Во моментов се попопуларни три типа на постројки за мешање на топла асфалт
Претворањето на агрегати и битумен во асфалт за изградба на патишта бара процес на термичко мешање. За ова е неопходна фабрика за мешање асфалт. Целта на фабриката за мешање асфалт е да се спојат агрегатот и асфалтот заедно на покачена температура за да се добие хомогена смеса за асфалтирање. Употребениот агрегат може да биде еден материјал, комбинација од груби и фини агрегати, со или без минерално полнење. Материјалот за врзување што се користи е вообичаено асфалт, но може да биде асфалтна емулзија или еден од различните модифицирани материјали. Во смесата може да се вградат и различни адитиви, вклучувајќи течни и прашкасти материјали.
Во моментов има уште три популарни типови на постројки за мешање на топла асфалт: сериска мешавина, мешавина на барабан и континуирана мешавина на барабан. Сите три типа служат за истата крајна цел, а асфалтната смеса треба да биде суштински слична без оглед на видот на фабриката што се користи за нејзино производство. Сепак, трите типа постројки се разликуваат во работата и протокот на материјалите, како што е опишано во следните делови.
Фабрика за асфалтна мешавина за сериифабриката за мешање асфалт е клучна опрема за секоја компанија за изградба на патишта. Секоја работа на фабриката за мешање на асфалтна серија има многу функции. Асфалт Сериските постројки произведуваат топла мешавина на асфалт во серија од серии. Овие фабрики за сериски мешавини произведуваат асфалт со топла мешавина во континуиран процес. Можно е да се смени и користи оваа опрема за производство на топла мешавина на асфалт со користење на рециклиран материјал. Постројките од типот на серија имаат варијации во нив што овозможуваат додавање на RAP (рекултивиран асфалтен коловоз). Компонентите на стандардната постројка за мешање на серии на асфалт се: систем за ладно напојување, систем за снабдување со асфалт, машина за сушење агрегати, кула за мешање и систем за контрола на емисијата. Кулата на сериските постројки се состои од топол лифт, палуба со екран, канти за топла вода, бункер за вага, кофа за мерење на асфалтот и мопсарка. Агрегатот што се користи во смесата се отстранува од залихите и се става во поединечни канти за ладна храна. Агрегатите со различни големини се пропорционални надвор од нивните канти со комбинација на големината на отворот на капијата на дното на секоја корпа и брзината на подвижната лента под корпата. Општо земено, појасот за полнење под секоја корпа го депонира агрегатот на транспортер за собирање сместен под сите корпи за ладна храна. Агрегатот се транспортира со транспортерот за собирање и се пренесува во транспортер за полнење. Материјалот на транспортерот за полнење потоа се носи до машината за сушење на агрегати.
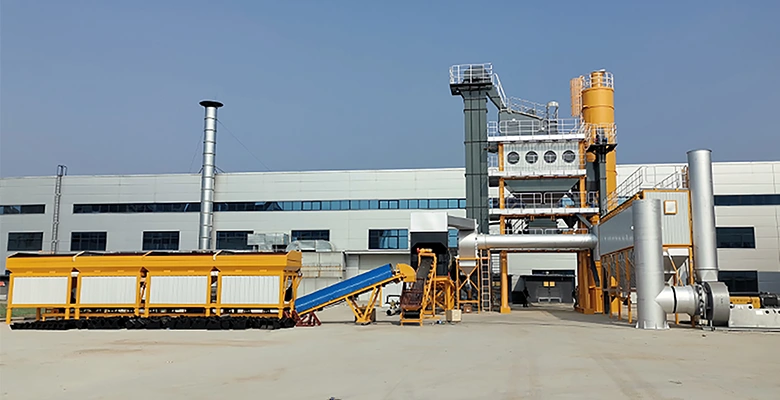
Машината за сушење работи на основа против проток. Агрегатот се внесува во машината за сушење на горниот крај и се поместува надолу по барабанот и со ротација на барабанот (гравитациски тек) и со конфигурацијата на летот во внатрешноста на ротирачката машина за сушење. Пламеникот се наоѓа на долниот крај на машината за сушење, а издувните гасови од процесот на согорување и сушење се движат кон горниот крај на машината за сушење, против (против) протокот на агрегатот. Како што агрегатот се превртува низ издувните гасови, материјалот се загрева и се суши. Влагата се отстранува и се изнесува од машината за сушење како дел од протокот на издувните гасови.
Топлиот, сув агрегат потоа се испушта од машината за сушење на долниот крај. Топлиот агрегат обично се транспортира до врвот на кулата за мешање на растенијата со лифт со кофа. По испуштањето од лифтот, агрегатот вообичаено поминува низ збир на вибрирачки екрани во, обично, една од четирите жешки корпи за складирање. Најдобриот агрегат материјал оди директно низ сите екрани во топла корпа бр. 1; погрубите агрегатни честички се одделени со
екрани со различна големина и се депонираат во една од другите топли канти. Одвојувањето на агрегатот во жешките канти зависи од големината на отворите на екранот што се користи во палубата на екранот и од градацијата на агрегатот во корпите за ладна храна.
Загреаниот, исушениот агрегат и променетата големина се чува во врелите канти додека не се испушти од портата на дното на секоја корпа во бункер за вага. Точниот дел од секој агрегат се одредува според тежината.
Во исто време кога агрегатот се пропорционализира и мери, асфалтот се испумпува од неговиот резервоар за складирање во посебна загреана корпа за мерење сместена на кулата веднаш над багажникот. Соодветното количество материјал се мери во кофата и се чува додека не се испразни во мопсарката. Агрегатот во бункерот за мерење се празнат во машина со две вратило, а различните фракции на агрегатот се мешаат заедно за многу краток временски период - обично помалку од 5 секунди. По ова кратко време на сушење, асфалтот од корпата за мерење се испушта.
во мопскарницата и започнува времето на влажно мешање. Времето на мешање за мешање на асфалтот со агрегатот не треба да биде повеќе од потребното за целосно обложување на честичките од агрегат со тенок филм од асфалтниот материјал - обично во опсег од 25 до 35 секунди, со долниот крај на овој опсег. е за мопсарка која е во добра состојба. Големината на серијата измешана во мопскарницата може да биде во опсег од 1,81 до 5,44 тони (2 до 6 тони).
Кога ќе заврши мешањето, портите на дното на пигмата се отвораат и смесата се испушта во возилото за влечење или во преносен уред што ја носи смесата до силос од кој камионите ќе се товарат на сериски начин. За повеќето сериски постројки, времето потребно за отворање на портите на мопскарницата и испуштање на смесата е приближно 5 до 7 секунди. Вкупното време на мешање (време на суво мешање + време на влажно мешање + време на празнење на мешавината) за една серија може да биде кратко до околу 40 секунди, но обично, вкупното време на мешање е околу 45 секунди.
Постројката е опремена со уреди за контрола на емисиите, кои опфаќаат примарни и секундарни собирни системи. Сув колектор или нокаут кутија обично се користи како примарен колектор. Како систем за секундарно собирање може да се користи или систем за влажно чистење или, почесто, систем за филтрирање за сува ткаенина (багажник) за отстранување на честичките од издувните гасови што течат од машината за сушење и испраќаат чист воздух во атмосферата преку оџакот. .
Ако RAP е вграден во смесата, се става во посебна корпа за ладна храна од која се доставува до фабриката. RAP може да се додаде на новиот агрегат на една од трите локации: дното на топлиот лифт; топли канти; или, најчесто, бункер за вага. Преносот на топлина помеѓу прегреаниот нов агрегат и рекултивираниот материјал започнува веднаш штом двата материјали ќе дојдат во контакт и продолжува за време на процесот на мешање во мопсарката.
Фабрика за асфалт со тапаниВо споредба со типот на серија, постројката за асфалт за мешање барабани има помала термичка загуба, помала работна моќност, нема прелевање, помалку летање прашина и стабилна контрола на температурата. Контролниот систем автоматски ја прилагодува стапката на проток на асфалтот во согласност со брзината на проток на агрегати и однапред поставен сооднос асфалт-агрегати, за да обезбеди прецизен пропорционален излез. Фабриката за мешање на асфалтен тапан е типови на постројки кои се категоризираат како постројки за постојано мешање, кои произведуваат асфалт со топла мешавина во континуиран процес.
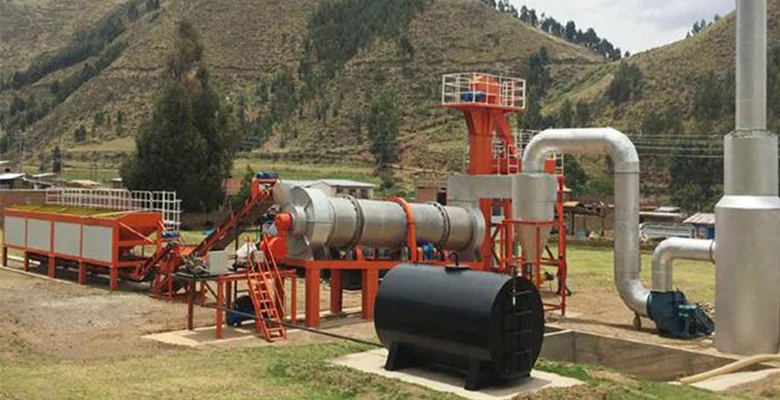
Вообичаено, системите за ладно напојување на постројките за серии и тапан-мешавина HMA се слични. Секој од нив се состои од канти за ладна храна, транспортери за полнење, транспортер за собирање и транспортер за полнење. На повеќето постројки за мешање на тапани и на некои сериски постројки, во одреден момент системот е вклучен екран за гребење. Ако RAP исто така се внесува во фабриката за да се произведе рециклирана смеса, потребна е дополнителна корпа или канти за ладна храна, појас за довод и/или транспортер за собирање, екран за гребење и транспортер за полнење за да се справи со дополнителниот материјал. Фабриките за мешање на барабанот се состојат од пет главни компоненти: систем за ладно напојување, систем за снабдување со асфалт, мешалка за тапани, силоси за пренапони или складирање и опрема за контрола на емисијата.
Корпите за ладна храна се користат за пропорција на материјалот со растението. Под секоја корпа се користи појас за снабдување со променлива брзина. Количината на агрегат извлечен од секоја корпа може да се контролира и од големината на отворот на портата и од брзината на појасот за снабдување за да се обезбеди точна испорака на материјалите со различна големина. Агрегатот на секој доводен појас се депонира на транспортер за собирање што се протега под сите канти за ладна храна. Комбинираниот материјал вообичаено се пренесува низ екран за гребење и потоа се пренесува во транспортер за полнење за транспорт до миксер со барабан.
Транспортерот за полнење е опремен со два уреди кои се користат за одредување на количеството на агрегат што се доставува до постројката: тежинскиот мост под транспортната лента ја мери тежината на агрегатот што минува над него, а сензорот ја одредува брзината на лентата. Овие две вредности се користат за пресметување на влажната тежина на агрегат, во тони (тони) на час, што влегува во миксер на барабанот. Компјутерот на фабриката, со количината на влага во агрегатот обезбедена како влезна вредност, ја претвора влажната тежина во сува тежина со цел да се одреди точната количина на асфалт потребна во мешавината.
Конвенционалниот миксер со барабан е систем со паралелен проток - издувните гасови и агрегатот се движат во иста насока. Пламеникот се наоѓа на горниот крај (крајот на влезот на агрегат) на барабанот. Агрегатот влегува во барабанот или од наклонет канал над горилникот или на транспортер Slinger под пламеникот. Агрегатот се движи надолу по барабанот со комбинација на гравитацијата и конфигурацијата на летовите лоцирани во внатрешноста на барабанот. Како што патува, агрегатот се загрева и се отстранува влагата. Во близина на средината на должината на барабанот е изграден густ превез од агрегат за да помогне во процесот на пренос на топлина.
Ако RAP се додаде на новиот агрегат, тој се депонира од сопствената корпа за ладно напојување и собирање/ транспортер систем за полнење во влез кој се наоѓа во близина на центарот на должината на барабанот (систем со сплит-хранење). Во овој процес, рекултивираниот материјал е заштитен од високотемпературните издувни гасови со превезот на новиот агрегат горе од влезната точка на RAP. Кога се користат мешавини со висока содржина на RAP, поверојатно е дека RAP ќе се прегрее во процесот. Ова може да резултира со испуштање чад од барабанот или оштетување на RAP.
Новиот агрегат и рекултивираниот материјал, доколку се користат, се движат заедно во задниот дел од барабанот. Асфалтот се извлекува од резервоарот за складирање со пумпа и се внесува преку метар, каде што се одредува правилниот волумен на асфалтот. Материјалот за врзување потоа се доставува преку цевка во задниот дел на барабанот за мешање, каде што асфалтот се вбризгува на агрегатот. Обложувањето на агрегатот се случува кога материјалите се превртуваат заедно и се преместуваат до крајот на празнење на барабанот. Во задниот дел на барабанот се додаваат минерални филер или фини за торбичка, или и двете, или веднаш пред или заедно со додавањето на асфалтот.
Асфалтната смеса се депонира во преносен уред (транспортна лента за влечење, транспортер со лента или лифт со кофа) за транспорт до силос за складирање. Силосот го претвора континуираниот проток на смесата во сериски проток за испуштање во возилото за влечење.
Општо земено, истиот тип на опрема за контрола на емисиите се користи во постројката за мешање барабан како и во постројката за серии. Може да се користи примарен сув колектор и систем за влажно чистење или секундарен колектор за торбичка. Ако се користи влажен систем за чистење, собраните фини не можат да се рециклираат назад во смесата и се трошат; ако се користи торбичка, собраните казни може целосно или делумно да се вратат во барабанот за мешање или да се потрошат.
Погон за асфалт за континуирано мешањеВо континуираните постројки нема прекин во производниот циклус бидејќи ритамот на производство не се дели во серии. Мешањето на материјалот се одвива во внатрешноста на барабанот за сушење кој е издолжен, бидејќи истовремено се суши и меша. Бидејќи нема кула за мешање или лифтови, системот е значително поедноставен, со последователно намалување на трошоците за одржување. Отсуството на екранот сепак го прави неопходно да се има прецизни контроли на почетокот на производниот циклус, пред агрегатите да се внесат во машината за сушење и пред тие последователно да се испуштат од машината за сушење како асфалт.
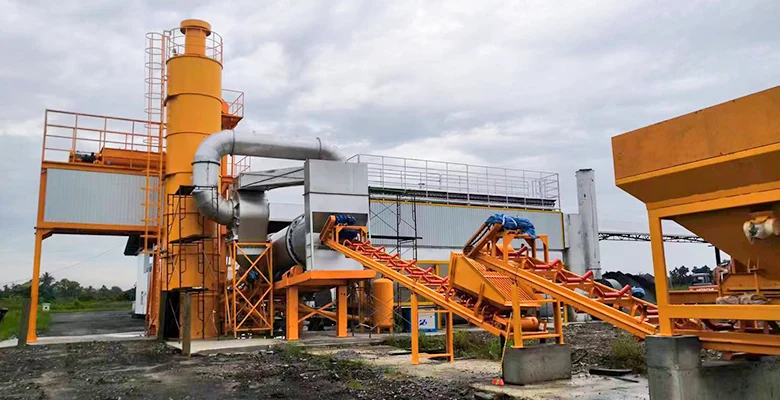
АГРЕГАТНО МЕРЕЊЕ
Слично на сериските погони за мешање асфалт,
циклусот на производство на континуирани постројки, исто така, започнува со ладни колибри, каде што агрегатите генерално се мерат по волумен; доколку е потребно, вагачот на песок може да биде опремен со ремен за мерење.
Контролата на вкупната тежина на девствените агрегати, сепак, се врши во две различни фази од производниот циклус во двете различни погони. Во континуираниот тип има појас за напојување, пред влажните агрегати да се внесат во барабанот за сушење, каде што содржината на влага се поставува рачно за да се овозможи одземање на тежината на водата. Затоа е исклучително важно содржината на влага во агрегатите, особено песокот, да има константна вредност која постојано се следи преку чести лабораториски испитувања.
БИТУМЕНСКО МЕРЕЊЕ
Во постојаните постројки, мерењето на битуменот е генерално волуметриско преку литарски бројач последователна пумпа за напојување. Алтернативно, можно е да се инсталира бројач за маса, неопходен избор доколку се користи модифициран битумен, што бара чести операции за чистење.
Мерење на полнење
Во непрекинатите постројки, системот за мерење е вообичаено волуметриски, со помош на завртки за напојување со променлива брзина кои го замениле претходниот пневматски систем за мерење.
Контролната табла е PLC тип во сите наши извозни постројки. Ова е огромен додаток на вредност затоа што можеме да го прилагодиме PLC според нашите барања. Мешачот на барабанот што е опремен со PLC панел е различна машина од постројка со микропроцесорска плоча. PLC панелот исто така е без одржување во споредба со панелот на микропроцесорот. Ние секогаш веруваме да им го дадеме најдоброто на клиентите за да можат да останат пред нивната конкуренција. Не сите производители и извозници на постројки за тапани за асфалт нудат постројка со PLC панел.
Пред-тестирањето на сите постројки е направено за да се осигура дека сè што ја напушта нашата фабрика е подготвено да се изврши со помала мака на локацијата.
Sinoroader има повеќе од 30 години искуство во производството и производ кој е поддржан од професионална услуга и поевтини резервни делови за да ја негувате и користите вашата опрема во годините што доаѓаат.