В настоящее время более популярны три типа заводов по производству горячего асфальтобетона.
Превращение заполнителей и битума в асфальт для строительства дорог требует процесса термического смешивания. Для этого незаменима асфальтосмесительная установка. Назначение асфальтосмесительной установки состоит в том, чтобы смешать заполнитель и асфальт вместе при повышенной температуре для получения однородной асфальтобетонной смеси. Используемый заполнитель может быть одним материалом, комбинацией крупных и мелких заполнителей, с минеральным наполнителем или без него. Используемый вяжущий материал обычно представляет собой асфальт, но может представлять собой битумную эмульсию или один из множества модифицированных материалов. В смесь также могут быть включены различные добавки, в том числе жидкие и порошкообразные материалы.
В настоящее время существует еще три популярных типа заводов по производству горячего асфальтобетона: периодическая смесь, барабанная смесь и барабанная смесь непрерывного действия. Все три типа служат одной и той же конечной цели, и асфальтовая смесь должна быть по существу одинаковой, независимо от типа завода, используемого для ее производства. Однако три типа установок различаются по работе и потоку материалов, как описано в следующих разделах.
Асфальтовый завод периодического действия
Асфальтобетонные заводы – ключевое оборудование для любой дорожно-строительной компании. Работа любого завода по производству асфальтобетонных смесей имеет множество функций. Асфальтобетонные заводы производят горячую асфальтобетонную смесь несколькими партиями. Эти заводы периодического действия производят горячую асфальтобетонную смесь в непрерывном процессе. Это оборудование также можно модифицировать и использовать для производства горячей асфальтобетонной смеси из вторсырья. Заводы периодического действия имеют модификации, которые позволяют добавлять РАП (восстановленное асфальтовое покрытие). Компонентами стандартного асфальтосмесительного завода являются: система холодной подачи, система подачи асфальта, сушилка заполнителя, смесительная башня и система контроля выбросов. Башня бетонного завода состоит из горячего элеватора, грохота, горячих бункеров, бункера для взвешивания, ковша для взвешивания асфальта и мельницы. Заполнитель, используемый в смеси, снимается со складов и размещается в индивидуальных бункерах холодного питания. Заполнители разных размеров дозируются из своих бункеров в зависимости от комбинации размера открытия ворот на дне каждого бункера и скорости конвейерной ленты под бункером. Как правило, питающая лента под каждым бункером помещает заполнитель на сборочный конвейер, расположенный под всеми бункерами холодного питания. Заполнитель транспортируется сборочным конвейером и передается на загрузочный конвейер. Затем материал по загрузочному конвейеру подается в сушилку заполнителя.
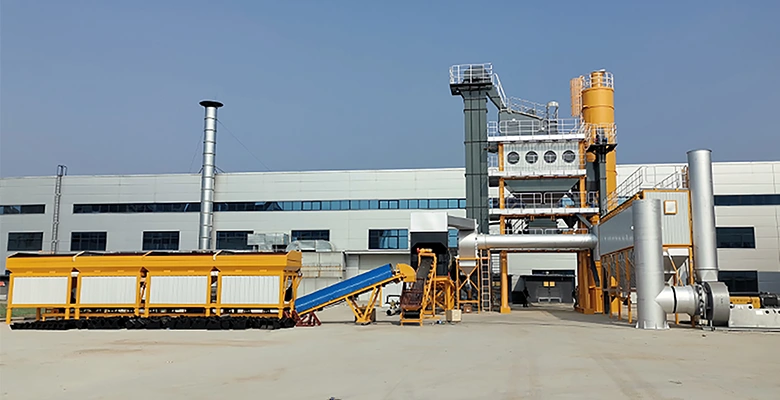
Сушилка работает по принципу противотока. Заполнитель вводится в сушилку с верхнего конца и перемещается вниз по барабану как за счет вращения барабана (самотеком), так и за счет конфигурации полета внутри вращающейся сушилки. Горелка расположена в нижней части сушилки, а выхлопные газы процесса сжигания и сушки движутся к верхней части сушилки, против потока агрегата. Когда заполнитель проходит через выхлопные газы, материал нагревается и высушивается. Влага удаляется и выносится из сушилки в составе потока отходящих газов.
Затем горячий сухой заполнитель выгружается из сушилки на нижнем конце. Горячий заполнитель обычно транспортируется наверх смесительной башни завода с помощью ковшового элеватора. После выгрузки из элеватора заполнитель обычно проходит через набор вибрационных грохотов, как правило, в один из четырех горячих накопительных бункеров. Самый мелкий заполнитель проходит прямо через все грохоты в горячий бункер № 1; более крупные частицы заполнителя отделяются
экраны разного размера и помещены в один из других горячих бункеров. Разделение заполнителя на горячие бункеры зависит от размера отверстий в сите, используемом в деке грохота, и градации заполнителя в бункерах с холодным питанием.
Нагретый, высушенный и измененный по размеру заполнитель хранится в горячих бункерах до тех пор, пока не будет выгружен через ворота в нижней части каждого бункера в весовой бункер. Правильная пропорция каждого заполнителя определяется по весу.
Одновременно с дозированием и взвешиванием заполнителя асфальт перекачивается из резервуара для хранения в отдельный подогреваемый ковш для взвешивания, расположенный на башне прямо над мельницей. Необходимое количество материала взвешивается в ведре и удерживается до тех пор, пока не будет высыпано в измельчитель. Заполнитель из весового бункера выгружается в двухвальную мельницу, и различные фракции заполнителя смешиваются вместе в течение очень короткого периода времени — обычно менее 5 секунд. После этого короткого периода сухой смеси асфальт из весового ковша выгружается.
в pugmill, и начинается время мокрой смеси. Время смешивания асфальта с заполнителем должно быть не больше времени, необходимого для полного покрытия частиц заполнителя тонкой пленкой битумного материала — обычно в диапазоне от 25 до 35 секунд, причем нижняя граница этого диапазона быть для pugmill, который находится в хорошем состоянии. Размер партии, смешанной в мельнице, может составлять от 1,81 до 5,44 тонны (от 2 до 6 тонн).
Когда смешивание завершено, ворота в нижней части мельницы открываются, и смесь выгружается в транспортное средство или в транспортное устройство, которое доставляет смесь в силос, из которого грузовики будут загружаться партиями. Для большинства заводов периодического действия время, необходимое для открытия заслонок мельницы и выгрузки смеси, составляет примерно 5–7 секунд. Общее время смешивания (время сухого смешивания + время мокрого смешивания + время выгрузки смеси) для партии может составлять всего около 40 секунд, но обычно общее время смешивания составляет около 45 секунд.
Завод оснащен устройствами контроля выбросов, включающими как первичную, так и вторичную системы сбора. В качестве первичного коллектора обычно используется сухой коллектор или выбивная коробка. Либо система мокрого скруббера, либо, чаще, система сухих тканевых фильтров (рукавный фильтр) может использоваться в качестве вторичной системы сбора для удаления твердых частиц из выхлопных газов, выходящих из осушителя, и направления чистого воздуха в атмосферу через дымовую трубу. .
Если РАП включен в смесь, он помещается в отдельный бункер холодного питания, из которого доставляется на завод. RAP можно добавить к новому заполнителю в одном из трех мест: в нижней части горячего элеватора; горячие баки; или, чаще всего, весовой бункер. Теплопередача между перегретым новым заполнителем и восстановленным материалом начинается, как только два материала вступают в контакт, и продолжается в процессе смешивания в смесителе.
Асфальтовый завод барабанной смеси
По сравнению с заводом периодического действия, асфальтобетонный завод барабанного типа имеет меньшие тепловые потери, меньшую рабочую мощность, отсутствие перелива, меньше летания пыли и стабильный контроль температуры. Система управления автоматически регулирует расход асфальта в соответствии с расходом заполнителя и предварительно установленным соотношением асфальта и заполнителя, чтобы обеспечить точную пропорциональную производительность. Асфальтобетонные барабанные заводы — это типы заводов, которые относятся к категории заводов непрерывного действия и производят горячую асфальтобетонную смесь в непрерывном процессе.
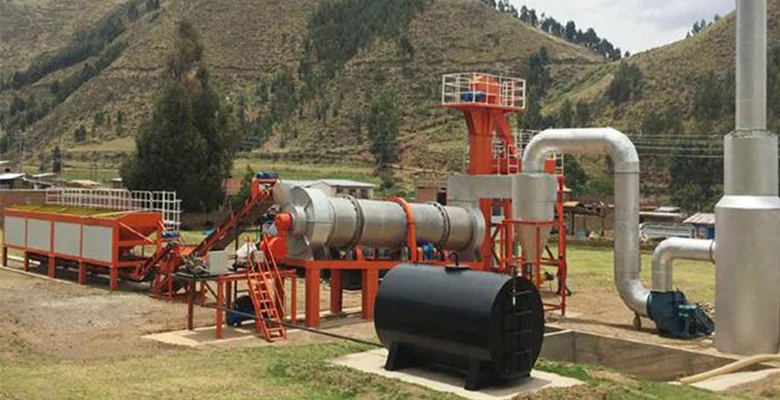
Как правило, системы холодной подачи на заводах периодического и барабанного смешения HMA аналогичны. Каждая из них состоит из бункеров холодного питания, подающих конвейеров, сборочного конвейера и загрузочного конвейера. На большинстве заводов по производству барабанных смесей и на некоторых заводах периодического действия в систему в какой-то момент включается грохот для скальпирования. Если RAP также подается на завод для производства переработанной смеси, для обработки дополнительного материала необходимы дополнительный бункер или бункеры для холодной подачи, ленточный питатель и/или сборочный конвейер, грохот для скальпирования и загрузочный конвейер. барабанные смесительные установки состоят из пяти основных компонентов: системы подачи холодного сырья, системы подачи асфальта, барабанного смесителя, уравнительного или накопительного бункера и оборудования для контроля выбросов.
Бункеры с холодным питанием используются для распределения материала по фабрике. Лента подачи с переменной скоростью используется под каждым бункером. Таким образом, количество заполнителя, извлекаемого из каждого бункера, можно контролировать как размером отверстия затвора, так и скоростью ленты питателя, чтобы обеспечить точную подачу материалов разного размера. Заполнитель на каждой питающей ленте осаждается на сборочный конвейер, который проходит под всеми бункерами холодного питания. Объединенный материал обычно проходит через сито для скальпирования, а затем переносится на загрузочный конвейер для транспортировки в барабанный смеситель.
Загрузочный конвейер оборудован двумя устройствами, которые используются для определения количества заполнителя, подаваемого на завод: мостовые весы под конвейерной лентой измеряют вес проходящего по нему заполнителя, а датчик определяет скорость движения ленты. Эти два значения используются для расчета сырого веса заполнителя в тоннах (тоннах) в час, поступающего в барабанный смеситель. Заводской компьютер с количеством влаги в заполнителе, предоставленным в качестве входного значения, преобразует влажный вес в сухой вес, чтобы определить правильное количество асфальта, необходимое в смеси.
Обычный барабанный смеситель представляет собой систему с параллельным потоком — выхлопные газы и заполнитель движутся в одном направлении. Горелка расположена на верхнем конце (агрегатном входе) барабана. Заполнитель поступает в барабан либо по наклонному желобу над горелкой, либо по транспортеру стропальщика под горелкой. Агрегат перемещается вниз по барабану под действием силы тяжести и конфигурации скребков, расположенных внутри барабана. По мере движения заполнитель нагревается и удаляется влага. Плотная завеса заполнителя создается около середины длины барабана, чтобы способствовать процессу теплопередачи.
Если к новому заполнителю добавляется РАП, он подается из собственного бункера холодного питания и сборной/загрузочной конвейерной системы во впускное отверстие, расположенное ближе к центру длины барабана (система раздельной подачи). В этом процессе регенерируемый материал защищен от высокотемпературных выхлопных газов завесой из нового заполнителя перед точкой входа РАП. При использовании смесей с высоким содержанием РАП более вероятно, что РАП будет перегреваться в процессе. Это может привести к выделению дыма из барабана или повреждению РПД.
Новый заполнитель и регенерированный материал, если они используются, перемещаются вместе в заднюю часть барабана. Асфальт вытягивается из резервуара с помощью насоса и подается через дозатор, где определяется необходимый объем асфальта. Затем вяжущий материал подается по трубе в заднюю часть смесительного барабана, где асфальт впрыскивается на заполнитель. Покрытие заполнителя происходит по мере того, как материалы перемешиваются и перемещаются к разгрузочному концу барабана. Минеральный наполнитель или мелочь рукавного фильтра, или и то и другое, также добавляются в заднюю часть барабана либо непосредственно перед добавлением асфальта, либо одновременно с ним.
Асфальтовая смесь укладывается в конвейерное устройство (скребковый пластинчатый конвейер, ленточный конвейер или ковшовый элеватор) для транспортировки в силос для хранения. Силос преобразует непрерывный поток смеси в порционный поток для выгрузки в транспортное средство.
Как правило, на заводе барабанного смешения используется тот же тип оборудования для контроля выбросов, что и на заводе периодического действия. Можно использовать первичный сухой коллектор и либо систему мокрого скруббера, либо вторичный коллектор с рукавным фильтром. Если используется система мокрого скруббера, собранная мелочь не может быть повторно использована в смеси и тратится впустую; если используется рукавный фильтр, собранная мелочь может быть полностью или частично возвращена в смесительный барабан, или же она может быть потрачена впустую.
Асфальтовый завод непрерывного действия
В непрерывных установках производственный цикл не прерывается, так как ритм производства не разбит на партии. Смешивание материала происходит внутри сушильного барабана, который имеет удлиненную форму, так как он сушит и перемешивает материал одновременно. Поскольку нет смесительной башни или элеваторов, система значительно упрощается, что приводит к снижению затрат на техническое обслуживание. Однако отсутствие грохота требует точного контроля в начале производственного цикла, перед подачей заполнителей в сушилку и перед их последующей выгрузкой из сушилки в виде асфальта.
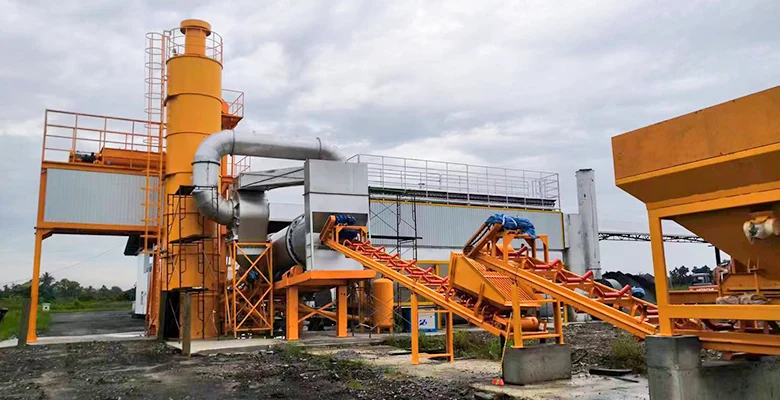
ОБЩИЙ УЧЕТ
Подобно асфальтосмесительным установкам периодического действия,
производственный цикл установок непрерывного действия также начинается с холодных питателей, где заполнители, как правило, дозируются по объему; При необходимости пескоуловитель можно оснастить ленточными весами для дозирования.
Однако контроль общего веса первичных заполнителей осуществляется на двух разных фазах производственного цикла на двух разных заводах. В непрерывном типе перед подачей влажных заполнителей в сушильный барабан имеется конвейерная лента, где содержание влаги устанавливается вручную, чтобы можно было вычесть вес воды. Поэтому чрезвычайно важно, чтобы содержание влаги в заполнителях, особенно в песке, имело постоянное значение, которое постоянно контролируется с помощью частых лабораторных испытаний.
УЧЕТ БИТУМА
В установках непрерывного действия дозирование битума, как правило, осуществляется объемным способом с помощью счетчика литров, расположенного после подающего насоса. В качестве альтернативы можно установить счетчик массы, необходимый выбор, если используется модифицированный битум, который требует частых операций по очистке.
дозирование наполнителя
В установках непрерывного действия система дозирования обычно объемная, с использованием подающих шнеков с регулируемой скоростью, которые заменили предыдущую пневматическую дозирующую систему.
Панель управления типа PLC на всех наших экспортных заводах. Это огромное преимущество, потому что мы можем настроить ПЛК в соответствии с нашими требованиями. Барабанный смеситель, оснащенный панелью ПЛК, отличается от установки с панелью микропроцессора. Панель ПЛК также не требует технического обслуживания по сравнению с панелью микропроцессора. Мы всегда верим в лучшее для клиентов, чтобы они могли оставаться впереди своих конкурентов. Не все производители и экспортеры асфальтобетонных заводов предлагают установку с панелью ПЛК.
Предварительное тестирование всех установок проводится для того, чтобы гарантировать, что все, что покидает наш завод, готово к работе с меньшими трудностями на месте.
Sinoroader имеет более чем 30-летний опыт производства и продукт, который поддерживается профессиональным обслуживанием и более дешевыми запчастями, чтобы вы дорожили своим оборудованием и использовали его долгие годы.