మూడు రకాల హాట్ తారు మిక్సింగ్ ప్లాంట్లు ప్రస్తుతం బాగా ప్రాచుర్యం పొందాయి
రోడ్లను నిర్మించడానికి కంకర మరియు బిటుమెన్ను తారుగా మార్చడానికి థర్మల్ మిక్సింగ్ ప్రక్రియ అవసరం. దీనికి తారు మిక్సింగ్ ప్లాంట్ అనివార్యం. తారు మిక్సింగ్ ప్లాంట్ యొక్క ఉద్దేశ్యం ఏమిటంటే, సజాతీయ తారు సుగమం మిశ్రమాన్ని ఉత్పత్తి చేయడానికి ఒక ఎత్తైన ఉష్ణోగ్రత వద్ద మొత్తం మరియు తారును కలపడం. మినరల్ ఫిల్లర్తో లేదా లేకుండా ఒకే మెటీరియల్, ముతక మరియు చక్కటి కంకరల కలయికగా ఉపయోగించిన మొత్తం ఉంటుంది. బైండర్ మెటీరియల్ సాధారణంగా తారుగా ఉంటుంది, అయితే తారు ఎమల్షన్ లేదా వివిధ రకాల సవరించిన పదార్థాలలో ఒకటి కావచ్చు. ద్రవ మరియు పొడి పదార్థాలతో సహా వివిధ సంకలనాలను కూడా మిశ్రమంలో చేర్చవచ్చు.
ప్రస్తుతం హాట్ తారు మిక్సింగ్ ప్లాంట్లలో మూడు ప్రసిద్ధ రకాలు ఉన్నాయి: బ్యాచ్ మిక్స్, డ్రమ్ మిక్స్ మరియు కంటిన్యూస్ డ్రమ్ మిక్స్. మూడు రకాలు ఒకే అంతిమ ప్రయోజనాన్ని అందిస్తాయి మరియు తారు మిశ్రమం తయారీకి ఉపయోగించే మొక్క రకంతో సంబంధం లేకుండా తప్పనిసరిగా సమానంగా ఉండాలి. కింది విభాగాలలో వివరించిన విధంగా మూడు రకాలైన మొక్కలు వేర్వేరుగా ఉంటాయి, అయితే, ఆపరేషన్ మరియు పదార్థాల ప్రవాహం.
బ్యాచ్ మిక్స్ తారు ప్లాంట్ఏదైనా రహదారి నిర్మాణ సంస్థకు తారు మిక్సింగ్ ప్లాంట్ కీలకమైన పరికరం. ఏదైనా తారు బ్యాచ్ మిక్స్ ప్లాంట్ ఆపరేషన్ అనేక విధులను కలిగి ఉంటుంది. తారు బ్యాచ్ మొక్కలు వరుస బ్యాచ్లలో హాట్ మిక్స్ తారును ఉత్పత్తి చేస్తాయి. ఈ బ్యాచ్ మిక్స్ ప్లాంట్లు నిరంతర ప్రక్రియలో హాట్ మిక్స్ తారును ఉత్పత్తి చేస్తాయి. రీసైకిల్ చేసిన పదార్థాన్ని ఉపయోగించి హాట్ మిక్స్ తారు ఉత్పత్తికి ఈ పరికరాన్ని మార్చడం మరియు ఉపయోగించడం చాలా సాధ్యమే. బ్యాచ్ రకం మొక్కలు RAP (రీక్లెయిమ్డ్ తారు పేవ్మెంట్)ను జోడించడానికి అనుమతించే వైవిధ్యాలను కలిగి ఉంటాయి. ప్రామాణిక తారు బ్యాచ్ మిక్స్ ప్లాంట్ యొక్క భాగాలు: కోల్డ్ఫీడ్ సిస్టమ్, తారు సరఫరా వ్యవస్థ, మొత్తం డ్రైయర్, మిక్సింగ్ టవర్ మరియు ఉద్గార-నియంత్రణ వ్యవస్థ. బ్యాచ్ ప్లాంట్ టవర్లో హాట్ ఎలివేటర్, స్క్రీన్ డెక్, హాట్ బిన్లు, వెయిట్ హాప్పర్, తారు వెయిట్ బకెట్ మరియు పగ్మిల్ ఉంటాయి. మిక్స్లో ఉపయోగించిన మొత్తం నిల్వల నుండి తీసివేయబడుతుంది మరియు వ్యక్తిగత కోల్డ్-ఫీడ్ డబ్బాలలో ఉంచబడుతుంది. వివిధ పరిమాణాల కంకరలు ప్రతి బిన్ దిగువన ఉన్న గేట్ యొక్క ఓపెనింగ్ పరిమాణం మరియు బిన్ కింద కన్వేయర్ బెల్ట్ యొక్క వేగం కలయికతో వాటి డబ్బాల నుండి నిష్పత్తిలో ఉంటాయి. సాధారణంగా, ప్రతి డబ్బా క్రింద ఉన్న ఫీడర్ బెల్ట్ మొత్తం కోల్డ్-ఫీడ్ డబ్బాల క్రింద ఉన్న ఒక సేకరణ కన్వేయర్పై జమ చేస్తుంది. మొత్తం సేకరణ కన్వేయర్ ద్వారా రవాణా చేయబడుతుంది మరియు ఛార్జింగ్ కన్వేయర్కు బదిలీ చేయబడుతుంది. ఛార్జింగ్ కన్వేయర్లోని మెటీరియల్ మొత్తం డ్రైయర్ వరకు తీసుకువెళుతుంది.
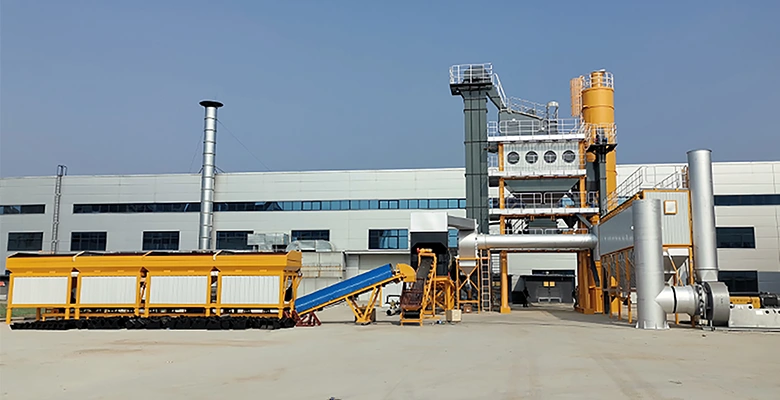
డ్రైయర్ కౌంటర్-ఫ్లో ఆధారంగా పనిచేస్తుంది. కంకర ఎగువ చివర డ్రైయర్లోకి ప్రవేశపెట్టబడింది మరియు డ్రమ్ భ్రమణ (గురుత్వాకర్షణ ప్రవాహం) మరియు తిరిగే డ్రైయర్లోని ఫ్లైట్ కాన్ఫిగరేషన్ రెండింటి ద్వారా డ్రమ్ క్రిందికి తరలించబడుతుంది. బర్నర్ డ్రైయర్ యొక్క దిగువ చివరలో ఉంది మరియు దహన మరియు ఎండబెట్టడం ప్రక్రియ నుండి వచ్చే ఎగ్జాస్ట్ వాయువులు మొత్తం ప్రవాహానికి వ్యతిరేకంగా (కౌంటర్ టు) డ్రైయర్ ఎగువ ముగింపు వైపు కదులుతాయి. మొత్తం ఎగ్జాస్ట్ వాయువుల ద్వారా దొర్లినందున, పదార్థం వేడి చేయబడుతుంది మరియు ఎండబెట్టబడుతుంది. ఎగ్సాస్ట్ గ్యాస్ స్ట్రీమ్లో భాగంగా డ్రైయర్ నుండి తేమ తొలగించబడుతుంది మరియు నిర్వహించబడుతుంది.
వేడి, పొడి కంకర అప్పుడు దిగువ చివరలో డ్రైయర్ నుండి విడుదల చేయబడుతుంది. వేడి మొత్తం సాధారణంగా బకెట్ ఎలివేటర్ ద్వారా ప్లాంట్ మిక్సింగ్ టవర్ పైభాగానికి రవాణా చేయబడుతుంది. ఎలివేటర్ నుండి డిశ్చార్జ్ అయిన తర్వాత, మొత్తం సాధారణంగా వైబ్రేటింగ్ స్క్రీన్ల సెట్ గుండా వెళుతుంది, సాధారణంగా, నాలుగు హాట్ స్టోరేజ్ బిన్లలో ఒకటి. అత్యుత్తమ మొత్తం పదార్థం నేరుగా అన్ని స్క్రీన్ల గుండా నం. 1 హాట్ బిన్లోకి వెళుతుంది; ముతక మొత్తం కణాలు వేరుచేయబడతాయి
విభిన్న-పరిమాణ స్క్రీన్లు మరియు ఇతర హాట్ బిన్లలో ఒకదానిలో జమ చేయబడతాయి. హాట్ బిన్లలోకి మొత్తం వేరుచేయడం అనేది స్క్రీన్ డెక్లో ఉపయోగించే స్క్రీన్లోని ఓపెనింగ్ల పరిమాణం మరియు కోల్డ్-ఫీడ్ బిన్లలోని కంకర యొక్క గ్రేడేషన్పై ఆధారపడి ఉంటుంది.
వేడిచేసిన, ఎండబెట్టిన మరియు పరిమాణం మార్చబడిన మొత్తం వేడి బిన్లలో ఉంచబడుతుంది, ప్రతి బిన్ దిగువన ఉన్న గేట్ నుండి వెయిట్ హాప్పర్లోకి విడుదల చేయబడుతుంది. ప్రతి కంకర యొక్క సరైన నిష్పత్తి బరువు ద్వారా నిర్ణయించబడుతుంది.
మొత్తానికి అనులోమానుపాతంలో మరియు తూకం వేయబడుతున్న అదే సమయంలో, తారు దాని నిల్వ ట్యాంక్ నుండి పగ్మిల్ పైన ఉన్న టవర్పై ఉన్న ప్రత్యేక వేడిచేసిన బకెట్కు పంప్ చేయబడుతుంది. సరైన మొత్తంలో పదార్థం బకెట్లోకి తూకం వేయబడుతుంది మరియు పగ్మిల్లోకి ఖాళీ అయ్యే వరకు ఉంచబడుతుంది. వెయిట్ హాప్పర్లోని మొత్తం ట్విన్-షాఫ్ట్ పగ్మిల్లోకి ఖాళీ చేయబడుతుంది మరియు విభిన్న కంకర భిన్నాలు చాలా తక్కువ వ్యవధిలో కలిసి ఉంటాయి-సాధారణంగా 5 సెకన్ల కంటే తక్కువ. ఈ క్లుప్త పొడి-మిక్స్ సమయం తర్వాత, బరువు బకెట్ నుండి తారు డిస్చార్జ్ చేయబడుతుంది.
పగ్మిల్లోకి, మరియు వెట్-మిక్స్ సమయం ప్రారంభమవుతుంది. కంకరతో తారును కలపడానికి మిక్సింగ్ సమయం తారు పదార్థం యొక్క పలుచని ఫిల్మ్తో మొత్తం కణాలను పూర్తిగా పూయడానికి అవసరమైన దానికంటే ఎక్కువ ఉండకూడదు-సాధారణంగా 25 నుండి 35 సెకన్ల పరిధిలో, ఈ శ్రేణి యొక్క దిగువ ముగింపుతో. మంచి స్థితిలో ఉన్న పగ్మిల్ కోసం. పగ్మిల్లో కలిపిన బ్యాచ్ పరిమాణం 1.81 నుండి 5.44 టన్నుల (2 నుండి 6 టన్నులు) పరిధిలో ఉంటుంది.
మిక్సింగ్ పూర్తయినప్పుడు, పగ్మిల్ దిగువన ఉన్న గేట్లు తెరవబడతాయి మరియు మిక్స్ హాల్ వెహికల్లోకి లేదా మిక్స్ను ట్రక్కులను బ్యాచ్ పద్ధతిలో లోడ్ చేసే గోతిలోకి తీసుకువెళ్లే రవాణా పరికరంలోకి విడుదల చేయబడుతుంది. చాలా బ్యాచ్ ప్లాంట్ల కోసం, పగ్మిల్ గేట్లను తెరిచి, మిక్స్ను డిశ్చార్జ్ చేయడానికి సుమారు 5 నుండి 7 సెకన్ల సమయం పడుతుంది. ఒక బ్యాచ్ కోసం మొత్తం మిక్సింగ్ సమయం (డ్రై-మిక్స్ సమయం + వెట్-మిక్స్ సమయం + మిక్స్ డిశ్చార్జ్ సమయం) దాదాపు 40 సెకన్ల వరకు ఉంటుంది, కానీ సాధారణంగా, మొత్తం మిక్సింగ్ సమయం దాదాపు 45 సెకన్లు ఉంటుంది.
ప్లాంట్ ప్రాథమిక మరియు ద్వితీయ సేకరణ వ్యవస్థలను కలిగి ఉన్న ఉద్గార-నియంత్రణ పరికరాలతో అమర్చబడి ఉంటుంది. డ్రై కలెక్టర్ లేదా నాకౌట్ బాక్స్ సాధారణంగా ప్రాథమిక కలెక్టర్గా ఉపయోగించబడుతుంది. తడి స్క్రబ్బర్ సిస్టమ్ లేదా, తరచుగా, డ్రై ఫాబ్రిక్ ఫిల్టర్ సిస్టమ్ (బ్యాగ్హౌస్)ని సెకండరీ కలెక్షన్ సిస్టమ్గా ఉపయోగించవచ్చు, డ్రైయర్ నుండి ప్రవహించే ఎగ్జాస్ట్ వాయువుల నుండి రేణువులను తొలగించి స్టాక్ ద్వారా వాతావరణానికి స్వచ్ఛమైన గాలిని పంపవచ్చు. .
RAPని మిక్స్లో చేర్చినట్లయితే, అది ప్రత్యేక కోల్డ్-ఫీడ్ బిన్లో ఉంచబడుతుంది, దాని నుండి అది ప్లాంట్కు పంపిణీ చేయబడుతుంది. RAPని మూడు స్థానాల్లో ఒకదానిలో కొత్త మొత్తానికి జోడించవచ్చు: హాట్ ఎలివేటర్ దిగువన; వేడి డబ్బాలు; లేదా, చాలా సాధారణంగా, బరువు తొట్టి. సూపర్ హీట్ చేయబడిన కొత్త కంకర మరియు రీక్లెయిమ్ చేయబడిన మెటీరియల్ మధ్య ఉష్ణ బదిలీ రెండు పదార్థాలు సంపర్కంలోకి వచ్చిన వెంటనే ప్రారంభమవుతుంది మరియు పగ్మిల్లో మిక్సింగ్ ప్రక్రియలో కొనసాగుతుంది.
డ్రమ్ మిక్స్ తారు ప్లాంట్బ్యాచ్ రకంతో పోలిస్తే, డ్రమ్ మిక్స్ తారు ప్లాంట్ తక్కువ ఉష్ణ నష్టం, తక్కువ పని శక్తి, ఓవర్ఫ్లో లేదు, తక్కువ దుమ్ము ఎగురుతుంది మరియు స్థిరమైన ఉష్ణోగ్రత నియంత్రణను కలిగి ఉంటుంది. ఖచ్చితమైన అనుపాత అవుట్పుట్ని నిర్ధారించడానికి కంకర ఫ్లో రేట్ మరియు ప్రీ-సెట్టింగ్ తారు-మొత్తం నిష్పత్తి ప్రకారం నియంత్రణ వ్యవస్థ స్వయంచాలకంగా తారు ప్రవాహం రేటును సర్దుబాటు చేస్తుంది. తారు డ్రమ్ మిక్స్ ప్లాంట్ అనేది నిరంతర మిక్సింగ్ ప్లాంట్లుగా వర్గీకరించబడిన మొక్కల రకాలు, నిరంతర ప్రక్రియలో హాట్ మిక్స్ తారును ఉత్పత్తి చేస్తుంది.
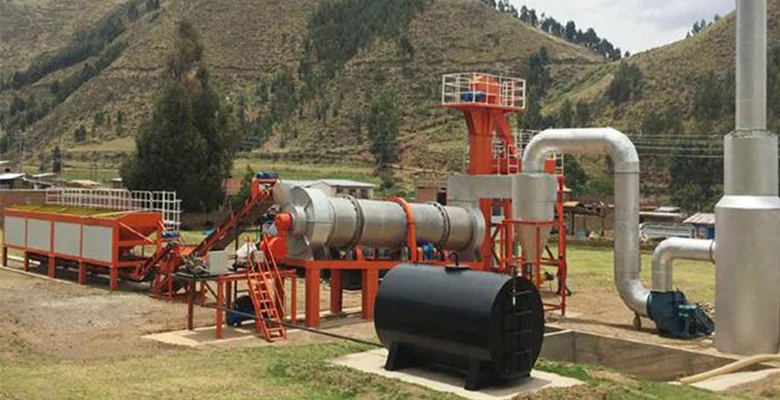
సాధారణంగా HMA బ్యాచ్ మరియు డ్రమ్-మిక్స్ ప్లాంట్లలో కోల్డ్-ఫీడ్ సిస్టమ్లు ఒకే విధంగా ఉంటాయి. ప్రతి ఒక్కటి కోల్డ్ఫీడ్ డబ్బాలు, ఫీడర్ కన్వేయర్లు, సేకరణ కన్వేయర్ మరియు ఛార్జింగ్ కన్వేయర్లను కలిగి ఉంటుంది. చాలా డ్రమ్-మిక్స్ ప్లాంట్లలో మరియు కొన్ని బ్యాచ్ ప్లాంట్లలో, సిస్టమ్లో ఏదో ఒక సమయంలో స్కాల్పింగ్ స్క్రీన్ చేర్చబడుతుంది. రీసైకిల్ చేసిన మిశ్రమాన్ని ఉత్పత్తి చేయడానికి ప్లాంట్లోకి RAPని కూడా అందించినట్లయితే, అదనపు పదార్థాన్ని నిర్వహించడానికి అదనపు కోల్డ్-ఫీడ్ బిన్ లేదా డబ్బాలు, ఫీడర్ బెల్ట్ మరియు/లేదా సేకరణ కన్వేయర్, స్కాల్పింగ్ స్క్రీన్ మరియు ఛార్జింగ్ కన్వేయర్ అవసరం. డ్రమ్-మిక్స్ ప్లాంట్లు ఐదు ప్రధాన భాగాలను కలిగి ఉంటాయి: కోల్డ్-ఫీడ్ సిస్టమ్, తారు సరఫరా వ్యవస్థ, డ్రమ్ మిక్సర్, ఉప్పెన లేదా నిల్వ గోతులు మరియు ఉద్గార నియంత్రణ పరికరాలు.
చల్లటి-ఫీడ్ డబ్బాలు మొక్కకు పదార్థాన్ని నిష్పత్తిలో ఉంచడానికి ఉపయోగిస్తారు. ప్రతి బిన్ కింద వేరియబుల్-స్పీడ్ ఫీడర్ బెల్ట్ ఉపయోగించబడుతుంది. ప్రతి బిన్ నుండి తీసుకోబడిన మొత్తం మొత్తాన్ని గేట్ ఓపెనింగ్ పరిమాణం మరియు ఫీడర్ బెల్ట్ యొక్క వేగం రెండింటి ద్వారా వేర్వేరు-పరిమాణ పదార్థాల ఖచ్చితమైన డెలివరీని అందించడం ద్వారా నియంత్రించవచ్చు. ప్రతి ఫీడర్ బెల్ట్లోని మొత్తం కోల్డ్-ఫీడ్ బిన్లన్నింటికి దిగువన నడిచే సేకరణ కన్వేయర్లో జమ చేయబడుతుంది. మిశ్రమ పదార్థం సాధారణంగా స్కాల్పింగ్ స్క్రీన్ ద్వారా పంపబడుతుంది మరియు డ్రమ్ మిక్సర్కు రవాణా చేయడానికి ఛార్జింగ్ కన్వేయర్కు బదిలీ చేయబడుతుంది.
ఛార్జింగ్ కన్వేయర్లో రెండు పరికరాలను అమర్చారు, ఇవి ప్లాంట్కు పంపిణీ చేయబడే మొత్తం మొత్తాన్ని నిర్ణయించడానికి ఉపయోగించబడతాయి: కన్వేయర్ బెల్ట్ కింద ఉన్న ఒక బరువు వంతెన దానిపై ప్రయాణిస్తున్న మొత్తం బరువును కొలుస్తుంది మరియు సెన్సార్ బెల్ట్ వేగాన్ని నిర్ణయిస్తుంది. ఈ రెండు విలువలు డ్రమ్ మిక్సర్లోకి ప్రవేశించిన గంటకు టన్నుల (టన్నులు) మొత్తం యొక్క తడి బరువును గణించడానికి ఉపయోగించబడతాయి. ప్లాంట్ కంప్యూటర్, ఇన్పుట్ విలువగా అందించబడిన మొత్తంలో తేమ మొత్తంతో, మిశ్రమంలో అవసరమైన తారు యొక్క సరైన మొత్తాన్ని నిర్ణయించడానికి తడి బరువును పొడి బరువుగా మారుస్తుంది.
సాంప్రదాయ డ్రమ్ మిక్సర్ అనేది సమాంతర-ప్రవాహ వ్యవస్థ-ఎగ్జాస్ట్ వాయువులు మరియు మొత్తం ఒకే దిశలో కదులుతాయి. బర్నర్ డ్రమ్ యొక్క ఎగువ చివర (మొత్తం ఇన్లెట్ ముగింపు) వద్ద ఉంది. మొత్తం బర్నర్ పైన ఉన్న వంపుతిరిగిన చ్యూట్ నుండి లేదా బర్నర్ కింద ఉన్న స్లింగర్ కన్వేయర్ నుండి డ్రమ్లోకి ప్రవేశిస్తుంది. గురుత్వాకర్షణ మరియు డ్రమ్ లోపల ఉన్న విమానాల కాన్ఫిగరేషన్ కలయిక ద్వారా మొత్తం డ్రమ్ క్రిందికి తరలించబడుతుంది. ఇది ప్రయాణిస్తున్నప్పుడు, కంకర వేడి చేయబడుతుంది మరియు తేమ తొలగించబడుతుంది. ఉష్ణ-బదిలీ ప్రక్రియలో సహాయం చేయడానికి డ్రమ్ పొడవు యొక్క మధ్య బిందువు దగ్గర మొత్తం యొక్క దట్టమైన వీల్ నిర్మించబడింది.
కొత్త మొత్తానికి RAP జోడించబడితే, అది దాని స్వంత కోల్డ్-ఫీడ్ బిన్ మరియు సేకరణ/చార్జింగ్ కన్వేయర్ సిస్టమ్ నుండి డ్రమ్ పొడవు (స్ప్లిట్-ఫీడ్ సిస్టమ్) మధ్యలో ఉన్న ఇన్లెట్లోకి జమ చేయబడుతుంది. ఈ ప్రక్రియలో, RAP ఎంట్రీ పాయింట్ యొక్క అప్స్ట్రీమ్లో కొత్త కంకర యొక్క వీల్ ద్వారా అధిక-ఉష్ణోగ్రత ఎగ్జాస్ట్ వాయువుల నుండి తిరిగి పొందబడిన పదార్థం రక్షించబడుతుంది. అధిక RAP కంటెంట్తో మిక్స్లను ఉపయోగించినప్పుడు, ఆ ప్రక్రియలో RAP వేడెక్కడానికి అవకాశం ఉంది. దీని ఫలితంగా డ్రమ్ నుండి పొగ వెలువడవచ్చు లేదా RAPకి నష్టం జరగవచ్చు.
కొత్త మొత్తం మరియు రీక్లెయిమ్ చేయబడిన మెటీరియల్, ఉపయోగించినట్లయితే, డ్రమ్ వెనుక భాగానికి కలిసి కదులుతాయి. తారు నిల్వ ట్యాంక్ నుండి పంప్ ద్వారా లాగబడుతుంది మరియు మీటర్ ద్వారా ఫీడ్ చేయబడుతుంది, ఇక్కడ తారు యొక్క సరైన వాల్యూమ్ నిర్ణయించబడుతుంది. బైండర్ పదార్థం అప్పుడు మిక్సింగ్ డ్రమ్ వెనుక భాగంలో పైపు ద్వారా పంపిణీ చేయబడుతుంది, ఇక్కడ తారు మొత్తం మీద ఇంజెక్ట్ చేయబడుతుంది. పదార్థాలు కలిసి దొర్లడం మరియు డ్రమ్ యొక్క ఉత్సర్గ చివరకి తరలించడం వలన మొత్తం పూత ఏర్పడుతుంది. మినరల్ ఫిల్లర్ లేదా బ్యాగ్హౌస్ జరిమానాలు, లేదా రెండూ కూడా డ్రమ్ వెనుక భాగంలోకి జోడించబడతాయి, దీనికి ముందు లేదా తారుతో కలిపి ఉంటాయి.
తారు మిశ్రమం ఒక స్టోరేజ్ సిలోకి రవాణా చేయడానికి ఒక రవాణా పరికరంలో (డ్రాగ్ స్లాట్ కన్వేయర్, బెల్ట్ కన్వేయర్ లేదా బకెట్ ఎలివేటర్) జమ చేయబడుతుంది. సిలో మిక్స్ యొక్క నిరంతర ప్రవాహాన్ని హాల్ వాహనంలోకి విడుదల చేయడానికి బ్యాచ్ ఫ్లోగా మారుస్తుంది.
సాధారణంగా, బ్యాచ్ ప్లాంట్లోని డ్రమ్-మిక్స్ ప్లాంట్లో అదే రకమైన ఉద్గార-నియంత్రణ పరికరాలు ఉపయోగించబడతాయి. ప్రైమరీ డ్రై కలెక్టర్ మరియు వెట్ స్క్రబ్బర్ సిస్టమ్ లేదా బ్యాగ్హౌస్ సెకండరీ కలెక్టర్ని ఉపయోగించవచ్చు. తడి స్క్రబ్బర్ వ్యవస్థను ఉపయోగించినట్లయితే, సేకరించిన జరిమానాలను తిరిగి మిశ్రమంలోకి రీసైకిల్ చేయడం సాధ్యం కాదు మరియు వృధా అవుతుంది; బ్యాగ్హౌస్ని ఉపయోగించినట్లయితే, సేకరించిన జరిమానాలను పూర్తిగా లేదా కొంత భాగాన్ని మిక్సింగ్ డ్రమ్కు తిరిగి ఇవ్వవచ్చు లేదా అవి వృధా కావచ్చు.
నిరంతర మిక్స్ తారు ప్లాంట్నిరంతర ప్లాంట్లలో ఉత్పత్తి యొక్క లయ బ్యాచ్లుగా విభజించబడనందున ఉత్పత్తి చక్రంలో అంతరాయం ఉండదు. పదార్థం యొక్క మిక్సింగ్ పొడిగించబడిన డ్రమ్ లోపల జరుగుతుంది, ఎందుకంటే ఇది పొడిగా ఉంటుంది మరియు అదే సమయంలో పదార్థాన్ని కలుపుతుంది. మిక్సింగ్ టవర్ లేదా ఎలివేటర్లు లేనందున, నిర్వహణ ఖర్చు తగ్గడంతో, సిస్టమ్ గణనీయంగా సరళీకృతం చేయబడింది. అయితే స్క్రీన్ లేకపోవడం వలన ఉత్పత్తి చక్రం ప్రారంభంలో, కంకరలను డ్రైయర్లోకి ఫీడ్ చేయడానికి ముందు మరియు తత్ఫలితంగా డ్రైయర్ నుండి తారుగా విడుదలయ్యే ముందు ఖచ్చితమైన నియంత్రణలను కలిగి ఉండటం అవసరం.
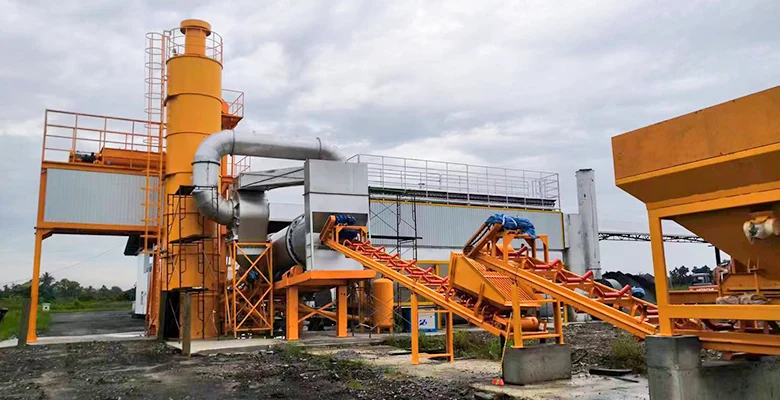
సమగ్ర మీటరింగ్
బ్యాచ్ తారు మిక్సింగ్ ప్లాంట్ల మాదిరిగానే,
నిరంతర మొక్కల ఉత్పత్తి చక్రం కోల్డ్ ఫీడర్లతో ప్రారంభమవుతుంది, ఇక్కడ కంకరలు సాధారణంగా వాల్యూమ్ ద్వారా మీటర్ చేయబడతాయి; అవసరమైతే, ఇసుక వెలికితీసే యంత్రం మీటరింగ్ కోసం బరువు-బెల్ట్తో అమర్చబడుతుంది.
వర్జిన్ కంకరల మొత్తం బరువు నియంత్రణ, అయితే, రెండు వేర్వేరు ప్లాంట్లలో ఉత్పత్తి చక్రంలో రెండు వేర్వేరు దశల్లో అమలు చేయబడుతుంది. నిరంతర రకంలో ఫీడ్ బెల్ట్ ఉంది, తడిగా ఉన్న కంకరలను డ్రైయర్ డ్రమ్లోకి ఫీడ్ చేయడానికి ముందు, నీటి బరువును తీసివేయడానికి వీలుగా తేమ కంటెంట్ మానవీయంగా సెట్ చేయబడుతుంది. అందువల్ల కంకరలలో తేమ శాతం, ముఖ్యంగా ఇసుక, స్థిరమైన విలువను కలిగి ఉండటం చాలా ముఖ్యం, ఇది తరచుగా ప్రయోగశాల పరీక్షల ద్వారా నిరంతరం పర్యవేక్షించబడుతుంది.
బిటుమెన్ మీటరింగ్
నిరంతర ప్లాంట్లలో ఫీడ్ పంప్ తర్వాత లీటర్-కౌంటర్ ద్వారా బిటుమెన్ మీటరింగ్ సాధారణంగా వాల్యూమెట్రిక్ అవుతుంది. ప్రత్యామ్నాయంగా, మాస్ కౌంటర్ను ఇన్స్టాల్ చేయడం సాధ్యపడుతుంది, సవరించిన బిటుమెన్ ఉపయోగించినట్లయితే అవసరమైన ఎంపిక, ఇది తరచుగా శుభ్రపరిచే కార్యకలాపాలు అవసరం.
పూరక మీటరింగ్
నిరంతర ప్లాంట్లలో మీటరింగ్ సిస్టమ్ సాధారణంగా వాల్యూమెట్రిక్గా ఉంటుంది, ఇది మునుపటి వాయు మీటరింగ్ సిస్టమ్ను భర్తీ చేసిన వేరియబుల్-స్పీడ్ ఫీడ్ స్క్రూలను ఉపయోగిస్తుంది.
మా అన్ని ఎగుమతి ప్లాంట్లలో కంట్రోల్ ప్యానెల్ PLC రకం. ఇది భారీ విలువ జోడింపు ఎందుకంటే మేము మా అవసరాలకు అనుగుణంగా PLCని అనుకూలీకరించవచ్చు. PLC ప్యానెల్తో అమర్చబడిన డ్రమ్ మిక్సర్ మైక్రోప్రాసెసర్ ప్యానెల్ ఉన్న ప్లాంట్ కంటే భిన్నమైన యంత్రం. మైక్రోప్రాసెసర్ ప్యానెల్తో పోలిస్తే PLC ప్యానెల్ మెయింటెనెన్స్ ఫ్రీ. మేము ఎల్లప్పుడూ కస్టమర్లకు ఉత్తమమైన వాటిని అందించాలని విశ్వసిస్తాము, తద్వారా వారు వారి పోటీ కంటే ముందుండగలరు. తారు డ్రమ్ ప్లాంట్ల తయారీదారులు మరియు ఎగుమతిదారులు PLC ప్యానెల్తో ప్లాంట్ను అందించరు.
మా కర్మాగారం నుండి బయలుదేరే ఏదైనా సైట్లో తక్కువ అవాంతరంతో పని చేయడానికి సిద్ధంగా ఉందని నిర్ధారించుకోవడానికి అన్ని మొక్కలను ముందస్తుగా పరీక్షించడం జరుగుతుంది.
సినోరోడర్కు 30 సంవత్సరాల కంటే ఎక్కువ తయారీ అనుభవం ఉంది మరియు వృత్తిపరమైన సేవ మరియు చౌకైన విడిభాగాల మద్దతు ఉన్న ఉత్పత్తిని కలిగి ఉంది, తద్వారా మీరు రాబోయే సంవత్సరాల్లో మీ పరికరాలను ఎంతో ఆదరించి, ఉపయోగించుకోవచ్చు.