Atualmente, três tipos de usinas de mistura asfáltica a quente são mais populares
Transformar agregados e betume em asfalto para construir estradas requer um processo de mistura térmica. Uma usina de mistura asfáltica é indispensável para isso. O objetivo de uma usina de mistura asfáltica é misturar agregado e asfalto a uma temperatura elevada para produzir uma mistura homogênea de asfalto para pavimentação. O agregado utilizado pode ser de um único material, uma combinação de agregados graúdos e miúdos, com ou sem carga mineral. O material aglutinante usado é normalmente asfalto, mas pode ser uma emulsão asfáltica ou um de uma variedade de materiais modificados. Vários aditivos, incluindo materiais líquidos e em pó, também podem ser incorporados à mistura.
Atualmente, existem três tipos mais populares de usinas de mistura asfáltica a quente: mistura em lote, mistura em tambor e mistura em tambor contínuo. Todos os três tipos servem ao mesmo propósito final, e a mistura asfáltica deve ser essencialmente semelhante, independentemente do tipo de planta usada para fabricá-la. Os três tipos de plantas diferem, no entanto, em operação e fluxo de materiais, conforme descrito nas seções a seguir.
Usina de mistura de asfalto em loteA usina de mistura asfáltica é um equipamento essencial para qualquer empresa de construção de estradas. Qualquer operação de usina de mistura asfáltica tem muitas funções. As usinas de lotes de asfalto produzem mistura asfáltica a quente em uma série de lotes. Essas usinas de mistura em batelada produzem mistura asfáltica a quente em um processo contínuo. Também é possível alterar e utilizar este equipamento para produção de mistura asfáltica a quente com material reciclado. As usinas do tipo batelada possuem variações nelas que permitem a adição de RAP (Pavimento Asfáltico Recuperado). Os componentes de uma usina de mistura asfáltica padrão são: o sistema de alimentação a frio, o sistema de abastecimento de asfalto, o secador de agregados, a torre de mistura e o sistema de controle de emissões. A torre da planta de batelada consiste em um elevador quente, uma plataforma de peneiramento, silos quentes, uma tremonha de pesagem, uma caçamba de pesagem de asfalto e um pugmill. O agregado utilizado na mistura é retirado dos estoques e colocado em silos individuais de dosagem a frio. Agregados de diferentes tamanhos são proporcionados para fora de seus silos por uma combinação do tamanho da abertura da porta na parte inferior de cada silo e a velocidade da correia transportadora sob o silo. Geralmente, uma correia alimentadora abaixo de cada silo deposita o agregado em um transportador coletor localizado sob todos os silos de alimentação a frio. O agregado é transportado pelo transportador de coleta e transferido para um transportador de carregamento. O material no transportador de carregamento é então transportado até o secador de agregados.
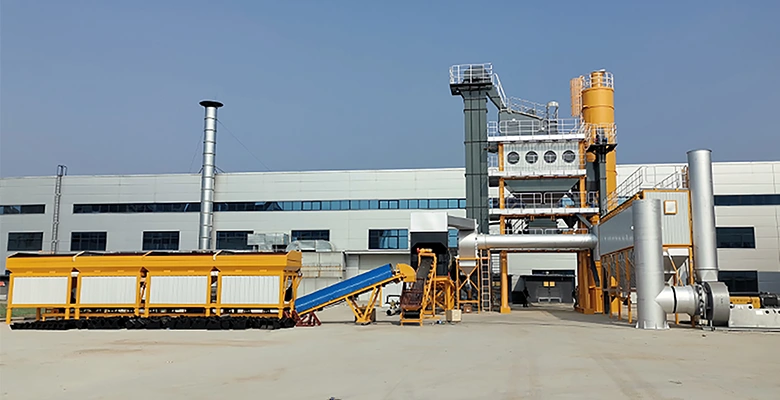
O secador funciona em contrafluxo. O agregado é introduzido no secador na extremidade superior e é movido para baixo no tambor tanto pela rotação do tambor (fluxo de gravidade) quanto pela configuração de vôo dentro do secador rotativo. O queimador está localizado na extremidade inferior do secador, e os gases de exaustão do processo de combustão e secagem se movem em direção à extremidade superior do secador, contra (contra) o fluxo do agregado. À medida que o agregado passa pelos gases de exaustão, o material é aquecido e seco. A umidade é removida e transportada para fora do secador como parte do fluxo de gás de exaustão.
O agregado quente e seco é então descarregado do secador na extremidade inferior. O agregado quente geralmente é transportado para o topo da torre de mistura da usina por um elevador de caçamba. Após a descarga do elevador, o agregado normalmente passa por um conjunto de peneiras vibratórias para, normalmente, um dos quatro silos de armazenamento quente. O material agregado mais fino passa diretamente por todas as telas para o silo quente nº 1; as partículas agregadas mais grossas são separadas pelo
telas de tamanhos diferentes e depositadas em uma das outras lixeiras quentes. A separação do agregado nos silos quentes depende do tamanho das aberturas na peneira que é utilizada no deck de peneiras e da gradação do agregado nos silos de alimentação a frio.
O agregado aquecido, seco e redimensionado é mantido nos silos quentes até ser descarregado por uma porta no fundo de cada silo para uma tremonha de pesagem. A proporção correta de cada agregado é determinada pelo peso.
Ao mesmo tempo em que o agregado está sendo dosado e pesado, o asfalto está sendo bombeado de seu tanque de armazenamento para um balde de pesagem aquecido separado localizado na torre logo acima do pugmill. A quantidade adequada de material é pesada no balde e mantida até ser esvaziada no pugmill. O agregado no funil de pesagem é esvaziado em um pugmill de eixo duplo e as diferentes frações de agregado são misturadas por um período de tempo muito curto - geralmente menos de 5 segundos. Após este breve tempo de mistura seca, o asfalto do balde de pesagem é descarregado.
no pugmill, e o tempo de mistura úmida começa. O tempo de mistura do asfalto com o agregado não deve ser maior do que o necessário para revestir completamente as partículas de agregado com uma película fina do material asfáltico - geralmente na faixa de 25 a 35 segundos, com o limite inferior dessa faixa sendo para um pugmill que está em boas condições. O tamanho do lote misturado no pugmill pode estar na faixa de 1,81 a 5,44 toneladas (2 a 6 toneladas).
Quando a mistura é concluída, as comportas no fundo do pugmill são abertas e a mistura é descarregada no veículo de transporte ou em um dispositivo de transporte que transporta a mistura para um silo de onde os caminhões serão carregados em lotes. Para a maioria das usinas de batelada, o tempo necessário para abrir as comportas do pugmill e descarregar a mistura é de aproximadamente 5 a 7 segundos. O tempo total de mistura (tempo de mistura seca + tempo de mistura úmida + tempo de descarga da mistura) para um lote pode ser tão curto quanto cerca de 40 segundos, mas normalmente o tempo total de mistura é de cerca de 45 segundos.
A planta está equipada com dispositivos de controle de emissões, compreendendo sistemas de coleta primária e secundária. Um coletor seco ou caixa de extração é normalmente usado como coletor primário. Um sistema de lavagem úmida ou, mais frequentemente, um sistema de filtro de tecido seco (baghouse) pode ser usado como sistema de coleta secundário para remover o material particulado dos gases de exaustão que saem do secador e enviar ar limpo para a atmosfera através da chaminé .
Se o RAP for incorporado à mistura, ele é colocado em um silo de alimentação a frio separado, de onde é entregue à planta. O RAP pode ser adicionado ao novo agregado em um dos três locais: a parte inferior do elevador quente; as lixeiras quentes; ou, mais comumente, o funil de pesagem. A transferência de calor entre o novo agregado superaquecido e o material recuperado começa assim que os dois materiais entram em contato e continua durante o processo de mistura no pugmill.
Usina de Asfalto de Mistura de TamboresComparando com o tipo de lote, a usina de asfalto de mistura de tambor tem menos perda térmica, menor potência de trabalho, sem transbordamento, menos poeira voando e controle de temperatura estável. O sistema de controle ajusta automaticamente a taxa de fluxo de asfalto de acordo com a taxa de fluxo de agregados e pré-ajusta a relação asfalto-agregados, para garantir uma saída proporcional precisa. A usina de mistura de tambor de asfalto é o tipo de usina que é categorizada como usina de mistura contínua, produz asfalto de mistura quente em um processo contínuo.
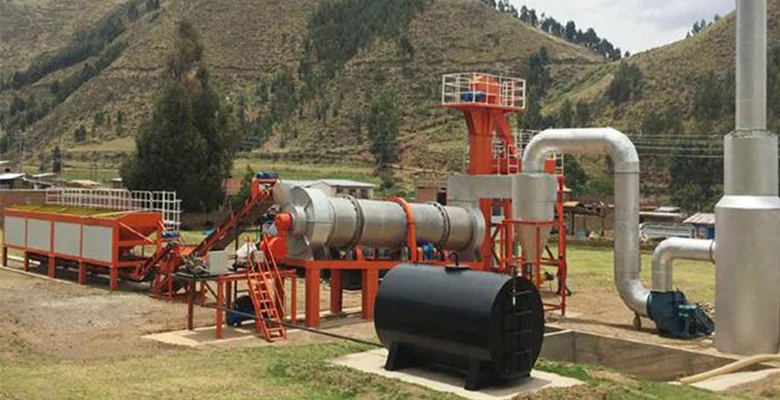
Normalmente, os sistemas de alimentação a frio nas plantas de batelada e de mistura de tambor HMA são semelhantes. Cada um consiste em silos de alimentação fria, transportadores de alimentação, um transportador de coleta e um transportador de carregamento. Na maioria das usinas de mistura de tambores e em algumas usinas de batelada, uma tela de escalpe é incluída no sistema em algum ponto. Se o RAP também estiver sendo alimentado na planta para produzir uma mistura reciclada, um ou mais silos de alimentação a frio, correia alimentadora e/ou transportador de coleta, peneira de escalpelamento e transportador de carregamento são necessários para manusear o material extra. As usinas de mistura de tambor consistem em cinco componentes principais: o sistema de alimentação a frio, o sistema de abastecimento de asfalto, o misturador de tambor, os silos de armazenamento e o equipamento de controle de emissões.
Os silos de alimentação a frio são usados para dosar o material para a planta. Uma correia alimentadora de velocidade variável é usada sob cada caixa. A quantidade de agregado retirada de cada silo pode, assim, ser controlada tanto pelo tamanho da abertura do portão quanto pela velocidade da correia alimentadora para fornecer uma entrega precisa dos materiais de tamanhos diferentes. O agregado em cada correia alimentadora é depositado em um transportador de coleta que passa por baixo de todos os silos de alimentação a frio. O material combinado é normalmente passado por uma tela de escalpelamento e então transferido para um transportador de carregamento para transporte para o misturador de tambor.
A esteira de carga é equipada com dois dispositivos que determinam a quantidade de agregado que está sendo entregue à usina: uma balança sob a esteira transportadora mede o peso do agregado que passa por ela e um sensor determina a velocidade da esteira. Esses dois valores são usados para calcular o peso úmido do agregado, em toneladas (toneladas) por hora, entrando no misturador de tambor. O computador da usina, com a quantidade de umidade no agregado fornecida como valor de entrada, converte o peso úmido em peso seco para determinar a quantidade correta de asfalto necessária na mistura.
O misturador de tambor convencional é um sistema de fluxo paralelo - os gases de exaustão e o agregado se movem na mesma direção. O queimador está localizado na extremidade superior (extremidade de entrada do agregado) do tambor. O agregado entra no tambor a partir de um chute inclinado acima do queimador ou em um transportador Slinger sob o queimador. O agregado é movido para baixo no tambor por uma combinação de gravidade e configuração das lamelas localizadas dentro do tambor. À medida que se desloca, o agregado é aquecido e a umidade removida. Um véu denso de agregado é construído próximo ao ponto médio do comprimento do tambor para auxiliar no processo de transferência de calor.
Se o RAP for adicionado ao novo agregado, ele é depositado de seu próprio silo de alimentação a frio e sistema transportador de coleta/carregamento em uma entrada localizada próxima ao centro do comprimento do tambor (sistema de alimentação dividida). Nesse processo, o material recuperado é protegido dos gases de escape de alta temperatura pelo véu de novo agregado a montante do ponto de entrada do RAP. Quando misturas com alto conteúdo de RAP são usadas, é mais provável que o RAP seja superaquecido no processo. Isso pode resultar na emissão de fumaça do tambor ou danos ao RAP.
O novo agregado e o material recuperado, se usados, movem-se juntos para a parte traseira do tambor. O asfalto é puxado do tanque de armazenamento por uma bomba e alimentado por um medidor, onde é determinado o volume adequado de asfalto. O material aglutinante é então entregue através de um tubo na parte traseira do tambor de mistura, onde o asfalto é injetado no agregado. O revestimento do agregado ocorre quando os materiais são misturados e movidos para a extremidade de descarga do tambor. Carga mineral ou finos de manga, ou ambos, também são adicionados na parte de trás do tambor, pouco antes ou em conjunto com a adição do asfalto.
A mistura asfáltica é depositada em um dispositivo de transporte (um transportador de ripas de arrasto, transportador de correia ou elevador de caçamba) para transporte para um silo de armazenamento. O silo converte o fluxo contínuo de mistura em um fluxo de lote para descarga no veículo de transporte.
Em geral, o mesmo tipo de equipamento de controle de emissões é usado na planta de mistura de tambor e na planta de batelada. Um coletor seco primário e um sistema de depuração úmida ou um coletor secundário de filtro de mangas podem ser usados. Se for usado um sistema de depuração úmida, os finos coletados não podem ser reciclados de volta à mistura e são desperdiçados; se for utilizado um filtro de mangas, os finos recolhidos podem ser devolvidos total ou parcialmente ao tambor misturador, ou podem ser desperdiçados.
Usina de Asfalto de Mistura ContínuaNas plantas contínuas não há interrupção no ciclo de produção, pois o ritmo de produção não é dividido em lotes. A mistura do material ocorre dentro do tambor secador que é alongado, pois seca e mistura o material ao mesmo tempo. Como não há torre de mistura ou elevadores, o sistema é, portanto, consideravelmente simplificado, com a consequente redução do custo de manutenção. A ausência da peneira, no entanto, torna necessário um controle preciso no início do ciclo de produção, antes que os agregados sejam alimentados no secador e, consequentemente, sejam descarregados do secador como asfalto.
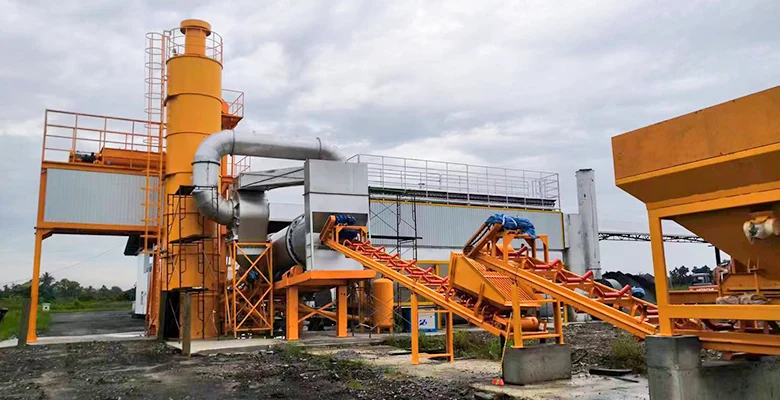
MEDIÇÃO AGREGADA
Semelhante às usinas de mistura asfáltica em batelada,
o ciclo de produção das usinas contínuas também se inicia nos dosadores a frio, onde os agregados são geralmente dosados por volume; se necessário, o extrator de areia pode ser equipado com um cinto de pesagem para dosagem.
O controle do peso total dos agregados virgens, no entanto, é feito em duas fases diferentes do ciclo de produção nas duas plantas diferentes. No tipo contínuo existe uma esteira alimentadora, antes que os agregados úmidos sejam alimentados no tambor secador, onde o teor de umidade é ajustado manualmente para permitir a subtração do peso da água. Por isso é de extrema importância que o teor de umidade dos agregados, principalmente da areia, tenha um valor constante, continuamente monitorado por meio de frequentes testes de laboratório.
DOSAGEM DE BETUME
Em plantas contínuas a dosagem de betume é geralmente volumétrica através de um contador de litros posterior à bomba de alimentação. Alternativamente, é possível instalar um contador de massa, uma escolha necessária se for usado betume modificado, o que requer operações de limpeza frequentes.
Medição de enchimento
Em plantas contínuas, o sistema de dosagem é normalmente volumétrico, usando roscas de alimentação de velocidade variável que substituíram o sistema de dosagem pneumático anterior.
O painel de controle é do tipo PLC em todas as nossas fábricas de exportação. Esta é uma grande adição de valor porque podemos personalizar o PLC conforme nossa necessidade. O misturador de tambor equipado com um painel PLC é uma máquina diferente de uma planta com painel microprocessado. O painel PLC também é livre de manutenção em comparação com o painel do microprocessador. Sempre acreditamos em dar o melhor aos clientes para que eles possam ficar à frente da concorrência. Nem todos os fabricantes e exportadores de usinas de tambor de asfalto oferecem usina com painel PLC.
O pré-teste de todas as plantas é feito para garantir que tudo o que sai de nossa fábrica esteja pronto para funcionar com menos problemas no local.
Sinoroader tem mais de 30 anos de experiência em fabricação e um produto que é apoiado por serviço profissional e peças de reposição mais baratas para que você aprecie e use seu equipamento por muitos anos.