Зараз більшою популярністю користуються три типи заводів гарячого асфальтозмішування
Перетворення наповнювачів і бітуму в асфальт для будівництва доріг вимагає процесу термічного змішування. Для цього не обійтися без асфальтозмішувальної установки. Метою асфальтозмішувальної установки є змішування заповнювачів і асфальту при високій температурі для отримання однорідної асфальтової суміші. Використовуваний заповнювач може бути одним матеріалом, комбінацією крупних і дрібних заповнювачів, з мінеральним наповнювачем або без нього. В’яжучим матеріалом зазвичай є асфальт, але це може бути асфальтова емульсія або один із різноманітних модифікованих матеріалів. У суміш також можна вводити різні добавки, включаючи рідкі та порошкоподібні матеріали.
В даний час існує ще три типи установок для змішування гарячого асфальту: періодична суміш, барабанна суміш і безперервна барабанна суміш. Усі три типи служать одній кінцевій меті, і асфальтобетонна суміш повинна бути по суті однаковою незалежно від типу заводу, який використовується для її виробництва. Однак ці три типи установок відрізняються роботою та потоком матеріалів, як описано в наступних розділах.
Асфальтобетонний завод партійної діїАсфальтозмішувальна установка є основним обладнанням будь-якої дорожньо-будівельної компанії. Будь-який асфальтобетонний завод має багато функцій. Асфальтобетонні заводи виробляють гарячу асфальтобетонну суміш серією партій. Ці заводи періодичної дії виробляють гарячу асфальтобетонну суміш у безперервному процесі. Також можна змінити та використовувати це обладнання для виробництва гарячої асфальтобетонної суміші з переробленого матеріалу. Заводи партійного типу мають варіації, які дозволяють додавати RAP (регенероване асфальтне покриття). Компонентами стандартної асфальтобетонної суміші є: система холодної подачі, система подачі асфальту, сушарка заповнювачів, змішувальна вежа та система контролю викидів. Башта заводу періодичної дії складається з гарячого елеватора, ситового майданчика, гарячих бункерів, вагового бункера, ковша для зважування асфальту та пугмлина. Заповнювач, який використовується в суміші, виймають із запасів і поміщають в окремі бункери для холодного корму. Заповнювачі різних розмірів розподіляються з бункерів за допомогою комбінації розміру отвору воріт у дні кожного бункера та швидкості конвеєрної стрічки під бункером. Як правило, стрічка подачі під кожним бункером подає заповнювач на збиральний конвеєр, розташований під усіма бункерами холодної подачі. Інертний матеріал транспортується збиральним конвеєром і передається на завантажувальний конвеєр. Потім матеріал на завантажувальному конвеєрі транспортується до агрегатної сушарки.
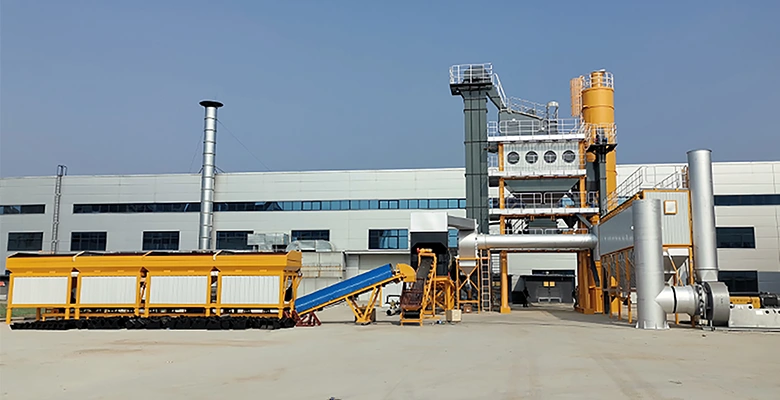
Сушарка працює за принципом протитоку. Заповнювач вводиться в сушарку з верхнього кінця і переміщується вниз по барабану як обертанням барабана (гравітаційний потік), так і конфігурацією польоту всередині обертової сушарки. Пальник розташований у нижньому кінці сушарки, а вихлопні гази, що утворюються в процесі згоряння та сушіння, рухаються до верхнього кінця сушарки, проти (проти) потоку агрегату. Коли заповнювач перекидається через вихлопні гази, матеріал нагрівається та сушиться. Волога видаляється і виводиться з сушарки як частина потоку відпрацьованих газів.
Гарячий сухий заповнювач потім вивантажується з сушарки в нижній частині. Гарячий заповнювач зазвичай транспортується до верхньої частини змішувальної вежі установки за допомогою ковшового елеватора. Після вивантаження з елеватора заповнювач зазвичай проходить через набір вібраційних грохотів в один із чотирьох бункерів для гарячого зберігання. Найдрібніший заповнювач проходить безпосередньо через усі сита в гарячий бункер № 1; більш грубі частинки заповнювача відокремлюються
сита різного розміру та помістили в один із інших гарячих бункерів. Розподіл заповнювачів у гарячих бункерах залежить від розміру отворів у ситах, які використовуються в ситовому настилі, та градації заповнювачів у бункерах для холодної подачі.
Нагрітий, висушений і змінений розмір заповнювача зберігається в гарячих бункерах до вивантаження через затвор на дні кожного бункера у ваговий бункер. Правильна пропорція кожного заповнювача визначається вагою.
У той самий час, коли заповнювач дозується та зважується, асфальт перекачується з резервуару для зберігання в окреме вагове відро з підігрівом, розташоване на вежі прямо над молотком. Потрібну кількість матеріалу зважують у відро і витримують, поки його не виливатимуть у мотовилку. Інертний матеріал у ваговому бункері виливається в двовальний молотковий млин, і різні фракції інертного матеріалу змішуються протягом дуже короткого періоду часу — зазвичай менше 5 секунд. Після цього короткого часу сухої суміші асфальт із вагового ковша вивантажується.
в пугмілл, і починається час вологого змішування. Час змішування для змішування асфальту з наповнювачем не повинен перевищувати час, необхідний для повного покриття частинок наповнювача тонкою плівкою асфальтового матеріалу — зазвичай у діапазоні від 25 до 35 секунд, з нижньою межею цього діапазону. будучи для pugmill, який знаходиться в хорошому стані. Розмір партії, що змішується в мочевому млині, може бути в діапазоні від 1,81 до 5,44 тонни (від 2 до 6 тонн).
Після завершення змішування відкриваються заслінки в нижній частині мотовила, і суміш вивантажується в транспортний засіб або в конвеєрний пристрій, який транспортує суміш до силосу, з якого вантажівки завантажуватимуться порційним способом. Для більшості заводів періодичної дії час, необхідний для відкриття затворів мотовила та вивантаження суміші, становить приблизно 5-7 секунд. Загальний час змішування (час сухого змішування + час вологого змішування + час вивантаження суміші) для партії може становити близько 40 секунд, але зазвичай загальний час змішування становить близько 45 секунд.
Завод обладнано пристроями контролю викидів, які містять як первинну, так і вторинну системи збору. Як первинний колектор зазвичай використовується сухий колектор або вибивна коробка. В якості вторинної системи збору для видалення твердих часток із вихлопних газів, які витікають із сушарки, можна використовувати або систему мокрого скруберу, або, частіше, систему сухого тканинного фільтра (рукавний фільтр) і направляти чисте повітря в атмосферу через трубу. .
Якщо RAP міститься в суміші, його поміщають в окремий бункер холодного корму, звідки він доставляється на завод. RAP можна додати до нового агрегату в одному з трьох місць: у нижній частині гарячого елеватора; гарячі баки; або, як правило, ваговий бункер. Передача тепла між перегрітим новим заповнювачем і відновленим матеріалом починається, як тільки обидва матеріали вступають у контакт, і продовжується під час процесу змішування в молотку.
Барабанний асфальтобетонний заводПорівняно з партійним типом, барабанна асфальтобетонна установка має менші втрати тепла, нижчу робочу потужність, відсутність переливу, менше летіння пилу та стабільний контроль температури. Система керування автоматично регулює швидкість потоку асфальту відповідно до швидкості потоку наповнювачів і попередньо встановленого співвідношення асфальт-наповнювачі, щоб забезпечити точну пропорційну продуктивність. Барабанні асфальтобетонні установки — це типи установок, які класифікуються як безперервні змішувальні установки, які виробляють гарячу асфальтобетонну суміш у безперервному процесі.
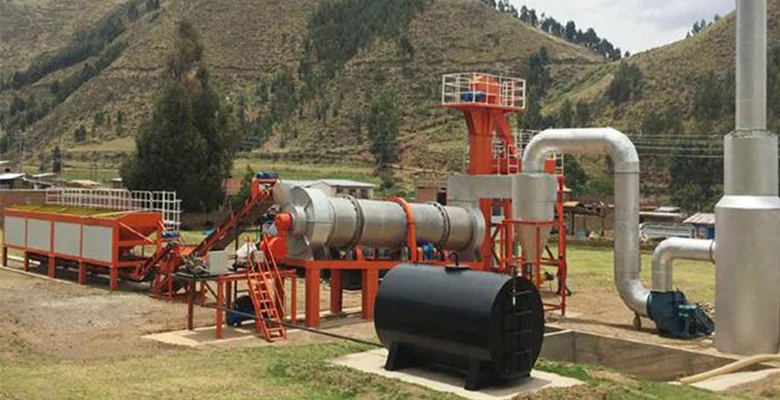
Зазвичай системи холодної подачі на установках періодичної дії та барабанних змішувачів HMA подібні. Кожен складається з бункерів холодної подачі, живильних конвеєрів, збирального конвеєра та завантажувального конвеєра. На більшості барабанних сумішоутворювальних установок і на деяких заводах періодичної дії до системи в якийсь момент включено скальп-грохо. Якщо RAP також подається на завод для виробництва переробленої суміші, для роботи з додатковим матеріалом необхідні додатковий бункер або бункери холодної подачі, стрічка подачі та/або збиральний конвеєр, решітка для скальпування та завантажувальний конвеєр. Барабанні сумішоутворювальні установки складаються з п’яти основних компонентів: системи холодної подачі, системи подачі асфальту, барабанного змішувача, силосів для зберігання або зберігання та обладнання для контролю викидів.
Бункери холодного корму використовуються для дозування матеріалу рослині. Під кожним бункером використовується подавальний ремінь із змінною швидкістю. Таким чином, кількість заповнювача, що витягується з кожного бункера, можна контролювати як розміром отвору воріт, так і швидкістю стрічки живильника, щоб забезпечити точну подачу матеріалів різного розміру. Заповнювач на кожній стрічці подачі подається на збиральний конвеєр, який проходить під усіма бункерами холодної подачі. Об’єднаний матеріал зазвичай пропускають через грохот, а потім передають на завантажувальний конвеєр для транспортування до барабанного змішувача.
Завантажувальний конвеєр оснащений двома пристроями, які використовуються для визначення кількості заповнювача, що надходить на завод: ваговий міст під конвеєрною стрічкою вимірює вагу заповнювача, що проходить по ньому, а датчик визначає швидкість руху стрічки. Ці два значення використовуються для обчислення вологої ваги заповнювача в тоннах (тоннах) на годину, що надходить у барабанний змішувач. Заводський комп’ютер, використовуючи кількість вологи в заповнювачі як вхідне значення, перетворює мокру вагу в суху вагу, щоб визначити правильну кількість асфальту, необхідного для суміші.
Звичайний барабанний змішувач — це система з паралельним потоком — вихлопні гази та агрегат рухаються в одному напрямку. Пальник розташований у верхньому кінці (кінець входу агрегату) барабана. Заповнювач надходить у барабан або з похилого жолоба над пальником, або по стропальному конвеєру під пальником. Заповнювач переміщується вниз по барабану завдяки поєднанню сили тяжіння та конфігурації рейок, розташованих усередині барабана. Під час руху заповнювач нагрівається, а волога видаляється. Поблизу середини довжини барабана утворюється щільна завіса із заповнювачів для сприяння процесу теплопередачі.
Якщо RAP додається до нового заповнювача, він подається з власного бункера холодної подачі та збиральної/завантажувальної конвеєрної системи у вхідний отвір, розташований поблизу центру довжини барабана (система розділеної подачі). У цьому процесі регенерований матеріал захищений від високотемпературних вихлопних газів завісою нового агрегату перед точкою входу RAP. Коли використовуються суміші з високим вмістом RAP, є більша ймовірність, що RAP буде перегріватися в процесі. Це може призвести до виділення диму з барабана або пошкодження RAP.
Новий заповнювач і регенерований матеріал, якщо він використовується, переміщуються разом у задню частину барабана. Асфальт забирається з резервуару насосом і подається через лічильник, де визначається необхідний об’єм асфальту. Потім в’яжучий матеріал подається через трубу в задню частину змішувального барабана, де асфальт впорскується на заповнювач. Покриття агрегату відбувається, коли матеріали збиваються разом і переміщуються до розвантажувального кінця барабана. Мінеральний наповнювач або мішкова дрібна фракція, або те й інше, також додається в задню частину барабана безпосередньо перед або разом з додаванням асфальту.
Асфальтобетонна суміш подається в транспортувальний пристрій (волоконний конвеєр, стрічковий конвеєр або ковшовий елеватор) для транспортування в силос для зберігання. Силос перетворює безперервний потік суміші в порційний потік для вивантаження в транспортний засіб.
Загалом, на установці барабанного змішування використовується той самий тип обладнання для контролю викидів, що й на установці періодичної дії. Можна використовувати первинний сухий колектор і або систему мокрого скрубера, або вторинний колектор з рукавною камерою. Якщо використовується система мокрого скрубера, зібрані дрібні фракції не можуть бути перероблені назад у суміш і викидаються даремно; якщо використовується рукавний фільтр, зібрані дрібні фракції можуть бути повернуті повністю або частково в змішувальний барабан, або вони можуть бути витрачені.
Асфальтобетонний завод безперервної діїНа безперервних заводах немає перерв у виробничому циклі, оскільки ритм виробництва не розбивається на партії. Змішування матеріалу відбувається всередині сушильного барабана, який має подовжену форму, оскільки він одночасно сушить і змішує матеріал. Оскільки немає змішувальної башти чи елеваторів, система значно спрощується, що призводить до зниження вартості обслуговування. Однак відсутність грохота робить необхідним точний контроль на початку виробничого циклу, перед подачею заповнювачів у сушарку та перед тим, як вони, відповідно, вивантажуються з сушарки у вигляді асфальту.
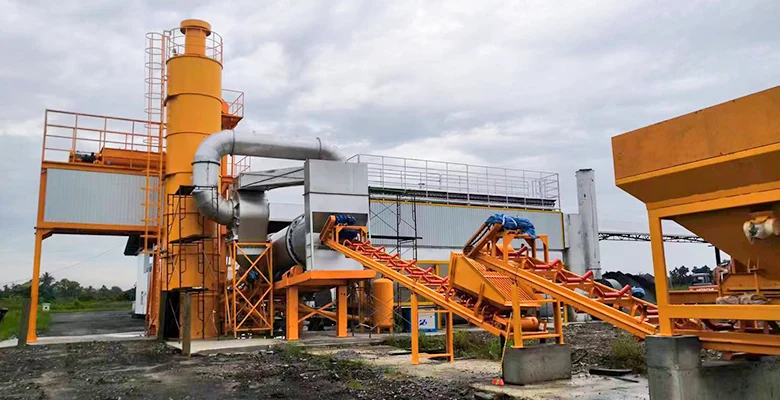
СУПОВНИЙ ОБЛІК
Подібно до асфальтозмішувальних установок періодичної дії,
виробничий цикл заводів безперервної дії також починається з холодних живильників, де заповнювачі зазвичай дозуються за об’ємом; якщо потрібно, піскоекстрактор може бути оснащений ваговим поясом для дозування.
Контроль загальної ваги первинних заповнювачів, однак, здійснюється на двох різних фазах виробничого циклу на двох різних заводах. У безперервному типі є стрічка подачі, перш ніж вологі агрегати подаються в сушильний барабан, де вміст вологи встановлюється вручну, щоб дозволити відняти вагу води. Тому надзвичайно важливо, щоб вміст вологи в заповнювачах, особливо в піску, мав постійне значення, яке постійно контролюється за допомогою частих лабораторних тестів.
ДОЗІР БІТУМУ
На установках безперервної дії дозування бітуму, як правило, відбувається об’ємно за допомогою лічильника літрів після живильного насоса. Крім того, можна встановити лічильник маси, необхідний вибір, якщо використовується модифікований бітум, який вимагає частих операцій очищення.
Дозування наповнювача
На заводах безперервної дії система дозування, як правило, об’ємна, використовує подавальні шнеки зі змінною швидкістю, які замінили попередню пневматичну систему дозування.
На всіх наших експортних заводах панель керування є типом PLC. Це величезна додаткова вартість, оскільки ми можемо налаштувати ПЛК відповідно до наших вимог. Барабанний змішувач, оснащений панеллю ПЛК, відрізняється від машини з мікропроцесорною панеллю. Панель ПЛК також не потребує обслуговування порівняно з панеллю мікропроцесора. Ми завжди віримо в надання клієнтам найкращого, щоб вони могли випереджати своїх конкурентів. Не всі виробники та експортери асфальтобетонних установок пропонують установку з панеллю PLC.
Попереднє тестування всіх заводів проводиться, щоб переконатися, що все, що покидає наш завод, готове до роботи з меншими труднощами на місці.
Sinoroader має більш ніж 30-річний досвід виробництва та продукт, який підтримується професійним обслуговуванням і дешевшими запчастинами, щоб ви берегли та використовували своє обладнання довгі роки.