Тренутно су популарнија три типа постројења за мешање врућег асфалта
Претварање агрегата и битумена у асфалт за изградњу путева захтева процес термичког мешања. За ово је неопходна фабрика за мешање асфалта. Сврха постројења за мешање асфалта је мешање агрегата и асфалта заједно на повишеној температури како би се добила хомогена мешавина за асфалтирање. Употребљени агрегат може бити један материјал, комбинација крупних и финих агрегата, са или без минералног пунила. Везивни материјал који се користи је обично асфалт, али може бити асфалтна емулзија или један од различитих модификованих материјала. У смешу се такође могу уградити различити адитиви, укључујући течне и прашкасте материјале.
Тренутно постоје још три популарна типа постројења за мешање врућег асфалта: шаржна мешавина, мешавина бубња и континуална мешавина бубња. Сва три типа служе истој крајњој сврси, а асфалтна мешавина би у суштини требало да буде слична без обзира на врсту постројења која се користи за њену производњу. Међутим, три типа постројења се разликују по раду и протоку материјала, као што је описано у следећим одељцима.
Фабрика серијске мешавине асфалтаПостројење за мешање асфалта је кључна опрема сваке компаније за изградњу путева. Било који рад постројења за мешање асфалта има много функција. Асфалтне серије производе врућу мешавину асфалта у низу серија. Ова постројења за серијску мешавину производе врућу мешавину асфалта у континуираном процесу. Такође је могуће мењати и користити ову опрему за производњу вруће мешавине асфалта од рециклираног материјала. Постројења серијског типа имају варијације које дозвољавају додавање РАП-а (Рецлаимед асфалтни коловоз). Компоненте стандардне фабрике за мешање асфалта су: систем за хладно напајање, систем за снабдевање асфалтом, сушара агрегата, торањ за мешање и систем за контролу емисије. Торањ за серијско постројење се састоји од топлог лифта, палубе за сито, врућих канти, резервоара за мерење, кашике за мерење асфалта и млина. Агрегат који се користи у мешавини се уклања из залиха и ставља у појединачне канте за хладну храну. Агрегати различитих величина се издвајају из својих канти комбинацијом величине отвора капије на дну сваке канте и брзине транспортне траке испод канте. Генерално, доводна трака испод сваке канте одлаже агрегат на сабирни транспортер који се налази испод свих канти за хладно пуњење. Агрегат се транспортује сабирним транспортером и преноси на транспортер за пуњење. Материјал на транспортеру за пуњење се затим преноси до сушаре агрегата.
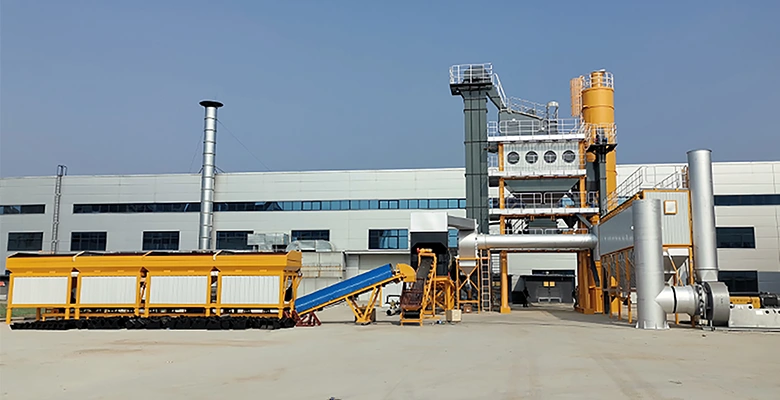
Сушара ради на принципу противтока. Агрегат се уводи у сушару на горњем крају и помера се низ бубањ и ротацијом бубња (гравитационим током) и конфигурацијом лета унутар ротирајуће сушаре. Горионик се налази на доњем крају сушаре, а издувни гасови из процеса сагоревања и сушења крећу се ка горњем крају сушаре, против (против) протока агрегата. Како се агрегат провлачи кроз издувне гасове, материјал се загрева и суши. Влага се уклања и изводи из сушаре као део струје издувних гасова.
Врући, суви агрегат се затим испушта из сушаре на доњем крају. Врући агрегат се обично транспортује до врха торња за мешање постројења помоћу елеватора. Након пражњења из лифта, агрегат нормално пролази кроз сет вибрирајућих сита у, типично, једну од четири канте за топло складиштење. Најфинији агрегатни материјал иде директно кроз сва сита у врућу канту бр. 1; грубље честице агрегата су одвојене
сита различите величине и депоновани у једну од других врућих канти. Раздвајање агрегата у вруће посуде зависи од величине отвора на ситу који се користи у ситој палуби и градације агрегата у посудама за хладно пуњење.
Загрејани, осушени и промењени агрегати се држе у врућим кантама док се не испусте из капије на дну сваке канте у резервоар за мерење. Тачна пропорција сваког агрегата је одређена тежином.
У исто време када се агрегат одмерава и вага, асфалт се пумпа из свог резервоара за складиштење у засебну загрејану канту за мерење која се налази на торњу одмах изнад млин. Одговарајућа количина материјала се извага у канту и држи док се не испразни у млин. Агрегат у резервоару за вагу се празни у млин са две осовине, а различите фракције агрегата се мешају заједно током веома кратког временског периода— обично мање од 5 секунди. Након овог кратког времена суве мешавине, асфалт се избацује из кашике.
у млин и почиње време мокрог мешања. Време мешања за мешање асфалта са агрегатом не би требало да буде дуже од потребног да се честице агрегата потпуно обложе танким филмом асфалтног материјала — обично у распону од 25 до 35 секунди, са доњом граном овог опсега за млин који је у добром стању. Величина шарже која се меша у млину може бити у распону од 1,81 до 5,44 тоне (2 до 6 тона).
Када је мешање завршено, капије на дну млина се отварају, а мешавина се испушта у транспортно возило или у транспортни уређај који носи мешавину до силоса из којег ће се камиони утоварити у серијама. За већину серијских постројења, време потребно да се отворе капије пугмилл и испразне смеша је отприлике 5 до 7 секунди. Укупно време мешања (време сувог мешања + време мокрог мешања + време пражњења мешавине) за серију може бити само око 40 секунди, али обично је укупно време мешања око 45 секунди.
Постројење је опремљено уређајима за контролу емисије, који обухватају примарни и секундарни систем за сакупљање. Суви колектор или кутија за избацивање се обично користи као примарни колектор. Или систем за мокро чишћење или, чешће, систем филтера од суве тканине (багхоусе) може се користити као секундарни систем за сакупљање за уклањање честица из издувних гасова који излазе из сушаре и шаљу чист ваздух у атмосферу кроз димњак. .
Ако се РАП угради у мешавину, он се ставља у посебну канту за хладну храну из које се испоручује у постројење. РАП се може додати новом агрегату на једној од три локације: на дну врућег лифта; вруће канте; или, најчешће, резервоар за вагу. Пренос топлоте између прегрејаног новог агрегата и обновљеног материјала почиње чим два материјала дођу у контакт и наставља се током процеса мешања у млину.
Фабрика асфалтних мешавина бубњеваУ поређењу са серијским типом, фабрика за мешање асфалта у бубњу има мање топлотних губитака, мању радну снагу, нема преливања, мање летења прашине и стабилну контролу температуре. Контролни систем аутоматски прилагођава брзину протока асфалта у складу са протоком агрегата и унапред подешеним односом асфалт-агрегат, како би се обезбедио прецизан пропорционални учинак. Постројења за мешање асфалтних бубњева су врсте постројења које су категорисане као постројења за континуално мешање, производе врућу мешавину асфалта у континуираном процесу.
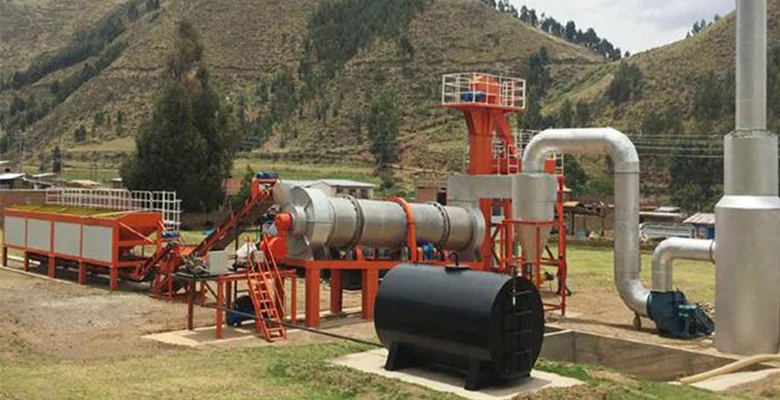
Типично, системи хладног храњења на ХМА серијским и бачвастим мешавинама су слични. Сваки се састоји од канти за хладно пуњење, доводних транспортера, сабирног транспортера и транспортера за пуњење. На већини постројења за мешање у бубњевима и на неким серијским постројењима, сито за скалпирање је укључено у систем у неком тренутку. Ако се РАП такође уноси у постројење да би се произвела рециклирана мешавина, додатна канта или канте за хладно пуњење, трака за довод и/или сабирни транспортер, сито за скалпирање и транспортер за пуњење су неопходни за руковање додатним материјалом. Постројења за мешање бубњева се састоје од пет главних компоненти: система за хладно напајање, система за снабдевање асфалтом, мешалице бубња, силоса за пренапон или складиштење и опреме за контролу емисије.
Канте за хладну храну користе се за пропорцију материјала према биљци. Испод сваке канте се користи трака за додавање са променљивом брзином. Количина агрегата извучена из сваке канте може се тако контролисати и величином отвора капије и брзином доводне траке како би се обезбедила тачна испорука материјала различитих величина. Агрегат на свакој доводној траци се одлаже на сабирни транспортер који пролази испод свих канти за хладно пуњење. Комбиновани материјал се обично пропушта кроз сито за скалпирање, а затим се преноси у транспортер за пуњење за транспорт у бубањ миксер.
Транспортер за пуњење је опремљен са два уређаја који се користе за одређивање количине агрегата који се испоручује у постројење: мост за мерење испод транспортне траке мери тежину агрегата који пролази преко ње, а сензор одређује брзину траке. Ове две вредности се користе за израчунавање влажне тежине агрегата, у тонама (тона) на сат, који улази у бубањ миксер. Рачунар постројења, са количином влаге у агрегату која је дата као улазна вредност, претвара мокру тежину у суву тежину како би се одредила тачна количина асфалта потребна у мешавини.
Конвенционални бубањ миксер је систем са паралелним протоком - издувни гасови и агрегат се крећу у истом смеру. Горионик се налази на горњем крају (крају на улазу агрегата) бубња. Агрегат улази у бубањ или из косог отвора изнад горионика или на Слингер транспортеру испод горионика. Агрегат се помера низ бубањ комбинацијом гравитације и конфигурације летова смештених унутар бубња. Док путује, агрегат се загрева и влага се уклања. Густи вео агрегата је изграђен близу средине дужине бубња да би помогао у процесу преноса топлоте.
Ако се РАП дода новом агрегату, он се депонује из сопствене канте за хладно пуњење и сабирног система транспортера за пуњење у улаз који се налази близу центра дужине бубња (систем подељеног довода). У овом процесу, регенерисани материјал је заштићен од високотемпературних издувних гасова велом новог агрегата узводно од улазне тачке РАП-а. Када се користе мешавине са високим садржајем РАП-а, већа је вероватноћа да ће РАП бити прегрејан током процеса. То може довести до избијања дима из бубња или оштећења РАП-а.
Нови агрегат и регенерисани материјал, ако се користе, померају се заједно у задњи део бубња. Асфалт се пумпом извлачи из резервоара и доводи кроз метар, где се одређује одговарајућа запремина асфалта. Везивни материјал се затим испоручује кроз цев у задњи део бубња за мешање, где се асфалт убризгава на агрегат. Облагање агрегата настаје када се материјали преврћу заједно и померају до краја бубња за пражњење. Минерална пунила или ситне материје, или обоје, се такође додају у задњи део бубња, непосредно пре или заједно са додатком асфалта.
Асфалтна мешавина се одлаже у транспортни уређај (покретни транспортер, тракасти транспортер или елеватор) за транспорт до складишног силоса. Силос претвара континуирани ток мешавине у шаржни ток за испуштање у транспортно возило.
Уопштено говорећи, исти тип опреме за контролу емисија се користи у постројењу за мешање у бубњевима као и на серијском постројењу. Могу се користити примарни суви колектор и систем за мокро чишћење или секундарни колектор са врећастом комором. Ако се користи систем за мокро прање, прикупљене ситне честице се не могу рециклирати назад у мешавину и расипају се; ако се користи врећа, прикупљене казне се могу вратити у целини или делимично у бубањ за мешање, или се могу потрошити.
Фабрика континуалног мешања асфалтаУ континуалним постројењима нема прекида у производном циклусу јер се ритам производње не дели на серије. Мешање материјала се одвија унутар бубња за сушење који је издужен, пошто се истовремено суши и меша материјал. Пошто нема торња за мешање или лифтова, систем је због тога знатно поједностављен, са последичним смањењем трошкова одржавања. Међутим, одсуство сита чини неопходним прецизне контроле на почетку производног циклуса, пре него што се агрегати унесу у сушару и пре него што се последично испусте из сушаре као асфалт.
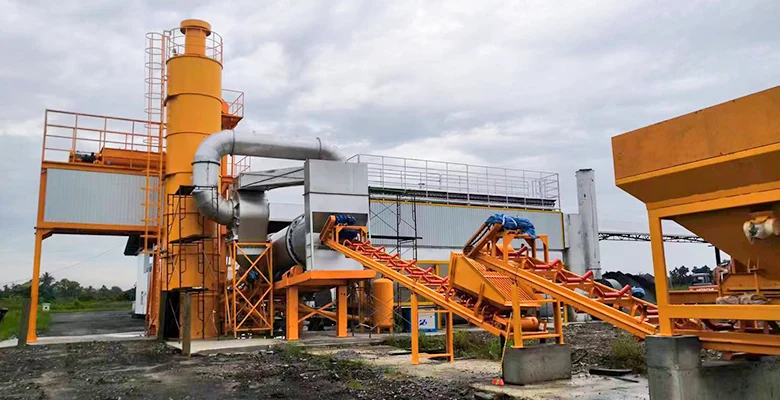
АГРЕГАТНО МЕРЕЊЕ
Слично постројењима за серијско мешање асфалта,
производни циклус континуалних постројења такође почиње са хладним хранилицама, где се агрегати углавном дозирају по запремини; ако је потребно, усисивач песка се може опремити траком за мерење.
Контрола укупне тежине првобитних агрегата се, међутим, врши у две различите фазе производног циклуса у две различите фабрике. У континуалном типу постоји доводна трака, пре него што се влажни агрегати доводе у бубањ сушаре, где се садржај влаге подешава ручно како би се омогућило да се одузме тежина воде. Због тога је изузетно важно да садржај влаге у агрегатима, посебно у песку, има константну вредност која се континуирано прати честим лабораторијским испитивањима.
БИТУМЕН МЕТЕРИНГ
У континуалним постројењима дозирање битумена је генерално волуметријско преко бројача литара након доводне пумпе. Алтернативно, могуће је уградити бројач масе, неопходан избор ако се користи модификовани битумен, који захтева честе операције чишћења.
Дозирање пунила
У континуалним постројењима систем за дозирање је обично волуметријски, користећи вијке за дозирање променљиве брзине који су заменили претходни пнеуматски систем за дозирање.
Контролна табла је типа ПЛЦ у свим нашим извозним погонима. Ово је огроман додатак вредности јер можемо да прилагодимо ПЛЦ према нашим захтевима. Миксер бубња који је опремљен ПЛЦ панелом је другачија машина од постројења са микропроцесорском плочом. ПЛЦ панел такође не захтева одржавање у поређењу са панелом микропроцесора. Увек верујемо у пружање најбољег клијентима како би могли да буду испред конкуренције. Не нуде сви произвођачи и извозници фабрика асфалтних бубњева постројења са ПЛЦ панелом.
Претходно тестирање свих погона се врши како би се осигурало да је све што напусти нашу фабрику спремно за обављање са мање муке на локацији.
Синороадер има више од 30 година искуства у производњи и производ који је подржан професионалном услугом и јефтинијим резервним деловима тако да негујете и користите своју опрему годинама које долазе.