע בתהליך העברת החום.
אם RAP מתווסף למצרף החדש, הוא מופקד ממיכל ההזנה הקרה ומערכת המסוע הטעינה שלו לכניסה הממוקמת בסמוך למרכז אורך התוף (מערכת הזנה מפוצלת). בתהליך זה, החומר המוחזר מוגן מגזי הפליטה בטמפרטורה גבוהה על ידי מעטה של צבר חדש במעלה הזרם של נקודת הכניסה RAP. כאשר משתמשים בתערובות עם תכולת RAP גבוהה, סביר יותר שה-RAP יתחמם יתר על המידה בתהליך. הדבר עלול לגרום לפליטת עשן מהתוף או לנזק ל-RAP.
החומר המצטבר והמוחזר החדש, אם נעשה בו שימוש, נעים יחד אל החלק האחורי של התוף. האספלט נמשך ממיכל האגירה על ידי משאבה ומוזן דרך מטר, שם נקבע נפח האספלט המתאים. חומר הקלסר מועבר לאחר מכן דרך צינור אל החלק האחורי של תוף הערבוב, שם מוזרק האספלט אל האגרגט. ציפוי האגרגט מתרחש כאשר החומרים מתגלגלים יחד ומועברים לקצה הפריקה של התוף. חומר מילוי מינרלי או קנסות תיקים, או שניהם, מתווספים גם לחלק האחורי של התוף, ממש לפני או בשילוב עם הוספת האספלט.
תערובת האספלט מופקדת לתוך מתקן שינוע (מסוע גרירה, מסוע רצועות או מעלית דלי) להובלה לממגורת אחסון. הממגורה ממירה את הזרימה הרציפה של התערובת לזרימה אצווה להפרשה לרכב ההובלה.
באופן כללי, אותו סוג של ציוד בקרת פליטה משמש במפעל תערובת תופים כמו במפעל האצווה. ניתן להשתמש בקולט יבש ראשי ובמערכת מקרצפת רטובה או בקולט משני של בית תיקים. אם נעשה שימוש במערכת מקרצפת רטובה, לא ניתן למחזר את הקנס שנאסף בחזרה לתערובת והם מתבזבזים; אם נעשה שימוש ב-baghouse, ניתן להחזיר את הקנסות שנאספו במלואם או בחלקם לתוף הערבוב, או שהם יכולים להתבזבז.
מפעל אספלט מיקס מתמשךבמפעלים רציפים אין הפרעה במחזור הייצור שכן קצב הייצור אינו מפורק למנות. ערבוב החומר מתבצע בתוך תוף המייבש המוארך, כשהוא מתייבש ומערבב את החומר בו זמנית. מכיוון שאין מגדל ערבוב או מעליות, לכן המערכת מפושטת במידה ניכרת, וכתוצאה מכך הוזלה בעלות התחזוקה. עם זאת, היעדר המסך מחייב בקרות מדויקות בתחילת מחזור הייצור, לפני הזנת האגרגטים למייבש ולפני שהם נפלטים מהמייבש כאספלט.
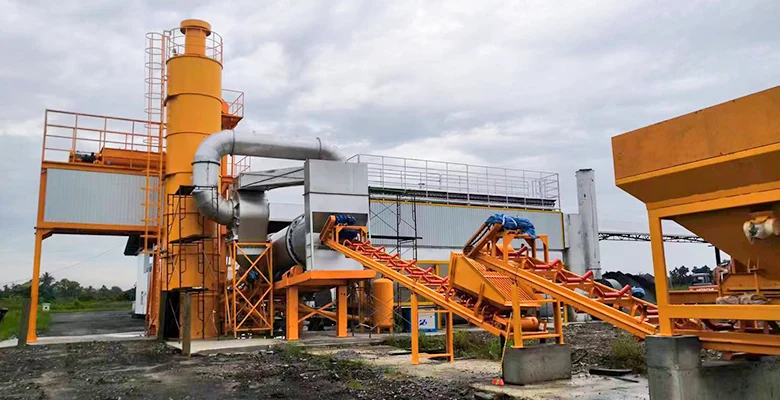
מדידה מצרפית
בדומה למפעלי ערבוב אספלט אצווה,
מחזור הייצור של מפעלים רציפים מתחיל גם עם המזינים הקרים, שבהם האגרגטים נמדדים בדרך כלל לפי נפח; במידת הצורך, לחולץ החול ניתן להרכיב חגורת שקילה למדידה.
השליטה על המשקל הכולל של האגרגטים הבתולים, לעומת זאת, מתבצעת בשני שלבים שונים של מחזור הייצור בשני המפעלים השונים. בסוג הרציף קיימת חגורת הזנה, לפני הזנת האגרגטים הלחים לתוף המייבש, כאשר תכולת הלחות נקבעת באופן ידני על מנת לאפשר הפחתה של משקל המים. לכן חשוב ביותר שתכולת הלחות באגרגטים, במיוחד בחול, תהיה בעלת ערך קבוע המנוטר באופן שוטף באמצעות בדיקות מעבדה תכופות.
מדידת ביטומן
במפעלים רציפים מדידת הביטומן היא בדרך כלל נפחית דרך מונה ליטר לאחר משאבת ההזנה. לחלופין, ניתן להתקין מונה מסה, בחירה הכרחית אם נעשה שימוש ביטומן שונה, המצריך פעולות ניקוי תכופות.
מדידת מילוי
במפעלים רציפים מערכת המדידה היא בדרך כלל נפחית, תוך שימוש בברגי הזנה בעלי מהירות משתנה שהחליפו את מערכת המדידה הפנאומטית הקודמת.
לוח הבקרה הוא מסוג PLC בכל מפעלי הייצוא שלנו. זוהי תוספת ערך עצומה מכיוון שאנו יכולים להתאים אישית PLC לפי הדרישה שלנו. מערבל התופים המצויד בפאנל PLC הוא מכונה שונה ממפעל עם פאנל מיקרו-מעבד. פאנל PLC הוא גם ללא תחזוקה בהשוואה לפאנל המיקרו-מעבד. אנו תמיד מאמינים במתן הטוב ביותר ללקוחות כדי שיוכלו להקדים את המתחרים שלהם. לא כל היצרנים והיצואנים של מפעלי תופי אספלט מציעים מפעל עם פאנל PLC.
בדיקה מוקדמת של כל הצמחים נעשית על מנת להבטיח שכל מה שיוצא מהמפעל שלנו מוכן לביצוע בפחות טרחה באתר.
ל-Sinoroader יש יותר מ-30 שנות ניסיון בייצור ומוצר המגובה בשירות מקצועי וחלפים זולים יותר, כך שתוקיר ותשתמש בציוד שלך במשך שנים רבות.