മൂന്ന് തരം ഹോട്ട് അസ്ഫാൽറ്റ് മിക്സിംഗ് പ്ലാന്റുകൾ നിലവിൽ കൂടുതൽ ജനപ്രിയമാണ്
റോഡുകൾ നിർമ്മിക്കുന്നതിന് അഗ്രഗേറ്റുകളും ബിറ്റുമിനും അസ്ഫാൽറ്റാക്കി മാറ്റുന്നതിന് ഒരു തെർമൽ മിക്സിംഗ് പ്രക്രിയ ആവശ്യമാണ്. ഒരു അസ്ഫാൽറ്റ് മിക്സിംഗ് പ്ലാന്റ് ഇതിന് ഒഴിച്ചുകൂടാനാവാത്തതാണ്. ഒരു അസ്ഫാൽറ്റ് മിക്സിംഗ് പ്ലാന്റിന്റെ ഉദ്ദേശം ഒരു ഏകീകൃത അസ്ഫാൽറ്റ് പേവിംഗ് മിശ്രിതം ഉൽപ്പാദിപ്പിക്കുന്നതിന് ഉയർന്ന ഊഷ്മാവിൽ മൊത്തവും അസ്ഫാൽറ്റും കൂടിച്ചേർന്നതാണ്. മിനറൽ ഫില്ലറിനൊപ്പമോ അല്ലാതെയോ മൊത്തത്തിൽ ഉപയോഗിച്ചിരിക്കുന്ന മൊത്തത്തിലുള്ളത്, പരുക്കൻ, സൂക്ഷ്മമായ അഗ്രഗേറ്റുകളുടെ സംയോജനമാണ്. ഉപയോഗിക്കുന്ന ബൈൻഡർ മെറ്റീരിയൽ സാധാരണയായി അസ്ഫാൽറ്റ് ആണ്, പക്ഷേ ഒരു അസ്ഫാൽറ്റ് എമൽഷനോ അല്ലെങ്കിൽ പലതരം പരിഷ്കരിച്ച വസ്തുക്കളിൽ ഒന്നോ ആകാം. ദ്രാവകവും പൊടിച്ചതുമായ വസ്തുക്കൾ ഉൾപ്പെടെ വിവിധ അഡിറ്റീവുകളും മിശ്രിതത്തിൽ ഉൾപ്പെടുത്താം.
നിലവിൽ മൂന്ന് ജനപ്രിയ ഹോട്ട് അസ്ഫാൽറ്റ് മിക്സിംഗ് പ്ലാന്റുകൾ ഉണ്ട്: ബാച്ച് മിക്സ്, ഡ്രം മിക്സ്, തുടർച്ചയായ ഡ്രം മിക്സ്. മൂന്ന് തരങ്ങളും ഒരേ ആത്യന്തിക ഉദ്ദേശ്യം നിറവേറ്റുന്നു, കൂടാതെ അസ്ഫാൽറ്റ് മിശ്രിതം നിർമ്മിക്കാൻ ഉപയോഗിക്കുന്ന ചെടിയുടെ തരം പരിഗണിക്കാതെ തന്നെ സാമ്യമുള്ളതായിരിക്കണം. മൂന്ന് തരം സസ്യങ്ങൾ വ്യത്യസ്തമാണ്, എന്നിരുന്നാലും, ഇനിപ്പറയുന്ന വിഭാഗങ്ങളിൽ വിവരിച്ചിരിക്കുന്നതുപോലെ, വസ്തുക്കളുടെ പ്രവർത്തനത്തിലും ഒഴുക്കിലും.
ബാച്ച് മിക്സ് അസ്ഫാൽറ്റ് പ്ലാന്റ്ഏതൊരു റോഡ് നിർമ്മാണ കമ്പനിയുടെയും പ്രധാന ഉപകരണമാണ് അസ്ഫാൽറ്റ് മിക്സിംഗ് പ്ലാന്റ്. ഏതെങ്കിലും അസ്ഫാൽറ്റ് ബാച്ച് മിക്സ് പ്ലാന്റ് പ്രവർത്തനത്തിന് നിരവധി പ്രവർത്തനങ്ങൾ ഉണ്ട്. അസ്ഫാൽറ്റ് ബാച്ച് സസ്യങ്ങൾ ഒരു കൂട്ടം ബാച്ചുകളിൽ ഹോട്ട് മിക്സ് അസ്ഫാൽറ്റ് ഉത്പാദിപ്പിക്കുന്നു. ഈ ബാച്ച് മിക്സ് പ്ലാന്റുകൾ തുടർച്ചയായ പ്രക്രിയയിൽ ഹോട്ട് മിക്സ് അസ്ഫാൽറ്റ് ഉത്പാദിപ്പിക്കുന്നു. റീസൈക്കിൾ ചെയ്ത മെറ്റീരിയൽ ഉപയോഗിച്ച് ഹോട്ട് മിക്സ് അസ്ഫാൽറ്റ് ഉൽപ്പാദിപ്പിക്കുന്നതിന് ഈ ഉപകരണം മാറ്റാനും ഉപയോഗിക്കാനും സാധ്യമാണ്. ബാച്ച് ഇനം ചെടികൾക്ക് RAP (വീണ്ടെടുത്ത അസ്ഫാൽറ്റ് നടപ്പാത) ചേർക്കാൻ അനുവദിക്കുന്ന വ്യതിയാനങ്ങൾ ഉണ്ട്. ഒരു സ്റ്റാൻഡേർഡ് അസ്ഫാൽറ്റ് ബാച്ച് മിക്സ് പ്ലാന്റിന്റെ ഘടകങ്ങൾ ഇവയാണ്: കോൾഡ് ഫീഡ് സിസ്റ്റം, അസ്ഫാൽറ്റ് സപ്ലൈ സിസ്റ്റം, അഗ്രഗേറ്റ് ഡ്രയർ, മിക്സിംഗ് ടവർ, എമിഷൻ കൺട്രോൾ സിസ്റ്റം. ബാച്ച് പ്ലാന്റ് ടവറിൽ ഒരു ഹോട്ട് എലിവേറ്റർ, ഒരു സ്ക്രീൻ ഡെക്ക്, ഹോട്ട് ബിന്നുകൾ, ഒരു വെയ്റ്റ് ഹോപ്പർ, ഒരു അസ്ഫാൽറ്റ് വെയ്റ്റ് ബക്കറ്റ്, ഒരു പഗ്മിൽ എന്നിവ അടങ്ങിയിരിക്കുന്നു. മിക്സിൽ ഉപയോഗിക്കുന്ന അഗ്രഗേറ്റ് സ്റ്റോക്ക്പൈലുകളിൽ നിന്ന് നീക്കം ചെയ്യുകയും വ്യക്തിഗത കോൾഡ് ഫീഡ് ബിന്നുകളിൽ സ്ഥാപിക്കുകയും ചെയ്യുന്നു. ഓരോ ബിന്നിന്റെയും താഴെയുള്ള ഗേറ്റിന്റെ ഓപ്പണിംഗിന്റെ വലിപ്പവും ബിന്നിനു കീഴിലുള്ള കൺവെയർ ബെൽറ്റിന്റെ വേഗതയും സംയോജിപ്പിച്ച് വ്യത്യസ്ത വലുപ്പത്തിലുള്ള അഗ്രഗേറ്റുകൾ അവയുടെ ബിന്നുകളിൽ നിന്ന് ആനുപാതികമാണ്. സാധാരണയായി, ഓരോ ബിന്നിനും താഴെയുള്ള ഒരു ഫീഡർ ബെൽറ്റ് എല്ലാ കോൾഡ് ഫീഡ് ബിന്നുകളുടെയും കീഴിലുള്ള ഒരു ശേഖരണ കൺവെയറിൽ മൊത്തം നിക്ഷേപിക്കുന്നു. അഗ്രഗേറ്റ് ശേഖരിക്കുന്ന കൺവെയർ വഴി കൊണ്ടുപോകുകയും ചാർജിംഗ് കൺവെയറിലേക്ക് മാറ്റുകയും ചെയ്യുന്നു. ചാർജിംഗ് കൺവെയറിലെ മെറ്റീരിയൽ പിന്നീട് അഗ്രഗേറ്റ് ഡ്രയറിലേക്ക് കൊണ്ടുപോകുന്നു.
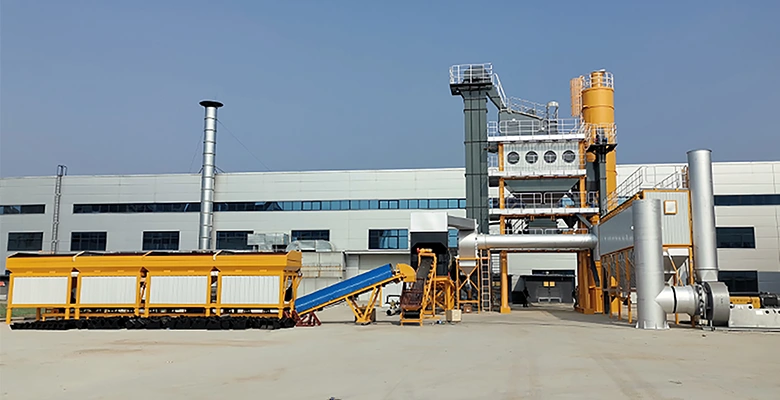
ഡ്രയർ ഒരു കൌണ്ടർ ഫ്ലോ അടിസ്ഥാനത്തിലാണ് പ്രവർത്തിക്കുന്നത്. മുകളിലെ അറ്റത്തുള്ള ഡ്രയറിലേക്ക് അഗ്രഗേറ്റ് അവതരിപ്പിക്കുകയും ഡ്രം റൊട്ടേഷൻ (ഗ്രാവിറ്റി ഫ്ലോ), കറങ്ങുന്ന ഡ്രയറിനുള്ളിലെ ഫ്ലൈറ്റ് കോൺഫിഗറേഷൻ എന്നിവ ഉപയോഗിച്ച് ഡ്രമ്മിന്റെ താഴേക്ക് നീക്കുകയും ചെയ്യുന്നു. ഡ്രയറിന്റെ താഴത്തെ അറ്റത്താണ് ബർണർ സ്ഥിതിചെയ്യുന്നത്, ജ്വലന പ്രക്രിയയിൽ നിന്നും ഉണക്കൽ പ്രക്രിയയിൽ നിന്നുമുള്ള എക്സ്ഹോസ്റ്റ് വാതകങ്ങൾ ഡ്രയറിന്റെ മുകൾ ഭാഗത്തേക്ക് നീങ്ങുന്നു, മൊത്തം ഒഴുക്കിനെതിരെ (എതിർക്കുന്നു). എക്സ്ഹോസ്റ്റ് വാതകങ്ങളിലൂടെ അഗ്രഗേറ്റ് വീഴുമ്പോൾ, മെറ്റീരിയൽ ചൂടാക്കി ഉണക്കുന്നു. എക്സ്ഹോസ്റ്റ് ഗ്യാസ് സ്ട്രീമിന്റെ ഭാഗമായി ഡ്രയറിൽ നിന്ന് ഈർപ്പം നീക്കം ചെയ്യുകയും പുറത്തുവിടുകയും ചെയ്യുന്നു.
ചൂടുള്ളതും ഉണങ്ങിയതുമായ അഗ്രഗേറ്റ് താഴത്തെ അറ്റത്തുള്ള ഡ്രയറിൽ നിന്ന് ഡിസ്ചാർജ് ചെയ്യുന്നു. ചൂടുള്ള അഗ്രഗേറ്റ് സാധാരണയായി ഒരു ബക്കറ്റ് എലിവേറ്റർ വഴി പ്ലാന്റ് മിക്സിംഗ് ടവറിന്റെ മുകളിലേക്ക് കൊണ്ടുപോകുന്നു. എലിവേറ്ററിൽ നിന്ന് ഡിസ്ചാർജ് ചെയ്യുമ്പോൾ, മൊത്തം ഒരു കൂട്ടം വൈബ്രേറ്റിംഗ് സ്ക്രീനുകളിലൂടെ സാധാരണയായി നാല് ഹോട്ട് സ്റ്റോറേജ് ബിന്നുകളിൽ ഒന്നിലേക്ക് കടന്നുപോകുന്നു. ഏറ്റവും മികച്ച മൊത്തത്തിലുള്ള മെറ്റീരിയൽ എല്ലാ സ്ക്രീനുകളിലൂടെയും നമ്പർ 1 ഹോട്ട് ബിന്നിലേക്ക് നേരിട്ട് പോകുന്നു; പരുക്കൻ മൊത്തം കണങ്ങളെ വേർതിരിക്കുന്നു
വ്യത്യസ്ത വലിപ്പത്തിലുള്ള സ്ക്രീനുകളും മറ്റ് ഹോട്ട് ബിന്നുകളിൽ ഒന്നിലേക്ക് നിക്ഷേപിക്കുന്നു. ഹോട്ട് ബിന്നുകളിലേക്ക് അഗ്രഗേറ്റിനെ വേർതിരിക്കുന്നത് സ്ക്രീനിലെ ഡെക്കിൽ ഉപയോഗിക്കുന്ന സ്ക്രീനിലെ ഓപ്പണിംഗുകളുടെ വലുപ്പത്തെയും കോൾഡ് ഫീഡ് ബിന്നുകളിലെ മൊത്തത്തിന്റെ ഗ്രേഡേഷനെയും ആശ്രയിച്ചിരിക്കുന്നു.
ചൂടാക്കിയതും ഉണക്കിയതും വലുപ്പം മാറ്റിയതുമായ അഗ്രഗേറ്റ് ഓരോ ബിന്നിന്റെയും താഴെയുള്ള ഒരു ഗേറ്റിൽ നിന്ന് ഒരു വെയ്റ്റ് ഹോപ്പറിലേക്ക് ഡിസ്ചാർജ് ചെയ്യുന്നതുവരെ ചൂടുള്ള ബിന്നുകളിൽ സൂക്ഷിക്കുന്നു. ഓരോ അഗ്രഗേറ്റിന്റെയും ശരിയായ അനുപാതം ഭാരം അനുസരിച്ചാണ് നിർണ്ണയിക്കുന്നത്.
അഗ്രഗേറ്റിന് ആനുപാതികവും തൂക്കവും നൽകുന്ന അതേ സമയം, അസ്ഫാൽറ്റ് അതിന്റെ സംഭരണ ടാങ്കിൽ നിന്ന് പഗ്മില്ലിന് തൊട്ടുമുകളിലുള്ള ടവറിൽ സ്ഥിതി ചെയ്യുന്ന ഒരു പ്രത്യേക ചൂടായ വെയ്റ്റ് ബക്കറ്റിലേക്ക് പമ്പ് ചെയ്യപ്പെടുന്നു. ശരിയായ അളവിലുള്ള മെറ്റീരിയൽ ബക്കറ്റിലേക്ക് തൂക്കി പഗ്മില്ലിലേക്ക് ഒഴിക്കുന്നതുവരെ പിടിക്കുന്നു. വെയ്റ്റ് ഹോപ്പറിലെ അഗ്രഗേറ്റ് ഒരു ഇരട്ട-ഷാഫ്റ്റ് പഗ്മില്ലിലേക്ക് ശൂന്യമാക്കപ്പെടുന്നു, കൂടാതെ വ്യത്യസ്ത അഗ്രഗേറ്റ് ഭിന്നസംഖ്യകൾ വളരെ കുറഞ്ഞ സമയത്തേക്ക്-സാധാരണയായി 5 സെക്കൻഡിൽ താഴെ മാത്രം. ഈ ഹ്രസ്വ ഡ്രൈ-മിക്സ് സമയത്തിന് ശേഷം, വെയ്റ്റ് ബക്കറ്റിൽ നിന്നുള്ള അസ്ഫാൽറ്റ് ഡിസ്ചാർജ് ചെയ്യപ്പെടും.
പഗ്മില്ലിലേക്ക്, വെറ്റ്-മിക്സ് സമയം ആരംഭിക്കുന്നു. അസ്ഫാൽറ്റിനെ അഗ്രഗേറ്റുമായി മിശ്രണം ചെയ്യുന്നതിനുള്ള സമയം, അസ്ഫാൽറ്റ് മെറ്റീരിയലിന്റെ നേർത്ത ഫിലിം ഉപയോഗിച്ച് മൊത്തത്തിലുള്ള കണങ്ങളെ പൂർണ്ണമായും പൂശാൻ ആവശ്യമായതിനേക്കാൾ കൂടുതലാകരുത്-സാധാരണയായി 25 മുതൽ 35 സെക്കൻഡ് വരെയാണ്, ഈ ശ്രേണിയുടെ താഴത്തെ അറ്റത്ത്. നല്ല നിലയിലുള്ള ഒരു പഗ്മില്ലിന് വേണ്ടിയാണ്. പഗ്മില്ലിൽ കലർത്തിയ ബാച്ചിന്റെ വലിപ്പം 1.81 മുതൽ 5.44 ടൺ വരെ (2 മുതൽ 6 ടൺ വരെ) വരാം.
മിക്സിംഗ് പൂർത്തിയാകുമ്പോൾ, പഗ്മില്ലിന്റെ അടിയിലുള്ള ഗേറ്റുകൾ തുറന്ന്, മിക്സ് ഹാൾ വാഹനത്തിലേക്കോ ട്രക്കുകൾ ബാച്ച് രീതിയിൽ ലോഡുചെയ്യുന്ന ഒരു സൈലോയിലേക്ക് മിക്സ് കൊണ്ടുപോകുന്ന ഒരു കൺവെയിംഗ് ഉപകരണത്തിലേക്കോ ഡിസ്ചാർജ് ചെയ്യുന്നു. മിക്ക ബാച്ച് ചെടികൾക്കും, പഗ്മിൽ ഗേറ്റുകൾ തുറന്ന് മിശ്രിതം ഡിസ്ചാർജ് ചെയ്യാനുള്ള സമയം ഏകദേശം 5 മുതൽ 7 സെക്കൻഡ് വരെയാണ്. ഒരു ബാച്ചിന്റെ ആകെ മിക്സിംഗ് സമയം (ഡ്രൈ-മിക്സ് സമയം + വെറ്റ്-മിക്സ് സമയം + മിക്സ് ഡിസ്ചാർജ് സമയം) ഏകദേശം 40 സെക്കൻഡ് വരെ കുറവായിരിക്കും, എന്നാൽ സാധാരണയായി, മൊത്തം മിക്സിംഗ് സമയം ഏകദേശം 45 സെക്കൻഡാണ്.
പ്രാഥമിക, ദ്വിതീയ ശേഖരണ സംവിധാനങ്ങൾ ഉൾക്കൊള്ളുന്ന എമിഷൻ-നിയന്ത്രണ ഉപകരണങ്ങൾ പ്ലാന്റിൽ സജ്ജീകരിച്ചിരിക്കുന്നു. ഒരു ഡ്രൈ കളക്ടർ അല്ലെങ്കിൽ നോക്കൗട്ട് ബോക്സ് സാധാരണയായി പ്രാഥമിക കളക്ടറായി ഉപയോഗിക്കുന്നു. ഒന്നുകിൽ നനഞ്ഞ സ്ക്രബ്ബർ സംവിധാനം അല്ലെങ്കിൽ, മിക്കപ്പോഴും, ഡ്രൈ ഫാബ്രിക് ഫിൽട്ടർ സിസ്റ്റം (ബാഗ്ഹൗസ്) ഡ്രയറിൽ നിന്ന് പുറത്തേക്ക് ഒഴുകുന്ന എക്സ്ഹോസ്റ്റ് വാതകങ്ങളിൽ നിന്ന് കണികകൾ നീക്കം ചെയ്യുന്നതിനും സ്റ്റാക്കിലൂടെ അന്തരീക്ഷത്തിലേക്ക് ശുദ്ധവായു അയയ്ക്കുന്നതിനുമുള്ള ദ്വിതീയ ശേഖരണ സംവിധാനമായി ഉപയോഗിക്കാം. .
RAP മിശ്രിതത്തിൽ ഉൾപ്പെടുത്തിയാൽ, അത് ഒരു പ്രത്യേക കോൾഡ് ഫീഡ് ബിന്നിൽ സ്ഥാപിക്കുന്നു, അതിൽ നിന്ന് അത് പ്ലാന്റിലേക്ക് എത്തിക്കുന്നു. RAP മൂന്ന് സ്ഥലങ്ങളിൽ ഒന്നിൽ പുതിയ അഗ്രഗേറ്റിലേക്ക് ചേർക്കാവുന്നതാണ്: ചൂടുള്ള എലിവേറ്ററിന്റെ അടിഭാഗം; ചൂടുള്ള ബിന്നുകൾ; അല്ലെങ്കിൽ, ഏറ്റവും സാധാരണയായി, വെയ്റ്റ് ഹോപ്പർ. സൂപ്പർഹീറ്റഡ് പുതിയ അഗ്രഗേറ്റും വീണ്ടെടുക്കപ്പെട്ട മെറ്റീരിയലും തമ്മിലുള്ള താപ കൈമാറ്റം രണ്ട് മെറ്റീരിയലുകളും സമ്പർക്കം പുലർത്തുന്ന ഉടൻ ആരംഭിക്കുകയും പഗ്മില്ലിലെ മിക്സിംഗ് പ്രക്രിയയിൽ തുടരുകയും ചെയ്യുന്നു.
ഡ്രം മിക്സ് അസ്ഫാൽറ്റ് പ്ലാന്റ്ബാച്ച് തരവുമായി താരതമ്യപ്പെടുത്തുമ്പോൾ, ഡ്രം മിക്സ് അസ്ഫാൽറ്റ് പ്ലാന്റിന് കുറഞ്ഞ താപ നഷ്ടം, കുറഞ്ഞ പ്രവർത്തന ശക്തി, ഓവർഫ്ലോ ഇല്ല, കുറഞ്ഞ പൊടി പറക്കൽ, സ്ഥിരമായ താപനില നിയന്ത്രണം എന്നിവയുണ്ട്. കൃത്യമായ ആനുപാതികമായ ഔട്ട്പുട്ട് ഉറപ്പാക്കാൻ, അഗ്രഗേറ്റ് ഫ്ലോ റേറ്റ്, പ്രീ-സെറ്റ് അസ്ഫാൽറ്റ്-അഗ്രഗേറ്റ്സ് അനുപാതം എന്നിവ അനുസരിച്ച് കൺട്രോൾ സിസ്റ്റം സ്വയമേവ അസ്ഫാൽറ്റ് ഫ്ലോ റേറ്റ് ക്രമീകരിക്കുന്നു. അസ്ഫാൽറ്റ് ഡ്രം മിക്സ് പ്ലാന്റ് എന്നത് തുടർച്ചയായ മിക്സിംഗ് പ്ലാന്റുകളായി തരംതിരിച്ചിരിക്കുന്നതും തുടർച്ചയായ പ്രക്രിയയിൽ ഹോട്ട് മിക്സ് അസ്ഫാൽറ്റ് ഉത്പാദിപ്പിക്കുന്നതുമായ സസ്യങ്ങളാണ്.
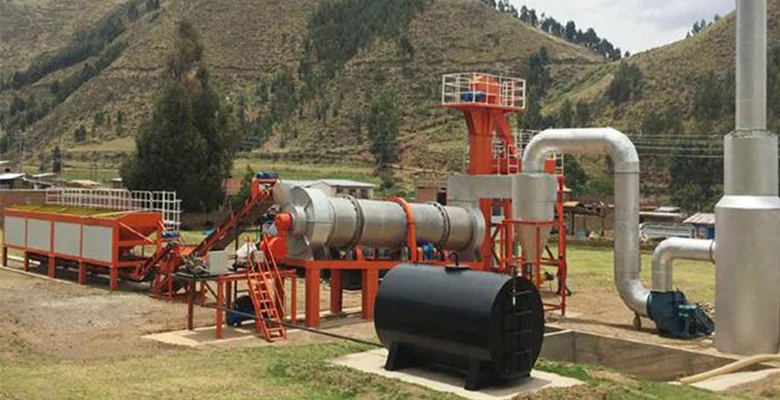
സാധാരണയായി HMA ബാച്ചിലെയും ഡ്രം-മിക്സ് പ്ലാന്റുകളിലെയും കോൾഡ് ഫീഡ് സംവിധാനങ്ങൾ സമാനമാണ്. ഓരോന്നിലും കോൾഡ് ഫീഡ് ബിന്നുകൾ, ഫീഡർ കൺവെയറുകൾ, ഒരു ശേഖരണ കൺവെയർ, ചാർജിംഗ് കൺവെയർ എന്നിവ അടങ്ങിയിരിക്കുന്നു. മിക്ക ഡ്രം-മിക്സ് പ്ലാന്റുകളിലും ചില ബാച്ച് പ്ലാന്റുകളിലും, ചില ഘട്ടങ്ങളിൽ ഒരു സ്കാൽപ്പിംഗ് സ്ക്രീൻ സിസ്റ്റത്തിൽ ഉൾപ്പെടുത്തിയിട്ടുണ്ട്. റീസൈക്കിൾ ചെയ്ത മിശ്രിതം ഉൽപ്പാദിപ്പിക്കാൻ പ്ലാന്റിലേക്ക് RAP നൽകുകയാണെങ്കിൽ, അധിക മെറ്റീരിയൽ കൈകാര്യം ചെയ്യാൻ ഒരു അധിക കോൾഡ് ഫീഡ് ബിൻ അല്ലെങ്കിൽ ബിന്നുകൾ, ഫീഡർ ബെൽറ്റ് കൂടാതെ/അല്ലെങ്കിൽ ശേഖരണ കൺവെയർ, സ്കാൽപ്പിംഗ് സ്ക്രീൻ, ചാർജിംഗ് കൺവെയർ എന്നിവ ആവശ്യമാണ്. ഡ്രം-മിക്സ് പ്ലാന്റുകളിൽ അഞ്ച് പ്രധാന ഘടകങ്ങൾ അടങ്ങിയിരിക്കുന്നു: കോൾഡ് ഫീഡ് സിസ്റ്റം, അസ്ഫാൽറ്റ് വിതരണ സംവിധാനം, ഡ്രം മിക്സർ, സർജ് അല്ലെങ്കിൽ സ്റ്റോറേജ് സിലോസ്, എമിഷൻ കൺട്രോൾ ഉപകരണങ്ങൾ.
ശീതീകരണ-ഫീഡ് ബിന്നുകൾ സസ്യത്തിന് ആനുപാതികമായി മെറ്റീരിയൽ ഉപയോഗിക്കുന്നു. ഓരോ ബിന്നിനു കീഴിലും ഒരു വേരിയബിൾ-സ്പീഡ് ഫീഡർ ബെൽറ്റ് ഉപയോഗിക്കുന്നു. ഓരോ ബിന്നിൽ നിന്നും വലിച്ചെടുക്കുന്ന മൊത്തം തുക ഗേറ്റ് തുറക്കുന്നതിന്റെ വലിപ്പവും ഫീഡർ ബെൽറ്റിന്റെ വേഗതയും ഉപയോഗിച്ച് വ്യത്യസ്ത വലിപ്പത്തിലുള്ള മെറ്റീരിയലുകളുടെ കൃത്യമായ ഡെലിവറി നൽകുന്നതിന് നിയന്ത്രിക്കാനാകും. ഓരോ ഫീഡർ ബെൽറ്റിലുമുള്ള അഗ്രഗേറ്റ് എല്ലാ കോൾഡ് ഫീഡ് ബിന്നുകൾക്കടിയിലും പ്രവർത്തിക്കുന്ന ഒരു ശേഖരണ കൺവെയറിൽ നിക്ഷേപിക്കുന്നു. സംയോജിത മെറ്റീരിയൽ സാധാരണയായി ഒരു സ്കാൽപ്പിംഗ് സ്ക്രീനിലൂടെ കടന്നുപോകുകയും പിന്നീട് ഡ്രം മിക്സറിലേക്ക് കൊണ്ടുപോകുന്നതിനായി ചാർജിംഗ് കൺവെയറിലേക്ക് മാറ്റുകയും ചെയ്യുന്നു.
ചാർജിംഗ് കൺവെയറിൽ രണ്ട് ഉപകരണങ്ങൾ സജ്ജീകരിച്ചിരിക്കുന്നു, അത് പ്ലാന്റിലേക്ക് വിതരണം ചെയ്യുന്ന മൊത്തം അളവിന്റെ അളവ് നിർണ്ണയിക്കാൻ ഉപയോഗിക്കുന്നു: കൺവെയർ ബെൽറ്റിന് കീഴിലുള്ള ഒരു വെയ്റ്റ് ബ്രിഡ്ജ് അതിന് മുകളിലൂടെ കടന്നുപോകുന്ന മൊത്തത്തിന്റെ ഭാരം അളക്കുന്നു, കൂടാതെ ഒരു സെൻസർ ബെൽറ്റിന്റെ വേഗത നിർണ്ണയിക്കുന്നു. ഡ്രം മിക്സറിലേക്ക് പ്രവേശിക്കുന്ന മണിക്കൂറിൽ ടൺ (ടൺ) എന്ന കണക്കിൽ മൊത്തം നനഞ്ഞ ഭാരം കണക്കാക്കാൻ ഈ രണ്ട് മൂല്യങ്ങളും ഉപയോഗിക്കുന്നു. പ്ലാന്റ് കമ്പ്യൂട്ടർ, ഒരു ഇൻപുട്ട് മൂല്യമായി നൽകിയ മൊത്തത്തിലുള്ള ഈർപ്പത്തിന്റെ അളവ്, മിശ്രിതത്തിൽ ആവശ്യമായ അസ്ഫാൽറ്റിന്റെ ശരിയായ അളവ് നിർണ്ണയിക്കാൻ, ആർദ്ര ഭാരത്തെ ഉണങ്ങിയ ഭാരമാക്കി മാറ്റുന്നു.
പരമ്പരാഗത ഡ്രം മിക്സർ ഒരു സമാന്തര-പ്രവാഹ സംവിധാനമാണ് - എക്സ്ഹോസ്റ്റ് വാതകങ്ങളും മൊത്തം ചലിക്കുന്നതും ഒരേ ദിശയിലാണ്. ഡ്രമ്മിന്റെ മുകളിലെ അറ്റത്ത് (അഗ്രഗേറ്റ് ഇൻലെറ്റ് എൻഡ്) ബർണർ സ്ഥിതിചെയ്യുന്നു. ബർണറിന് മുകളിലുള്ള ചരിഞ്ഞ ചട്ടിയിൽ നിന്നോ ബർണറിന് കീഴിലുള്ള സ്ലിംഗർ കൺവെയറിൽ നിന്നോ മൊത്തം ഡ്രമ്മിലേക്ക് പ്രവേശിക്കുന്നു. ഡ്രമ്മിനുള്ളിൽ സ്ഥിതി ചെയ്യുന്ന ഫ്ലൈറ്റുകളുടെ ഗുരുത്വാകർഷണത്തിന്റെയും കോൺഫിഗറേഷന്റെയും സംയോജനത്തിലൂടെ മൊത്തം ഡ്രമ്മിലേക്ക് നീങ്ങുന്നു. ഇത് സഞ്ചരിക്കുമ്പോൾ, മൊത്തം ചൂടാക്കുകയും ഈർപ്പം നീക്കം ചെയ്യുകയും ചെയ്യുന്നു. താപ-കൈമാറ്റ പ്രക്രിയയെ സഹായിക്കുന്നതിന് ഡ്രം നീളത്തിന്റെ മധ്യഭാഗത്തിന് സമീപം ഒരു സാന്ദ്രമായ മൂടുപടം നിർമ്മിച്ചിരിക്കുന്നു.
പുതിയ അഗ്രഗേറ്റിലേക്ക് RAP ചേർത്താൽ, അത് സ്വന്തം കോൾഡ് ഫീഡ് ബിന്നിൽ നിന്നും ശേഖരിക്കുന്നു/ചാർജിംഗ് കൺവെയർ സിസ്റ്റത്തിൽ നിന്നും ഡ്രം ദൈർഘ്യത്തിന്റെ (സ്പ്ലിറ്റ്-ഫീഡ് സിസ്റ്റം) മധ്യഭാഗത്തായി സ്ഥിതിചെയ്യുന്ന ഒരു ഇൻലെറ്റിലേക്ക് നിക്ഷേപിക്കും. ഈ പ്രക്രിയയിൽ, വീണ്ടെടുക്കപ്പെട്ട മെറ്റീരിയൽ RAP എൻട്രി പോയിന്റിന്റെ അപ്സ്ട്രീമിലെ പുതിയ സംഗ്രഹത്തിന്റെ മൂടുപടം വഴി ഉയർന്ന-താപനില എക്സ്ഹോസ്റ്റ് വാതകങ്ങളിൽ നിന്ന് സംരക്ഷിക്കപ്പെടുന്നു. ഉയർന്ന RAP ഉള്ളടക്കമുള്ള മിക്സുകൾ ഉപയോഗിക്കുമ്പോൾ, ഈ പ്രക്രിയയിൽ RAP അമിതമായി ചൂടാകാനുള്ള സാധ്യത കൂടുതലാണ്. ഇത് ഡ്രമ്മിൽ നിന്ന് പുക പുറപ്പെടുവിക്കുന്നതിനോ RAP-ന് കേടുപാടുകൾ വരുത്തുന്നതിനോ കാരണമായേക്കാം.
പുതിയ മൊത്തത്തിലുള്ളതും വീണ്ടെടുക്കപ്പെട്ടതുമായ മെറ്റീരിയൽ, ഉപയോഗിക്കുകയാണെങ്കിൽ, ഡ്രമ്മിന്റെ പിൻഭാഗത്തേക്ക് ഒരുമിച്ച് നീങ്ങുന്നു. സ്റ്റോറേജ് ടാങ്കിൽ നിന്ന് ഒരു പമ്പ് ഉപയോഗിച്ച് അസ്ഫാൽറ്റ് വലിച്ചെടുക്കുകയും ഒരു മീറ്ററിലൂടെ നൽകുകയും ചെയ്യുന്നു, അവിടെ അസ്ഫാൽറ്റിന്റെ ശരിയായ അളവ് നിർണ്ണയിക്കപ്പെടുന്നു. ബൈൻഡർ മെറ്റീരിയൽ ഒരു പൈപ്പിലൂടെ മിക്സിംഗ് ഡ്രമ്മിന്റെ പിൻഭാഗത്തേക്ക് എത്തിക്കുന്നു, അവിടെ അസ്ഫാൽറ്റ് മൊത്തത്തിൽ കുത്തിവയ്ക്കുന്നു. സാമഗ്രികൾ ഒന്നിച്ചുചേർന്ന് ഡ്രമ്മിന്റെ ഡിസ്ചാർജ് അറ്റത്തേക്ക് നീങ്ങുമ്പോൾ മൊത്തം പൂശുന്നു. മിനറൽ ഫില്ലർ അല്ലെങ്കിൽ ബാഗ്ഹൗസ് ഫൈനുകൾ അല്ലെങ്കിൽ രണ്ടും കൂടി ഡ്രമ്മിന്റെ പിൻഭാഗത്ത് ചേർക്കുന്നു, ഒന്നുകിൽ അസ്ഫാൽറ്റ് ചേർക്കുന്നതിന് തൊട്ടുമുമ്പ് അല്ലെങ്കിൽ അതിനോട് ചേർന്ന്.
അസ്ഫാൽറ്റ് മിശ്രിതം ഒരു സംഭരണ സൈലോയിലേക്ക് കൊണ്ടുപോകുന്നതിനായി ഒരു കൈമാറ്റ ഉപകരണത്തിലേക്ക് (ഡ്രാഗ് സ്ലാറ്റ് കൺവെയർ, ബെൽറ്റ് കൺവെയർ അല്ലെങ്കിൽ ബക്കറ്റ് എലിവേറ്റർ) നിക്ഷേപിക്കുന്നു. സിലോ മിക്സിന്റെ തുടർച്ചയായ പ്രവാഹത്തെ ഹാൾ വാഹനത്തിലേക്ക് ഡിസ്ചാർജ് ചെയ്യുന്നതിനുള്ള ഒരു ബാച്ച് ഫ്ലോ ആക്കി മാറ്റുന്നു.
പൊതുവേ, ബാച്ച് പ്ലാന്റിൽ ഉപയോഗിക്കുന്ന അതേ തരം എമിഷൻ-കൺട്രോൾ ഉപകരണങ്ങളാണ് ഡ്രം-മിക്സ് പ്ലാന്റിലും ഉപയോഗിക്കുന്നത്. ഒരു പ്രൈമറി ഡ്രൈ കളക്ടറും വെറ്റ് സ്ക്രബ്ബർ സിസ്റ്റവും അല്ലെങ്കിൽ ഒരു ബാഗ്ഹൗസ് സെക്കൻഡറി കളക്ടറും ഉപയോഗിക്കാം. ഒരു നനഞ്ഞ സ്ക്രബ്ബർ സംവിധാനം ഉപയോഗിക്കുകയാണെങ്കിൽ, ശേഖരിച്ച പിഴകൾ വീണ്ടും മിശ്രിതത്തിലേക്ക് റീസൈക്കിൾ ചെയ്യാൻ കഴിയില്ല, അത് പാഴായിപ്പോകും; ഒരു ബാഗ്ഹൗസ് ഉപയോഗിക്കുകയാണെങ്കിൽ, ശേഖരിച്ച പിഴകൾ മുഴുവനായോ ഭാഗികമായോ മിക്സിംഗ് ഡ്രമ്മിലേക്ക് തിരികെ നൽകാം, അല്ലെങ്കിൽ അവ പാഴായിപ്പോകാം.
തുടർച്ചയായ മിക്സ് അസ്ഫാൽറ്റ് പ്ലാന്റ്തുടർച്ചയായ പ്ലാന്റുകളിൽ ഉൽപ്പാദനത്തിന്റെ താളം ബാച്ചുകളായി തകരാത്തതിനാൽ ഉൽപ്പാദന ചക്രത്തിൽ തടസ്സമില്ല. പദാർത്ഥത്തിന്റെ മിശ്രിതം നീളമുള്ള ഡ്രയർ ഡ്രമ്മിനുള്ളിൽ നടക്കുന്നു, കാരണം അത് ഒരേ സമയം ഉണങ്ങുകയും മിശ്രിതമാക്കുകയും ചെയ്യുന്നു. മിക്സിംഗ് ടവറോ എലിവേറ്ററുകളോ ഇല്ലാത്തതിനാൽ, അറ്റകുറ്റപ്പണിയുടെ ചെലവ് കുറയുന്നതിനൊപ്പം സിസ്റ്റം ഗണ്യമായി ലളിതമാക്കിയിരിക്കുന്നു. സ്ക്രീനിന്റെ അഭാവം, ഉൽപ്പാദന ചക്രത്തിന്റെ തുടക്കത്തിൽ, അഗ്രഗേറ്റുകൾ ഡ്രയറിലേക്ക് നൽകുന്നതിനുമുമ്പ്, ഡ്രയറിൽ നിന്ന് അസ്ഫാൽറ്റായി ഡിസ്ചാർജ് ചെയ്യുന്നതിനുമുമ്പ് കൃത്യമായ നിയന്ത്രണങ്ങൾ ഉണ്ടായിരിക്കേണ്ടത് ആവശ്യമാണ്.
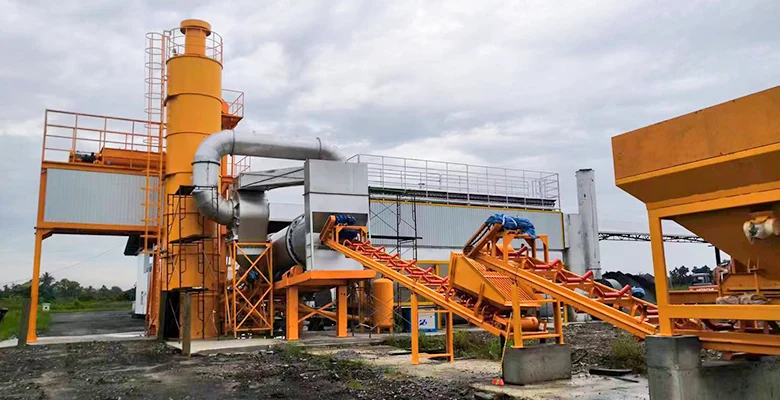
മൊത്തം മീറ്ററിംഗ്
ബാച്ച് അസ്ഫാൽറ്റ് മിക്സിംഗ് പ്ലാന്റുകൾക്ക് സമാനമാണ്,
തുടർച്ചയായ സസ്യങ്ങളുടെ ഉൽപ്പാദന ചക്രം ആരംഭിക്കുന്നത് തണുത്ത ഫീഡറുകളിൽ നിന്നാണ്, അവിടെ അഗ്രഗേറ്റുകൾ സാധാരണയായി അളവനുസരിച്ച് അളക്കുന്നു; ആവശ്യമെങ്കിൽ, മണൽ എക്സ്ട്രാക്റ്ററിൽ മീറ്ററിംഗിനായി ഒരു വെയ്റ്റ്-ബെൽറ്റ് ഘടിപ്പിക്കാം.
എന്നിരുന്നാലും, കന്യക അഗ്രഗേറ്റുകളുടെ ആകെ ഭാരത്തിന്റെ നിയന്ത്രണം രണ്ട് വ്യത്യസ്ത പ്ലാന്റുകളിൽ ഉൽപ്പാദന ചക്രത്തിന്റെ രണ്ട് വ്യത്യസ്ത ഘട്ടങ്ങളിൽ നടപ്പിലാക്കുന്നു. തുടർച്ചയായ തരത്തിൽ, നനഞ്ഞ അഗ്രഗേറ്റുകൾ ഡ്രയർ ഡ്രമ്മിലേക്ക് നൽകുന്നതിനുമുമ്പ് ഒരു ഫീഡ് ബെൽറ്റ് ഉണ്ട്, അവിടെ ജലത്തിന്റെ ഭാരം കുറയ്ക്കാൻ അനുവദിക്കുന്നതിന് ഈർപ്പത്തിന്റെ അളവ് സ്വമേധയാ സജ്ജീകരിച്ചിരിക്കുന്നു. അതിനാൽ, അഗ്രഗേറ്റുകളിലെ ഈർപ്പത്തിന്റെ അളവ്, പ്രത്യേകിച്ച് മണൽ, നിരന്തരമായ ലബോറട്ടറി പരിശോധനകളിലൂടെ നിരന്തരം നിരീക്ഷിക്കപ്പെടുന്ന സ്ഥിരമായ മൂല്യം ഉണ്ടായിരിക്കേണ്ടത് വളരെ പ്രധാനമാണ്.
ബിറ്റുമെൻ മീറ്ററിംഗ്
തുടർച്ചയായ സസ്യങ്ങളിൽ, ഫീഡ് പമ്പിന് ശേഷമുള്ള ഒരു ലിറ്റർ കൗണ്ടറിലൂടെ ബിറ്റുമെൻ മീറ്ററിംഗ് സാധാരണയായി വോള്യൂമെട്രിക് ആണ്. പകരമായി, ഒരു മാസ് കൌണ്ടർ ഇൻസ്റ്റാൾ ചെയ്യാൻ സാധിക്കും, പരിഷ്കരിച്ച ബിറ്റുമെൻ ഉപയോഗിക്കുകയാണെങ്കിൽ ആവശ്യമായ തിരഞ്ഞെടുപ്പ്, ഇതിന് പതിവായി വൃത്തിയാക്കൽ പ്രവർത്തനങ്ങൾ ആവശ്യമാണ്.
ഫില്ലർ മീറ്ററിംഗ്
തുടർച്ചയായ പ്ലാന്റുകളിൽ, മുമ്പത്തെ ന്യൂമാറ്റിക് മീറ്ററിംഗ് സിസ്റ്റത്തിന് പകരമായി വേരിയബിൾ-സ്പീഡ് ഫീഡ് സ്ക്രൂകൾ ഉപയോഗിച്ച് മീറ്ററിംഗ് സിസ്റ്റം സാധാരണയായി വോള്യൂമെട്രിക് ആണ്.
ഞങ്ങളുടെ എല്ലാ കയറ്റുമതി പ്ലാന്റുകളിലും കൺട്രോൾ പാനൽ PLC തരമാണ്. ഇത് ഒരു വലിയ മൂല്യവർദ്ധനയാണ്, കാരണം ഞങ്ങളുടെ ആവശ്യാനുസരണം PLC ഇഷ്ടാനുസൃതമാക്കാൻ കഴിയും. ഒരു PLC പാനൽ കൊണ്ട് സജ്ജീകരിച്ചിരിക്കുന്ന ഡ്രം മിക്സർ, മൈക്രോപ്രൊസസർ പാനലുള്ള ഒരു പ്ലാന്റിൽ നിന്ന് വ്യത്യസ്തമായ ഒരു യന്ത്രമാണ്. മൈക്രോപ്രൊസസർ പാനലുമായി താരതമ്യം ചെയ്യുമ്പോൾ PLC പാനലും മെയിന്റനൻസ് ഫ്രീയാണ്. ഉപഭോക്താക്കൾക്ക് അവരുടെ മത്സരത്തിൽ മുന്നിൽ നിൽക്കാൻ ഏറ്റവും മികച്ചത് നൽകുന്നതിൽ ഞങ്ങൾ എപ്പോഴും വിശ്വസിക്കുന്നു. അസ്ഫാൽറ്റ് ഡ്രം പ്ലാന്റുകളുടെ എല്ലാ നിർമ്മാതാക്കളും കയറ്റുമതിക്കാരും PLC പാനലുള്ള പ്ലാന്റ് വാഗ്ദാനം ചെയ്യുന്നില്ല.
ഞങ്ങളുടെ ഫാക്ടറിയിൽ നിന്ന് പുറപ്പെടുന്ന എന്തും സൈറ്റിൽ കുറച്ച് തടസ്സങ്ങളില്ലാതെ പ്രവർത്തിക്കാൻ തയ്യാറാണെന്ന് ഉറപ്പാക്കാൻ എല്ലാ സസ്യങ്ങളുടെയും പ്രീ ടെസ്റ്റിംഗ് നടത്തുന്നു.
സിനോറോഡറിന് 30 വർഷത്തിലധികം നിർമ്മാണ പരിചയവും പ്രൊഫഷണൽ സേവനവും വിലകുറഞ്ഞ സ്പെയറുകളും പിന്തുണയ്ക്കുന്ന ഒരു ഉൽപ്പന്നവും ഉണ്ട്, അതുവഴി വരും വർഷങ്ങളിൽ നിങ്ങളുടെ ഉപകരണങ്ങൾ നിങ്ങൾ വിലമതിക്കുകയും ഉപയോഗിക്കുകയും ചെയ്യുന്നു.